How Much Is an Inefficient Plant Maintenance Process Costing Your Company?
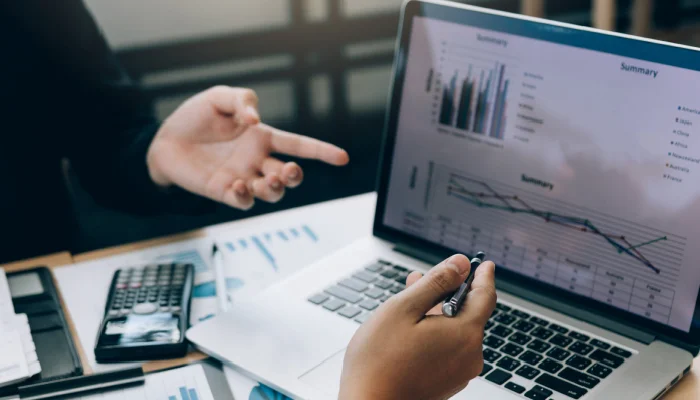
Ever rolled up a $100 bill and lit it on fire? No, of course not; money has value and it’s pretty foolish (and expensive) to simply waste it like. But wasting money is something you, as a plant maintenance manager or director, do each day you continue to employ an inefficient enterprise asset management program.
Unfortunately, too many plants (about half) still use reactive, run-to-fail maintenance, waiting for a piece of equipment to break down before initiating repairs. This is despite evidence showing that predictive and preventative plant maintenance programs are much more effective at cutting costly unplanned downtime and production stoppages.
Overall, unplanned downtime costs industrial manufacturers as much as $50 billion a year. It’s no surprise that 48% of manufacturers say they have considerable room for improvement.
Quantifying Plant Maintenance Inefficiency Is the First Step to Eliminating It
No one wants to waste money needlessly. The mark of a good manager, no matter the industry, is getting a strong, positive rate of return on investment (ROI) for every dollar spent. First, the hole in the money dike has to be identified before it can be plugged.
Four primary areas are rife with potential inefficiency and loss in a typical plant maintenance process. Each offers plenty of opportunities to eliminate wasteful costs and spending that can sink a company’s annual budget or process flaws that contribute to downtime. Getting these four areas in line is a great first step to controlling costs and improving the overall effectiveness of a maintenance program. These areas are:
- Technician productivity: Maintenance technician productivity is often poor, frequently as low as 20% to 30%. Techs find themselves awaiting instructions, looking for parts and materials, or traveling to and from locations instead of turning wrenches. Increasing wrench time can cut backlogs, reduce overtime and lessen the need for outside contractors.
- Overtime and contractor expenses: Labor is one of the biggest line items in any plant maintenance budget. Nearly half of all plants outsource up to 20% of their overall maintenance, and 10% use a contractor for half of their maintenance work. Improved in-house maintenance productivity can reduce this need to supplement in-house staff.
- Downtime: The average industrial plant suffers 800 hours of downtime per year – 15 hours a week. Each minute of downtime costs thousands of dollars in lost production, negatively impacting profit margins and putting customer relationships at risk.
- Downtime labor expenses: Unplanned downtime has far more costs than just lost production. There are also hidden labor costs that quickly add up each hour a piece of equipment is offline for repairs. Operators still have to be paid whether the machine is running or not. Improving maintenance processes enable you to reduce unplanned downtime and cut these additional hidden costs.
Do you have a way to determine what each of these four problem areas cost you yearly? If not, then there’s a good chance you’re not having as much success as you’d like transforming your plant maintenance process to one that consistently meets and exceeds your company’s goals in terms of performance and return on investment. Fortunately, help is available to rectify this situation.
Let Innovapptive Calculate Your Plant Maintenance ROI
Greater plant maintenance efficiency can translate into serious cost savings. Process improvement boosts in-house productivity and wrench time, cuts wasted, non-productive activities and reduces the need for expensive outside contractors.
For example, a highly efficient operation with 74% wrench time spends $100 million a year, versus $400 million a year on inefficient maintenance workforce management.
Innovapptive, a connected worker solution pioneer, specializes in SAP- and IBM Maximo-compatible mobile plant maintenance systems that improve technician productivity, transform reactive processes and cut downtime costs. Our industry experts can work with you to ascertain the effectiveness of your current plant maintenance and calculate your present ROI. They can also show how replacing a cumbersome paper-based process with a mobile plant maintenance solution can dramatically reduce costs and improve efficiencies.
Schedule a free demo of a world-class mobile plant maintenance app today, then call us at 888-464-6668 to partner with our industry experts to determine your ROI and map out a plan to raise it to new levels.
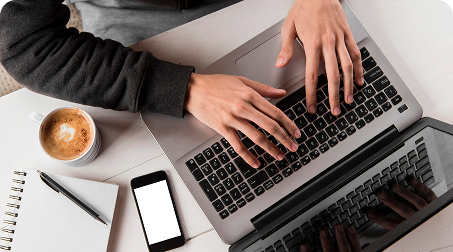
See It In Action
Schedule a personalized demo to see how our solutions can help your business thrive.
- 20-08-2025
Building the future of Industrial Operations with Innovapptive and AWS
Most manufacturers have already gone digital. Yet business outcomes haven’t moved in step. Many...
- 22-04-2025
The $3.6B Unlock: Solving the Chemical Industry’s Labor Crisis and EBITDA Pressure in One Move
“Constraints don’t slow innovation—they force it.”
- 21-04-2025
Chemical Industry's Margin Erosion: A Wake-Up Call for Operational Efficiency Amid China's Oversupply
The global chemical industry is facing mounting challenges, with revenue declines and shrinking...