Mobile Plant Maintenance for SAP ECC and S/4HANA
Simplify and digitize your SAP PM and SAP EAM systems with mobile online and offline access to SAP work orders, notifications, equipment and digital forms.
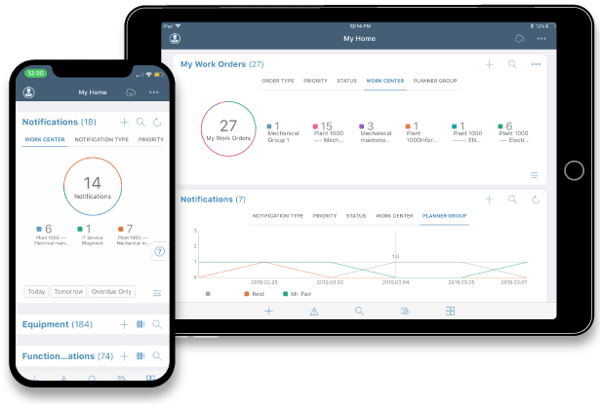
See It In Action
TRUSTED BY LEADING FRONTLINE WORKERS WORLDWIDE
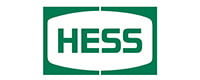
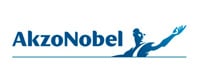
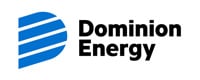
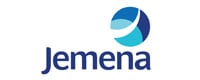
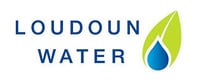
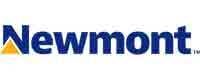
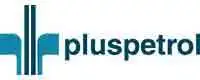
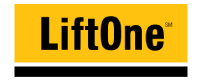
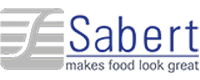
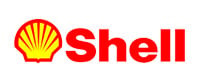
Reimagine Safer and Efficient Maintenance Operations
with Mobile SAP EAM and SAP PM
mWorkOrder for SAP PM has been designed to digitize and automate paper based maintenance processes. Starting from mobile work order creation, mobile notifications, mobile work instructions to digital documentation for work order completion, mWorkOrder provides an end to end mobile plant maintenance process flow.
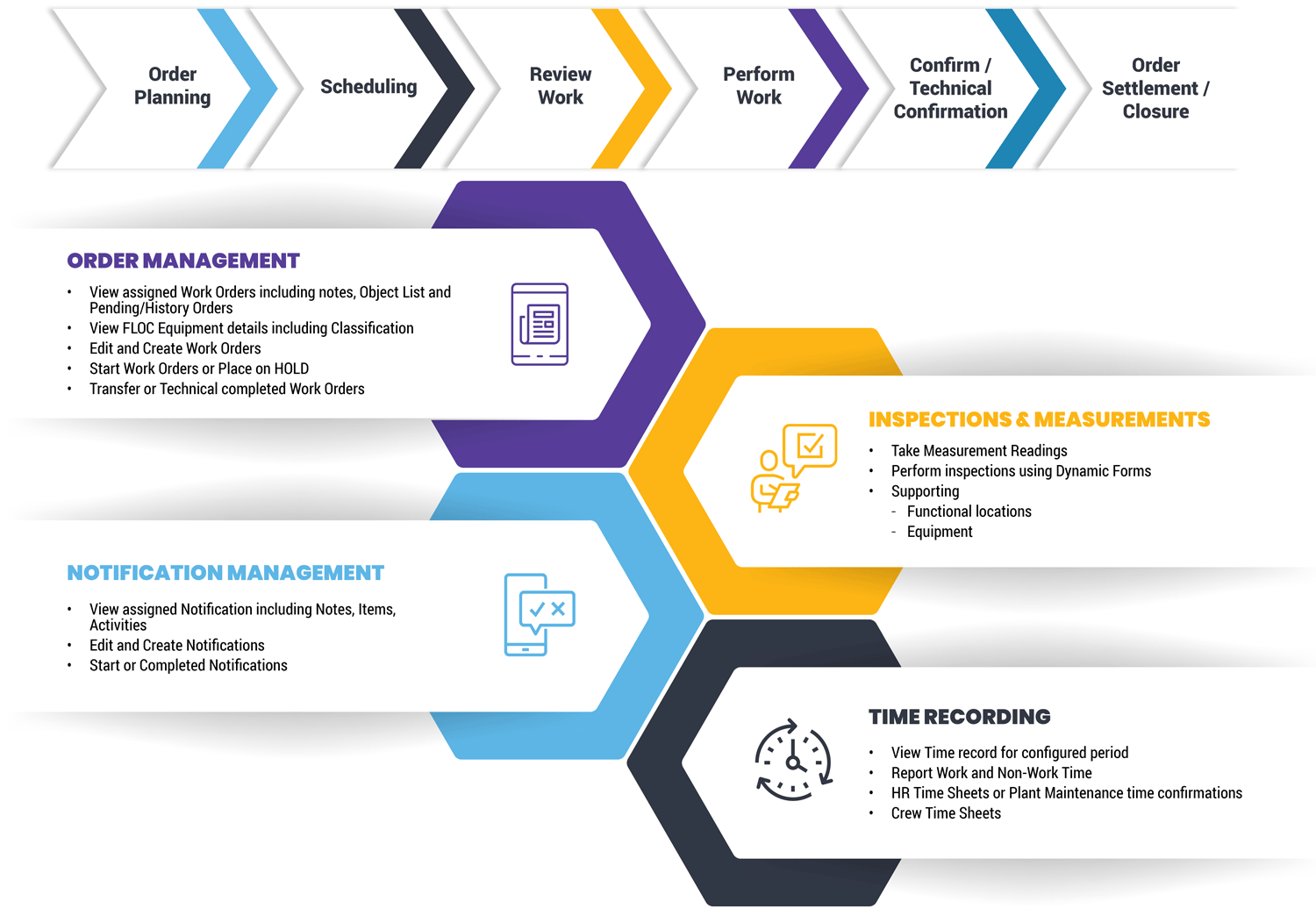
Key Features
Asset Equipment Dashboard
With one scan on your mobile or smart glass device, the Connected Maintenance application auto-detects your machine's complete health & history. Empower your planners, schedulers & technicians with important machine & equipment data at their finger tips. Make smart and intelligent decisions to keep work moving.
- Breakdowns Reported, Criticality Indicator & Annual Cost of Maintenance.
- Warranty & Manufacturer details.
- Manufacturer Part Information & Google Search.
- Historical maintenance activities & reports.
- Easy access to Documentation, Pictures and Videos.
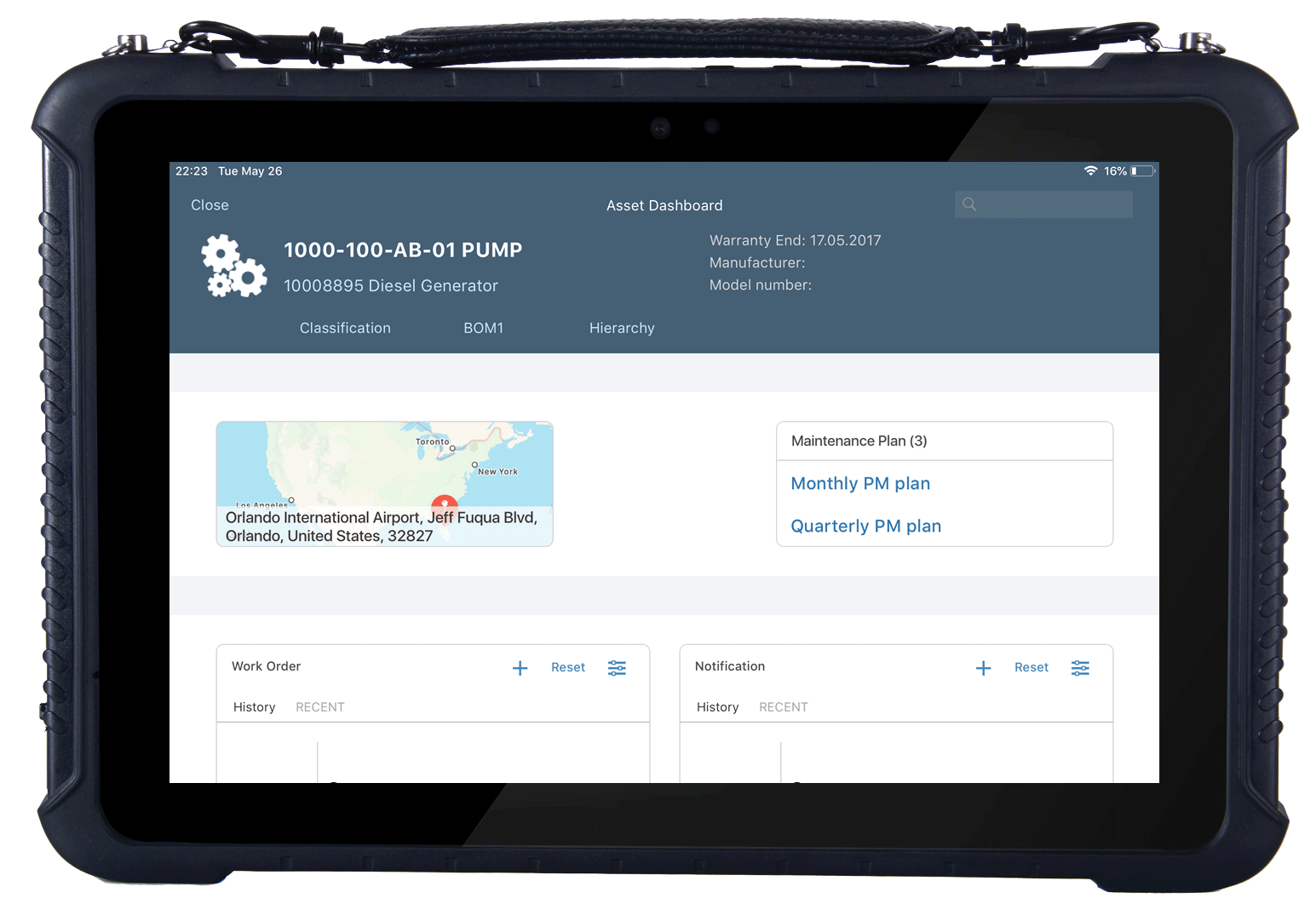
Auto Time Capture
Capturing accurate wrench time has been a burning challenge for maintenance managers & executives. The Auto Time Capture feature allows the technician to track time at an operations level.
- Start, pause & end the auto time feature on an operation.
- Accurate time capture & post to SAP Work Orders or CATS time sheet.
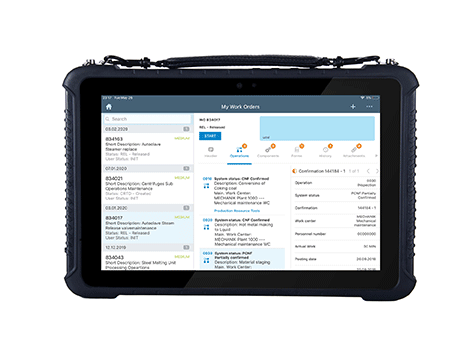
Embedded Work Instructions, Safety & Compliance Checklists
Make use of a digital library of 150+ prepackaged work instructions, inspections, compliance & safety procedures. Use forms as-is or reconfigure as needed, make changes to suit your specific needs & submit in SAP & IBM Maximo Notifications & Work Orders.
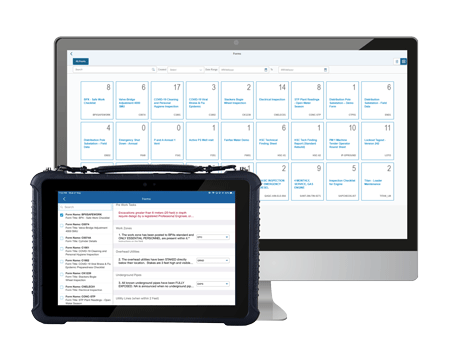
View Functional Location & Equipment Hierarchy
Drill down from a functional location into an Equipment Hierarchy and locate a specific Bill of Materials (BOM).
- View Functional Location Hierarchy.
- View Equipment Hierarchy.
- View Bill of materials & spare parts necessary to get the job done faster, better & safer.
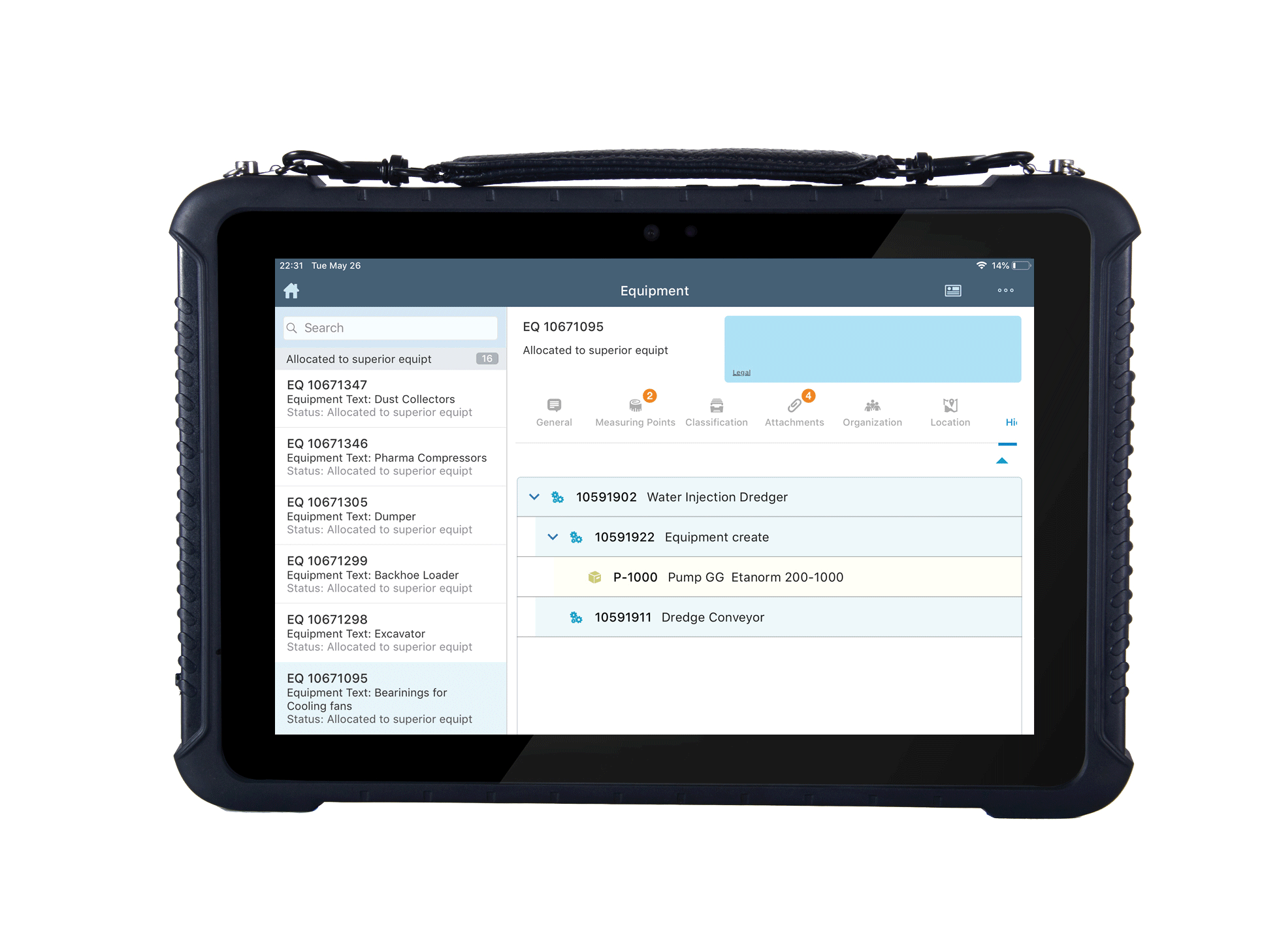
Capture & Annotate Images, Videos, PDFs & More
Graphically annotate documents & images attached to Work Orders, Notifications, Equipment, Functional Locations & other maintenance components.
- Add notes, call outs, arrows and shapes to highlight important content.
- Add a digital signature where tracking & approvals are required.
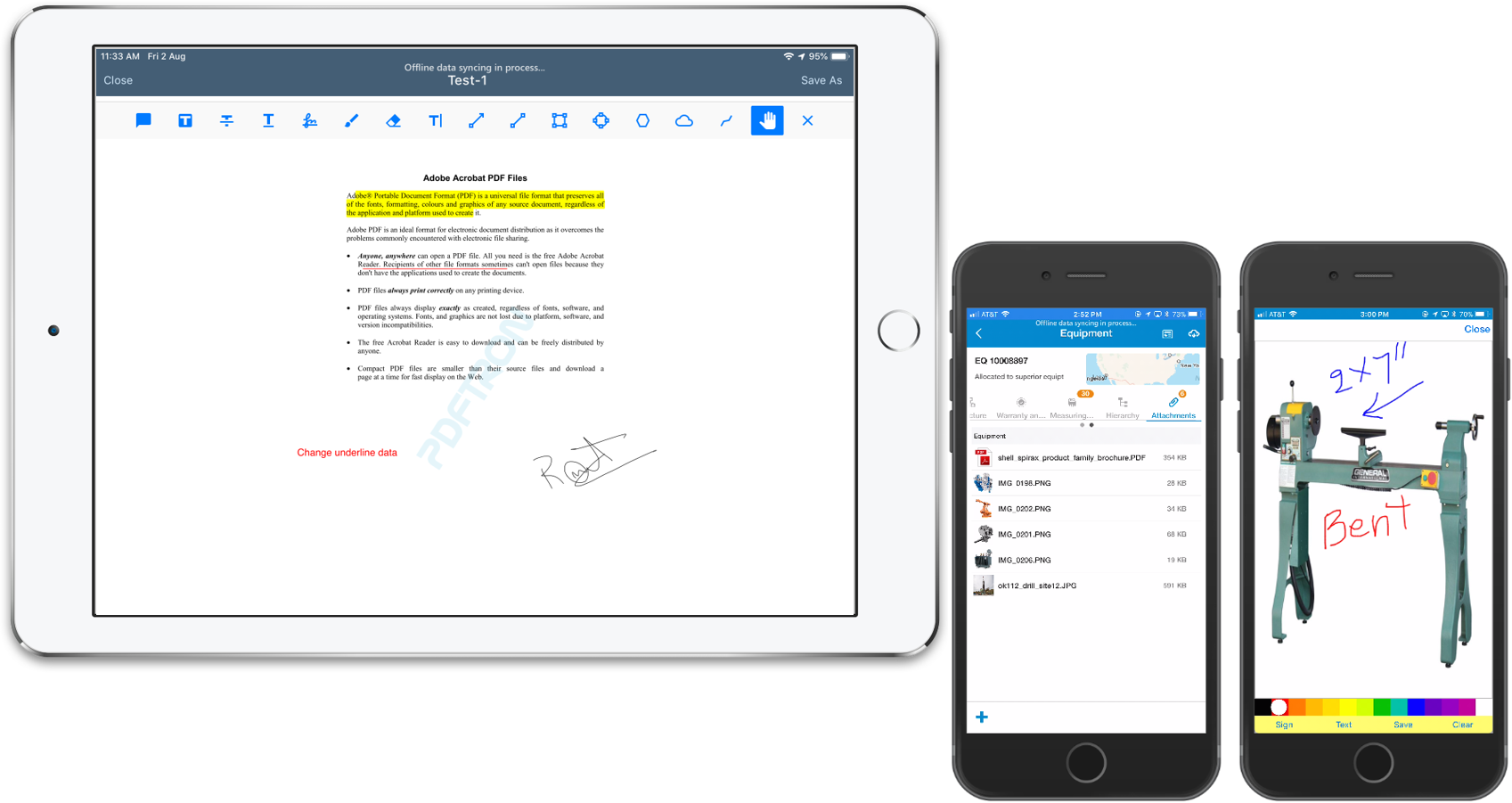
Remote Guided Work Instructions & Assistance via Smart Glasses
- Remote guided assistance is a hands-free collaboration and tele-presence for front-line workers.
- Enable front-line workers in the field to get assistance from experienced technicians.
- Enhanced two-way video call experience where the expert can remotely see and hear from the worker’s point of view.
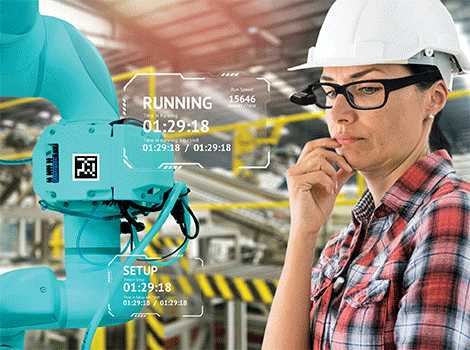
Configurable Dashboard
Personalize Connected Worker experiences by user personas, sites, plants & geographies. Simple and easy-to-use personalization helps the Connected Worker get the job done faster, better, cheaper & safer.
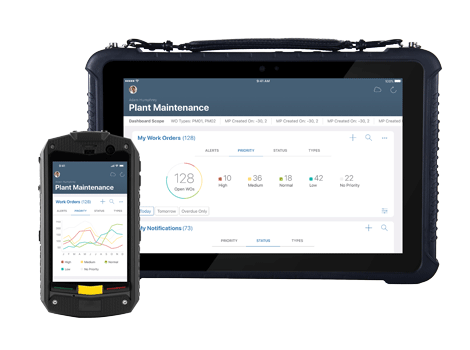
Optical Character Recognition (OCR)
Recognizes text & numeric information & digitizes it during the data capture process in a second. No barcode necessary.
- Capture equipment identifiers, numeric meter readings, paper document content & more.
- Embedded in search screens, object lists and forms - anywhere data capture is required.
-2.png)
Configurable Risk Matrix
Prioritize Maintenance Work Orders based on the Risk Profile of all equipment throughout the facility.
- Use risk information to prioritize Notifications & Work Orders.
- Factors include severity, likelihood & duration.
- Embed risk and safety measures information in safety plan section of work orders.
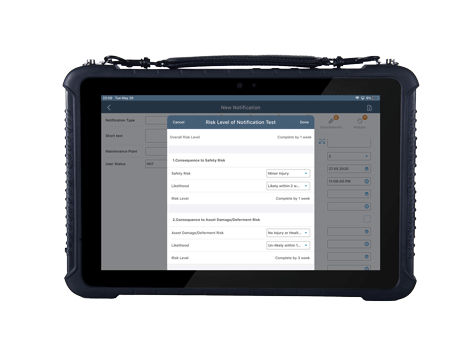
Geographical Information Spatial (GIS) Integration
Integrate any GIS - such as ESRI or GE Small World - with SAP and IBM Business Objects (Work Orders, Notifications, Equipment, Functional Location) & guided step-by-step work instructions, inspections & compliance forms.
-Integration%20(1).gif)
Improved Maintenance Execution KPIs
Increase Wrench Time
20%
Gain productivity by eliminating paperwork
Reduce Safety Incidents
40%
Standardize work and prevent accidents
Reduce Work Backlog
50%
Simplify work planning and execution
Increase Asset Uptime
>98%
Eliminate Preventable Failures
What our customers say
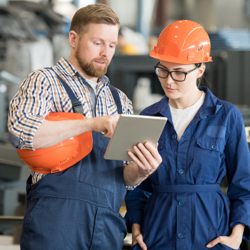
Mobile work orders have streamlined our process, reducing time to get paperwork from the field from many days to within minutes. It’s amazing, a great team, great teamwork and a great process improvement using the Innovapptive Connected Maintenance Execution solution. A win for our customers.
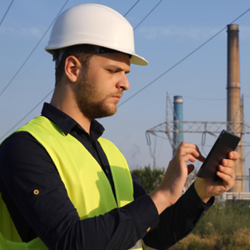
Post-Innovapptive, we have dramatically reduced our maintenance backlogs and improved our worker capacity by 12%. This is a direct savings of $10M/year we are experiencing after implementing Innovapptive.
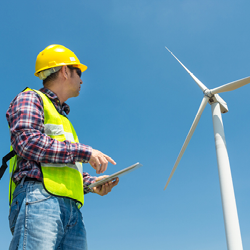
Innovapptive’s Connected Maintenance Execution solution has played a significant role in transforming how we approach maintenance, productivity, data analysis and decision making. We have the solution currently deployed to various locations across Europe and have plans to continue to significantly expand its use. We have experienced a substantial reduction in maintenance backlogs, seen a huge spike in overall productivity and continue to realize operational cost savings due to the visibility and access the solution continues to provide. - Business Manager
Resources
FAQs
What is Mobile Plant Maintenance, and how does it enhance asset management?
- Mobile Plant Maintenance is a mobile work order management solution that connects floor- or field-based technicians to management and back-office systems, streamlining work order assignment, tracking, resolution, and reporting. It mobilizes workers, automates processes, and bridges informational gaps to increase productivity, ensure safety, and maintain compliance.
How does Mobile Plant Maintenance integrate with SAP systems?
- Mobile Plant Maintenance is an SAP-certified mobile solution that offers out-of-the-box integration with the SAP Plant Maintenance Module, ensuring seamless data synchronization and process alignment.
What are the key features of Mobile Plant Maintenance?
- SAP certification for seamless integration.
- Compatibility with iOS, Android, Windows, and SAP Fiori launchpad.
- User-friendly interface to boost productivity.
- Data and business process validations.
- GIS integration for spatial analysis.
- Full offline capabilities for uninterrupted operations.
- Industry-specific customization through RACE™.
How does Mobile Plant Maintenance improve maintenance efficiency?
By digitizing work orders and automating workflows, mobile Plant Maintenance reduces manual data entry, minimizes errors, and accelerates maintenance processes, leading to increased wrench time and reduced downtime.
Can Mobile Plant Maintenance be customized to specific business needs?
- Yes, with the Rapid App Configurator Engine (RACE™), users can reconfigure and customize electronic forms, such as operator rounds checklists or safety reports, without coding, ensuring the solution aligns with unique operational requirements.
What types of organizations benefit most from Mobile Plant Maintenance?
- Asset-intensive industries using SAP® as their enterprise resource planning (ERP) system, including oil & gas, utilities, chemicals, mining & metals, and manufacturing, can significantly benefit from implementing Mobile Plant Maintenance.
How does Mobile Plant Maintenance support compliance and safety?
- The solution enables the creation and management of digital inspections, safety checklists, and compliance forms, ensuring that all regulatory requirements are met and safety protocols are consistently followed across the enterprise.
What results can organizations expect after implementing Mobile Plant Maintenance?
- Organizations have reported up to a 90% reduction in unplanned downtime, 26% lower maintenance costs, 40% fewer safety incidents, and a 50% increase in workforce capacity after adopting Mobile Plant Maintenance.
Is Mobile Plant Maintenance compatible with various devices and platforms?
Yes, the solution is truly device and platform agnostic, offering full native support on iOS, Android, Windows, and browser access through SAP Fiori launchpad, ensuring flexibility and ease of use across different devices.
How does Mobile Plant Maintenance handle offline scenarios?
Mobile Plant Maintenance offers full offline capabilities, allowing field technicians to continue working without network connectivity. Data is synchronized automatically once connectivity is restored, ensuring seamless operations.
Since the start of the project we have been nothing but pleased with the quality of the service we've received from Innovapptive. The whole team from the sales team to the project team have been nothing but supportive
I'd say Innovapptive for us has been a reliable product. It was easy to implement, the service has been good. So I would recommend checking them out if you're looking for some help with your workflow.
We hadn’t had much luck with mobile plant maintenance solutions in the past. Our frontline maintenance technicians didn’t want to use them because of poor UI/UX. They’d rather use paper, meaning we received a poor return on investment and achieved none of our operational objectives.