Data Digitalization Drives the Rise of the Connected Worker
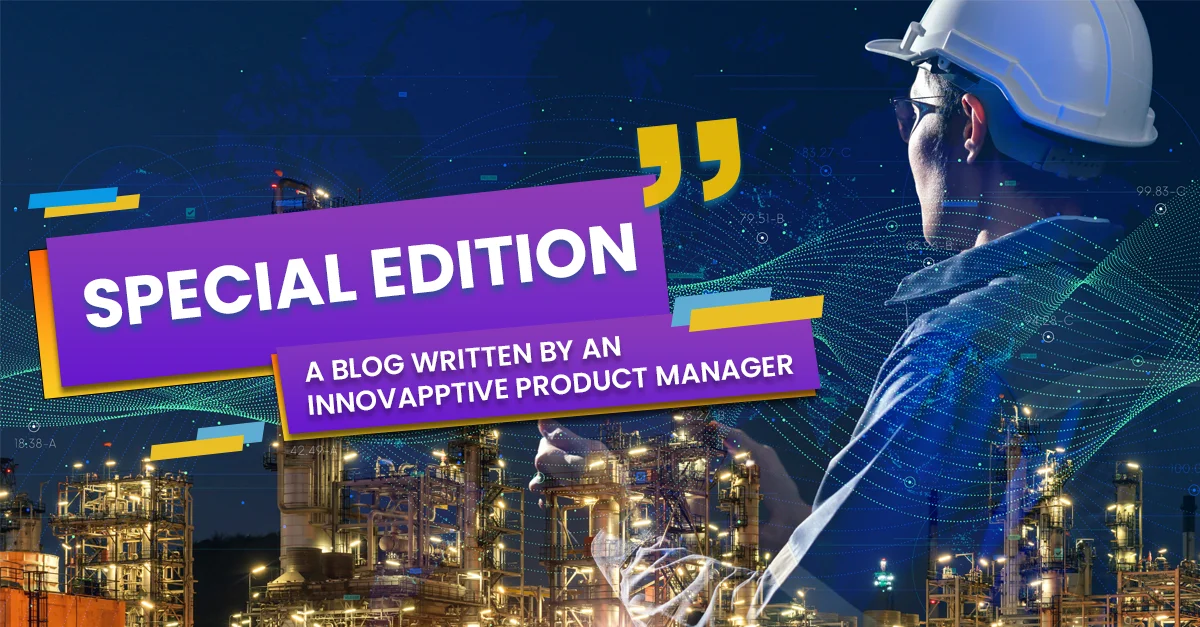
The industrial arena has always been at the forefront of innovation. Starting with the Industrial Revolution of the late 1700s, factories and plants have sought ways to make better use of people and machines. The latest effort towards that goal pairs mobile digital technology with frontline workers to create a new breed of employee – the connected worker.
What’s a connected worker? How can this new breed help your company prosper in the years ahead? We’ll take a closer look at this growing workplace phenomenon in the first of a three-part series.
Today we’ll examine:
- Why technology needs a more prominent spot on the factory floor
- The trend towards industrial digitalization
- The increasing role of data in a modern industrial organization
- Where to go to learn more about adopting digital transformation and connected worker solutions for your organization
Connected Worker Technology Needs a Bigger Place on the Factory Floor
Industrial operations, warehouse and maintenance frontline workers perform daily mission-critical tasks. Unfortunately, how they performed day-to-day tasks didn’t change much when the 20th century made way for a new millennium. Each of these roles utilized very little technology. Frontline workers carried clipboards and binders from place to place and communicated with supervisors and each other via walkie-talkies.
Paper-based systems greatly slow the data gathering and sharing process. What’s passed up the chain is often hours, even days old, making it inaccurate and nearly useless. This situation hinders decision makers, who need accurate, real-time information to improve the choices they make. Such systems make processes more difficult. They also put users at a competitive disadvantage.
Asset-intensive organizations need a faster, nimbler and more accurate means to get operational data to supervisors, managers and directors. And they want a better method for decision makers and frontline workers to collaborate. This way everyone can take full advantage of the wealth of operational data available in a modern production facility.
Digital Transformation Is Forever Altering the Workplace
The last decade has seen a drastic change in the ways people engage with their jobs and the workplace. Digital transformation is sweeping the globe as companies seek to make frontline workers an increased role in their production workflows.
Until now, industrial organizations only used technology to digitalize asset and operations data. Companies sought to improve core functional areas, such as:
- Asset and resource utilization
- Process and product quality
- Reliability
- Operational energy management
- Production floor efficiency
Organizations have made great strides away from paper-based data collection and storage systems. However, most of the treasure trove of information was inaccessible to those most in need – the frontline worker. They had little or no access to the back-office systems that store the data. Frontline workers couldn’t use the power of information to improve their jobs, performance or safety.
Digital transformation addresses this issue. New technologies empower frontline workers. Now, rather than being locked out from critical asset and operational data, such information becomes an integral part of their everyday work lives. This situation stands in stark contrast to the industrial workplace of just 10 years ago.
Data, Not Raw Materials, Are Now the Most Critical Part of the Industrial Process
Asset-intensive industries such as chemical processing, oil and gas, mining, and utilities are actively seeking new and productive ways to harness the power of their operational data. They want to transform such data into actionable insights. Supervisors and frontline workers can use these data-driven insights to make critical decisions at the point of work.
Integrating operational data and insights into the workflow can positively impact frontline worker productivity, equipment uptime, plant safety, regulatory compliance and profit margins. Digital transformation adds greater process visibility, which non-data-driven organizations lack. It also delivers agility, flexibility and nimbleness. Frontline workers can proactively respond to issues before they become production-stopping problems. Data becomes a crucial part of a modern industrial operation.
Put Your Operational Data to Optimum Use with a Connected Worker Solution
Innovapptive, a digital transformation and connected worker solution leader, specializes in SAP- and IBM Maximo-compatible mobile plant maintenance systems. These systems simplify the collection and sharing of operational data to improve technician productivity, transform reactive processes and cut downtime costs. Schedule a free demo of a world-class connected worker platform or call 888-464-6668. Our industry experts will be glad to explain the connected worker concept and guide you through how it can benefit your enterprise.
Vinod K. Vijayan has more than 16 years’ of experience in the MRO & Engineering space, with a focus on the aviation and aircraft engineering industry.
At Innovapptive, Vinod primarily looks after the Operator Rounds solution, where he helps customers plan and execute best practices for end-to-end asset management in the connected worker space
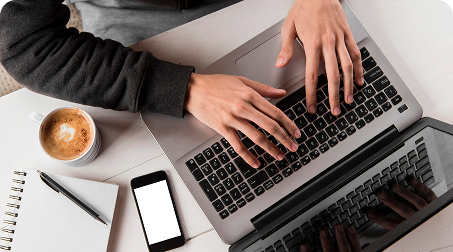
See It In Action
Schedule a personalized demo to see how our solutions can help your business thrive.
- 20-08-2025
Building the future of Industrial Operations with Innovapptive and AWS
Most manufacturers have already gone digital. Yet business outcomes haven’t moved in step. Many...
- 22-04-2025
The $3.6B Unlock: Solving the Chemical Industry’s Labor Crisis and EBITDA Pressure in One Move
“Constraints don’t slow innovation—they force it.”
- 21-04-2025
Chemical Industry's Margin Erosion: A Wake-Up Call for Operational Efficiency Amid China's Oversupply
The global chemical industry is facing mounting challenges, with revenue declines and shrinking...