Five mWorkOrder Features that Bolster Mining Preventative Maintenance
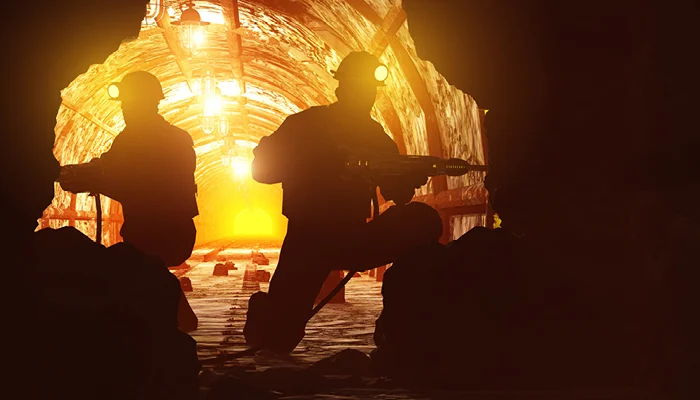
Two global mining giants recently warned of tough times ahead for the industry. Mines will need to keep production and revenues steady to weather such a rough patch. The best way to do that is to adopt a preventative maintenance program for mining equipment, and a mobile frontline worker application is one method of achieving that goal.
Preventative Maintenance Incurs Fewer Risks and Costs
Mines using inefficient, reactive maintenance processes like run-to-fail have several common attributes. They:
- Pay more for maintenance
- Lack real-time visibility into operations
- Rely on manual and paper-based data collection, entry and sharing
- Have numerous information silos where data gets stranded
- Experience poor equipment reliability
Forward-thinking mine maintenance directors, planners, schedulers, and managers realize that proactive, preventative maintenance programs relying on real-time data to identify and take remedial action before equipment breaks are the most efficient, economical and safe processes. Preventative maintenance can reduce unplanned downtime as well as help in:
- Maintaining efficiency in aging equipment
- Diagnosing equipment problems
- Prolonging asset lifespan
- Frontline worker safety
Using Mobile Frontline Worker Applications in Mining Preventative Maintenance
The digital transformation revolution has forever altered the way organizations approach maintenance. Mobile frontline worker applications enable frontline workers using mobile devices, such as smartphones, scanners, tablets, and wearables, fulfill maintenance work orders and perform inspections, operator rounds, equipment checks, etc. Operational data is uploaded instantly to the back-office system of record. Eliminating paper forms and manual data input boosts wrench time. It also cuts administrative costs.
The mWorkOrder Mobile Maintenance Solution for Mining
Innovapptive’s mWorkOrder supports preventive maintenance strategies that let mining maintenance teams move away from the inefficient and reactive “run-to-fail” approach. mWorkOrder increases communication between field technicians and supervisors:
- Managers can create and issue digital work orders and then follow their progress in real time, gaining greater visibility into the maintenance process
- Supervisors instantly receive work order updates and can send push notifications to their frontline workers’ mobile devices to notify them immediately of tasks or other information
- Frontline workers can digitally gather operational data while in front of the asset or piece of equipment and upload it automatically to SAP or IBM Maximo
- Decision makers can view this information in real time and take immediate remedial action to forestall or prevent unplanned equipment downtime
mWorkOrder can be used at any mining operation – open pit, surface, subsurface or in-situ – to increase the uptime of extraction, handling and processing equipment.
What Makes mWorkOrder the Right Choice for Your Mine?
mWorkOrder offers five main differentiators from other mobile preventative maintenance solutions. These differentiators will enable your mining organization to move away from inefficient reactive maintenance processes, increase equipment uptime and reliability, enjoy high user adoption rates and enjoy a positive return on investment.
Online/offline modes – mWorkOrder offers online/offline modes, allowing frontline workers and managers to be productive even when there’s no Wi-Fi signal, as can often be the case with mines operating in remote locations far from infrastructure. Take advantage of rapid synchronization after restoring a connection.
Rapid customization – mWorkOrder utilizes the proprietary, patented RACE™ (Rapid Application Configuration Engine) platform that empowers quick, easy no-code/low-code customization with no prior coding knowledge or experience. Configure the application for site, role, user and geographies. Quickly respond and adapt to changes, and better align the solution to your unique business requirements.
User interface/user experience – mWorkOrder is intuitive and easy to use with minimum training required to be productive. Satisfaction leads to high user adoption rates.
Integration with ERP systems – mWorkOrder seamlessly integrates with ERP systems, such as SAP and IBM Maximo.
Scalability – mWorkOrder can grow as your business expands to meet your ever-changing operational needs and requirements.
Ready to Take the Next Step? Here’s How to Learn More
This two-minute video looks at mWorkOrder’s power and versatility to change your reactive maintenance process to a proactive, preventative model. When you’ve finished, click here for a free demo. Have additional questions? Our experts are standing by now, ready to help. Give them a call at 844-464-6668.
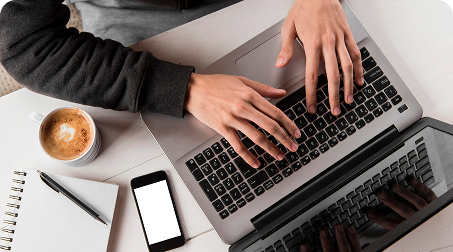
See It In Action
Schedule a personalized demo to see how our solutions can help your business thrive.
- 22-04-2025
The $3.6B Unlock: Solving the Chemical Industry’s Labor Crisis and EBITDA Pressure in One Move
“Constraints don’t slow innovation—they force it.”
- 21-04-2025
Chemical Industry's Margin Erosion: A Wake-Up Call for Operational Efficiency Amid China's Oversupply
The global chemical industry is facing mounting challenges, with revenue declines and shrinking...
- 21-04-2025
Why Wrench Time Isn’t Improving: The Hidden Costs of Traditional Maintenance Scheduling
For years, industrial leaders have relied on a common but flawed assumption: "Better planning and...