5 Reasons Why Mobile Work Orders Should Replace Paper-Based Processes – Especially in a Coronavirus World
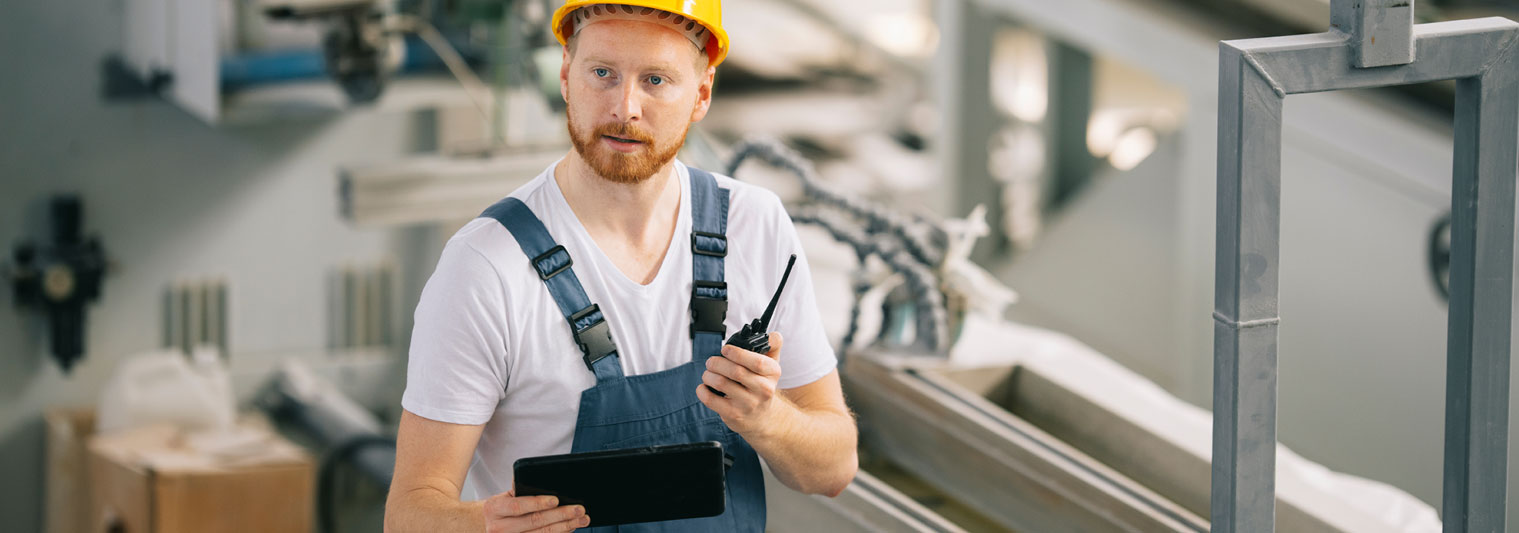
Change is the only constant in industrialized societies. For example, just a few short weeks ago, the coronavirus was a minor story, taking place in a far-off land. That certainly has changed. From a small outbreak of 44 people in Wuhan, China, COVID-19 has exploded into a global pandemic. This pandemic has brought the world economy to a near halt, closing industries deemed “non-essential” and suddenly throwing millions of people out of work.
The pandemic has also caused many companies to examine their operations not only in an effort to survive the pandemic-related shutdown, but to also better protect employees from infection while they work. One way to do that is to replace paper-based maintenance work order processes with digital ones. Before the pandemic, an ever-increasing number of companies were moving in that direction, but many others still lag behind.
A recent Dell Technologies survey found 78 percent of companies questioned felt digital transformation should be more widespread in their organizations. One in four felt they were unprepared for the pace of change.
Digital transformation technologies provide companies more employee safety (a critical factor in the age of COVID-19), as well as greater agility, flexibility and options to respond to maintenance and issues before they cause production shutdowns. Maintenance work order management is a critical operational function where mobile-first digital transformation technologies can make a quick and meaningful impact on safety, compliance, efficiency, productivity and cost control. Let’s take a closer look at each of these:
1. Keeping Maintenance Workers Safe from COVID-19Paper-based maintenance processes have a negative drawback: They put workers at greater risk of infection. Recent research in the American Journal of Nursing suggests that test organisms that were transferred onto paper survived on it for a considerable time. If someone were to later touch the contaminated paper containing the virus, it could be transferred to that person’s hands, raising the risks of passing on the coronavirus and contributing to the COVID-19 pandemic spread.
Using a mobile-first, digital work order management system rather than paper means employees will not have to handle risky paper forms. They perform all work and data collection electronically using mobile hand-held devices. This enables them to minimize interactions and practice safe “social distancing” protocols.
In the coronavirus era, companies must safeguard workers’ health to ensure they have enough staff to perform needed maintenance activities in a timely manner. Eliminating paper, then, is an obvious choice to increase efficiency, reduce costs and protect workers.
2. Stay Regulatory Compliant
Industrial plants and facilities constantly strive to remain in compliance with ever changing environmental and safety laws and regulations. Failure to do so could result in not only stiff fines, penalties and potential lawsuits; it also may injure employees and hurt worker morale. Mobile-first digital work order management systems can play an important role in ensuring plants remain in compliance. They enable quick, accurate and thorough inspections and risk assessments to identify and alert key decision makers to issues before they become costly problems. We used our patented platform – The Rapid Application Configuration Engine, or “RACETM” – to develop four use cases that combine worker environment, health and safety (EHS) with operations. These use cases can be reconfigured to dynamic and constantly evolving public health regulation guidelines from OSHA, CDC, MSHA, WHO, etc.
Innovapptive has developed several examples and videos on how you can embrace public health regulation guidelines, practice “social distancing” and reduce the risk of COVID-19 disease spread across your workforce:
- COVID-19 Work Order Execution and Job Safety Instructions – Derived from the CDC’s COVID-19 Preparedness Assessment Test, this checklist mandates technicians complete the coronavirus testing protocol before beginning any work order. This ensures workers don’t take unnecessary risks and remain compliant with health and safety procedures. View a video here.
- COVID-19 Site and Environment Risk Assessment – Conduct regular and thorough risk assessment exercises to determine your organization’s vulnerability to COVID-19. Rank risks by severity and likeliness of occurring, enabling decision makers to take prompt and appropriate action. View a video here.
- COVID-19 Safety Inspection Checklist – Develop and implement a response plan to promote personal protection and social distancing. Ensure your company has taken all needed preventative measures to safeguard workers and stop the spread of COVID-19. View a video here.
- COVID-19 Site Preparedness – Identify specific tasks you can perform today to prepare for, respond to and remain vigilant in the face of the COVID-19 pandemic, or any other public health threat. View a video here.
RACE Dynamic Forms is an exclusive Innovapptive solution. No one else offers a highly configurable, code-free digital forms application. This sets Innovapptive apart and is the true differentiator between it and other digital transformation platforms.
3. Enhance workforce productivityCompiling, issuing, tracking and filing paper-based work orders are repetitive and labor-intensive tasks. Technicians manually collect data in the field and bring those papers back to the office to upload it into the back-office system of record (such as SAP or IBM Maximo). This manual data entry process increases the risk of human error and inaccuracy. It also results in higher administrative costs.
A mobile work order management solution that is integrated with digital forms and checklists can be a time savior and productivity booster. Such tools enable technicians to digitally collect field-data without any manual entry and automatically upload them into the system of record in real time. Real-time data availability lets maintenance managers make informed decisions based on verified field data to achieve higher operational efficiencies.
4. Better conflict managementPaper-based processes and legacy systems provide fertile ground for conflicting maintenance activities. Conflicts stem from communication gaps, overlap in work assignments and ambiguities. For example, a technician receives a work order and arrives in the field only to realize that there’s already been another technician executing the same work order, preventing a wasted trip and an unproductive use of time that could have been utilized elsewhere.
Mobile-first digital work order solutions deliver real-time visibility into plant operations and maintenance. Maintenance managers can prioritize work orders and effectively assign resources.
5. Bridge knowledge gapsKnowledge gaps among maintenance technicians are continuously growing as new technologies, equipment, machinery and tools arrive. As a result, maintenance managers are facing challenges in balancing system operations and resource planning.
Equipment upgrades and modifications are an important and ongoing mission at industrial plants. So, updated product and maintenance manuals should be made available for the technicians. Printed manuals are highly susceptible to wear and tear, resulting in missing pages or worse, having the entire manual get misplaced or lost. Digital transformation offers a way for these manuals to be converted into PDFs and made easily accessible by technicians in the field via mobile devices.
Paper-based work orders, meanwhile, too often rely on maintenance managers’ and technicians’ experience, training, knowledge, intuition and memory rather than verified data to diagnose problems, prioritize jobs and assign staff. This process jeopardizes critical assets and technicians who work on them at risk.
The knowledge-gap risks with printed manuals and paper-based work orders show why businesses should consider joining the digital transformation revolution and adopt mobile-first work-order management solutions.
Introducing mWorkOrder – a highly configurable, mobile-first maintenance solution
Innovapptive’s mWorkOrder solution gives plants an agile, flexible way to address employee safety, operational efficiency challenges, increase productivity and reduce costs. mWorkOrder supports preventive and predictive maintenance strategies that lets plant maintenance teams move away from the inefficient and reactive “run-to-fail” approach.
Workers using mobile devices such as smartphones, scanners, tablets, wearables and drones fulfill maintenance work order repairs and perform inspections, operator rounds, equipment checks, etc. collecting performance data. With these devices, completed work orders are instantly uploaded to the back-office system of record. This boosts wrench time by eliminating the need to manually input data from paper forms. It also cuts administrative costs.
mWorkOrder increases communication between field technicians and supervisors. Supervisors instantly receive work orders as they are completed, and they can send push notifications to their employees’ mobile devices to notify them immediately of important tasks or other key information.
What differentiates mWorkOrder is its ability to integrate with RACETM Dynamic Forms.
RACE Dynamic Forms, working in conjunction with mWorkOrder, allows super users such as maintenance managers to create or edit role-based forms and COVID-19 checklists on the fly in 30 minutes of less. The solution is intuitive and easy to use; no coding experience is required. This video gives a look at the power and versatility mWorkOrder and RACE Dynamic Forms offer.
The result is a total transformation of your operations:
- Real-time digital updates have replaced the cumbersome manual paper process,
- Decision makers have gained greater visibility into the maintenance program,
- Wrench time has been increased,
- Workers are better protected from the coronavirus,
- Compliance and safety regulations have been met,
- Problems have been documented and electronically stored, providing a valuable history to help spot current and future risk trends,
To learn more about mWorkOrder and RACE Dynamic Forms, click here to schedule a free demo or call us at 844-464 6668. Our experts are standing by to introduce how digitally transforming your risk assessment can turn a business challenge into an advantage.
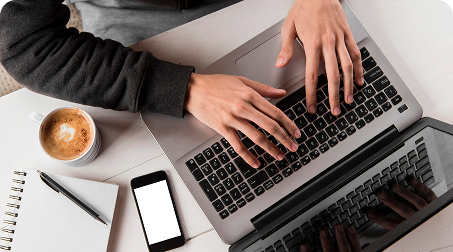
See It In Action
Schedule a personalized demo to see how our solutions can help your business thrive.
- 22-04-2025
The $3.6B Unlock: Solving the Chemical Industry’s Labor Crisis and EBITDA Pressure in One Move
“Constraints don’t slow innovation—they force it.”
- 21-04-2025
Chemical Industry's Margin Erosion: A Wake-Up Call for Operational Efficiency Amid China's Oversupply
The global chemical industry is facing mounting challenges, with revenue declines and shrinking...
- 21-04-2025
Why Wrench Time Isn’t Improving: The Hidden Costs of Traditional Maintenance Scheduling
For years, industrial leaders have relied on a common but flawed assumption: "Better planning and...