6 Ways a Mobile-First Warehouse Solution Can Cut Costs and Generate Revenue
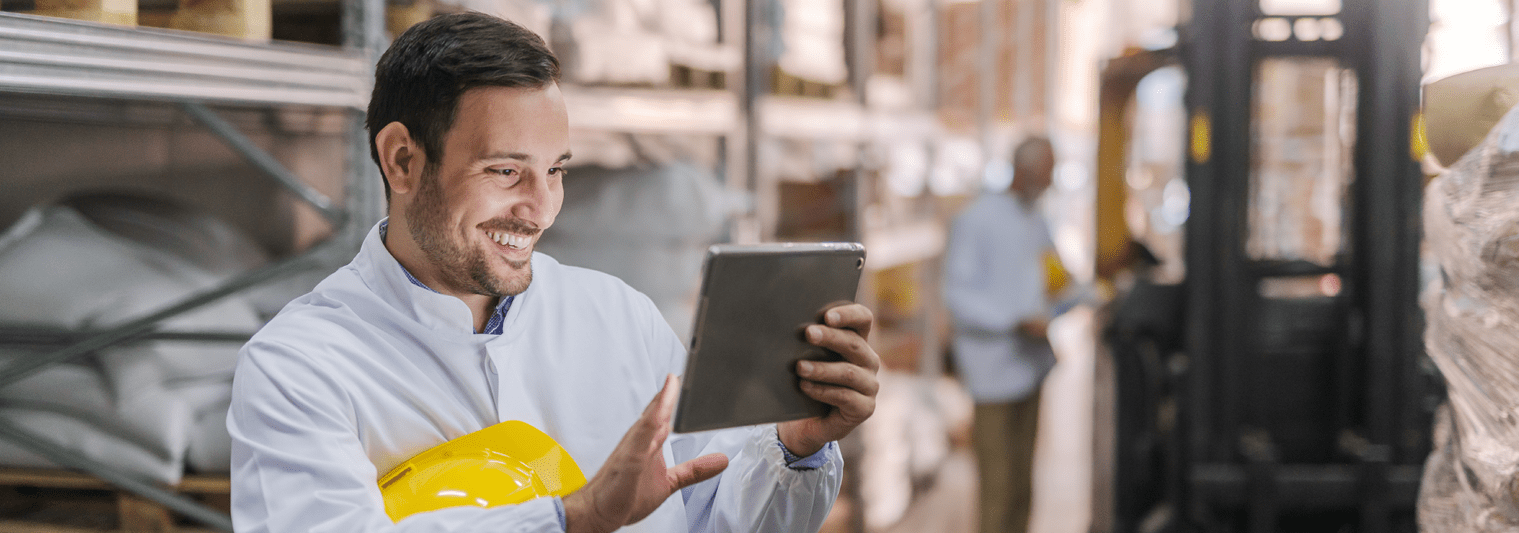
An inventory and warehouse management system isn’t confined to storing vital data about raw materials, products, and shipments. It also needs to track, process and distribute mission-critical information in “Real-Time” across multiple touchpoints to ensure high integrity and accuracy of the inventory for key stakeholder such as customers, employees, managers and decision makers.
Companies using manual data collection processes too often end up with inaccurate information, leading to incorrect stock levels, missed deadlines and disgruntled customers. A digital, mobile-first inventory & warehouse management solution can optimize your warehouse efficiency, enabling you to cut unnecessary costs and expenditures. Such a solution, if put to right use, can offer real-time insights about where stock is located, how many are in stock, their fulfilment status and much more.
Let's examine the pain points in a typical warehouse setup and how they impact revenue:
- Material movement: There is a constant movement of materials in and out of a warehouse. Poor receiving and tracking procedures cause errors, increasing costs and labor, negatively impacting bottom lines.
- Inefficient paper-based processes: If pickers can’t locate stock or waste time searching for items that have been moved, this affects timelines throughout the warehouse. Costs also escalate as pickers shuffle from shelf to shelf. Since they must rely on paper that contains dated information, checking each item makes this process highly inefficient.
- Stock availability: Revenue cycles are harmed when products lie idle on shelves. On the opposite side, customer demands remain unmet when items are out of stock. Either way, revenue is lost.
Warehouse mobility cuts costs and improves profitability
A mobile-first inventory solution delivers efficient turnaround times and optimized order fulfilment in every operational domain, including receiving, quality control, picking, packing and shipping. By leveraging a combination of technologies, such as RFID, barcode scanners, GPS, AI, or even IoT, a mobile-first solution ensures high-level inventory visibility, optimized warehouse operations, and superior customer satisfaction.
Here are the key benefits of adopting a mobile solution in your warehouse and inventory operations:
- Remove unnecessary stages
- Streamline processes by minimizing unnecessary touches
- Trace processes to find duplicating or repeating the steps
- Drive productivity and improve order fulfilment
- Empower workers with instant access to real-time data, anywhere, anytime
- Send orders to your workers’ mobile devices, instead of printing them on paper
- Print labels on-demand at the point of application to minimize walking time and errors
- Ensure order accuracy
- Workers can scan each item’s barcode as they pick to accurately capture data instantly
- Minimize incorrect picks
- Ensure faster and accurate cycle counting
- Continually update counts, eliminating inventory that lasts days or even weeks
- Ensure real-time supply chain tracking
- Locate items in real-time by leveraging GPS technologies
- Ensure timely statutory and audit compliances
If you’re still stuck in a paper-based process, Innovapptive offers a solid digital transformation foundation you can build upon. The first step on this road is mobilization. Innovapptive’s mobile-first inventory solution – mInventory – is a robust solution that enables users to avoid the common warehouse challenges addressed here, gaining complete visibility across your supply chain. Use mInventory to accurately determine supply levels; track receipts, movements and consumption; and better control costs as part of an optimized, efficient inventory and warehouse management process.
To learn more about mInventory and how it optimizes the warehouse and supply chain process, schedule a free demo today by calling 844-464-6668 or by clicking here.
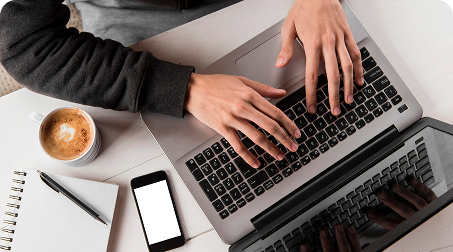
See It In Action
Schedule a personalized demo to see how our solutions can help your business thrive.
- 22-04-2025
The $3.6B Unlock: Solving the Chemical Industry’s Labor Crisis and EBITDA Pressure in One Move
“Constraints don’t slow innovation—they force it.”
- 21-04-2025
Chemical Industry's Margin Erosion: A Wake-Up Call for Operational Efficiency Amid China's Oversupply
The global chemical industry is facing mounting challenges, with revenue declines and shrinking...
- 21-04-2025
Why Wrench Time Isn’t Improving: The Hidden Costs of Traditional Maintenance Scheduling
For years, industrial leaders have relied on a common but flawed assumption: "Better planning and...