Innovapptive’s New Connected Worker Platform Delivers End-to-End Asset Management Visibility Within ERPs to Empower Frontline Workers
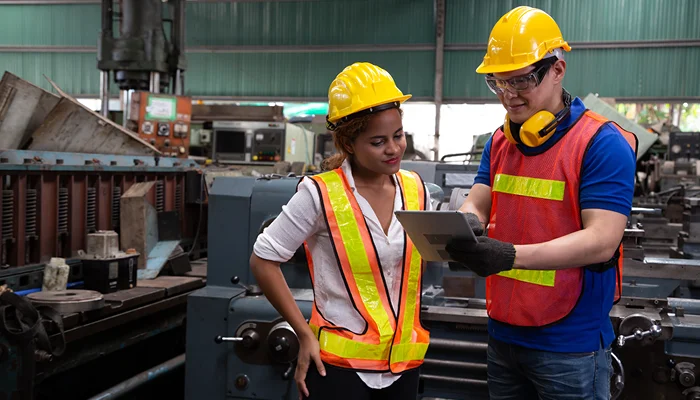
HOUSTON – Innovapptive, a digital transformation leader, announced today that it is launching its Connected Worker Platform that serves the needs of companies undergoing a digital transformation of their asset maintenance operations. The platform enables users to draw intelligent insights about operational inefficiencies and bottlenecks as well as enables seamless collaboration among maintenance and warehouse workers. Using the Connected Worker Platform gives decision-makers the real-time visibility they need to make informed choices towards eliminating workflow problems and boosting frontline worker productivity.
Innovapptive’s Connected Worker platform is the next logical step in the evolution of mobile frontline worker applications, greatly increasing departmental collaboration and process control. Companies using the platform gain additional clarity and flexibility to address maintenance work order and parts warehouse bottlenecks and knowledge gaps. These problems impair frontline worker productivity, delay important projects, wreck budgets and tighten critical profit margins.
“Our Connected Worker Platform helps asset-intensive organizations realize the full benefit of their back-office ERP and empowers frontline workers to do their jobs with greater ease and impact, plus stay safe while doing it,” said Innovapptive CEO and co-founder Sundeep Ravande. “Right now, these systems don’t provide needed end-to-end visibility into the maintenance work order and warehouse management arenas. There’s a costly gap in the process. Decision-makers have difficulty connecting the dots between ongoing maintenance work orders and warehouse parts availability. Our solution empowers companies to bridge that knowledge gap and boost productivity in real time.”
Innovapptive’s Connected Worker Platform can operate as a standalone productivity solution but best functions in conjunction with the company’s mWorkOrder and mInventory solutions to provide true end-to-end operational and process visibility.
A use case example illustrates how the product offering works in conjunction with Innovapptive’s mWorkOrder and mInventory eliminate information silos to correct a supply chain bottleneck threatening an important manufacturing plant maintenance project with delays:
A leaky gate valve needs replacement. Failure to replace this valve will keep the production line from restarting, resulting in a shutdown that will stop revenue flows.
A field technician notices that the valve is about to fail and raises a Notification/Work request in the field.
Using the Connected Worker Platform tied into mWorkOrder and mInventory, the plant’s warehouse manager can see the valve situation unfold in real time. She checks inventory and ensures that there are available workers to fulfill the request.
The warehouse manager issues notifications via mInventory to pickers to ready a valve for pickup. She understands the valve’s importance and assigns this order a high priority. The manager can follow order progress at each step of the kitting process as warehouse workers scan the valve’s barcode as it moves along the fulfillment chain.
Meanwhile, the maintenance manager ensures that the right personnel are available to replace the valve. Via his dashboard, he sees a replacement is ready at the warehouse and assigns a technician to pick it up before heading to the repair site, saving time and effort.
Thanks to real-time visibility, digital data sharing and collaboration, the valve is replaced much faster than it would have been using a manual, paper-based process. That method would have caused several critical delays in both the maintenance work order and warehouse parts fulfillment, jeopardizing production and revenues. This situation is avoided using the Connected Worker Platform. Each manager has immediate, real-time access to key information to understand what is happening and make appropriate and knowledge-based decisions.
Visit http://www.innovapptive.
About Innovapptive
Innovapptive is a digital transformation pioneer offering the only Connected Worker Platform that digitalizes the last mile of frontline workers into SAP and IBM Maximo technologies. Our solutions integrate GIS operational data and data from SAP and IBM Maximo solutions with work instructions, SOPs and checklists, connecting the entire industrial workforce, machines, workflows and executives to minimize plant outages and maximize margins. Innovapptive is transforming the experience of the industrial worker by engineering a platform that fuels innovation and collaboration to turn downtime into revenues, risks into safety and inefficiencies into growth. Innovapptive is headquartered in Houston with offices in Australia and India. Learn more at www.innovapptive.com.
###
SAP and other SAP products and services mentioned herein as well as their respective logos are trademarks or registered trademarks of SAP SE in Germany and other countries. Please see https://www.sap.com/copyright for additional trademark information and notices. IBM Maximo Asset Management, Maximo and other IBM products and services mentioned herein as well as their respective logos are trademarks or registered trademarks of IBM Corporation. Please see https://www.ibm.com/legal/copytrade for additional trademark information and notices. All other product and service names mentioned are the trademarks of their respective companies.
Any statements in this release that are not historical facts are forward-looking statements as defined in the U.S. Private Securities Litigation Reform Act of 1995. All forward-looking statements are subject to various risks and uncertainties described in SAP’s filings with the U.S. Securities and Exchange Commission, including its most recent annual report on Form 20-F, that could cause actual results to differ materially from expectations. SAP cautions readers not to place undue reliance on these forward-looking statements which SAP has no obligation to update and which speak only as of their dates.
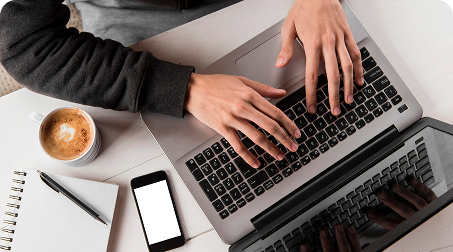
See It In Action
Schedule a personalized demo to see how our solutions can help your business thrive.