5S Checklist Audits: A Simple Way to Ensure Efficiency & Safety
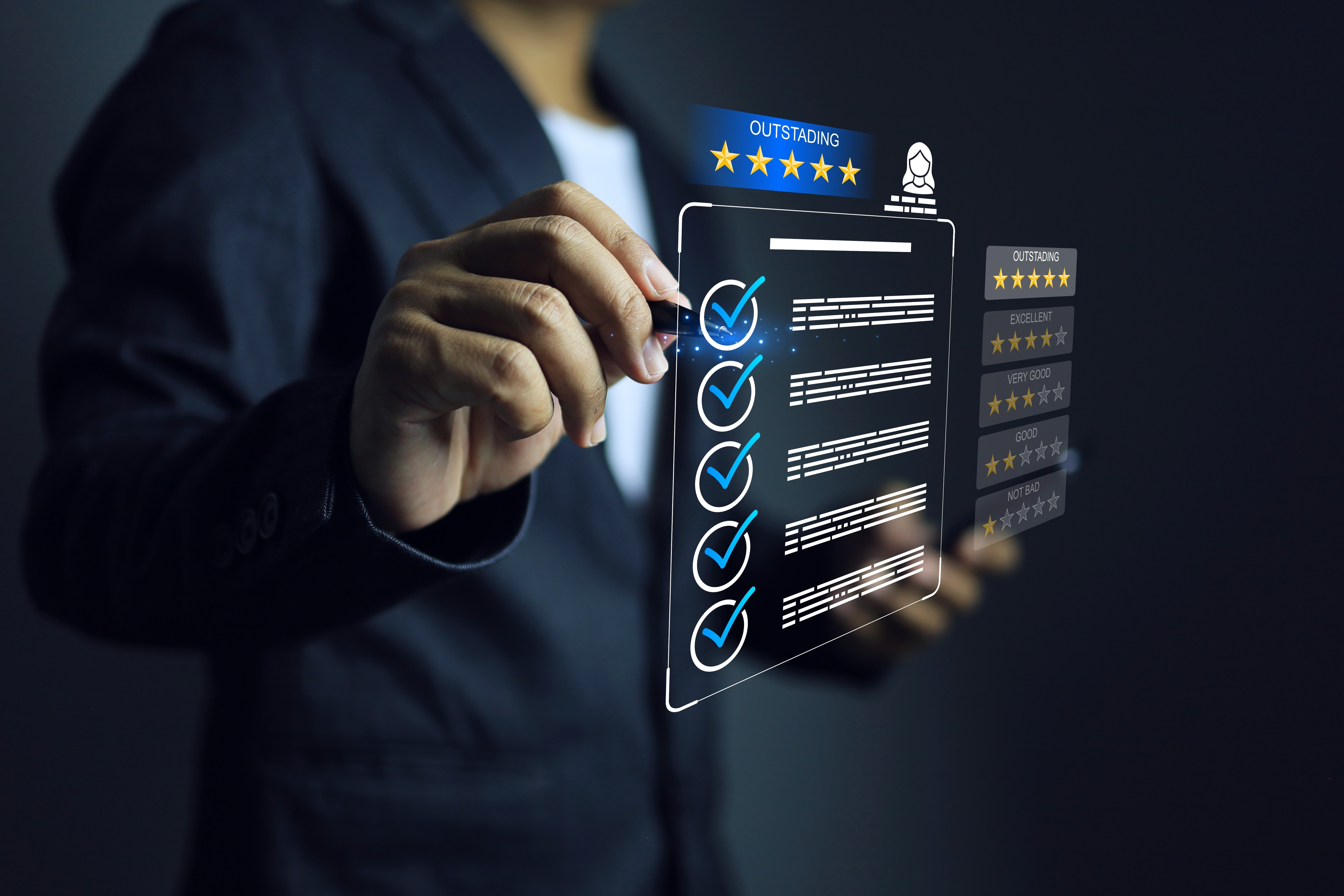
What Is a 5S Checklist Audit?
A 5S checklist audit is a structured process used by organizations to evaluate and sustain workplace organization, cleanliness, and efficiency. Rooted in Lean manufacturing principles, 5S (Sort, Set in Order, Shine, Standardize, Sustain) ensures that workplaces remain optimized for safety, productivity, and compliance.
By using a 5S checklist, businesses can proactively identify inefficiencies, safety hazards, and operational gaps, allowing for continuous improvement. These audits are especially critical in high-risk industries like manufacturing, oil & gas, chemical processing, and mining, where unorganized work environments can lead to accidents, downtime, and regulatory non-compliance.
Why Are 5S Checklist Audits Important?
1. Increased Workplace Safety
A clutter-free and organized workspace minimizes hazards like trips, falls, and misplaced tools that could cause injuries. A well-executed 5S checklist helps safety managers and EHS professionals enforce safety standards and ensure compliance with OSHA and other regulations.
2. Improved Operational Efficiency
5S audits eliminate unnecessary items, streamline workflows, and ensure that every tool, machine, and resource is easily accessible—reducing wasted time and improving productivity.
3. Standardized Processes
By following a structured 5S checklist, teams develop consistent procedures, making audits more effective and ensuring that best practices are sustained across shifts and locations.
4. Cost Savings
Poorly maintained workspaces often lead to damaged equipment, misplaced inventory, and delays—all of which increase costs. Regular 5S checklist audits prevent these issues, saving businesses money in the long run.
5. Regulatory Compliance
For industries with strict safety and environmental regulations, 5S checklist audits provide documentation and accountability, ensuring organizations remain compliant and audit-ready.
How to Conduct a 5S Checklist Audit
1. Prepare Your Audit Checklist
Develop a detailed 5S checklist that includes specific criteria for sorting, organizing, cleaning, standardizing, and sustaining workplace order. This should be customized for your industry and operational needs.
2. Conduct On-Site Inspections
Regularly walk through work areas and use your 5S checklist to identify non-compliance issues, inefficiencies, or hazards.
3. Document Findings & Take Action
Log issues, assign corrective actions, and ensure accountability for resolution. Tracking these findings over time helps identify recurring problems.
4. Train Employees & Encourage Engagement
5S success depends on employee participation. Train teams to understand the importance of 5S checklist audits and encourage them to report potential safety or efficiency concerns.
5. Monitor Progress & Continuously Improve
Consistently track your 5S audit results and look for trends that indicate areas needing improvement. Establish regular follow-ups to ensure sustained compliance.
Digitize Your 5S Checklist Audits
While traditional 5S checklists are effective, paper-based audits and manual data tracking can be inefficient, time-consuming, and prone to errors. Here’s how Innovapptive can make a difference:
✔ Issues & Task Management – Instantly capture non-conformances, assign corrective actions, and track resolutions in real-time.
✔ Mobile Forms & Checklists – Digitally conduct 5S audits from any location using customizable forms on mobile devices or tablets.
✔ Automated Reporting & Insights – Generate instant reports with AI-powered insights to track trends, ensure compliance, and drive continuous improvement.
✔ Collaboration & Visibility – Enable seamless collaboration between safety managers, EHS professionals, and frontline workers through a unified digital platform.
✔ AI-Powered Alerts & Predictive Analytics – Identify recurring safety hazards before they become major issues, reducing risks and downtime.
By digitizing 5S checklist audits, Innovapptive helps safety and operations managers enhance workplace organization, minimize risks, and achieve operational excellence without the hassle of paperwork.
Start Your Digital 5S Journey Today
Don’t let manual 5S checklist audits slow down your workplace efficiency. Innovapptive’s AI-powered solution makes 5S execution seamless, data-driven, and actionable—helping you maintain a safer and more productive work environment.
Request a demo today to see how Innovapptive can revolutionize your 5S checklist audits and drive continuous operational improvement!
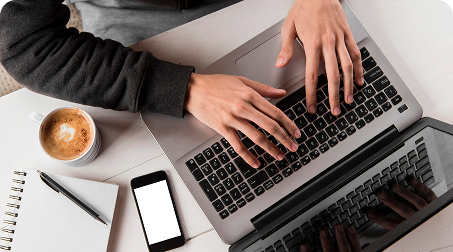
See It In Action
Schedule a personalized demo to see how our solutions can help your business thrive.
- 20-08-2025
Building the future of Industrial Operations with Innovapptive and AWS
Most manufacturers have already gone digital. Yet business outcomes haven’t moved in step. Many...
- 22-04-2025
The $3.6B Unlock: Solving the Chemical Industry’s Labor Crisis and EBITDA Pressure in One Move
“Constraints don’t slow innovation—they force it.”
- 21-04-2025
Chemical Industry's Margin Erosion: A Wake-Up Call for Operational Efficiency Amid China's Oversupply
The global chemical industry is facing mounting challenges, with revenue declines and shrinking...