Case Study: Refiner Reduces Downtime Using a Mobile Maintenance and Warehouse Solution
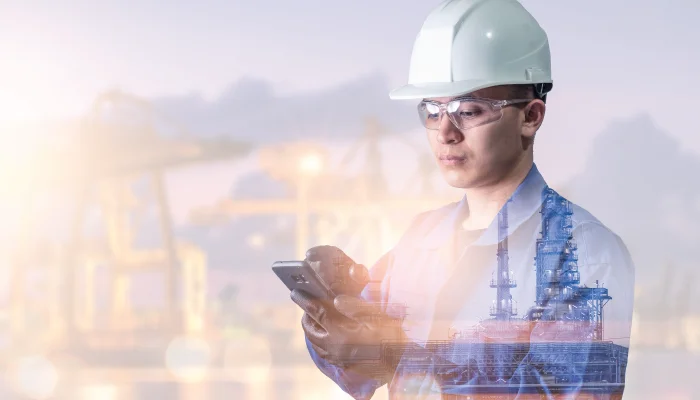
Refinery maintenance and warehouse teams encounter multiple challenges every day. The industry is constantly struggling to maximize asset availability and minimize downtime. Despite the digital revolution, nearly 40% of industrial plants and facilities still use paper records for maintenance and warehouse reporting. Such manual processes impede efficiency, collaboration, and productivity. A U.S. refinery realized it could overcome these operation issues by adopting a connected worker platform for its maintenance and warehouse departments. Read about it in our latest case study.
The maintenance process employed at refineries does little to empower workers in their fight to stave off downtime. Too many refinery frontline workers carry out labor-intensive, manual tasks using paper checklists or legacy digital systems now considered obsolete.
Manual processes in warehouses impede workflow efficiency delaying spare parts order fulfillment. Errors and inaccuracies in paper-based legacy processes delay the turnaround time of cycle counts, throwing off the counts, and leading to understocks or overstocks. Out-of-date technology hinders their performance. Lower worker performance means higher maintenance backlogs and unplanned downtime, and each impacts production and the bottom line.
Maintenance and operations teams using such legacy processes struggle to balance demand, procurement, and supply. Digitizing supply chain and plant maintenance functions offers the best solution to these challenges in modern refineries.
A mobile maintenance and warehouse management solution allows greater collaboration between them, the SAP back-office system, and the company procurement office. Modern integrated mobile applications offer an end-to-end work management application that supports preventive and predictive maintenance strategies. It lets maintenance teams move away from the inefficient and reactive “run-to-fail” approach to achieve greater operational efficiency and reduce downtime.
Leveraging mobile technology, refineries can maximize asset lifecycles while reducing planned downtime. Using mobile-first solutions, traditional refineries turn into smart ones by gaining deeper and real-time insight into their operations.
Check out our latest case study to learn how a U.S. refiner recently upgraded its maintenance and warehouse efficiency with an Innovapptive connected worker solution. The company sought a mobile maintenance and warehouse management solution that could tie its maintenance and operations departments together and allow greater collaboration between them, the SAP back-office system, and the procurement office.
The refinery considered multiple vendors during its digital transformation initiative. It selected Innovapptive for its unique connected solution featuring mobile device-based applications tied directly to SAP.
As a connected worker pioneer, Innovapptive specializes in mobile maintenance and warehouse management solutions. Offering two integrated mobile applications, mWorkOrder and mInventory, Innovapptive provided a refinery with an end-to-end work management application that supports preventive and predictive maintenance strategies to help them move away from the inefficient and reactive “run-to-fail” approach.
You Can Accomplish the Same; Here’s How
If you’re ready to transform into a smart refinery, explore our digital transformation solutions that will improve your frontline workers' lives. To learn more about our intuitive mobile-first applications request a free demo or speak to our industry experts at 888-464-6668.
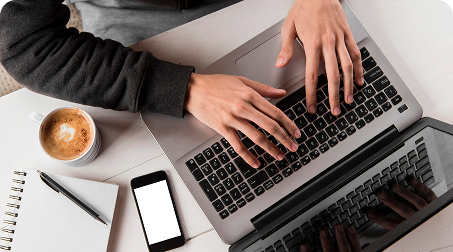
See It In Action
Schedule a personalized demo to see how our solutions can help your business thrive.
- 20-08-2025
Building the future of Industrial Operations with Innovapptive and AWS
Most manufacturers have already gone digital. Yet business outcomes haven’t moved in step. Many...
- 22-04-2025
The $3.6B Unlock: Solving the Chemical Industry’s Labor Crisis and EBITDA Pressure in One Move
“Constraints don’t slow innovation—they force it.”
- 21-04-2025
Chemical Industry's Margin Erosion: A Wake-Up Call for Operational Efficiency Amid China's Oversupply
The global chemical industry is facing mounting challenges, with revenue declines and shrinking...