Forget Everything You Know About Preventive Maintenance: AI Changes the Game
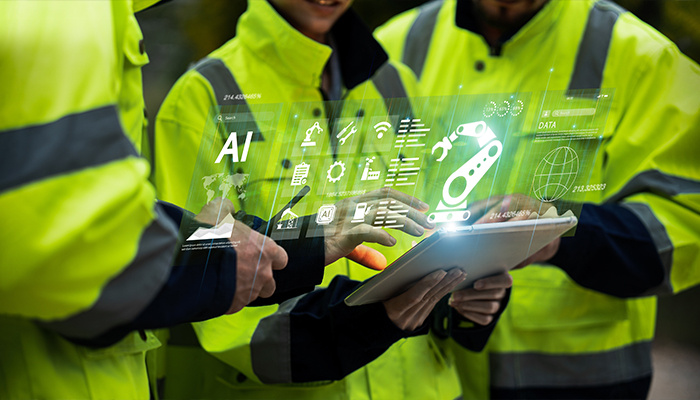
Introduction
Let's talk about something every plant manager dreads—downtime. It's expensive, disruptive, and, in many cases, totally preventable.
According to Siemens' 2024 Downtime Report, the cost of an idle production line in a process industry plant has surged to $59 million a year—that’s 1.6 times higher than in 2019.
To combat this, companies have long relied on preventive maintenance to minimize unexpected breakdowns.
Clearly, traditional time-based preventive maintenance isn’t cutting it anymore. But here’s the good news—AI-driven preventive maintenance is stepping in to change the game.
1. The Problem with Old-School Preventive Maintenance
For years, industrial preventive maintenance has relied on rigid, paper-based processes and calendar-based schedules. The result?
- Unnecessary maintenance on assets that don’t actually need servicing.
- Surprise failures that scheduled maintenance couldn’t catch.
- Sky-high maintenance costs with little to show for it.
- Wasted manpower, time, and resources on outdated processes.
- Limited real-time access to critical information.
- Maintenance backlog due to low technician productivity.
For example, one of the most pressing challenges in preventive maintenance is the growing maintenance backlog caused by low technician productivity. This issue stems from several factors like inefficient task allocation, lack of proper tools and resources, inadequate training and skill gaps and poor communication between teams.
To impact of outdated preventive maintenance on backlogs is huge, based on the following table:
*Industrial Data 2023-24
The backlog impact is huge and with increasing complexity in manufacturing operations, industries need preventive maintenance solutions that are smarter, faster, and more cost-effective.
2. How AI is Flipping the Script on Preventive Maintenance
AI doesn’t just improve preventive maintenance solutions—it completely transforms how maintenance works.
AI-Driven Predictive Insights
- AI crunches real-time sensor data to predict failures before they happen.
- It ditches fixed maintenance schedules in favor of data-driven servicing.
- AI-driven maintenance means more uptime, lower costs, and fewer surprises.
How Gen AI is Enhancing Preventive Maintenance
Generative AI is transforming maintenance by addressing skill gaps, improving efficiency, and streamlining knowledge retention. Companies are leveraging Gen AI to:
-
Boost workforce productivity – Virtual agents assist with planning, scheduling, troubleshooting, and repair, helping less-experienced staff perform better.
-
Enhance access to maintenance knowledge – AI-powered search and summarization generate fault diagnosis steps automatically.
-
Accelerate training and onboarding – Automated learning tools upskill new staff quickly, reducing integration time.
Leading organizations are rapidly deploying Gen AI to solve persistent maintenance challenges. According to McKinsey, a company in the oil and gas sector is using Gen AI to automate Failure Modes and Effects Analysis (FMEA) across thousands of equipment items. FMEA helps identify potential failures, assess risks, and prioritize corrective actions, but it is often time-consuming and complex. AI automates this process, improving efficiency and reducing lead times from months to weeks.
-
Maximizing Workforce Productivity
When issues arise, AI systems generate automatic notifications that include detailed troubleshooting steps. This proactive approach empowers technicians to address problems efficiently, reducing downtime and improving overall equipment effectiveness.
- AI automates routine industrial maintenance software tasks.
- Maintenance teams get real-time alerts and actionable recommendations.
- AI-driven connected worker solutions ensure that technicians always have the right tools, right insights, and right tasks.
Equipment That Runs Smoother, Longer
AI algorithms continuously monitor equipment health, detecting subtle changes that may indicate potential failures. This early detection allows for timely interventions, significantly improving equipment reliability and uptime.
- AI integrates with enterprise asset management (EAM) to fine-tune maintenance cycles.
- Predictive analytics slash unplanned downtime and boost operational efficiency.
- Digital twin technology simulates equipment performance, preventing breakdowns before they occur.
3. AI in Action: Preventive Maintenance for Oil & Gas and Chemical Manufacturing
Oil and Gas - Preventive Maintenance
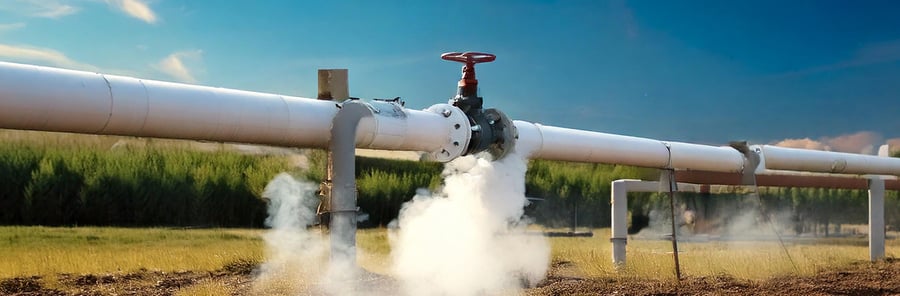
Imagine this: A pipeline leak in an offshore drilling site goes unnoticed until it causes a major production shutdown—unplanned downtime. The environmental damage, financial losses, and regulatory fines are massive.
With AI-driven preventive maintenance:
- AI-powered corrosion detection monitors pipeline health and schedules maintenance before failures occur.
- Preventive maintenance scheduling optimizes routine inspections to prevent unexpected equipment wear.
- Refinery digital shift logs ensure historical data is used to refine maintenance planning and prevent recurring failures.
- AI-driven mobile maintenance management keeps teams connected with real-time alerts and repair insights.
Chemical Manufacturing - Preventive Maintenance
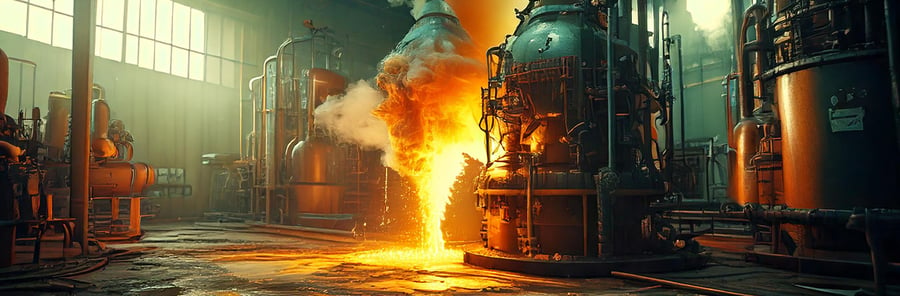
Picture a high-precision chemical plant where a minor equipment failure leads to contamination, causing product recalls worth millions.
With AI-driven preventive maintenance:
- AI enforces preventive maintenance compliance to meet strict industry regulations (FDA, GMP).
- Time-based preventive maintenance ensures equipment calibration before deviations impact production.
- AI-driven scheduling optimizes cleaning and servicing cycles to prevent downtime in sterile environments.
- AI-powered anomaly detection minimizes risks by continuously monitoring production assets.
4. Innovapptive Transforms Preventive Maintenance with AI
Today, maintenance teams spend too much time on manual tasks—checking equipment, filling out paperwork, and chasing down approvals. Breakdowns still happen, and preventive maintenance often feels like guesswork. But AI is changing that. Instead of relying on scheduled checks and reactive fixes, AI automates the entire workflow, ensuring the right work gets done at the right time—without wasted effort.
How Innovapptive Leverages AI to Automate Maintenance—From Detection to Execution
- AI Detect – Spot Problems To Minimize Downtime
Instead of relying on manual inspections, AI Detect identifies and alerts teams to potential risks, enabling proactive intervention to minimize downtime. It analyzes equipment conditions in real time, instantly detecting issues so the necessary action can be taken—eliminating unexpected breakdowns and last-minute scrambling. - AI Assist – Get Fixes Right the First Time
When an issue is detected, maintenance teams no longer need to waste time searching for solutions. AI Assist suggests the best course of action—whether it’s adjusting machine settings, replacing a part, or scheduling lubrication. With step-by-step guidance, technicians can resolve issues faster and with fewer mistakes, improving first-time fix rates and MTTR. - AI Plan – Automate Scheduling and Work Orders
Once an issue is detected and assessed, AI Plan expedites the process of creating work orders in a few clicks. It considers asset criticality and technician availability to optimize preventive maintenance. No more guesswork, just smart scheduling that prevents downtime and maximizes productivity. - AI Author – Create Smarter Workflows and SOPs
Instead of filling out forms manually or hunting for the right SOP, AI Author automates workflow creation. It helps supervisors and managers generate digital work orders, checklists, and SOPs with pre-filled data and best practices so technicians can execute tasks quickly and correctly. - AI Skills Management & RCA Insights
Empower technicians with AI-driven RCA, toolbox talks, and supervisor feedback to enhance problem-solving, retain knowledge, and refine troubleshooting—building a skilled workforce that minimizes failures and downtime.
By automating the entire preventive maintenance cycle, AI ensures less downtime, fewer manual errors, and a more efficient maintenance team.
Conclusion: The Future of Preventive Maintenance is AI-Driven
Let’s face it—the old way of doing preventive maintenance just isn’t working anymore. The cost of downtime is too high, and the inefficiencies are too great.
AI-driven preventive maintenance is the future. It’s smarter, more precise, and designed to keep your assets running at peak performance—without the guesswork.
Want to see AI in action?
Request a Demo to discover how Innovapptive’s AI-driven iMaintenance suite can optimize operations, reduce downtime, and drive significant cost savings.
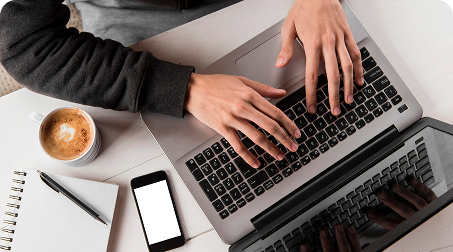
See It In Action
Schedule a personalized demo to see how our solutions can help your business thrive.
- 20-08-2025
Building the future of Industrial Operations with Innovapptive and AWS
Most manufacturers have already gone digital. Yet business outcomes haven’t moved in step. Many...
- 22-04-2025
The $3.6B Unlock: Solving the Chemical Industry’s Labor Crisis and EBITDA Pressure in One Move
“Constraints don’t slow innovation—they force it.”
- 21-04-2025
Chemical Industry's Margin Erosion: A Wake-Up Call for Operational Efficiency Amid China's Oversupply
The global chemical industry is facing mounting challenges, with revenue declines and shrinking...