Mobility helping Power Industry to Increase Asset Performance, Workers’ Productivity and Safety
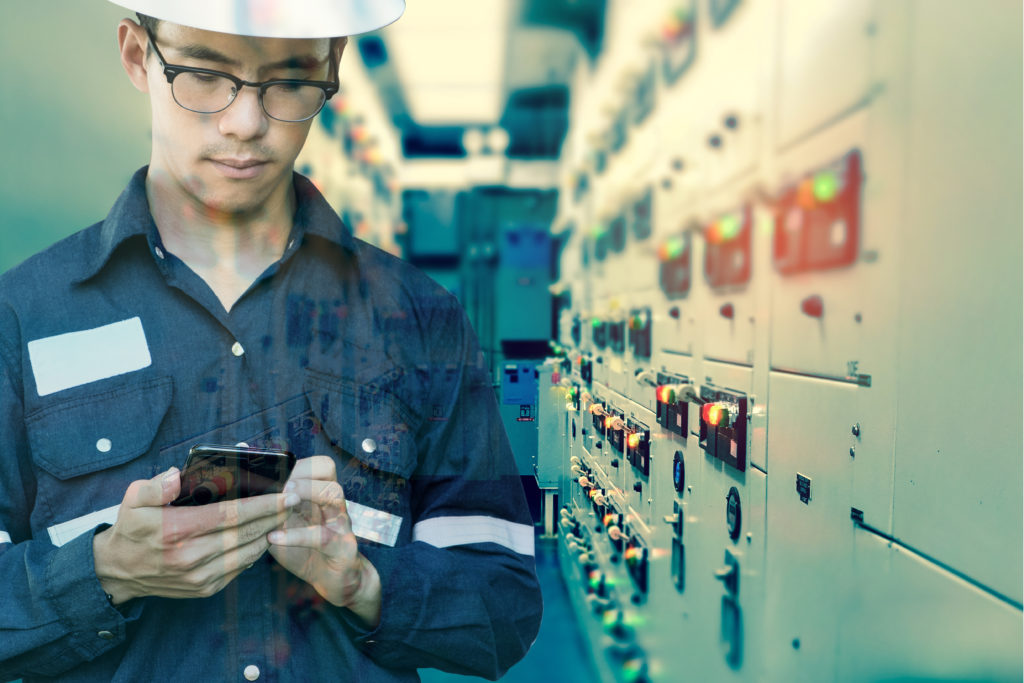
In recent years, a variety of external forces have significantly impacted the way power generation companies run their assets and meet business objectives. The industry is facing dramatic market dynamics resulting from changes in fuel prices, growing renewables, and changes in the regulatory environment. Managing power generation plants efficiently is getting tough, it involves challenges in it. Despite having a good ERP or software system in place, power operators still face significant barriers that make it difficult for them to take the right decision at the right time. A lack of asset level visibility — not knowing in advance when problems are about to occur, unplanned downtime, costly and often unnecessary routine preventive maintenance that introduces risk and decreases availability. And most importantly, critical information needed by maintenance technicians, operators, and managers get delayed that may impact reaching their deadlines.
Technology has changed almost everything, and a number of industries have been transformed by the wave of digital innovations. One area where we’re seeing a tremendous impact is Power Industry. As other industries are flourishing by using technological advancements, Power Industry also started selectively using technology to drive better economic outcomes from their power plants and existing software system.
As we discussed in our previous blog post, that technological advancement such as mobility, especially in oil and gas sector is not just the norm, but has become a necessity for success. In this blog, we will explore how Mobility helps Power Generation companies to increase asset performance, improve workers’ productivity and safety while reducing accidents/failures. This blog will help you understand that how smoothly it accompanies them to better meet efficiency and sustainability goals without sacrificing power reliability, safety, or productivity. To leverage their existing system to the fullest, the power industry needs a solution that can help them:
• Reduce maintenance costs — Simplified maintenance processes on mobile devices increase plant reliability while reducing the amount of maintenance activity performed overall
• Improve reliability — Real-time updates on mobile helps predict potential equipment failures with enough lead time to effectively plan maintenance. It enables power plant operators to draw insights more quickly and drive action.
• Maintain technical expertise — A unified and accurate view of assets’ information provides clear guidance to next occurrence as well as asset history, accessible through an intuitive user interface via mobile device.
• Improve availability — Accurate diagnosis of equipment issues that enables faster repairs and shortens outage duration
• Improved equipment/asset health — delivers complete visibility of machine status and issues anytime, anywhere that helps operators, supervisor, and managers in better decision-making.
• Improve ability to respond to market conditions — such as prices, demand and costs fluctuate performance
In today’s competitive environment, power operators can use the right mobile solution to provide on-going operational productivity — protecting against downside risk while constantly pursuing upside opportunities and increasing economic value while reducing total cost. Innovapptive provides an outstanding suite of SAP mobile solutions that help organizations achieve the most out of their SAP investments. There are many key benefits that speak directly to what Innovapptive’s mobile solutions can do for your organization. Innovapptive’s mWorkOrder gives maintenance workers, technicians anytime, anywhere access to the information they need to do their jobs, and their safety and productivity in the plant and in the field, will increase. With both online and offline access, it helps ensuring delivery of mission-critical support of assets without any interruptions or delays, leading to better performance and reliability across plants, fleets, networks, and the enterprise infrastructure. Fully configurable with RACE™, it gives you unparalleled flexibility to zero in on the specialized, industry requirements that can turn your company’s asset management into a competitive advantage.
Value Driver:
• Receive and update work orders.
• Get directions with GIS and GPS.
• Follow guided workflows, steps, and instructions
• View interactive part schematics (with SAP Visual Enterprise Viewer.
• View installed-base listings and access equipment, details, dependencies, and maintenance history.
If you would like a demo of Innovapptive’s mWorkOrder(SAP Mobile Plant Maintenance), please click on the link. Alternatively, if you would like to discuss with an Innovapptive solution expert, you can reach out to us by emailing us at sales@innovapptive.com or you can reach a sales representative at (713) 275-1804.
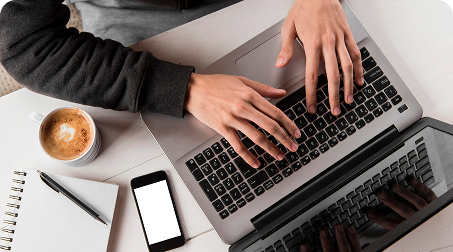
See It In Action
Schedule a personalized demo to see how our solutions can help your business thrive.
- 22-04-2025
The $3.6B Unlock: Solving the Chemical Industry’s Labor Crisis and EBITDA Pressure in One Move
“Constraints don’t slow innovation—they force it.”
- 21-04-2025
Chemical Industry's Margin Erosion: A Wake-Up Call for Operational Efficiency Amid China's Oversupply
The global chemical industry is facing mounting challenges, with revenue declines and shrinking...
- 21-04-2025
Why Wrench Time Isn’t Improving: The Hidden Costs of Traditional Maintenance Scheduling
For years, industrial leaders have relied on a common but flawed assumption: "Better planning and...