COVID-19 Response Plan: A “Mobile-First” Digital Inventory & Warehouse Management Platform to Reduce Oil & Gas Inventory Risks
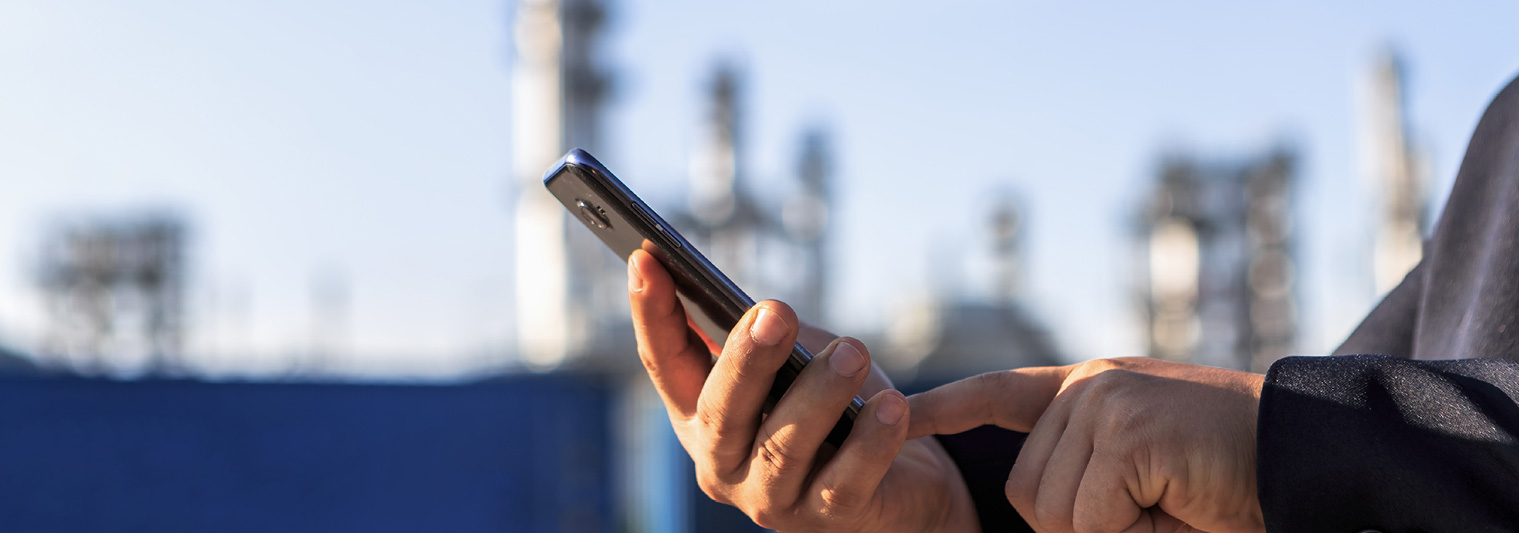
The global COVID-19 pandemic is having a huge impact on the world’s oil and gas industry. With entire cities and even nations being locked down to contain the spread of the virus, demand for oil and gasoline has plummeted by up to 20 million barrels a day. Compounded by the price war between Russia and Saudi Arabia, the price of West Texas Intermediate Light Sweet crude, at a 2020 high of $63.70 a barrel on Jan. 7, dropped nearly 27 percent to $46.75 by Mar. 2, and plunged dangerously close to the $20 mark at the close of Q1 2020.
After only a few weeks of the COVID-19 pandemic and the price war, companies in every corner of the industry are switching to survival mode, looking for ways to cut expenses, improve productivity and boost operational efficiency to weather this perfect storm.
One area ripe for expense, operational and productivity optimization is the oil and gas supply chain, especially at the MRO warehouse level. By maximizing efficiencies here, companies can reduce costs and ensure continued production, even in remote areas like offshore.
An oil and gas MRO warehouse’s role is to receive parts from suppliers, store parts, pick against work orders and ship the parts to waiting engineers and maintenance technicians at the plant or platform. Warehouse inventory movements are controlled through an ERP system such as SAP. (although the ERP likely lacks Warehouse Management functionality). This means the warehouse uses paper forms and slips to process items. Paper-based systems are time consuming, error prone and create a systematic disconnect between the physical world and the digital one. This often creates undesirable situations to not have the right parts at the right time during an emergency.
Oil and gas companies are looking for ways to gain greater visibility into their inventory, spare parts and warehouse operations to speed deliveries, reduce costs and minimize downtime. They want a more efficient process that cuts down on errors, increases accuracy and provides a clear picture of their warehouse and last mile process. They’d also welcome the elimination of the paper-based warehouse process. For one, it’s slow and cumbersome. And, in the current COVID-19 pandemic, paper exposes warehouse workers to a much greater chance of infection and illness. Recent research in the American Journal of Nursing (AJN), April 2020, Vol. 120, Issue 4 suggests that test organisms were transferred to paper, survived on it, and were retransferred back to hands, raising the risks of COVID-19 pandemic spread.
When an oil and gas platform or rig goes offline unexpectedly, even for a short time, the company sees its production drop, its revenue stream interrupted and its ability to timely satisfy customers’ orders curtailed. Now with oil and gas demand dropping, keeping revenues flowing and customers happy are more important than ever. In fact, the company’s survival during the COVID-19 crisis may be at stake.
That means it’s vital that maintenance staff and engineers be able to get needed parts and equipment to make the required repairs to get production moving again. A poorly organized warehouse relying on an inefficient paper-based process makes that job much more difficult, needlessly stretching out costly downtime at the worst possible time. Instead of quickly finding, picking, loading and shipping the parts to the platform or rig, warehouse clerks are sifting through paper documents to see what’s available only to find their recordkeeping is off. What’s supposed to be in the bin simply isn’t there and no one knows for sure if it’s a stock out or if the parts have simply been misplaced. All the while, the clock is ticking and revenue is being siphoned away.
Oil and gas companies want something that would allow them to:
- Eliminate manual, paper-dependent processes, increasing efficiency and reducing risks of COVID-19 infection.
- Accelerate warehouse goods receipt, putaway, picking, packing and dispatch.
- Track and manage oil and gas inventories with real-time accuracy.
- Provide field technicians with access to crucial inventory information.
- Lower inventory carrying costs.
Innovapptive, a mobile-first Connected Workforce platform provider, offers a robust solution that meets all the above. Our mInventory digital solution enables oil and gas MRO warehouses to quickly, efficiently and safely ensure the right part gets sent to the platform so repairs can be made and production restarted.
mInventory (Watch Video) provides control of the final mile from onshore warehouse to offshore platform by working seamlessly with SAP’s Remote Logistics Management (RLM) module. mInventory provides supply chain decision makers and supervisors the information they need to track parts, equipment and materials.
With mInventory’s mobile-first, digital capabilities, items come into the warehouse and go through each step of the process – from goods receipt to goods dispatch – with no paper required. No paper putaway slips, picking slips, packing slips … everything is electronic. There’s nothing to manually input, either onto a form or into the system of record, such as SAP.
Instead, warehouse workers armed with mobile devices such as smartphones, tablets, scanners, wearables, etc., scan incoming items’ barcodes or use optical character recognition (OCR) technology to read information and assign storage bins. Likewise, when an item is needed to ship to a platform or other facility, goods can be located, picked, packaged and dispatched electronically. Once the item is sent, mInventory works with RLM to give greater control over the outbound process. At each step, decision makers have immediate, real-time access to data via mobile applications. When an engineer or maintenance technician calls to inquire about where a part is, the answer is never, “I don’t know.” Rather it’s what the engineer or tech wants to hear: “We dispatched the part an hour ago. It’s on the supply boat now, on its way for delivery.”
mInventory, working in conjunction with SAP’s RLM module, lets oil and gas companies:
- Switch to a completely digital process, with no paper
- Accelerate receipt and backorder reporting by over 35%
- Manage inventory movement in real time, from receipt to final mile delivery
- Improve inventory accuracy by 30%
- Expedite physical and cycle counts with 98% accuracy of inventory levels
- Reduce inventory carrying costs by as much as 10%
Based on clients’ previous best experiences.
To learn more about how mInventory’s RLM capabilities can provide greater supply chain visibility, inventory accuracy and warehouse efficiency, schedule a free demo today by calling 844-464-6668 or by clicking here.
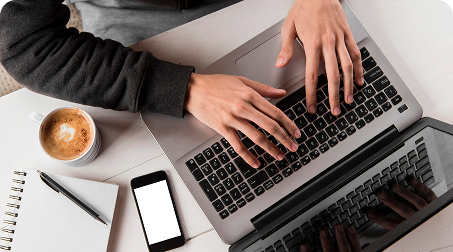
See It In Action
Schedule a personalized demo to see how our solutions can help your business thrive.
- 22-04-2025
The $3.6B Unlock: Solving the Chemical Industry’s Labor Crisis and EBITDA Pressure in One Move
“Constraints don’t slow innovation—they force it.”
- 21-04-2025
Chemical Industry's Margin Erosion: A Wake-Up Call for Operational Efficiency Amid China's Oversupply
The global chemical industry is facing mounting challenges, with revenue declines and shrinking...
- 21-04-2025
Why Wrench Time Isn’t Improving: The Hidden Costs of Traditional Maintenance Scheduling
For years, industrial leaders have relied on a common but flawed assumption: "Better planning and...