Connected Worker Platforms: Revolutionizing Productivity in Construction Machinery and Building Materials
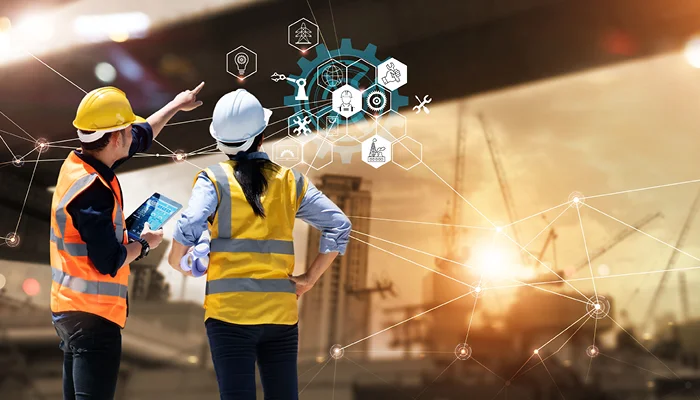
Labor is nearly always the largest expense for any building materials or construction machinery manufacturer. So, these organizations are always looking for ways to boost worker productivity. A promising industry newcomer that’s already transformed labor productivity in other fields may provide help. What is it? It’s called a connected worker platform.
The connected worker platform is a fast-growing digital solution that has enabled oil and gas, chemical, utilities, and mining organizations to make big productivity gains in their warehouses and maintenance departments. Frontline workers in those industries approach their daily tasks in a new way thanks to the connected worker platform. Now, this technology is ready to revolutionize building materials and construction machinery manufacturing in a similar manner.
What Is a Connected Worker?
You may have heard the term "connected worker" at a conference or in the news media, but aren't quite sure of its meaning. It's a simple concept. According to the Visual Capitalist, connected workers are “employees who carry out different tasks on-site or remotely using digital technologies.” Such workers are:
- Integrated into their environment and connected to other workers
- Empowered with real-time information
- Supported by their working systems
OK, seems easy enough, right? But how are these workers connected, and what are the benefits? Essentially, workers are connected via digital technology. This can include a smartphone application, a tablet, a wearable (such as smart glasses or a smart watch), and even drones. Workers use these devices to communicate and collaborate with their managers and supervisors in real time.
Because these devices are mobile, such communication and collaboration can occur anywhere, at any time.
How Does a Connected Platform Work?
For example, a building materials warehouse clerk on the shipping dock can collaborate directly and in real time with an item picker. Perhaps a large customer has added a request for additional drywall. The clerk can check inventory and immediately know that there is sufficient stock on hand to complete to amended order.
The clerk uses the connected worker platform to alert a picker that more drywall is needed, attaching a pdf of the amended requisition sheet. The picker can get the extra drywall to the shipping clerk to successfully fulfill the order and keep the customer happy.
Meanwhile, at a construction machinery manufacturer, a problem has arisen that threatens production of a custom set of cranes. If the problem isn’t fixed quickly, the cranes won’t be completed on time and the client will have to delay a construction project. Such a situation would jeopardize the manufacturer’s relationship with the construction contractor.
The plant’s maintenance technician lacks the experience to fix the production equipment problem. Thanks to a connected worker platform, the technician can communicate with the maintenance guru at a sister plant who has considerable experience dealing with similar issues. The technician dons a pair of smart glasses and engages in a two-way conference call with the guru. The guru virtually guides the technician and sends an SOP detailing the procedure to correct the problem. The machinery is quickly returned to production with no further issues.
Connected worker platforms don’t just connect frontline employees, managers, and supervisors; they also empower cross-departmental collaboration. Take our technician at the equipment manufacturer, for instance. He needs a spare part to complete the repair. Instead of having to leave the repair site to check with the parts warehouse, which might take an hour or two and add further delay, the technician can use the connected worker platform to digitally check warehouse inventory in real time, fill out a requisition, and receive an alert when the part is ready.
In each case, workers, managers, and supervisors have easier, faster access to information and each other. Slow or ineffective processes or tools like paper forms or walkie-talkies are banished, replaced by quicker and more efficient means that give greater response flexibility and agility to all involved.
Productivity Problems Connected Worker Platforms Solve
Too many building materials warehouses and construction machinery manufacturing plants are using inefficient and outdated processes to conduct operations. Primarily we’re talking about paper-based work order forms, checklists, inventory tally sheets, and supply requisitions.
Organizations using inefficient processes (like paper) have several bad attributes in common. For example, they:
- Lack real-time visibility into daily operations
- Rely on manual data collection, entry, and sharing
- Have numerous information silos where data gets stranded
- Have difficulty making knowledge-based decisions
- Suffer low worker productivity and wrench time
- Pay more overtime than necessary to get work done
Warehouses in this category frequently employ many repetitive and counterproductive tasks that require more work and effort rather than less. Many building materials warehouse managers fret about how these four issues negatively impact worker productivity:
- Inventory control and tracking issues
- Low or no-value inventory data
- Transaction and processing errors
- Use of outdated technology
Meanwhile, at the equipment manufacturer, too many maintenance technicians must perform tasks other than an actual wrench. Rather than using a hammer, a drill, or a power saw, they're instead waiting on materials, traveling to and from job sites or warehouses, or something else. The result is that productivity suffers.
Adopting a digital solution, such as a connected worker platform, offers numerous benefits. Primarily, it minimizes paper-based documentation, allowing frontline employees in the warehouse or the machinery plant to move freely with a mobile device in hand and remain productive. Managers and supervisors can follow progress and receive updates in real time from anywhere. Such capabilities empower proactive decision making based on knowledge. It also enables companies to become nimbler in proactively addressing issues before they become production-stopping problems.
This situation is a complete sea change from how many warehouses and job sites function today. Instead of real time updates and proactive actions, supervisory personnel must wait for information to reach them before they can do anything. It's a reactionary setup, lacking flexibility and agility. Decisions are made more on hunches, guesswork, and experience.
Managers and supervisors aren't the only ones that benefit from a connected worker platform. Frontline workers also gain from their adoption.
Join the Connected Worker Revolution Today – Here’s How
Why maintain the status quo? There’s a better way to increase productivity at a building materials warehouse and the construction job site. Ditch paper-based processes and adopt a connected worker solution.
Innovapptive is a connected worker platform pioneer. We've helped several big-name clients digitally revolutionize and transform outdated operational processes. By connecting their workforces in the warehouse and at the machinery manufacturing plant, these clients gained deeper visibility, could make more informed decisions, and increased frontline worker productivity. Read our free case study here. Then visit our website to see our connected worker platform in action. You can arrange a no-obligation demonstration here. Have questions or want to speak to a live person? Our industry experts are standing by now to help. Simply call 1-844-464-6668.
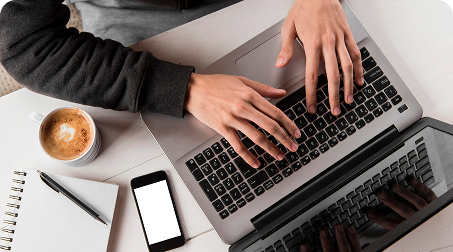
See It In Action
Schedule a personalized demo to see how our solutions can help your business thrive.
- 20-08-2025
Building the future of Industrial Operations with Innovapptive and AWS
Most manufacturers have already gone digital. Yet business outcomes haven’t moved in step. Many...
- 22-04-2025
The $3.6B Unlock: Solving the Chemical Industry’s Labor Crisis and EBITDA Pressure in One Move
“Constraints don’t slow innovation—they force it.”
- 21-04-2025
Chemical Industry's Margin Erosion: A Wake-Up Call for Operational Efficiency Amid China's Oversupply
The global chemical industry is facing mounting challenges, with revenue declines and shrinking...