Mobile Warehouse Management Boosts Utility’s Productivity and Accuracy
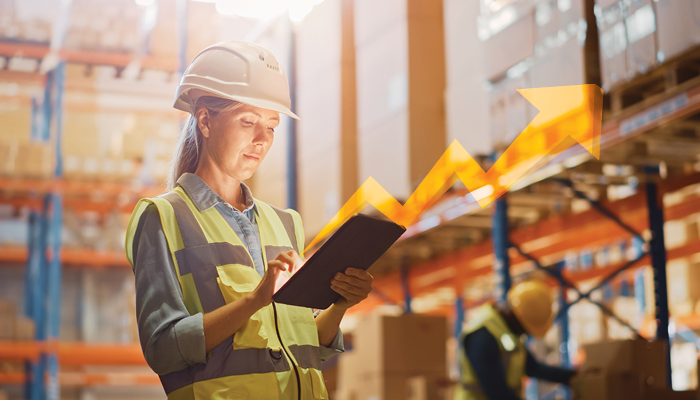
Loudoun Water, a fast-growing water utility in northern Virginia, relied on a paper-based warehouse management system that created inefficiencies and prevented the utility from achieving a high level of inventory accuracy.
The company's needed a better way to receive the increasing flood of incoming parts, accurately track their location in the warehouse and issue requested items for maintenance work orders in a timely manner.
Keeping Up With Rapid Growth
Loudoun Water’s service area encompasses over 80,000 households just west of Washington, D.C. The region experienced rapid population growth as people flock to a strong economy, good jobs and proximity to the nation's capital. This led to a surge of new customers for the utility.
This growth caused Loudoun Water some operational problems. More customers means more maintenance work on the company’s facilities to keep them up and running. Loudon Water’s warehouse had to ramp up to keep pace.
The organization turned to SAP in 2014 when it had 760 different types of parts in its warehouse. Now, the warehouse has to handle 4,500 different parts and materials. Even with SAP, the warehouse and its staff were swamped and its traditional paper-based inventory and cycle count process was no longer able to keep pace.
Mobile Warehouse Management Offers Solution to Utility’s Problems
Loudoun Water needed a mobile warehouse management solution to boost its warehouse operations, productivity and inventory accuracy to cope with the rising tide of growth.
The right solution needed to:
- Tie seamlessly into SAP Materials Management
- Function with iOS mobile devices
- Offer an easy to use interface
- Have minimal configuration requirements
- Work “out of the box”
- Be from a proven vendor
Enter Innovapptive and mInventory
Innovapptive’s mInventory mobile warehouse management solution ticked all the boxes. Impressed with the app’s features and functionalities, the organization integrated the application into its operations.
The project yielded results across the warehouse.
“Truck inspections used to take us nearly a day with paper,” said Manager of Warehouse Operations Ken Harvey. “Now it’s just an hour. Cycle count times have been
cut in half, from four hours to only two.”
Learn more about the benefits Loudoun Water experienced in our latest case study, Utility Streamlines Inventory Processes with Warehouse Management Automation. Afterward, be sure to view our free on-demand webinar about Loudoun Water here.
Ready for a free mInventory demo to see how your organization can experience the same transformation? Our experts are standing by to answer your questions and discuss how mInventory can help your utility increase inventory accuracy, raise productivity, cut inventory carrying costs and avoid paying unneeded taxes. Call us at 1-844-464-6668 or email info@innovapptive.com.
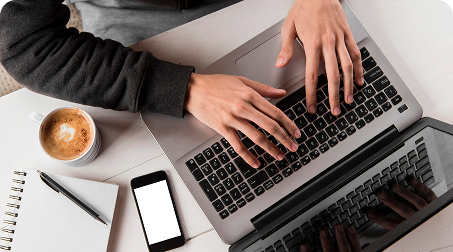
See It In Action
Schedule a personalized demo to see how our solutions can help your business thrive.
- 20-08-2025
Building the future of Industrial Operations with Innovapptive and AWS
Most manufacturers have already gone digital. Yet business outcomes haven’t moved in step. Many...
- 22-04-2025
The $3.6B Unlock: Solving the Chemical Industry’s Labor Crisis and EBITDA Pressure in One Move
“Constraints don’t slow innovation—they force it.”
- 21-04-2025
Chemical Industry's Margin Erosion: A Wake-Up Call for Operational Efficiency Amid China's Oversupply
The global chemical industry is facing mounting challenges, with revenue declines and shrinking...