5 Ways a Mobile Maintenance Management Solution Helps You Create a High Performing Maintenance Team
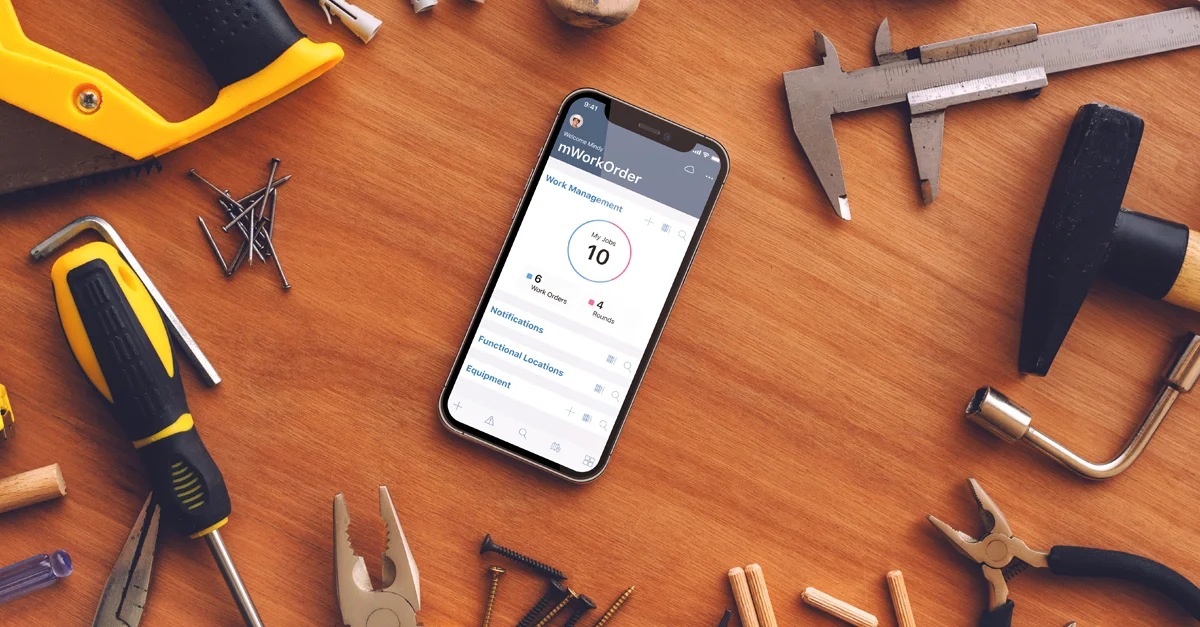
Leveraging digital technologies and mobile maintenance management solutions can bridge downtime-causing gaps within plant operations. Discover five ways these technologies and solutions can improve a maintenance team’s effectiveness and productivity.
Everyday, you find a new stat about talent shortage in asset-intensive industries. On the other hand, sales teams are pushing for more production. What comes to mind when thinking about boosting productivity: Increasing workforce and deploying new equipment. However, these strategies don't always yield a justifiable ROI. Before making such new investments, focus first on bridging gaps within your production environment by leveraging digital technologies. Today, we’ll discuss five ways to leverage digital technologies on a mobile maintenance management solutions for high performing maintenance teams:
Digital Technologies to Integrate in Your Maintenance Management Solution
1. IIoT Delivers Instant, Real-Time Information
The Industrial Internet of Things (IIoT) forms the foundation of any predictive maintenance program. It enables maintenance teams to digitally monitor and manage assets in real time even in remote locations. IIoT uses interconnected and Web-enabled sensors, instruments, and other devices, to link key decision makers with the shop and production floor. Thanks to IIoT, maintenance directors, managers and supervisors can receive and view real-time data via the Web instead of having to physically check every instrument in the plant.
2. Identifying Potential Equipment Failure Beforehand Using Artificial Intelligence (AI)
AI-enabled devices on the production floor not only monitor equipment condition in real time, but can collect data on its own, compare it to data point readings taken over time to determine any inconsistencies, analyze what may be happening, predict potential problems or failures based, and issue appropriate warnings so action can be taken before a downtime-causing incident occurs. AI-enabled devices can do this much quicker than a human, saving time, reducing costs, improving decision making and increasing efficiency.
3. Gaining Greater Maintenance Insight through Big Data Analytics
Big data is far more than an Excel spreadsheet or a paper checklist. It’s the sum of digital information gathered from equipment and machinery throughout a plant or facility. The data is electronically collected by many sources, including frontline workers outfitted with mobile applications and AI-enabled sensors, instrumentation, etc. As you can imagine, it’s a lot of information, hence the term “big” data. This information is gathered in one digital location. In its raw form, it’s far too much data for any one person to decipher and make meaningful conclusions. But a computer can utilize machine learning (ML) algorithms quickly comb through what’s been gathered to find patterns and provide real-time insights that would take humans months to discover.
Big data gives reliability engineers valuable clues that enable them to determine when to repair, replace or upgrade equipment before it fails instead of waiting until it stops functioning. As such, big data analytics reduces operational disruptions and equipment downtime, extends asset lifetime, and improves workflows, making it an integral part of any predictive maintenance program.
4. Reducing Maintenance Errors via Augmented Reality
Augmented reality (AR) through smartglasses offers hands-free access to work instructions and product manuals for maintenance technicians. For example, a technician wearing smartglasses stands before a motor and sees all information about it on the screen. He can follow step by step instructions to work on the motor, leaving no room for errors. This makes the working conditions clutter-free for the technicians. AR helps young technicians learn key information about equipment in the facility.
5. Connected Worker Platforms Digitize Enterprise Asset Management
Connected worker - the new buzzword in digital transformation, integrates cutting-edge technologies into a unified mobile platform and connects frontline workforces with the back office. Maintenance technicians, who would otherwise carry paper binders back and forth between plant and office, can do all their paperwork over the mobile device.
Historically, different organizations in an asset-intensive industry have been siloed, making digital transformation initiatives incomplete. Connected worker technologies break these barriers and complete your digital ecosystem. This will boost productivity and improve operational efficiency without burning a hole in your pocket.
Looking for a Mobile Maintenance Management Solution with these Capabilities?
Innovapptive offers a mobile maintenance management solution, mWorkOrder, that connects frontline maintenance teams with ERP systems like SAP and IBM Maximo. By eliminating paper binders and empowering technicians with real-time data, mWorkOrder boosts operational efficiency and productivity. Want to see how mWorkOrder works for your organization? Our experts are always happy to help you. Schedule a free demo today or call us at 844-464-6668.
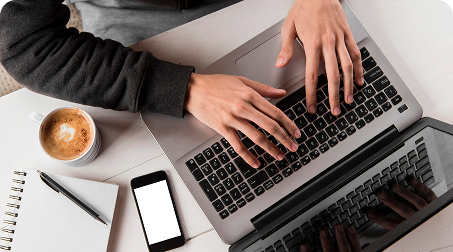
See It In Action
Schedule a personalized demo to see how our solutions can help your business thrive.
- 20-08-2025
Building the future of Industrial Operations with Innovapptive and AWS
Most manufacturers have already gone digital. Yet business outcomes haven’t moved in step. Many...
- 22-04-2025
The $3.6B Unlock: Solving the Chemical Industry’s Labor Crisis and EBITDA Pressure in One Move
“Constraints don’t slow innovation—they force it.”
- 21-04-2025
Chemical Industry's Margin Erosion: A Wake-Up Call for Operational Efficiency Amid China's Oversupply
The global chemical industry is facing mounting challenges, with revenue declines and shrinking...