Why Wrench Time Isn’t Improving: The Hidden Costs of Traditional Maintenance Scheduling
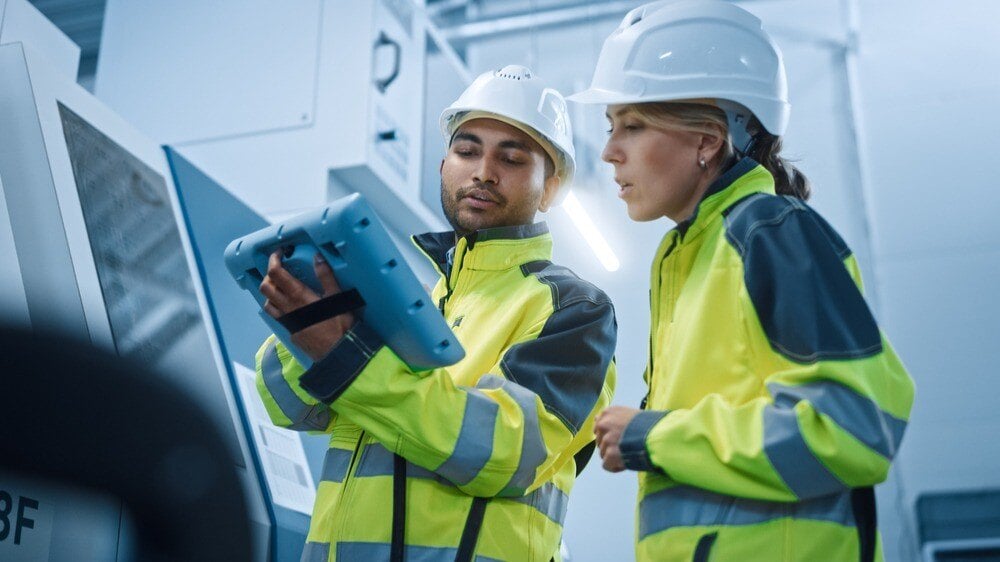
For years, industrial leaders have relied on a common but flawed assumption: "Better planning and scheduling will naturally improve wrench time." Despite the billions spent on sophisticated tools, detailed meetings, and labor forecasting, wrench time—productivity during hands-on maintenance tasks—remains alarmingly low, typically hovering around 25%–30%. As a result, backlogs rise, budgets tighten, and technician frustration grows.
But why has traditional planning and scheduling failed to deliver better results?
A Shocking Truth: One-Third of Maintenance Budgets Are Wasted
Industry expert R. Keith Mobley highlights a staggering truth: nearly one-third of every maintenance dollar is wasted on unnecessary or inefficient tasks. Given that over $200 billion is spent on industrial maintenance annually, this waste equates to a massive $66 billion problem.
More strikingly, labor costs represent 42% of total maintenance expenses, according to Dr. Alan Wilson. Optimizing labor efficiency could drastically reduce maintenance costs. Yet, many organizations overlook the root causes of inefficiency, instead doubling down on planning and scheduling alone, assuming this approach will solve the problem.
Direct Wrench Time Range from 25% to 35%. Huge Hidden Opportunities
Applying First Principles: The Hidden Truth
First principles thinking demands we break wrench-time inefficiencies down to their fundamental root causes. When we do this, a different picture emerges clearly:
Low wrench time isn’t primarily a scheduling or planning issue. It's fundamentally an issue of visibility, transparency, and real-time collaboration between maintenance, operations, storerooms, and safety teams.
Let’s examine why technicians are losing productive wrench time in the real world:
- Waiting for Spare Parts: Technicians are idle because storerooms lack visibility into maintenance priorities, delaying parts delivery.
- Waiting for Instructions: Communication breakdowns between planners and technicians result in unnecessary delays.
- Delays in Permits and Isolation: Lack of coordination between teams causes delays in initiating tasks, often due to slow permitting processes.
- Excessive Travel and Idle Time: Poor visibility into technician workloads leads to inefficient routing and excessive travel.
- Frequent Interruptions: Without real-time collaboration, technicians are frequently interrupted, which disrupts their workflow.
Planners plan and schedule around known inefficiencies rather than removing them to improve wrench time.
Why Traditional Planning & Scheduling Tools Fail
In practice, planners reinforce inefficiencies by accepting delays as a norm or ignoring them altogether. This results in unrealistic schedules built on guesswork, perpetuating firefighting and ever-increasing backlogs.
The Impact of Traditional Scheduling in Maintenance
- Status Quo Planning: Schedules are built around known inefficiencies, not ways to eliminate them.
- Disconnected Teams: Lack of real-time visibility prevents planners from solving delays in the field.
- Estimation vs. Reality: Relying on estimated task durations leads to errors and scheduling mistakes.
Thus, planning and scheduling tools become ineffective, even counterproductive, due to their disconnect from real-world challenges.
The Real-World Example: A $20B Global Chemical Company’s Success Story
A leading $20B chemical company was facing low wrench time and rising maintenance costs at a major manufacturing site. The company decided to challenge the traditional maintenance approach:
- Prioritizing Visibility and Transparency: They introduced real-time visibility across maintenance, storerooms, operations, and safety teams.
- Real-Time Collaboration: Integrated communication systems helped eliminate delays caused by parts availability, unclear instructions, and slow permitting.
- Data-Driven Decision Making: They replaced guesswork with real-time data on technician downtime, delays, and disruptions, which informed their planning and scheduling processes.
This holistic approach, which focused on eliminating roadblocks before refining planning and scheduling, resulted in significant improvements in wrench time and maintenance cost savings.
The Results: $8M–$12M Annual Maintenance Savings
By addressing the core issues—visibility, collaboration, and data capture—before revisiting planning and scheduling, this company achieved $8M–$12M in annual maintenance savings at a single site. These improvements weren’t theoretical; they were grounded in real, measurable results.
Time to Rethink Your Priorities: Tackling Root Causes First
The challenge for industrial leaders is clear: if you still prioritize planning and scheduling over visibility and collaboration, it’s time to reconsider your approach. Don’t plan around inefficiencies—address them first. Only then can planning and scheduling become meaningful tools that truly enhance maintenance productivity.
Final Thought: Stop Planning Around Inefficiencies—Eliminate Them
Ask yourself: "Are we scheduling ourselves deeper into inefficiency, or are we ready to address the root causes first?" The $20B chemical company proved that wrench time can only improve when real-world problems like poor visibility and siloed communication are resolved first.
If you’re still planning around inefficiencies, it’s time to rethink your strategy. Start solving real-world problems, and let effective planning follow. Ready to optimize your wrench time? Start addressing visibility and collaboration challenges today for better maintenance outcomes and cost savings.
Originally posted by Sundeep Ravande, CEO & Co-Founder at Innovapptive Inc on LinkedIn
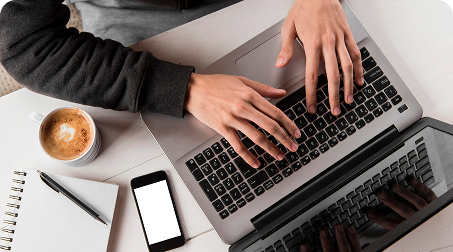
See It In Action
Schedule a personalized demo to see how our solutions can help your business thrive.
- 20-08-2025
Building the future of Industrial Operations with Innovapptive and AWS
Most manufacturers have already gone digital. Yet business outcomes haven’t moved in step. Many...
- 22-04-2025
The $3.6B Unlock: Solving the Chemical Industry’s Labor Crisis and EBITDA Pressure in One Move
“Constraints don’t slow innovation—they force it.”
- 21-04-2025
Chemical Industry's Margin Erosion: A Wake-Up Call for Operational Efficiency Amid China's Oversupply
The global chemical industry is facing mounting challenges, with revenue declines and shrinking...