The Connected Worker Revolutionizes Manufacturing with Mobile Work Orders
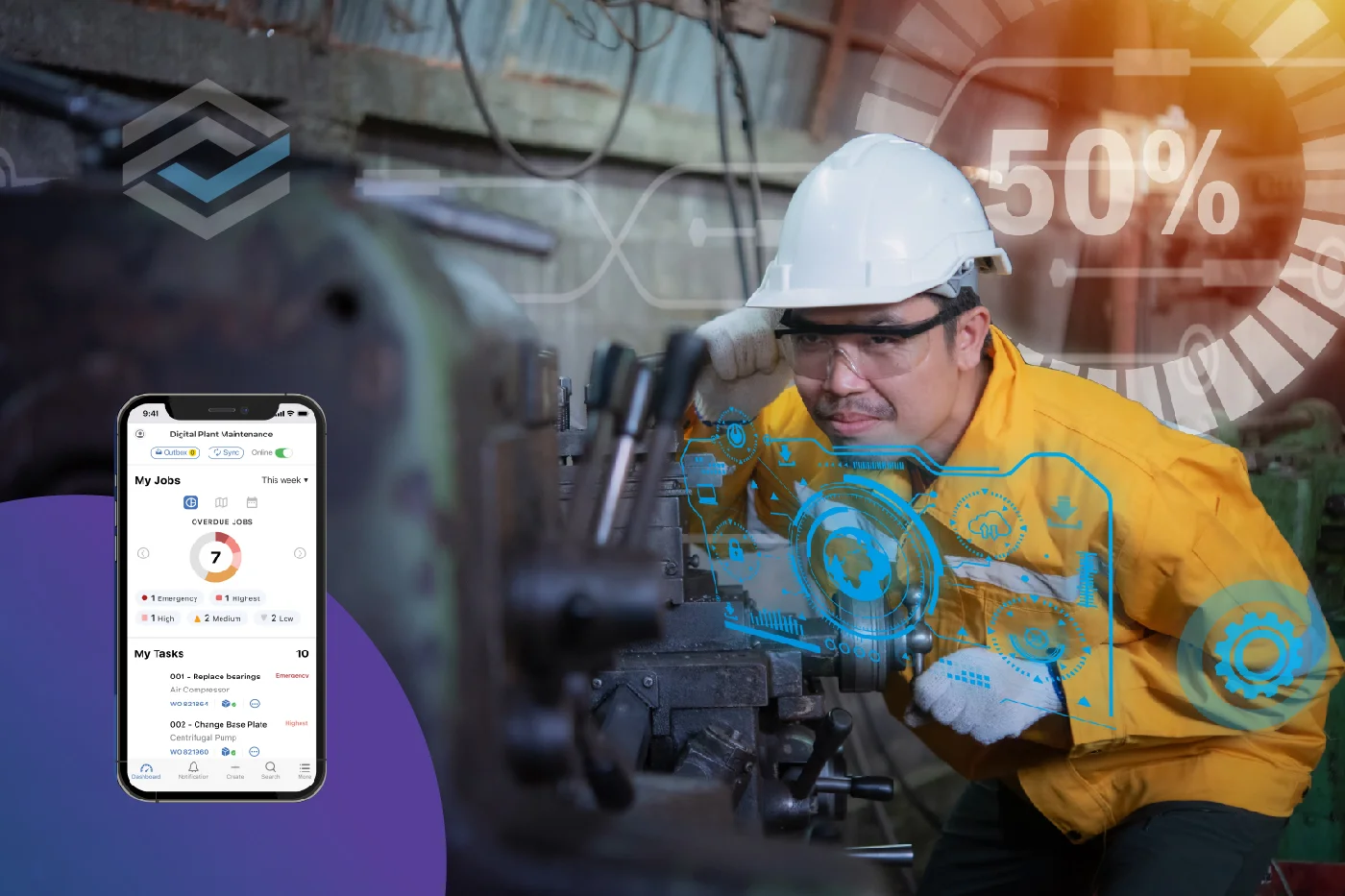
In the fast-paced world of manufacturing, efficiency is king. Every second wasted searching for information, troubleshooting issues, or waiting on approvals can lead to costly downtime and missed production targets. But imagine a world where workers have instant access to critical information, guided step-by-step through procedures, and empowered to collaborate seamlessly – all thanks to mobile work orders delivered to their fingertips. This is the Connected Worker revolution, and it's transforming manufacturing.
The Pain of Paper-Based Work Orders
Let's face it, traditional paper-based work orders are cumbersome, prone to errors, and a drain on productivity. Imagine technicians scrambling for misplaced documents, deciphering handwritten instructions, or waiting for approvals stuck in email chains. These inefficiencies translate to:
- Increased downtime: Precious minutes wasted searching for information or approvals.
- Human error: Misinterpretations of instructions can lead to costly mistakes.
- Poor communication: Delays and bottlenecks due to lack of real-time visibility.
Enter the Mobile Work Order Hero
Now, picture this: workers equipped with smart devices receiving dynamic, digital work orders. These orders, powered by the Connected Worker concept, unlock a new level of efficiency:
- Real-time access to information: Procedures, schematics, and relevant data are readily available at the point of work, minimizing downtime due to information gaps.
- Step-by-step guidance: Augmented reality (AR) overlays provide visual instructions, reducing error rates and ensuring consistent quality.
- Instant collaboration: Workers can share photos, videos, and notes with colleagues and experts in real-time, accelerating problem-solving.
- Seamless approvals: Electronic signatures and approvals eliminate delays and keep the production line moving.
The Tech Stack Powering the Transformation
This mobile magic isn't accidental; it's fueled by a powerful tech stack:
- Mobile App Development: Intuitive and user-friendly apps deliver work orders directly to worker devices.
- Cloud Computing: Data is securely stored and accessible from anywhere, anytime.
- Internet of Things (IoT): Sensors embedded in machines provide real-time data for predictive maintenance and process optimization.
- Artificial Intelligence (AI): AI algorithms analyze data to identify potential issues and recommend corrective actions.
More Than Just Mobile
While mobile work orders are a game-changer, the Connected Worker vision extends beyond devices. It's about empowering individuals through:
- Upskilling and training: Equipping workers with the skills to leverage technology effectively.
- Data-driven decision making: Encouraging workers to analyze data and suggest improvements.
- A culture of collaboration: Fostering teamwork and knowledge sharing across departments.
Real-World Impact
The proof is in the pudding. Manufacturers embracing mobile work orders and the Connected Worker approach are reporting:
- Significant reductions in downtime.
- Improved production efficiency and quality.
- Enhanced worker safety and satisfaction.
- Data-driven insights for continuous improvement.
The Road Ahead
The future of mobile work orders and the Connected Worker is bright, with even more exciting possibilities on the horizon:
- Edge computing: Bringing AI and analytics closer to devices for faster, more localized decision-making.
- Digital twins: Creating virtual replicas of physical assets for advanced simulations and optimization.
- Extended reality (XR): Immersive training experiences to upskill workers faster and more effectively.
Beyond the Technology
Remember, technology is a tool, not a replacement. Successful implementation requires:
- Addressing workforce concerns: Open communication and training are crucial to manage anxieties about job displacement.
- Responsible data practices: Ensuring data privacy and security is paramount.
- Focus on the human element: Technology should empower workers, not dehumanize them.
The Mobile Work Order Revolution: It's Happening Now
Mobile work orders, coupled with the Connected Worker approach, are not futuristic dreams, but present-day realities transforming the manufacturing landscape. By embracing technology, empowering people, and fostering a culture of innovation, manufacturers can unlock new levels of efficiency, agility, and profitability. So, step into the future, equip your workforce with mobile superpowers, and watch your production soar.
Diving Deeper into Manufacturing Pain Points: A Mobile Work Order Antidote
In our previous exploration of the "Connected Worker" revolution, we touched upon the pain points plaguing traditional paper-based work orders. But let's delve deeper into the broader challenges currently hindering the manufacturing industry, and how mobile work orders, empowered by the Connected Worker vision, can serve as an effective antidote.
Beyond Paperwork Woes
While inefficient work orders are a significant bottleneck, they merely represent the tip of the iceberg. Here are some of the major pain points manufacturers face today:
- Talent Shortage and Skills Gap: The industry struggles to attract and retain skilled workers, leading to production delays and decreased quality. Mobile work orders, paired with upskilling initiatives, can bridge the gap by:
-
- Providing intuitive, step-by-step guidance: Reducing reliance on senior workers for basic tasks.
- Offering on-demand access to training materials: Enabling continuous learning and skill development.
- Facilitating knowledge sharing: Connecting experienced workers with newcomers, fostering collaboration.
- Supply Chain Disruptions: Uncertain material availability and unpredictable lead times disrupt production flow. Mobile work orders, integrated with real-time inventory data and supplier networks, can help by:
-
- Enabling dynamic scheduling and material allocation: Adapting to changing circumstances quickly.
- Providing early warnings of potential shortages: Triggering proactive sourcing and procurement strategies.
- Improving communication and collaboration with suppliers: Streamlining logistics and expediting deliveries.
- Quality Control and Traceability: Maintaining consistent quality and accurately tracking production history can be cumbersome. Mobile work orders, integrated with quality control tools and digital twins, can offer:
-
- Real-time data capture and analysis: Identifying quality deviations early in the process.
- Digitized inspection checklists and reports: Eliminating paperwork errors and ensuring traceability.
- QR code integration for parts and materials: Tracking provenance and ensuring correct usage.
- Safety Concerns and Compliance: Accidents and regulatory violations can lead to hefty fines and production stoppages. Mobile work orders, combined with safety checklists and training modules, can promote:
-
- Safe work practices with visual reminders and procedures.
- Real-time incident reporting and corrective action.
- Compliance with safety regulations and certifications.
- Data Silos and Lack of Visibility: Fragmented data across departments hinders informed decision-making. Mobile work orders, integrated with a central platform, can provide:
-
- Real-time performance dashboards and analytics.
- Data-driven insights for process optimization and resource allocation.
- Improved collaboration and information sharing across teams.
The Mobile Work Order Advantage
By addressing these fundamental pain points, mobile work orders equipped with the Connected Worker approach can create a ripple effect of positive change:
- Increased productivity and efficiency.
- Improved quality and reduced defects.
- Enhanced worker safety and satisfaction.
- Data-driven decision making and continuous improvement.
- Stronger resilience to disruptions and agile problem-solving.
Remember, the transition to a connected workforce requires more than just technology. Successful implementation involves:
- Leadership buy-in and clear communication of goals.
- Collaboration with workers to address concerns and ensure adoption.
- Investment in training and upskilling programs.
- Selection of secure and user-friendly technology solutions.
By embracing this holistic approach, manufacturers can unlock the full potential of mobile work orders and the Connected Worker, transforming their operations and propelling themselves towards a brighter, more efficient future.
Ready to Learn More? Here’s How
Innovapptive is a global leader in providing Connected Worker Solutions to industrial and manufacturing plants. These solutions can help your organization improve operations, maintenance, and warehouse processes and productivity. Watch our informative video and then click here to schedule a free, no-obligation demonstration of our solutions in action.
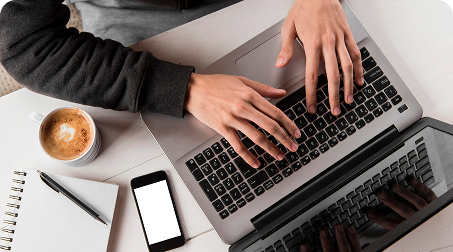
See It In Action
Schedule a personalized demo to see how our solutions can help your business thrive.
- 20-08-2025
Building the future of Industrial Operations with Innovapptive and AWS
Most manufacturers have already gone digital. Yet business outcomes haven’t moved in step. Many...
- 22-04-2025
The $3.6B Unlock: Solving the Chemical Industry’s Labor Crisis and EBITDA Pressure in One Move
“Constraints don’t slow innovation—they force it.”
- 21-04-2025
Chemical Industry's Margin Erosion: A Wake-Up Call for Operational Efficiency Amid China's Oversupply
The global chemical industry is facing mounting challenges, with revenue declines and shrinking...