The $3.6B Unlock: Solving the Chemical Industry’s Labor Crisis and EBITDA Pressure in One Move
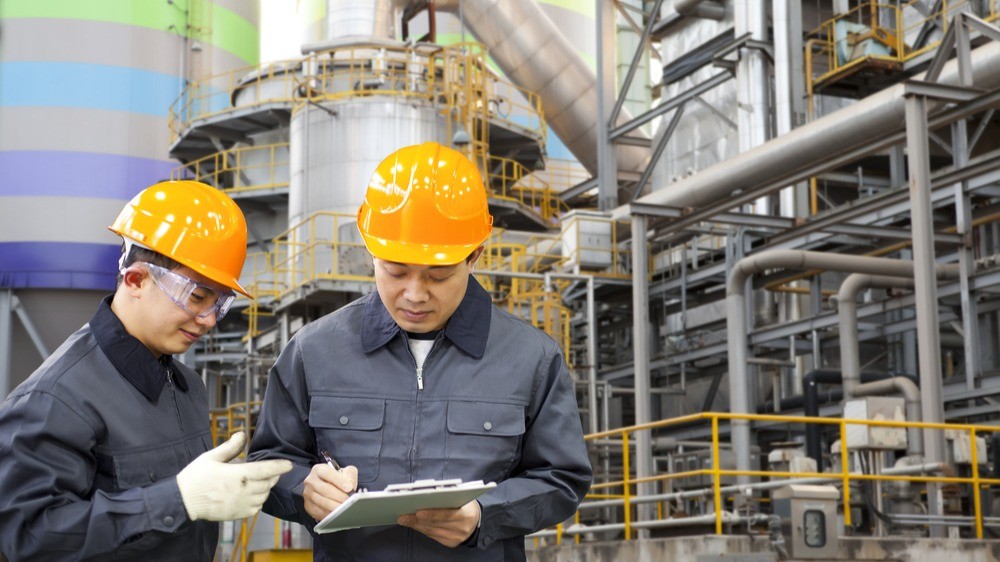
“Constraints don’t slow innovation—they force it.”
Across the global chemical manufacturing industry, a massive opportunity is hiding in plain sight. One that executives often overlook in favor of shinier, trendier digital transformation initiatives. But make no mistake—it’s one of the most financially powerful levers left to pull.
Let’s break down the numbers:
- The top global chemical manufacturers with revenues exceeding $5B collectively generate over $1.2 trillion in revenue annually (based on C&EN’s Global Top 50 rankings).
- Maintenance spend typically averages 3% of total revenue, equating to a $36 billion annual maintenance spend across this group.
- Yet studies consistently show wrench time—the portion of time technicians actually spend performing value-added work—is just 25–30%.
- Best-in-class performance achieves 60–65% wrench time.
It is now proven that a modest 10% reduction in maintenance costs is attainable—driven by improved wrench time and process discipline—unlocking $3.6 billion in annual savings across the top global chemical manufacturers.
This isn’t just a theoretical model. In a recent blog titled "Chemical Industry's Margin Erosion: A Wake-Up Call for Operational Efficiency Amid China's Oversupply", we shared a real-world success story that showed a $24B Global Chemical Company attaining these very benefits.
These aren’t incremental improvements. They’re operational breakthroughs revealing how much hidden margin lies in frontline execution—and what’s possible when execution is transformed, not just tracked.
This doesn’t require expensive infrastructure upgrades or speculative AI pilots—it requires changing how frontline work gets done.
The Perfect Storm: Labor Crisis Meets Margin Compression
The chemical manufacturing sector is at a breaking point:
- 30% of the chemical workforce will retire by 2035
- Only half of that gap will be filled based on current labor trends
- Margin pressures persist due to global oversupply (especially from China), volatile energy costs, and shrinking capital flexibility
The result? A crisis of capacity, cost, and capability.
You can’t hire your way out of this. You can’t outsource your way out either. The only path forward is to optimize operations, maximize asset performance, and do more with less.
(Sources: McKinsey – Chemicals Sector Operations Report, Deloitte – The Future of Work in Chemicals)
The DeepSeek Paradox: Innovation Without Unlimited Resources
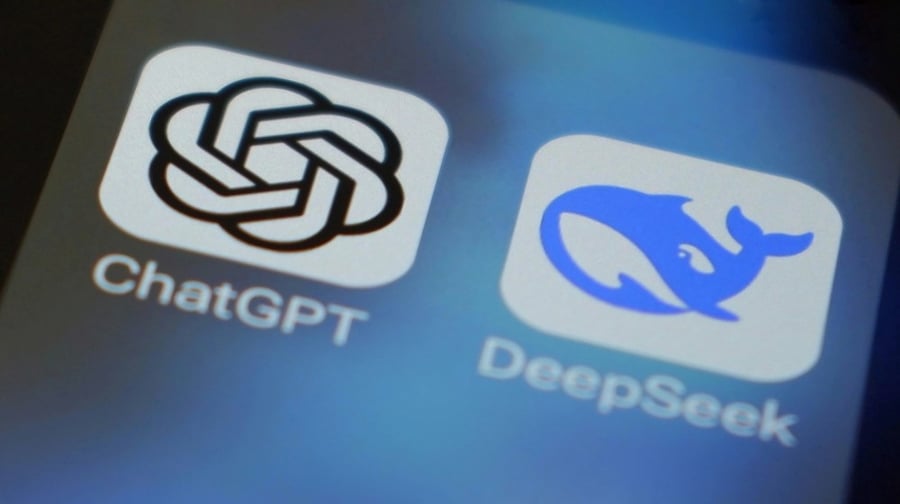
DeepSeek vs. ChatGPT - "Cracking the The Theory of Constraints Code
In the AI world, Chinese firm DeepSeek recently outperformed OpenAI’s ChatGPT benchmarks—not with NVIDIA’s premium GPUs, but by optimizing for lower-cost infrastructure.
They didn’t outspend the competition. They out-executed them.
The chemical industry is in a similar race. The winners won’t be the ones with the biggest tech stack—they’ll be the ones who eliminate inefficiencies, compress execution time, and unlock hidden capacity across their operations.
The Real Enemy: Inefficiency at the Frontline
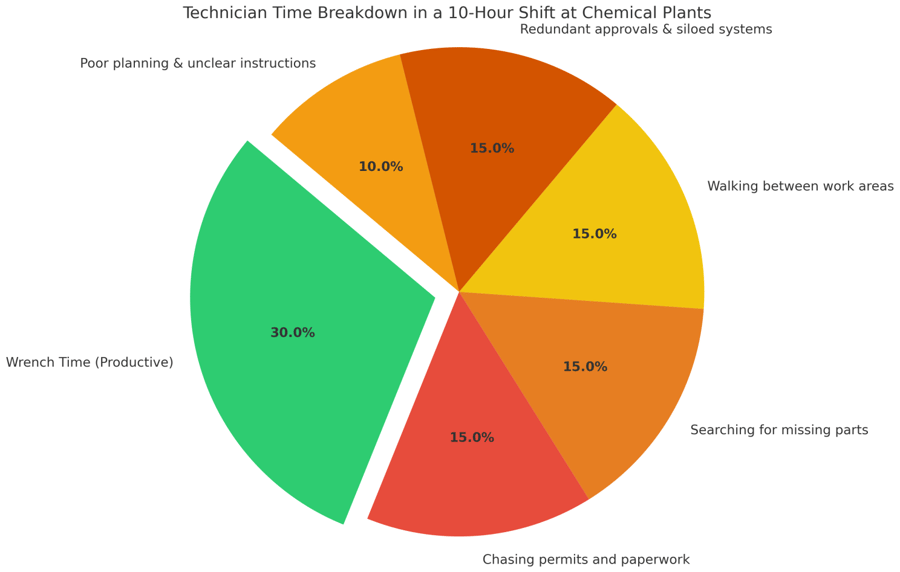
At most chemical plants, technicians spend less than 3 hours per 10-hour shift actually turning wrenches. The rest of their time is lost to:
- Chasing permits and paperwork
- Searching for missing parts
- Walking between work areas
- Redundant approvals and siloed systems
- Poor planning and unclear work instructions
Now imagine if you could:
- Increase wrench time from 30% to 60%
- Eliminate the need to hire 30% more labor to meet production targets
- Cut operations and maintenance (O&M) costs by up to 30%—without reducing headcount
That’s not a theory. That’s the future of frontline productivity—already happening at leading plants using connected execution platforms.
The Path Forward: A Unified Platform for Frontline Execution
The key isn’t more digital tools. It’s one connected workforce platform that synchronizes operations, maintenance, safety, quality, and inventory in real time.
A system where:
- Operators, maintainers, EHS, and storeroom teams work in lockstep
- AI and mobile technology guide workers step-by-step
- Spare parts are pre-kitted and staged ahead of time
- Data is structured at the source, enabling root cause analysis (RCA) and real-time KPIs
- Feedback loops drive continuous improvement and predictive maintenance
This is how wrench time improves, labor dependency drops, and cost optimization becomes sustainable—not in PowerPoint, but on the plant floor.
It’s not about running another digital twin pilot. It’s about operationalizing real change, where tribal knowledge becomes institutionalized, and execution becomes intelligent, not reactive.
What Most Digital Manufacturing Portfolios Miss
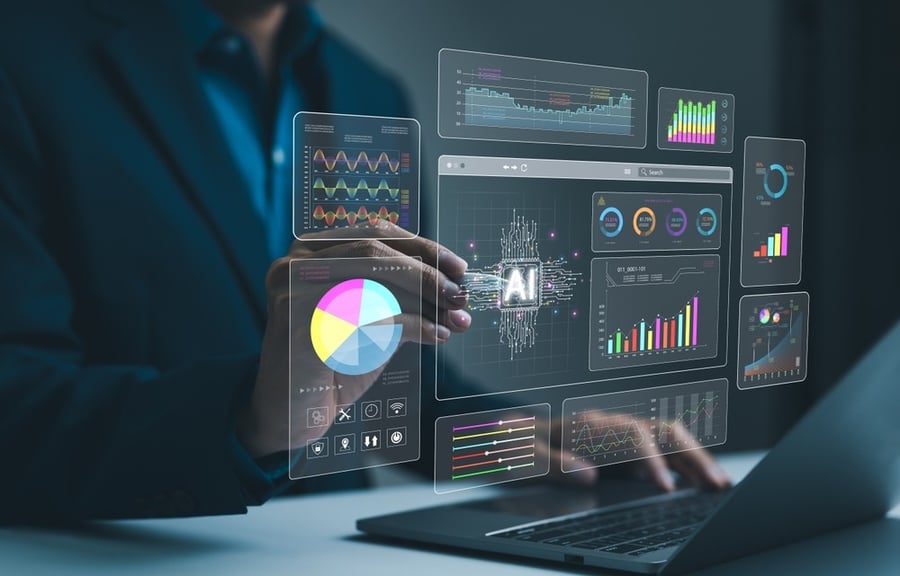
The Illusion of Progress: When Digital Portfolios Prioritize Optics Over Impact
Let’s be honest: Most digital portfolios prioritize:
- Digital twins
- Advanced analytics
- AI agents
- Energy dashboards
These technologies are valuable, but they often fail to impact near-term EBITDA because they overlook the foundational layer—how maintenance execution and frontline operations are actually performed.
This is where 80% of the value lies. But it only unlocks when people, process, and platform align.
Why Most Maintenance Transformations Fail
Because they stop at tech.
To deliver lasting ROI, companies must invest in:
- A centralized Manufacturing Excellence Council to govern execution
- Poka-Yoke practices for maintenance data—from requests to corrective actions
- Training programs that instill process discipline
- Data-driven workflows that unify operations, inventory, quality, and safety
It’s this orchestration—not siloed apps—that drives sustainable EBITDA impact.
The Hard Truth: Maintenance Doesn’t Fail Because of Technology—It Fails Because of People and Process
Key Levers for O&M Cost Reduction:
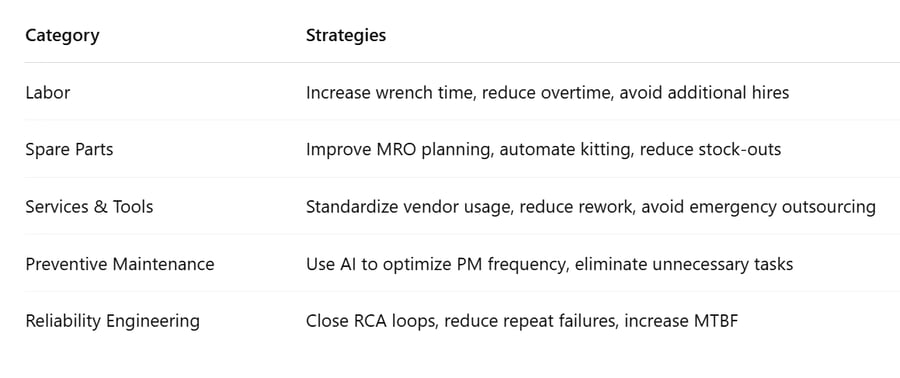
A Final Word to the C-Suite: Prioritize This Now
If you’re in the C-Suite, evaluating where to place your next digital dollar, ask yourself:
- Are we solving real execution problems?
- Are we reducing reliance on a shrinking workforce?
- Are we investing in initiatives that drive near-term EBITDA?
Because the next generation of chemical manufacturing leaders won’t be those who digitize the most—but those who eliminate the most waste.
Your Wrench Time is a $100M Lever
Let’s reframe wrench time as more than a maintenance KPI.
It’s your #1 operational lever to:
- Tackle the chemical industry labor shortage
- Maximize field technician productivity
- Drive $50M to $100M+ in EBITDA improvement
- Reduce dependency on talent you can’t hire fast enough
This must be the #1 priority in your digital manufacturing roadmap. This isn’t a transformation for show—it’s a transformation for survival.
And the clock is ticking.
Ready to Unlock $3.6B in Hidden Value?
See how leading chemical manufacturers are transforming frontline execution—not with more dashboards, but with real results.
Talk to our experts today and discover how your plants can double wrench time, cut costs, and boost EBITDA without increasing headcount.
Originally posted by Sundeep Ravande, CEO & Co-Founder at Innovapptive Inc on LinkedIn
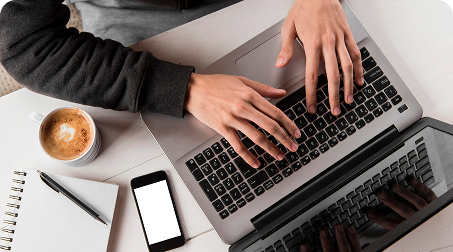
See It In Action
Schedule a personalized demo to see how our solutions can help your business thrive.
- 20-08-2025
Building the future of Industrial Operations with Innovapptive and AWS
Most manufacturers have already gone digital. Yet business outcomes haven’t moved in step. Many...
- 22-04-2025
The $3.6B Unlock: Solving the Chemical Industry’s Labor Crisis and EBITDA Pressure in One Move
“Constraints don’t slow innovation—they force it.”
- 21-04-2025
Chemical Industry's Margin Erosion: A Wake-Up Call for Operational Efficiency Amid China's Oversupply
The global chemical industry is facing mounting challenges, with revenue declines and shrinking...