Unifying People, Processes & Technology in Real-Time
AI-powered, mobile-first Connected Worker Platform uniting operations, maintenance, warehouse, and safety teams—optimized for cost reduction and peak operational efficiency.
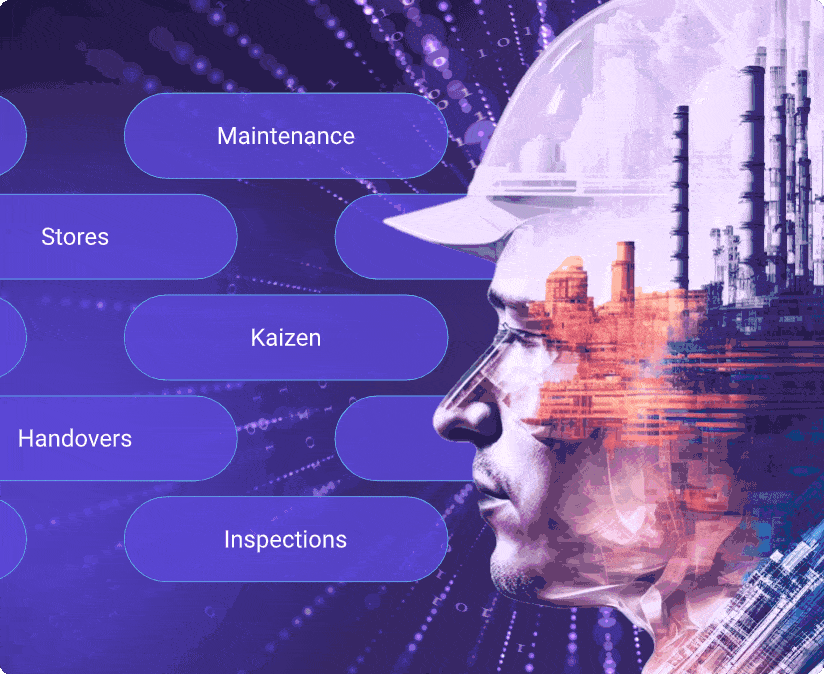
Trusted by Industry Leaders to Drive Operational Efficiency
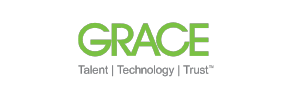
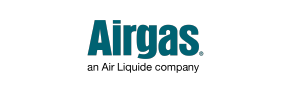
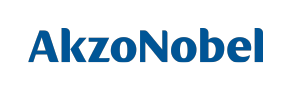
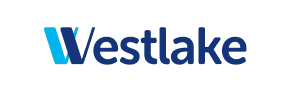
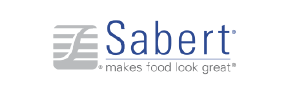
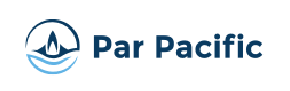
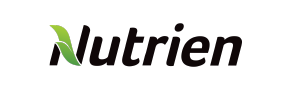
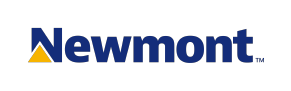
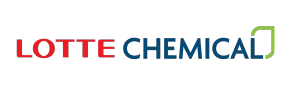
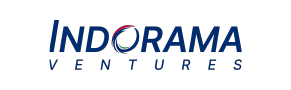
A Unified Platform for Frontline Excellence
Frontline operations are complex, with disconnected teams, siloed systems, and paper-based workflows slowing efficiency. The Connected Worker Platform provides an integrated digital ecosystem that enhances collaboration, improves decision-making, and drives continuous operational improvement with real-time insights.
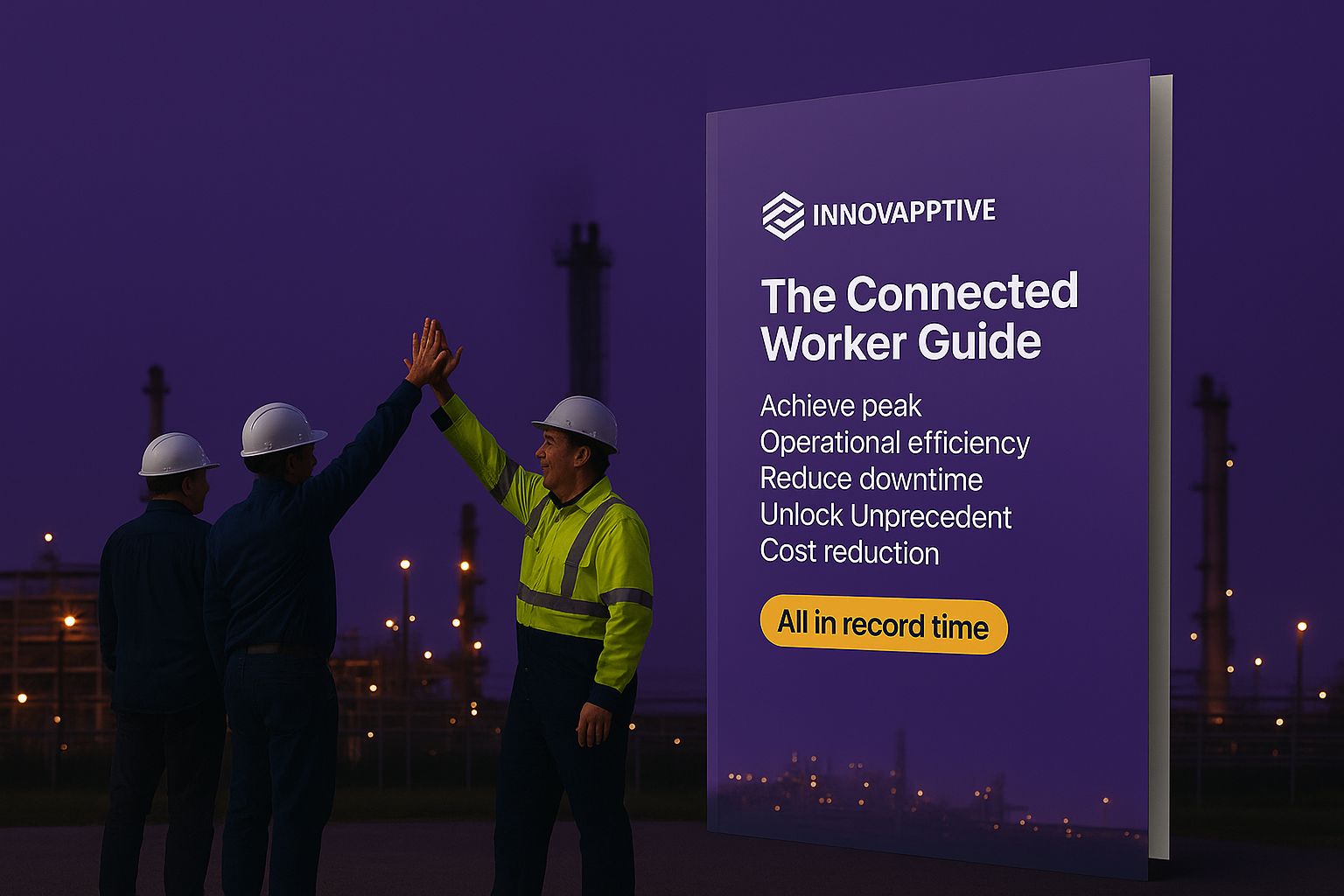
Built for the Frontline. Engineered for Zero Downtime
The Connected Worker Guide is your blueprint to transform frontline operations. Learn how industry leaders are digitizing execution, reducing downtime, and unlocking millions in real, measurable savings.
Grab Your Free CopyOne Platform. Every Shift Maximum Impact.
The Connected Worker Platform serves as the central hub for operations, maintenance, warehouse, safety, and continuous improvement, driving efficiency across all teams.

Digital Leaders
Drive Innovation & 15X ROI with AI-Powered Digital Transformation
- Seamless Enterprise Integration – Connect operations, maintenance, and warehouse with ERP, EAM & IoT.
- 10-15x ROI Guaranteed – Speed up processes, cut costs with intelligent automation.

Plant Managers
Reduce Unplanned Downtime by 30% & Optimize Production Efficiency
- Predictive Maintenance – AI detects early failures to prevent costly breakdowns.
- Live OEE Tracking – Monitor efficiency and eliminate production bottlenecks.

Operations Leaders
Reduce Compliance Fines by 75% & Improve Proactive Maintenance
- #1 Operator Round Solution – Streamline inspections and routine checks with AI-driven workflows.
- Industry’s Only Automated Shift Handover Report – Eliminate data gaps with structured, AI-generated reports.

Maintenance Leaders
Cut Breakdowns by 50% & Increase Wrench Time with AI-Driven Autonomous Maintenance.
- AI-Powered Failure Prediction – Detects issues before they cause breakdowns.
- Connected ERP & IoT Integrations – Sync with SAP, Maximo, and sensors for proactive maintenance insights.

Reliability Managers
Optimize Asset Performance & Improve Process Reliability by 25%
- AI-Driven Root Cause Analysis – Identify and resolve inefficiencies faster.
- Live KPI Dashboards – Gain real-time insights into process performance.

CIOs & IT Leaders
Accelerate Enterprise-Wide AI & No-Code Automation for 15X ROI
- Enterprise-Wide Integrations – Connect SAP, Maximo, IoT, and other key systems seamlessly.
- Real-Time Operational KPI Tracking – Deliver actionable insights for business teams.
- Scalable No-Code Automation – Reduce IT dependency and accelerate digital transformation.
Unlock a Proven Path to $30M+ EBITDA Gains
Top Industries leaders has achieved measurable EBITDA improvements using our Connected Worker Platform. You can too.
-
Reduce Downtime Costs – Early detection of equipment issues leads to fewer outages and production losses.
-
Improve Wrench Time – Mobile-enabled maintenance reduces admin overhead and improves actual time-on-tools.
-
Optimize MRO Spend – Eliminate excess inventory and stockouts with real-time tracking and usage analytics.
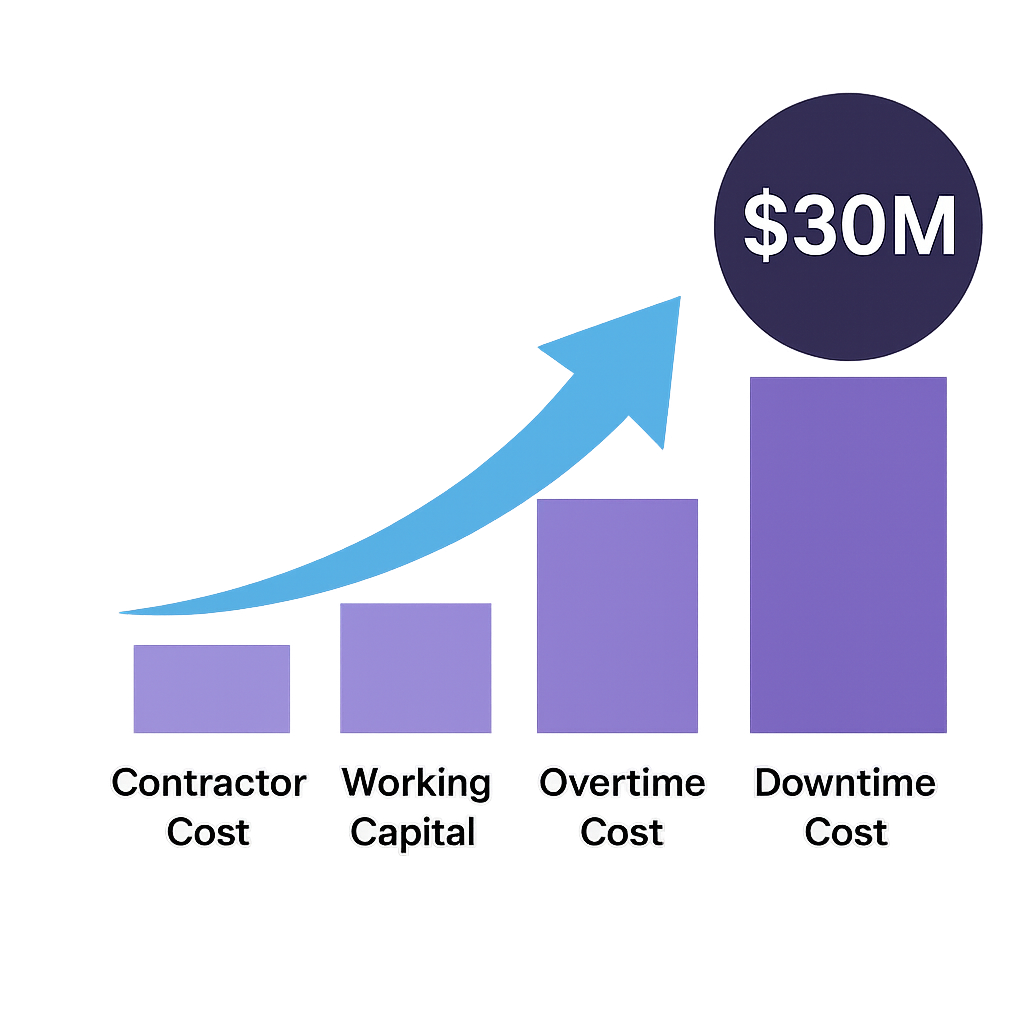
A Single Pane of Glass That Powers a Unified Experience
No more paper. No more silos. From Maintenance and Operations to Warehouse, EHS, and Quality, digitize every frontline workflow with a single mobile experience.
-
Consumer-Grade UX – Intuitive interface requires minimal training across roles—from operators to contractors
-
50+ Prebuilt Integrations – Instantly connect to SAP, Maximo, Oracle, Historians, EHS, and more.
-
Interactive SOPs & Work Instructions – Digital, step-by-step guidance ensures execution accuracy.
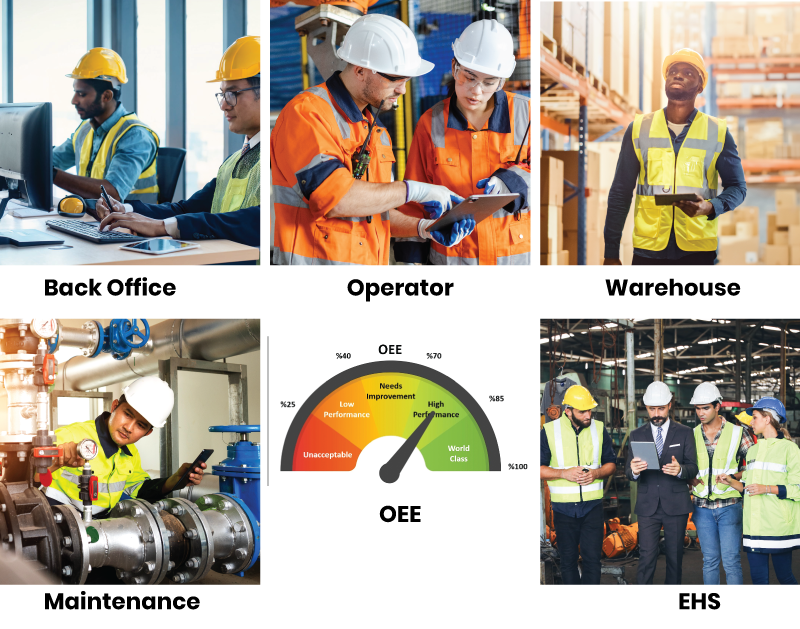
15+ AI Agents That Cut Downtime
AI Agents Built to Eliminate Downtime and Lower Maintenance Costs
-
Stay ahead of failures: Our AI Agents use predictive analytics to anticipate breakdowns before they happen, helping you cut unplanned downtime and costly disruptions.
-
Empower every worker: With natural language and computer vision capabilities, frontline teams can interact conversationally and visually — making inspections faster, smarter, and error-free.
-
See the full picture, act faster: Seamless integration with SAP, Maximo, and other systems gives you real-time visibility and AI-driven insights across your entire maintenance landscape.
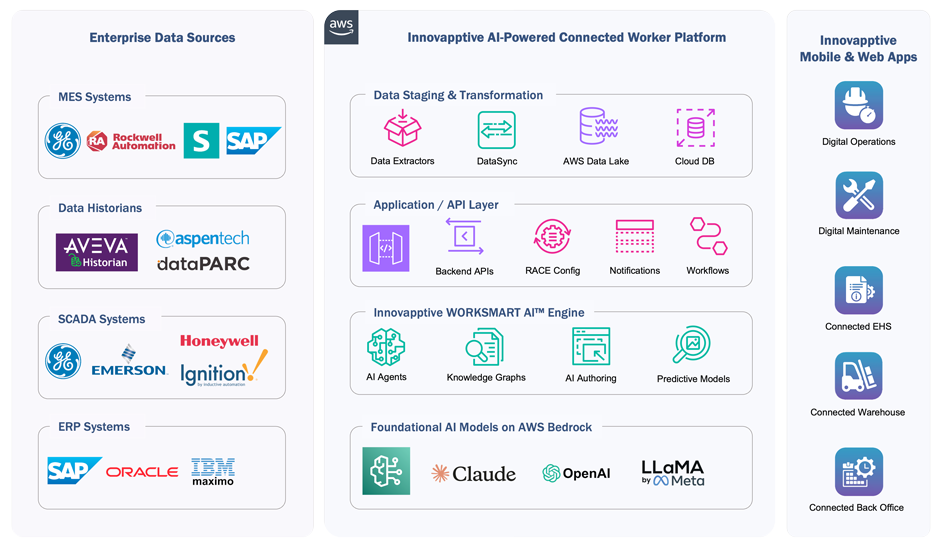
Why Process & Discrete Manufacturing have Unique Connected Worker Needs
-
Process Industries
(Oil & Gas, Chemicals, Pharmaceuticals, Mining, etc.)
-
-
Discrete Industries
(Automotive, Electronics, Industrial Equipment, Food & Beverage, etc.)
-
- Hazardous operations
- Formula-based manufacturing
-
Nature of Operations
-
- Batch-based assembly
- Component-driven production
-
- Permits, shift handovers & safety
- Sustainability & compliance tracking
-
Connected Workforce Priorities
-
- Skill management & digital work instructions
- Defect tracking & quality assurance
-
- Reduced unplanned downtime
- Improved safety compliance
- Higher production efficiency
-
Key Success Metrics
-
- Faster production cycles
- Lower defect rates
- Improved workforce efficiency
Built for real-world grit. Proven across the world’s most demanding industries.
Maximize Your Team’s Potential with One Connected Platform
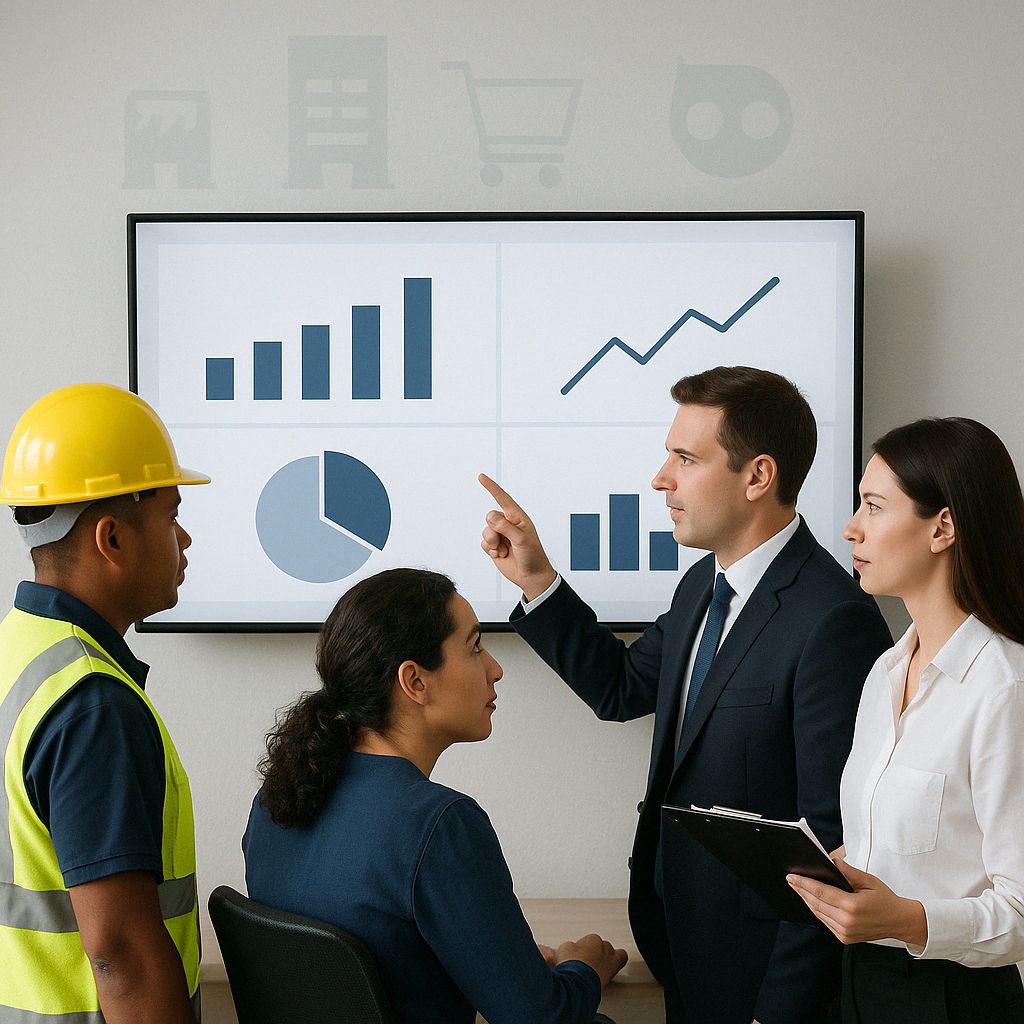
Single Pane of Glass
A single platform for operations, maintenance, storerooms, safety, and quality teams—offering a unified experience, consistent workflows, and cross-functional visibility.
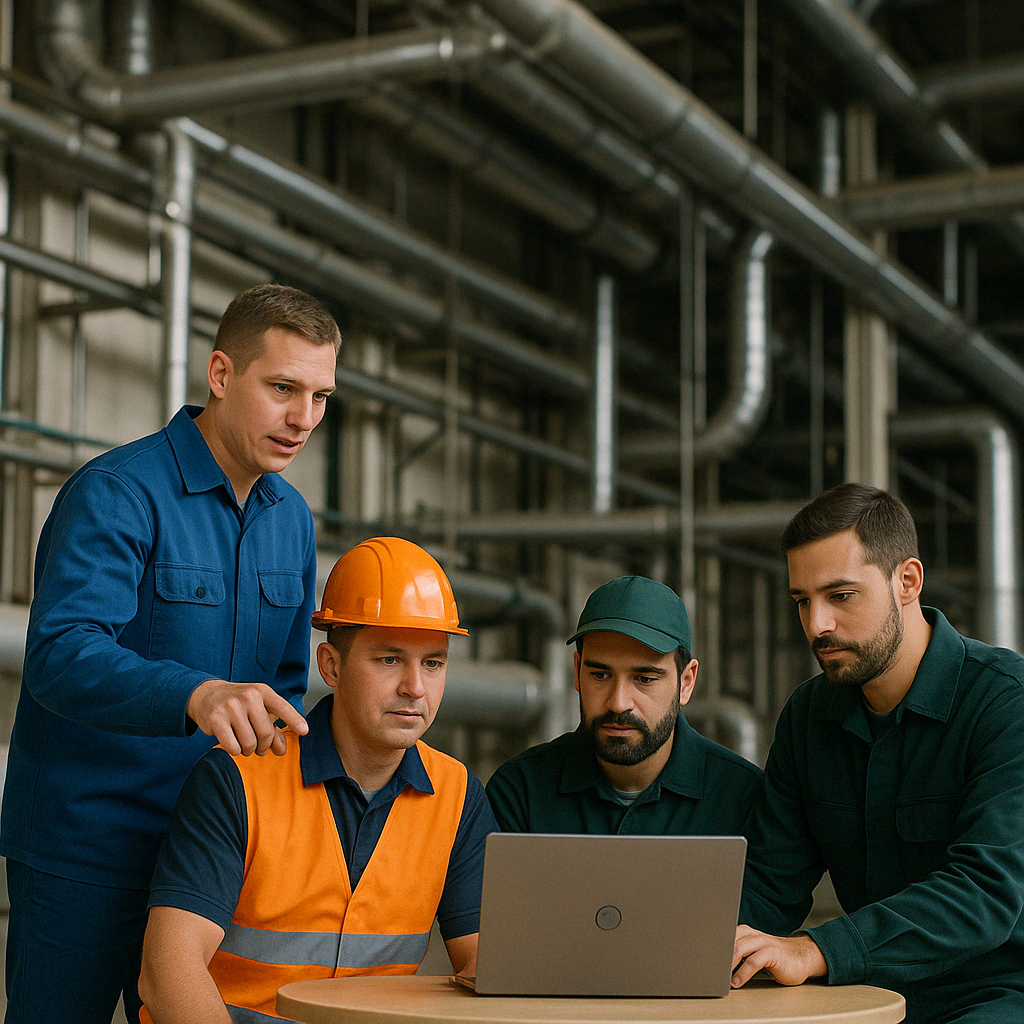
How Work Gets Done
Seamless cross-functional workflows that unify the value chain—from planning through execution to analysis—for real-time collaboration and faster outcomes.
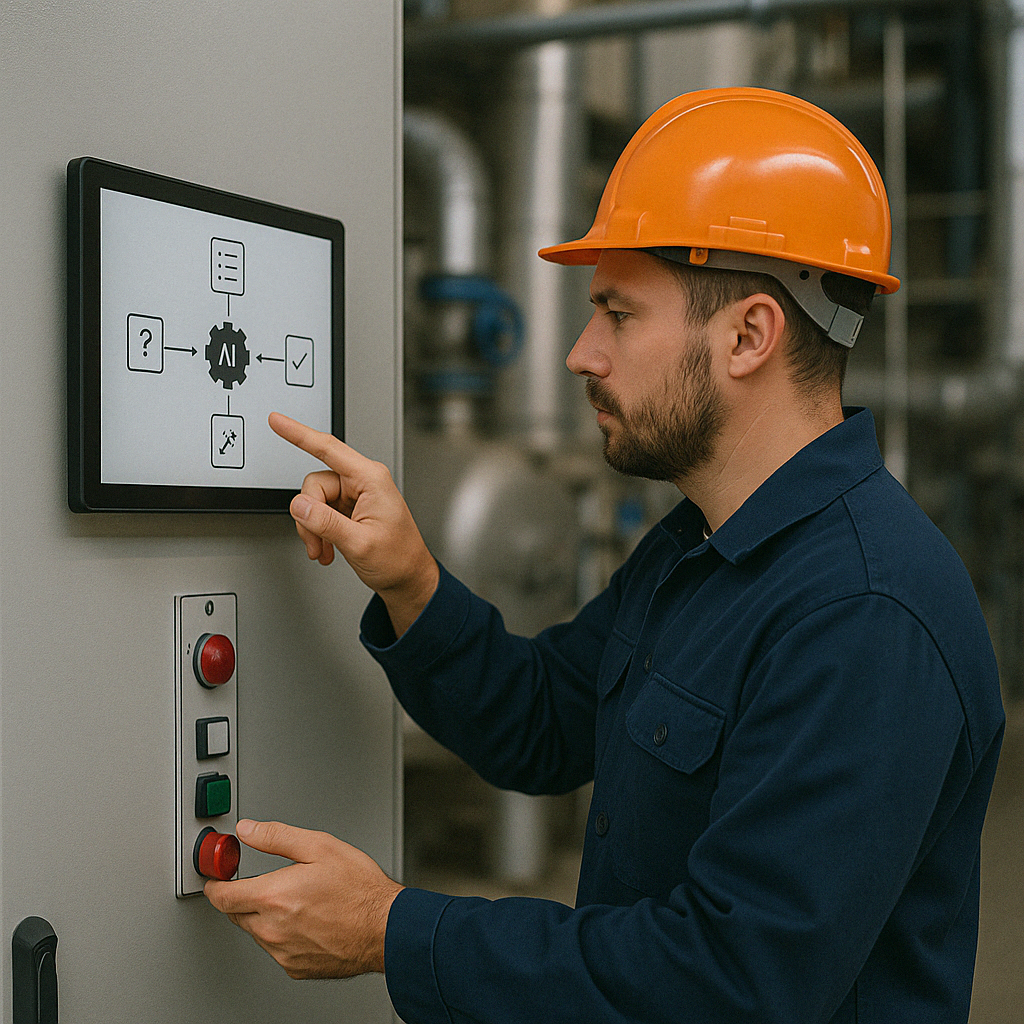
AI Autonomous Workflows
AI that eliminates manual work by automating routine tasks and guiding teams through RCA, 5-Why analysis, and on-the-spot troubleshooting.
Unlock Measurable Operational Impact Today
-
%
Boost in Operational Efficiency
-
%
Reduction in Unplanned Downtime
-
%
Improvement in Cost Savings
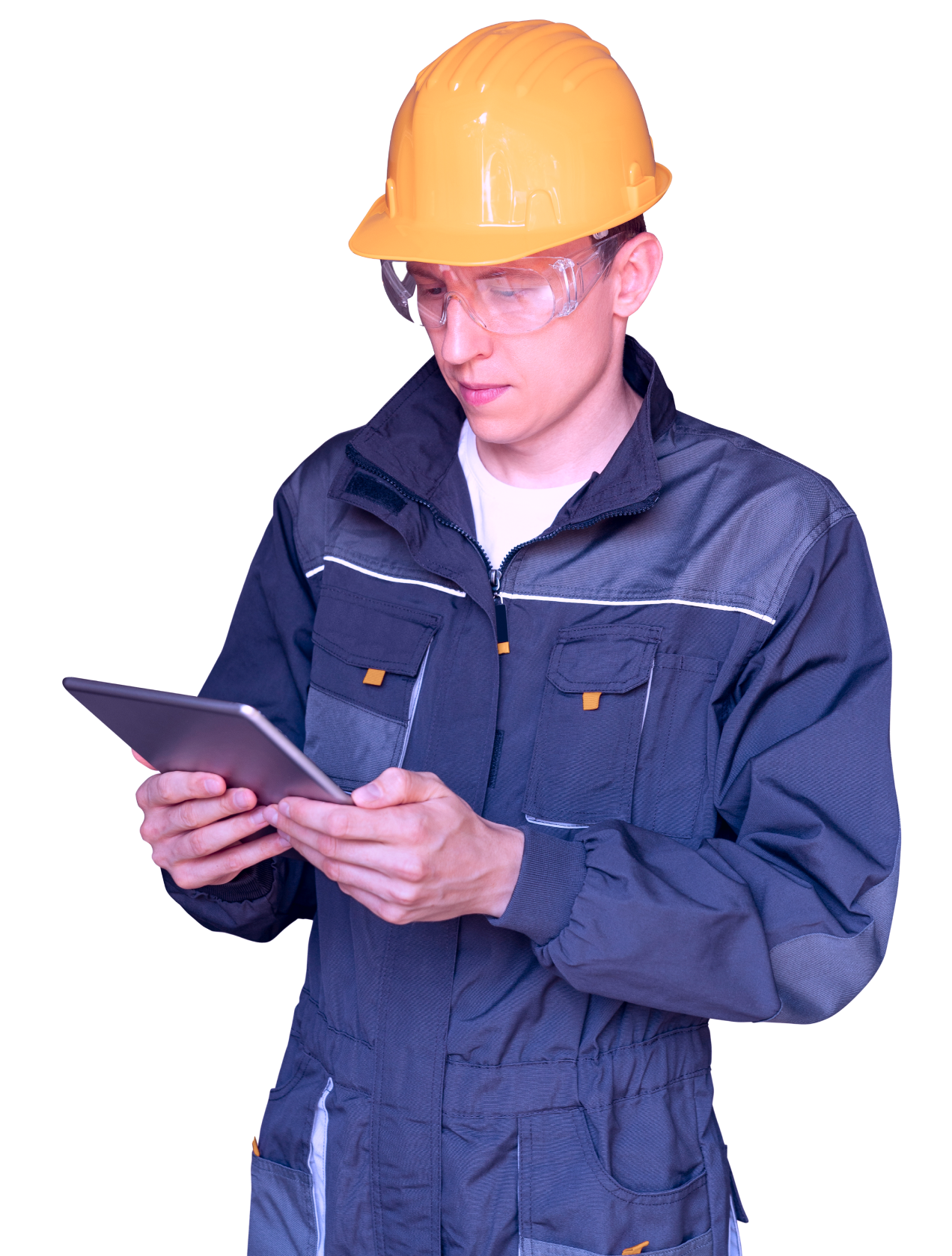
Everything You Need to Know
What is a Connected Worker Platform?
What industries does Innovapptive’s Connected Worker Platform support?
Innovapptive serves process and discrete industries, including:
- Oil & Gas, Chemicals, and Mining (Process Manufacturing Software)
- Automotive, Electronics, and Industrial Equipment (Connected Worker Manufacturing)
- Pharmaceuticals and Food & Beverage (Regulated Industries)
How is Innovapptive leveraging AI to transform frontline work?
Innovapptive is an AI-first platform, built to reduce unplanned downtime with 15+ AI Agents tailored for frontline workers. These AI capabilities allow workers to click and move forward with tasks effortlessly by:
- Detecting issues before failures occur
- Auto-packaging work orders & streamlining workflows
- Performing root cause analysis (RCA) instantly
- Providing real-time analytics & actionable insights
- Enhancing decision-making with AI-powered automation
- Want to see it in action? Explore [WorkSmartAI] now!
Does Innovapptive’s platform replace existing ERP systems like SAP?
How does Innovapptive improve workforce efficiency and productivity?
How does Innovapptive ensure compliance and safety in hazardous industries?
How can I see Innovapptive’s platform in action?
Read Our Latest Blogs Curated by Industry Experts
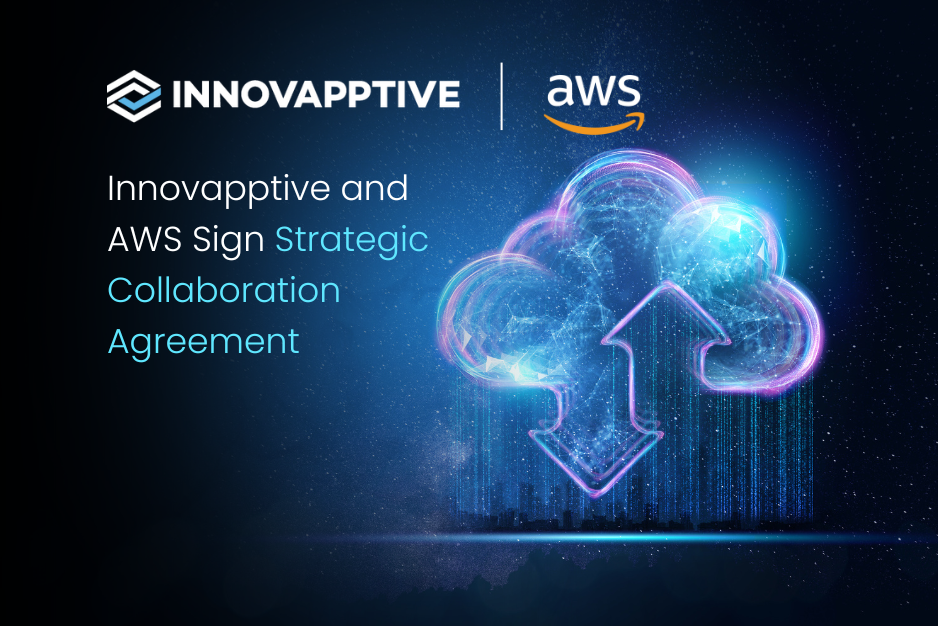
- 20-08-2025
Building the future of Industrial Operations with Innovapptive and AWS
Most manufacturers have already gone digital. Yet business outcomes haven’t moved in step. Many Connected Worker tools simply extend ERP interfaces to mobile devices. They digitize tasks but don’t fix how the work flows between operations, maintenance, safety, and inventory. Each team ends up in its own application. Data gets stuck. Outcomes stay flat. These “extender solutions” support individual roles in isolation, not the plant as a whole. So the core problems, contractor overuse, low ...
Read More