Transforming Industrial Operations: The Power of Connected Worker and Digital Technologies
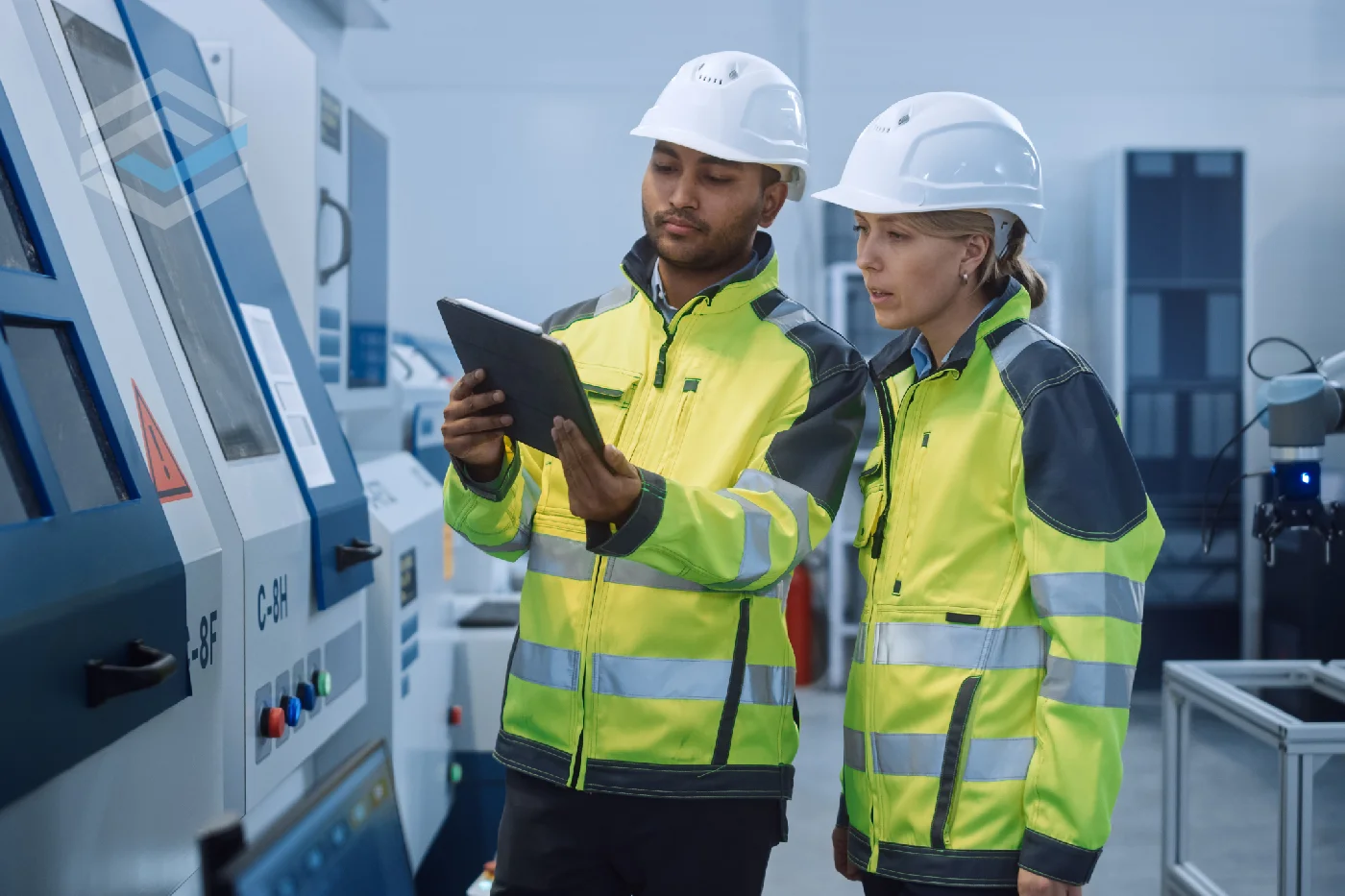
The future of industrial operations hinges on the seamless integration of Connected Worker solutions, workforce technology, and Digital Transformation initiatives. This blog explores how these technological advancements—such as digital work instructions, modernized asset performance management, and mobile work order solutions—synergize to minimize unplanned downtime, enhance plant productivity, and transform the way industries function.
The Connected Worker: Bridging the Digital Divide in Industrial Operations
The Connected Worker concept represents a paradigm shift in industrial processes, transforming traditional workflows into a data-driven ecosystem. By equipping workers with cutting-edge tools like wearables, IoT devices, and smart technologies, companies enable real-time data access and collaboration. This transformation fosters greater efficiency, innovation, and operational visibility, ensuring more proactive management of industrial facilities.
Reducing Unplanned Downtime with Predictive Maintenance
Unplanned downtime can lead to millions in lost revenue and disrupted operations. By leveraging Connected Worker platforms, industries can adopt predictive maintenance strategies that utilize real-time data from IoT-enabled devices. These platforms help identify and mitigate issues before they lead to breakdowns, reducing downtime and improving asset reliability.
Empowering the Workforce with Mobile Work Order Solutions
Workforce technology is essential for keeping industrial teams agile and responsive. Mobile work order management systems, a key element of Connected Worker technology, enable employees to manage tasks on the go. The integration of digital work instructions allows for the streamlining of complex processes, ensuring that the workforce has real-time access to necessary information, leading to faster issue resolution and enhanced productivity.
Optimizing Plant Productivity with Data-Driven Approaches
To stay competitive, companies need to adopt modernized asset performance management strategies. By leveraging advanced analytics and machine learning, organizations can gain insights into equipment performance, identify potential bottlenecks, and optimize maintenance schedules. This data-driven approach reduces operational costs and maximizes plant productivity—a core goal for industries looking to remain competitive.
Digital Work Instructions: Streamlining Operations
The shift from paper-based to digital work instructions is a critical step toward operational efficiency. Digital formats reduce errors, provide real-time updates, and ensure employees always have access to the most current guidelines. This enhances compliance and contributes to standardized workflows across industrial operations.
Maximizing Efficiency with Modernized Asset Management
A move towards modernized asset performance management is essential for businesses aiming to stay ahead. By continuously monitoring equipment and analyzing performance data, industries can transition from reactive to proactive maintenance, reducing unexpected failures, extending asset lifespans, and minimizing operational costs.
The Role of Digital Transformation in Industrial Operations
Digital transformation involves the implementation of technologies like Connected Worker solutions, mobile workforce management, and predictive analytics. This comprehensive approach drives efficiency, innovation, and long-term competitiveness. For industrial plants, adopting these strategies means embracing a future where adaptability and optimization are central to success.
Mobile Work Order: Enhancing On-the-Go Efficiency
Mobile work order solutions are revolutionizing the way tasks are managed on the shop floor. By enabling workers to create, manage, and track work orders via mobile devices, organizations reduce paperwork, speed up response times, and resolve issues faster. This leads to improved overall operational efficiency and faster task completion.
The Synergy of Connected Worker and Digital Technologies
The true power of these technologies lies in their synergistic effects. Connected Worker platforms, workforce technologies, digital work instructions, and mobile work orders work together to create a transformative impact on industrial operations. The real-time data these solutions provide enables businesses to adopt predictive maintenance strategies, improve resource allocation, and ensure that operations remain flexible and adaptive to change.
Key Benefits for Industrial Operations:
- Minimized Unplanned Downtime: Predictive maintenance strategies identify and address potential equipment failures before they occur, significantly reducing unplanned downtime.
- Enhanced Workforce Efficiency: Mobile work orders and digital work instructions empower employees with real-time data, increasing agility and responsiveness.
- Optimized Plant Productivity: Data-driven decision-making ensures that assets are always operating at peak efficiency, boosting overall productivity.
- Improved Safety and Compliance: Digital work instructions ensure that operations comply with industry standards and regulations, enhancing safety and operational consistency.
- Informed Strategic Decision-Making: Real-time data flow enables organizations to make accurate, data-driven decisions crucial for staying competitive in today’s market.
Conclusion:
The integration of Connected Worker solutions, modernized asset performance management, and digital transformation represents a critical evolution in industrial operations. By adopting these technologies, companies can reduce downtime, improve productivity, and stay competitive in a rapidly changing landscape. The journey toward a digitally transformed industrial ecosystem is not just a technological evolution but a strategic imperative for success in the 21st century.
Looking to transform your industrial operations? Innovapptive offers industry-leading Connected Worker solutions designed to improve maintenance, warehouse management, and operational efficiency. Watch our video to learn more, and schedule a free demo to see how we can help your business thrive.
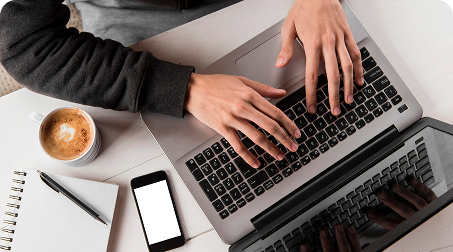
See It In Action
Schedule a personalized demo to see how our solutions can help your business thrive.
- 20-08-2025
Building the future of Industrial Operations with Innovapptive and AWS
Most manufacturers have already gone digital. Yet business outcomes haven’t moved in step. Many...
- 22-04-2025
The $3.6B Unlock: Solving the Chemical Industry’s Labor Crisis and EBITDA Pressure in One Move
“Constraints don’t slow innovation—they force it.”
- 21-04-2025
Chemical Industry's Margin Erosion: A Wake-Up Call for Operational Efficiency Amid China's Oversupply
The global chemical industry is facing mounting challenges, with revenue declines and shrinking...