Connected Worker Platforms: Empowering the Building Materials and Construction Machinery Industries
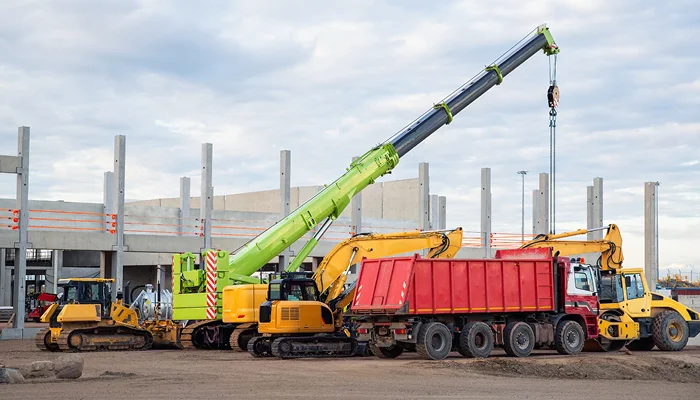
Building materials and construction machinery manufacturers are constantly searching for ways to boost frontline worker productivity, streamline workflows, and maximize efficiency. Traditionally, this industry has used a paper-based process for maintenance work orders and spare parts fulfillment. Unfortunately, such a process is slow and unwieldy. It’s also outdated. Might digitally connected workers provide the answer?
A connected worker strategy eliminates paper-based operations and digitally transforms how maintenance and warehouse frontline workers perform their daily tasks. Today we’ll take a closer look at what a connected worker platform is. We’ll also examine how one vendor’s solution differs from others in the market.
What Is Connected Worker Technology?
Connected worker technology spans the gamut of modern digital tools. It spans hardware like:
- Consumer-grade smartphones
- Tablet computers
- Barcode scanners
- Mobile printers
- Wearables (smartglasses and smartwatches)
- even drones!
It also includes network and software applications, whether on premises, in the Cloud, or software-as-a-service (SaaS).
These tools, used alone or in any imaginable combination, enable frontline workers and supervisors to collaborate and communicate with each other in real time while in the field, on the production or warehouse floors, or in the office. The connected workers do not have to be in the same location to digitally collaborate.
According to Gartner, a "Connected Worker is an online employee that has the ability to work from anywhere, anytime, and using any device.” Gartner also says that such technology has dramatically changed the way frontline workers do their jobs.
What Does Connected Worker Technology Do?
A connected worker solution integrates the mobile applications of two or more operational groups to provide a single, unified source of accurate, real-time data that delivers end-to-end visibility enterprise-wide, across departments and processes. Simply put, with a connected worker platform, maintenance, and the warehouse can digitally communicate and collaborate to ensure spare parts are ready in time for an important project.
A connected worker platform also delivers valuable information that supports knowledgeable decision making. Finally, such a platform is equipped with operational dashboards to better facilitate certain actions.
Connected worker platforms offer users:
- Greater operational visibility throughout an enterprise
- Insight into the potential cause of a problem and its effects
- A way to assign resources and check spare part availability
- Improved collaboration to undertake recommended actions in a timely fashion
Who Needs a Connected Worker Platform?
Building materials and construction machinery manufacturing maintenance technicians need real-time visibility into current equipment health and performance to maximize reliability and reduce unscheduled downtime. When equipment goes down unexpectedly, frontline workers require quick access to operational and historical information to expedite repairs and complete them.
Warehouse workers in these same industries need a way to accurately track inventory across the entire process, from receiving to stocking to picking to shipping. A smoother, more efficient warehouse process reduces carrying costs, lowers tax bills, and helps maintenance ensure that requested parts are on-hand and ready to go when a work order is issued.
For supervisors and decision-makers, connected worker technology delivers instant, real-time information from the field. No more waiting for hours for a paper checklist to be turned in or inputted into the ERP. Instead, decision-makers get an immediate update on conditions within the plant or warehouse. They can make knowledgeable choices based on what's happening now, rather than relying on information that may already be out of date.
What to Look For In a Connected Worker Platform
Building materials and construction machinery manufacturers in the market for a connected worker platform will want six things in any solution they select.
- Offline capable: Allows frontline workers to continue working without a public or Wi-Fi network.
- Out-of-the-box integration: Seamless integration with Enterprise Resource Planning systems (systems of record).
- Operational dashboards: Delivers real-time visibility into operations for managers and supervisors, driving better decisions.
- Industry personas: Provides all the features for frontline workers in production, maintenance, and warehouses to work safer and more efficiently.
- No-code/low-code tools: Enables rapid scaling of the solution across operations and countries without the need to write code.
- Digital forms: Digitize end-to-end work processes with checklists, SOPs, work instructions, and training.
The Innovapptive Connected Worker Platform
Innovapptive is a global leader in developing and deploying connected worker solutions for industrial and manufacturing organizations. Our Connected Worker Platform helps manufacturers bridge maintenance and spare parts inventory teams to establish real-time communication.
It solves problems like:
- Manual data capture and human errors
- Poor integration with back-office systems
- Miscommunication and poor collaboration
- Lack of process flexibility and agility
- Reworks and backlogs
- Detached maintenance and spare parts inventory management
The platform combines two Innovapptive applications – mWorkOrder and mInventory – into one unified solution. This combination provides a single source of accurate, real-time data enterprise-wide across departments and processes.
mWorkOrder is an end-to-end work management application that supports preventive and predictive maintenance strategies that let maintenance teams move away from the inefficient and reactive "run-to-fail" approach. Frontline workers using mobile devices such as smartphones, scanners, tablets, and wearables fulfill maintenance work orders and perform inspections, operator rounds, equipment checks, etc. With these devices, operational data automatically uploads instantly to SAP.
mInventory integrates third-party barcode scanners and peripherals (or even the device's camera) to deliver a more efficient and accurate inventory-counting process. Gone are the cumbersome paper forms, tally sheets, and tickets that lead to frustrated employees, missing information, and incorrect counts. Instead, workers use smartphones and scanners to count, with continuously updated totals. This capability delivers accurate, verified data to key stakeholders, enabling them to make informed, knowledgeable warehouse management decisions in real time.
When these applications come together, building materials and construction machinery maintenance and warehouse workers can digitally communicate and collaborate to ensure spare parts are ready for an important project. The platform also delivers valuable information that supports knowledgeable decision making.
The Innovapptive Connected Worker Platform offers three control centers:
Maintenance Control Center: Integrated with mWorkOrder. Supervisors and managers can assign work orders to maintenance workers, send notifications, see real-time spare parts availability and kit status, and monitor work order progress from a single interface. Field workers can execute work orders within a paperless process.
Work Instructions Authoring Tool: Integrated with mWorkOrder. Maintenance planners and supervisors can create and attach digital work instructions to work orders to ensure work is completed right the first time with no reworks or backlogs.
Spare Parts Control Center: Integrated with mInventory. Digitizes warehouse processes to ensure maintenance teams receive the right parts at the right time to increase productivity. Supply chain managers can use the SPCC to assign and monitor warehouse tasks such as kitting parts for work orders.
Is a Connected Worker Platform Right For You? Find Out Today
Check out our recent ebook and case study about Innovapptive’s Connected Worker Platform to learn more about its capabilities. Then click here to arrange for a free no-obligation demonstration of our solution in action. Want to speak to one of our industry experts? They’re standing by to answer your questions now at 844-464-6668.
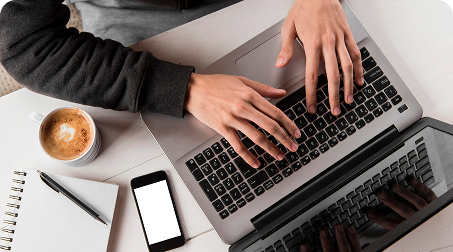
See It In Action
Schedule a personalized demo to see how our solutions can help your business thrive.
- 20-08-2025
Building the future of Industrial Operations with Innovapptive and AWS
Most manufacturers have already gone digital. Yet business outcomes haven’t moved in step. Many...
- 22-04-2025
The $3.6B Unlock: Solving the Chemical Industry’s Labor Crisis and EBITDA Pressure in One Move
“Constraints don’t slow innovation—they force it.”
- 21-04-2025
Chemical Industry's Margin Erosion: A Wake-Up Call for Operational Efficiency Amid China's Oversupply
The global chemical industry is facing mounting challenges, with revenue declines and shrinking...