Optimize Your Oil and Gas Facility’s Maintenance Using a Mobile MRO Solution
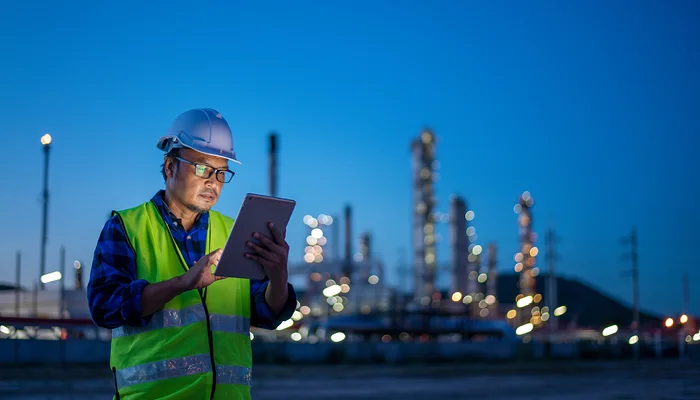
Oil and gas facilities spending more than 5 percent of their asset’s value on maintenance are suffering the consequences of an inefficient program. There’s a way to reduce maintenance costs and increase equipment reliability and uptime. How? A mobile MRO solution offers relief for upstream, midstream and downstream companies.
What Is a Mobile MRO Solution?
A mobile MRO application eliminates slow, inefficient paper-based data collection and replaces it with real-time data capture and distribution. Instead of clipboards and binders, oil and gas frontline workers use smartphones, tablets, wearables and drones to perform tasks in the field. This can be at a:
- Land rig
- Offshore platform
- FPSO
- Gas treatment plant
- Compressor or pump station
- Tank farm
- Refinery
- Loading rack
Mobile MRO solutions automatically upload operational data into the back-office system of record, such as SAP or IBM Maximo. They cut out labor-intensive and time-consuming manual data entry and other administrative chores, enabling maintenance technicians to spend more time conducting repairs.
Thanks to automatic uploads, oil and gas decision makers enjoy:
- Real-time visibility into operations
- Accurate and timely data
- No information silos
- Greater collaboration with field workers
- Ability to make knowledge-based decisions
Mobile MRO Solution Sample Use Case
Oil and gas facilities are full of pumps. It doesn’t matter if it’s a drilling rig, a floating production/offloading unit, a pipeline station or a refinery. Pumps frequently malfunction, requiring repairs, upgrades or replacements.
An operator equipped with a mobile MRO solution can conduct a regularly scheduled inspection round. During the round, the operator notices the pump is at risk of failure. The operator can conduct a quick risk assessment and send a digital notification to a shift supervisor or manager alerting them of the situation.
If the risk of failure is great enough, the supervisor can create and issue an emergency work order to begin the repair process and forestall potential asset downtime. The supervisor can assign resources, dispatch them to the repair site and electronically attach SOPs and work instructions to guide the maintenance technician.
Using a mobile MRO solution, maintenance can digitally collaborate with the warehouse during the work order to ensure needed parts are ready when needed. This capability reduces time wasted on trips to the warehouse to check on availability and readiness. It also speeds repairs by alerting the warehouse to upcoming needs. This gives pickers and shipping clerks lead time to assemble and kit the necessary parts. When the technician arrives, everything is already set for pick up, saving valuable time and effort.
For this particular repair, a less-experienced is assigned to the work order. The technician is a hard worker, but lacks the knowledge and skill set of a veteran frontline worker. This situation could cause problems in a traditional, paper-based maintenance system. With no way to ask questions during the repair, there’s a greater chance of mistakes that can result in reworks and backlogs for an already stretched-out staff.
But using a mobile MRO solution, frontline workers like our hypothetical newbie technician can connect with remote experts on-demand via two-way video conferencing to receive digital work instructions and coaching. The remote expert can actually “see” what the technician onsite is viewing and guide him in the proper procedure to complete the repair. The technician can attach photos and videos of the situation while the expert can respond with PDFs of repair manuals and user guides.
The expert or a supervisor can edit an existing checklist or create a new one in just minutes and send it to the technician in the field to make sure all the repair steps have been followed and that no other work needs to be done. This ensures the repair is completed correctly… the first time.
Mobile MRO Solutions Redefine Work Order Management
Oil and gas maintenance supervisors and managers can prioritize maintenance work orders based on the risk profile of equipment throughout the facility. For example, they’re able to:
- Rank issues based on problem severity, likelihood and duration, or the criteria of your choice
- Use risk information to prioritize work orders and push notifications
- Embed risk and safety information into the work order
- Alert the warehouse to parts needed for the repair
A mobile MRO solution transforms reactive and inefficient oil and gas maintenance programs. Maintenance technicians, supervisors and managers see their daily work lives improved through:
- The elimination of manual processes
- Access to real-time operational data
- Guided work instructions
- The ability to edit, create and issue digital forms
- The digitization of the work order process
- Greater collaboration with the warehouse
A mobile MRO solution optimizes oil and gas maintenance operations, reducing costs and increasing equipment uptime.
A Mobile MRO Solution to Optimize Your Oil and Gas Maintenance Program
Discover how a best-in-class mobile MRO solution transforms maintenance activities through a customized, live demo of Innovapptive’s mWorkOrder. For more information, call 1-844-464-6668 to speak with one of our oil and gas industry experts today. They’ll take the time to understand your unique situation and construct a plan incorporating mWorkOrder to optimize your maintenance process.
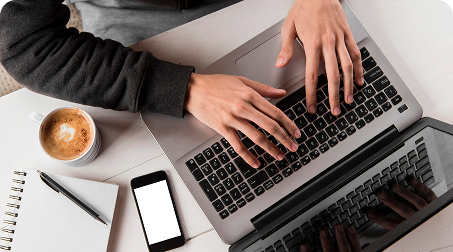
See It In Action
Schedule a personalized demo to see how our solutions can help your business thrive.
- 20-08-2025
Building the future of Industrial Operations with Innovapptive and AWS
Most manufacturers have already gone digital. Yet business outcomes haven’t moved in step. Many...
- 22-04-2025
The $3.6B Unlock: Solving the Chemical Industry’s Labor Crisis and EBITDA Pressure in One Move
“Constraints don’t slow innovation—they force it.”
- 21-04-2025
Chemical Industry's Margin Erosion: A Wake-Up Call for Operational Efficiency Amid China's Oversupply
The global chemical industry is facing mounting challenges, with revenue declines and shrinking...