How Life Sciences Can Keep Production Going in the COVID-19 Pandemic and Help Employees Stay Safe from Infection
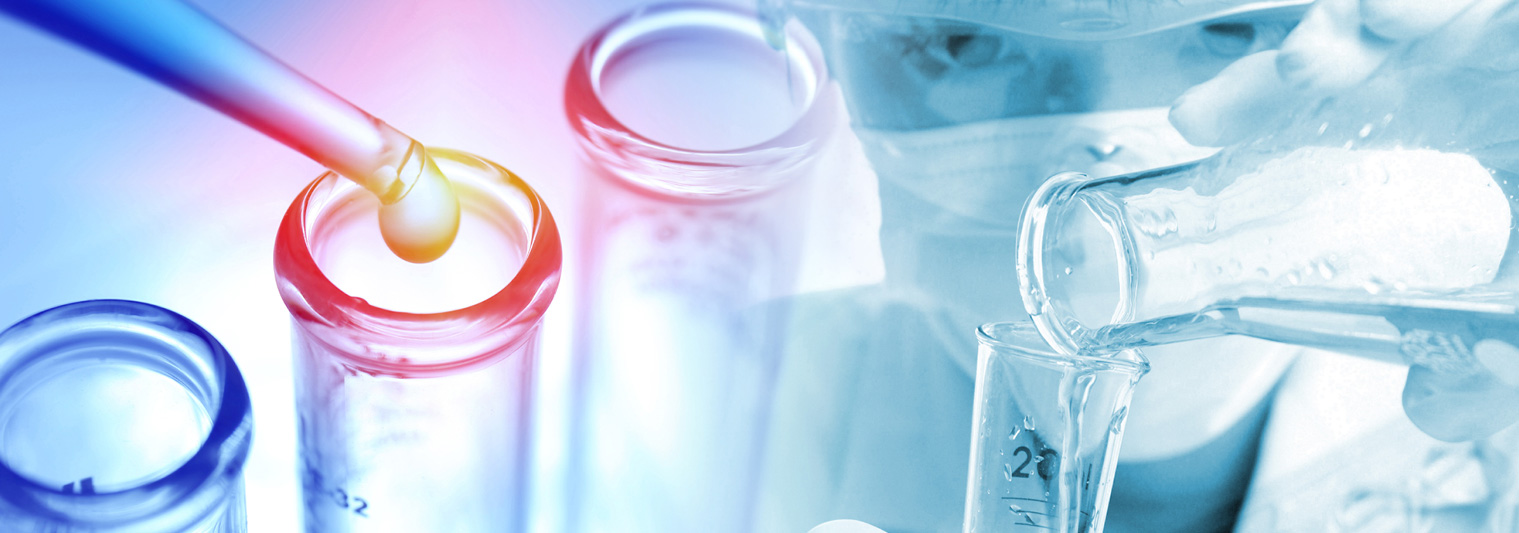
Life Sciences has gotten a lot of bad press in recent years. However, if there ever was a time when the world needs life sciences companies and the medicinal, personal hygiene, healthcare and nutritional products they make, it certainly is now. Thanks to the coronavirus and the COVID-19 pandemic, demand for personal hygiene, healthcare, nutritional products and medicines is skyrocketing. But, with the fear of infection high, essential manufacturers of all kinds are having trouble keeping production lines going while maintaining employee safety.
Reducing costly equipment downtime is a must for any manufacturer. This is especially crucial now for pharmaceutical plants. In normal times, having a production line unexpectedly go down due to equipment failure results in lost revenues. That’s not good. Now, however, if a life science company line shuts down due to a single COVID-19 case, it could mean more unanticipated revenue lost, illnesses and innocent lives lost in a world that doesn’t need either. Lost pharmaceutical production means hospitals, clinics, doctors and pharmacies may not be able to treat patients, weakening their immune systems and increasing their risk of contracting the coronavirus.
At the same time, Life Sciences companies must also ensure their workers remain protected and healthy while on the job. It’s not easy to make Life Sciences products at home on a large scale. The plant must remain in operation. The U.S. Department of Homeland Security lists Life Science plants as one of 16 critical industries that must remain open during an emergency. If the workers become ill, there will be no one around to run the production lines.
McKinsey & Co. suggests developing workforce protection policies and actions to “help manage productivity, using such means as staggered work times; respecting social distancing norms; and instituting health checks.”
These are definitely good workforce safety ideas worth implementing. But, there are other steps Life Sciences plants can take to ensure continued production and worker safety.
Nearly 30 years into the Information Age, many Life Sciences facilities maintenance departments still use paper as their primary communication and equipment data collection method. From a productivity standpoint, paper-based processes breed human error and inaccuracy, which leads to:- Less wrench time thanks to inefficient, disconnected and paper-based workflows
- Greater administrative costs as employees need to input data into the back-office system of record (such as SAP)
- Additional reworks as issues weren’t fixed properly the first time due to incomplete or wrong information
- More work order backlogs thanks to more reworks clogging the system
- Reactive maintenance practices which employ ineffective “run-to-failure” tactics rather than a preventive or proactive system
- Increased chance of costly equipment failure and downtime disrupting production
Now add in the effects of the global COVID-19 pandemic. Paper-based maintenance processes have an additional negative drawback: They put workers at greater risk of infection. Recent research in the American Journal of Nursing suggests that test organisms that were transferred onto paper survived on it for a considerable time. If someone were to later touch the contaminated paper containing the virus, it could be transferred to that person’s hands, raising the risks of spreading the coronavirus and contributing to the COVID-19 pandemic spread. In addition, a paper-based workflow does exactly the opposite of the “Social Distancing” guidelines being issued by public health regulators, such as the Center for Disease Controls (CDC), OSHA and WHO. A paper-based workflow increases the spread of COVID-19 due to the number of human interactions and touch-points associated with such a workflow.
In the coronavirus era, Life Sciences facilities must find a way to make technicians safe, more productive and get rid of waste in their maintenance process. Otherwise, they run an increased risk of growing maintenance work-order backlogs and more costly asset downtime. They must also safeguard workers’ health to ensure they have enough staff to perform needed maintenance activities in a timely manner. Eliminating paper, then, is an obvious choice to increase efficiency, reduce costs and protect workers. Now, how to do that?
mWorkOrder – the answer to Life Sciences maintenance and safety challenges
Innovapptive is a mobile-first, connected workforce platform provider. We’ve developed mWorkOrder, a configurable, agile, adaptable and intuitive solution that transforms reactive, risky, paper-based maintenance programs into proactive, safe and digital ones. The need for such a solution is now and imperative. Narendra Modi, Prime Minister of India, recently highlighted his vision of how to convert the COVID-19 crisis into an opportunity. The prime minister urges the world to become a “Digital-First” society that can envision and immediately implement the following:
- A “Digital-First” approach to develop new business models
- Operations must be highly adaptable and flexible to respond to change.
- Workforces must and will become highly productive and efficient in a “Digital World”
- Embrace “Digital-Solution Operations” that safeguard the well-being of your workforce
mWorkOrder (watch video here) replaces paper. It offers a scalable, agile and responsive platform to reconfigure stricter government and public health regulations and guidelines. It helps shape new environments, health and safety policies, and standard operating procedures (SOPs) as new job instructions. It helps Life Sciences companies combat the COVID-19 crisis, become a “Digital-First” enterprise like Prime Minister Modi highlighted, makes field workers highly productive and enables Life Sciences companies embrace “social distancing” as the “new normal.” Workers equipped with mobile devices such as smartphones, scanners, tablets, wearables, drones, etc., perform “real-time” and “socially distant” digital:
- Risk assessments
- Operator rounds
- Field inspections
- Measurement and readings data collection
- Work orders
- Asset tracking
- Reporting and automatic uploading to the back-office system of record
Supervisors and managers have real-time access to this information as it’s being collected in the field. They can then:
- Analyze safety of workforce and protect their well being and health
- Develop a repository of performance and business data
- Identify and analyze trends
- Ensure safety and regulatory compliance
- Spot issues before they become problems and take appropriate action
- Prioritize tasks
- Assign work orders
- Track progress
- Minimize downtime
As the maintenance staff is using mobile devices, they have no or limited exposure to risky paper forms, greatly mitigating the potential spread of the coronavirus. They also don’t have to work in close proximity, enabling them to practice the social distancing protocols that have been shown to reduce the chance of contracting COVID-19. Your employees can work in safety, assured their risk of getting ill has been curtailed, while you can continue operations and service customers, confident your staff can find and fix any problem before it takes your facility offline, costing you revenue.
mWorkOrder clients have seen numerous quantifiable benefits, including:
- 25% to 50% reduction in downtime and production delays
- 70% to 80% decrease in preventable failures
- 40% to 60% drop in maintenance backlogs
Discover more
The world of work is a much different place than it was only a few weeks ago. It may never return to what it once was. Life Sciences companies’ productivity is as important as ever, but now so is worker health and safety. Innovapptive’s mWorkOrder is a mobile-first, digital solution that can help your company and its employees make it through the COVID-19 pandemic.
You can see an online demonstration of mWorkOrder in action by clicking this link. Once you’ve seen the benefits and versatility they offer, call us at 888-464-6668. Our experts are standing by to answer your questions, listen to your needs and to configure a solution to overcome your challenges.
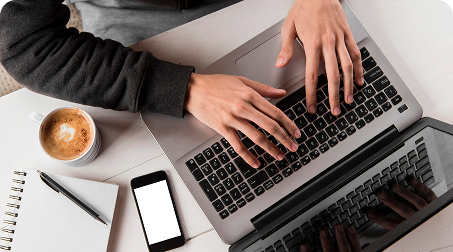
See It In Action
Schedule a personalized demo to see how our solutions can help your business thrive.
- 22-04-2025
The $3.6B Unlock: Solving the Chemical Industry’s Labor Crisis and EBITDA Pressure in One Move
“Constraints don’t slow innovation—they force it.”
- 21-04-2025
Chemical Industry's Margin Erosion: A Wake-Up Call for Operational Efficiency Amid China's Oversupply
The global chemical industry is facing mounting challenges, with revenue declines and shrinking...
- 21-04-2025
Why Wrench Time Isn’t Improving: The Hidden Costs of Traditional Maintenance Scheduling
For years, industrial leaders have relied on a common but flawed assumption: "Better planning and...