Maximize asset life, improve wrench time & asset reliability with a comprehensive mobile EAM solution
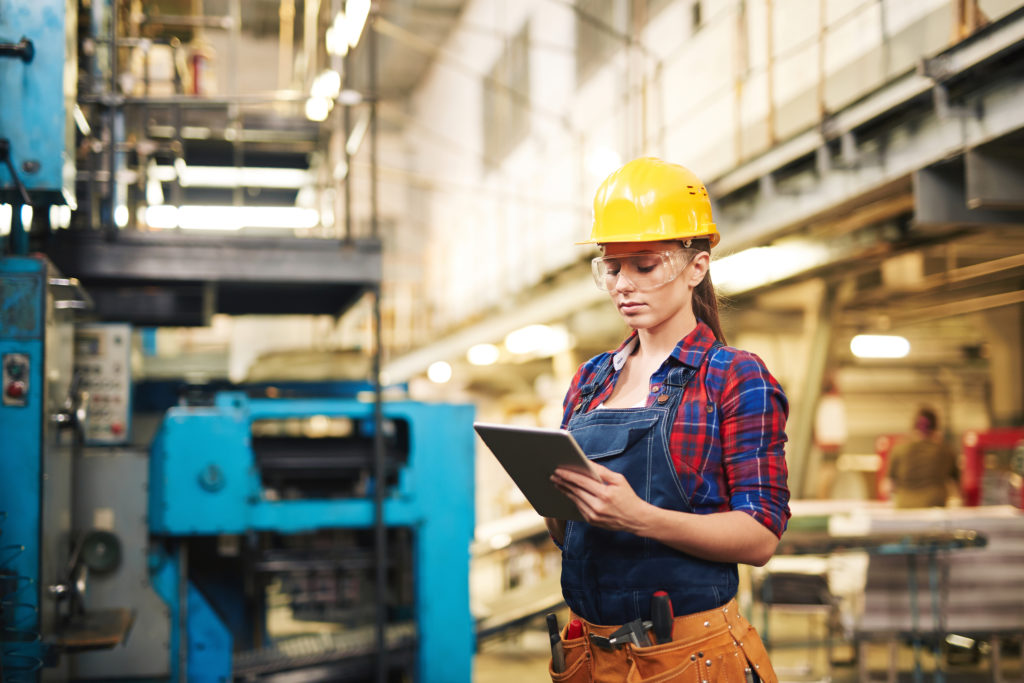
In today’s challenging business climate, enterprises are under pressure to increase efficiency and essential points. Existing maintenance operation tools do not provide any optimization methods to improve maintenance costs and life-cycle costs. Without a powerful mobile EAM tool, managers are trapped in a trial-and-error paradigm that leads to losses, useless expenditures, and missed ROI objectives.
Asset-intensive facilities everywhere face the same challenge, translating the organization’s objectives into asset-related decisions, plans, and activities. In fact, an effective asset management program is essential for any facility to achieve maximum asset value. An effective program manages risk and opportunity to achieve the desired balance of cost, risk, and performance. Changing one’s approach to asset management keeps cost low and uptime high.
Asset Management Strategy(Mobile EAM)
Asset Management is complex. Without a solid strategy, organizations frequently find themselves in reactive, emergency mode, spending too much time and money to keep their facility operating efficiently. Focus on risk evaluation and reduction which in turn helps maximize the return on your facility assets and investments. Proactively identifying the right maintenance at the right time improves asset performance and assures regulatory compliance. Strategic asset management solutions drive continuous improvement and produce measurable results, improving your bottom-line.
What you need:
- Provide critical knowledge enabling you to optimize reliability and operational performance.
- A single-minded focus on maximizing asset value by improving uptime and reducing emergencies, tailored to your specific needs and requirements.
- Employ industry best practices and advanced tools, providing you with data-driven analytics that supports your specific conditions. This will enable you to establish and sustain effective maintenance and reliability processes saving you money, time, and stress.
- Redesign or improve your existing practices, assuring you get the right maintenance at the right time, performed by the right team.
Establish fully qualified, optimized asset installations through early equipment management with a focus on front end planning and by designing for reliability. This results in improved uptime which reduces the need for routine outages and reduces operating costs throughout the life of your assets. The end goal is reduced life cycled costs. Identifying opportunities in your existing asset management strategy can help minimize risk, lower running costs, and optimize operational performance.
Meet Your Needs and Deliver ROI
Reactive maintenance and most preventive maintenance programs are expensive. In addition, they eventually result in issues with process reliability and manufacturing performance. An effective maintenance program requires a strong asset management strategy at its foundation. Best practice and compliance based asset management programs are achieved by establishing, implementing, maintaining, and continually improving the organization’s asset management strategy. Maintenance and reliability industry expertise, regulatory compliance experience to improve or establish an asset management program tailored to your specific needs. Advanced asset strategies deliver sustained, optimized asset performance and increase ROI by helping you maximize the value of your assets
Benchmark your maintenance program against the best practices in your industry as well as other industries to help you make strategic, data-driven decisions and achieve your goals. These goals serve as your guideposts on a journey to continuous improvement, equipment reliability, and optimized production. This optimization process results in increased quality and equipment reliability, and a reduction in equipment downtime.
Digital future state, do more with less
Organizations where at least half the maintenance workforce is mobile
- Integrate mobile capabilities into operational tasks to drive productivity and optimize maintenance costs by cutting wait times, reducing administrative burden, and minimizing time spent on the job. Gain >25% lower fixed asset service and maintenance cost and 15-20% higher wrench time.
- Deliver up to date information and instructions at the point of execution to minimize the variance between planned and actual tasks and mitigate the risk of unplanned downtime, enabling the experience, on average, of 24% lower unplanned downtime and 28% lower order backlog.
- Enable a seamless flow of data from the point of execution to master systems to improve process efficiency and reduce lead times, gaining ~50% higher service and maintenance parts inventory turns.
End to end work management with Innovapptive’s mWorkOrder
Double your wrench time, compared to traditional products. Over 15-20% improvement in wrench time through an agile & scalable mobile framework to improve this metric.
- Enable data access and data entry anywhere, avoiding errors and speeding up the end-to-end business process.
- Increase first-call closure rate.
- Provide accurate visibility of field activities to the back office.
- Increase asset utilization and minimize downtime.
- Minimize manufacturing or supply chain interruptions due to asset malfunction or breakdowns.
- Increase technician efficiency while in the field.
Innovapptive’s mWorkOrder (mobile work order management solution), transforms your entire enterprise asset management
- With real-time access to data, online and offline with speed.
- Ability to plan, schedule and assign emergency jobs on the plant floor.
- The user interface and user experience personas, simplicity and agility tailored to a job role.
- Captures images and voice to text, allows describing problems through visuals and voice to text.
- On-demand and role-based barcode scanning enablement allow craftspersons, supervisors, planners to automate searching for parts, equipment, and history of equipment to improve wrench time.
- Powerful Amazon and Google like fuzzy search, ability to search by equipment hierarchy and BOM maximized user efficiency to help improve repair timelines.
- Document viewing such as work order instructions, technical documents, safety instructions, equipment manual, and troubleshooting steps cuts down printing of paper and improves repair timelines
- RACE™ provides a highly configurable framework to continuously add “Wrench Time Improvement” relevant features as the solution scales within your enterprise. RACE™ allows for rapid deployment within weeks, compared to traditional approaches of typical 6-12 month timelines. Significant reduction in IT costs delivered.
If you would like a demo of Innovapptive’s mWorkOrder (Mobile Work Order) with RACE™ solution, please click on the link. You can also speak with one of Innovapptive's Solution Experts directly by emailing us at sales@innovapptive.com or at (713) 275-1804.
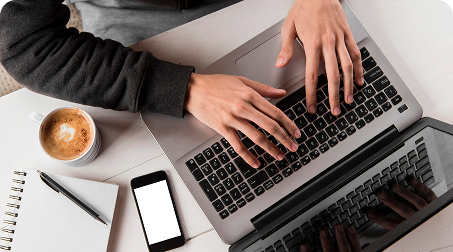
See It In Action
Schedule a personalized demo to see how our solutions can help your business thrive.
- 22-04-2025
The $3.6B Unlock: Solving the Chemical Industry’s Labor Crisis and EBITDA Pressure in One Move
“Constraints don’t slow innovation—they force it.”
- 21-04-2025
Chemical Industry's Margin Erosion: A Wake-Up Call for Operational Efficiency Amid China's Oversupply
The global chemical industry is facing mounting challenges, with revenue declines and shrinking...
- 21-04-2025
Why Wrench Time Isn’t Improving: The Hidden Costs of Traditional Maintenance Scheduling
For years, industrial leaders have relied on a common but flawed assumption: "Better planning and...