Overcoming Equipment Maintenance Challenges in Mining Industry
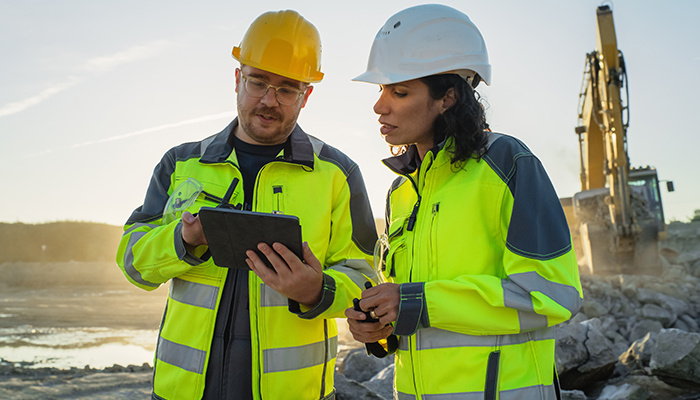
Key Takeaways
- The Cost of Mining Equipment Downtime: is about $180,000 per incident on average totaling up to $10 billion annually across the industry.
- Challenges in Mining Equipment Maintenance: Hindered by frequent breakdowns in harsh environments, limited spare parts availability, paper-trails, and skill shortage.
- Best Practices for Overcoming Challenges: Adopting preventive maintenance strategies and technology for real-time monitoring to improve equipment reliability.
Introduction
Mining companies depend on heavy machinery to keep operations running smoothly. But what happens when machinery breaks down?
As per industry experts, the cost of downtime can be staggering, averaging about $180,000 per incident. If these issues persist regularly, annual downtime costs can skyrocket to $10 billion.
To combat this, mining companies allocate 35-50% of their annual budgets to equipment maintenance. This significant investment highlights the critical role of maintenance in preventing costly disruptions, ensuring smooth operations, and reducing unplanned downtime.
However, maintaining a mining operation is far from straightforward. This industry relies on a complex ecosystem of machinery—from towering haul trucks and excavators to intricate drilling rigs and processing plants—all operating 24/7 in some of the harshest environments imaginable. Every minute of downtime means lost productivity, economic impact, and delayed projects.
Neglecting equipment maintenance can have devastating consequences. Let’s delve into the high costs of poor maintenance, exploring the challenges it presents and its impact on production, safety, and budgets.
Challenges of Mining Equipment Maintenance: A Minefield of Obstacles
Maintaining equipment in the mining industry is no walk in the park. Unlike a car in your garage, these machines face a unique set of challenges that can send even the most robust maintenance plan into disarray. Let's explore some of the major obstacles that mining companies face in keeping their equipment operational:
- Frequent Breakdowns: Mining equipment operates under immense stress, constantly exposed to dust, extreme temperatures, and vibrations. This harsh environment accelerates wear and tear, leading to frequent breakdowns. These breakdowns create a domino effect, disrupting operations, delaying deliveries, and impacting downstream processes.
- Unplanned Downtime: Even minor equipment failures can lead to significant unplanned downtime. This downtime not only impacts production but can also pose safety hazards as maintenance crews rush to fix issues under pressure.
- The High Price Tag of Equipment Failure: Equipment failure comes with a hefty price tag. Beyond the immediate cost of repairs or replacements, lost productivity due to downtime can significantly impact the bottom line. Additionally, damaged equipment can cause environmental damage, further adding to the overall cost burden.
- Limited Spare Parts: Mining operations often take place in remote locations, making it challenging to maintain a readily available stock of spare parts. Long lead times for specific components can further delay repairs and exacerbate downtime issues.
- The Paper Trail: Traditional paper-based maintenance records are prone to errors, loss, and difficulty in data analysis. This reliance on paper can lead to missed preventive maintenance schedules, incomplete information about equipment history, and challenges in identifying trends and potential problems.
- Inexperienced Workforce: The mining industry faces a growing shortage of skilled personnel, making it difficult to find experienced technicians who can effectively maintain complex equipment. This lack of expertise can compromise safety, efficiency, and compliance with industry regulations.
These challenges paint a clear picture of the minefield that mining companies navigate when it comes to equipment maintenance. However, there's hope. By understanding these obstacles and implementing effective solutions, mining companies can mitigate potential risks, optimize operations, and ensure the continued success of this vital industry.
Causes of Mining Equipment Maintenance Challenges
- Aging Equipment: Many mining operations rely on aging equipment, often exceeding its intended lifespan. While these machines may still function, they are more susceptible to breakdowns and require increased maintenance efforts.
- Harsh Environments: Mining environments are inherently harsh and unforgiving, subjecting equipment to extreme temperatures, dust, and constant vibrations. These factors accelerate wear and tear, significantly increasing maintenance needs.
- Lack of Skilled Workforce: The mining industry faces a shrinking pool of skilled workers, creating a gap in essential maintenance expertise. This lack of knowledge and experience can lead to improper maintenance practices and increase the risk of equipment failures.
- Insufficient Funding: Balancing cost and efficiency can be challenging for mining companies. Budgetary constraints can lead to deferred maintenance, ultimately leading to higher long-term costs due to increased repairs, replacements, and lost production.
- Inefficient Maintenance Procedures: Outdated and inefficient maintenance procedures can significantly contribute to equipment problems. Additionally, lack of planning and preventive maintenance strategies can lead to reactive maintenance, addressing issues only after they arise. This reactive approach is often more expensive and disrupts operations unnecessarily.
Discovering the Future of Mining With an AI-Powered Connected Worker Platform Read The Blog.
Best Practices for Overcoming Challenges
- Preventive Maintenance: Implementing a comprehensive preventive maintenance (PM) program is crucial to combat equipment issues. This proactive approach involves regular inspections, servicing, and lubrication to identify and address potential problems before they escalate into breakdowns.
- Investing in New Equipment: While maintaining legacy equipment can be tempting, investing in new modern equipment can offer significant benefits. Newer machines often boast improved reliability, efficiency, and longer lifespans, ultimately reducing maintenance needs and downtime.
- Training Maintenance Personnel: Investing in training and upskilling existing maintenance personnel is essential. This can include providing training on specific equipment, troubleshooting techniques, and the latest advancements in maintenance technology. Additionally, encouraging knowledge sharing among experienced and new personnel can foster a culture of continuous learning and improve overall maintenance practices.
- Regular Inspections: Conducting regular inspections allows for early detection of potential problems. This can be enhanced by adopting condition-based maintenance (CBM) techniques, where real-time data from sensors and equipment monitoring systems is used to identify and address issues based on actual operating conditions rather than relying solely on traditional calendar-based maintenance schedules.
How Innovapptive’s mWorkOrder Helps with Equipment Maintenance
Innovapptive’s mobile plant maintenance solution - mWorkOrder - offers the right mix of simplicity, functionality, and scalability to meet your unique business needs within your budget. This robust solution optimizes your maintenance process, digitally connecting far-flung workers in the field to management in the office, enabling more effective communications and collaboration, quicker and more accurate identification of issues, more knowledgeable decision-making, and faster responses to problems.
Here are some features that help with equipment maintenance:
- Maintenance Control Center: Supervisors can monitor maintenance tasks in real-time, tracking progress, addressing issues promptly, and ensuring operational efficiency.
- Digital work instructions: Maintenance crews need timely access to work instructions. Unlike manual or paper-based instructions, digital platforms offer easy access, helping operators complete maintenance tasks efficiently.
- Rich Media Integration: The app supports capturing photos, videos, and documents, adding a rich layer of detail to work orders and notifications. This feature significantly enhances the quality of data collected during inspections.
- Real-time SAP integration: Our maintenance solutions seamlessly integrate with SAP ERP systems, eliminating manual data transfer and creating a unified ecosystem for managing and optimizing maintenance operations.
- Asset Health Dashboard: Get a comprehensive snapshot of your equipment’s history, past work details, and current conditions while keeping tabs on expenses and issues—all in one place with smart suggestions.
- Computer Vision: Our app's camera acts like a superhero's keen eye, spotting even the tiniest wear and tear to eliminate manual errors. By catching issues early, we boost Mean Time Between Failures (MTBF), keeping your assets running smoothly and enhancing productivity and safety.
- GIS Integration: By integrating geospatial systems, mWorkOrder promotes efficient processes and better decision-making through an understanding of equipment location and spatial relationships.
Ready to Take the Next Step? Here’s How to Learn More
Innovapptive, as a connected worker platform pioneer, specializes in mobile maintenance management solutions that integrate seamlessly with SAP and IBM Maximo. These solutions improve data accuracy, transform reactive processes, increase technician productivity, and cut downtime. They’ll enable your mines to realize your ERP’s potential. Watch this two-minute video to understand mWorkOrder’s power and versatility to change your reactive maintenance process to a proactive preventative model. When you’ve finished, click here for a free demo. Have additional questions? Our experts are standing by now, ready to help. Give them a call at 844-464-6668.
FAQ
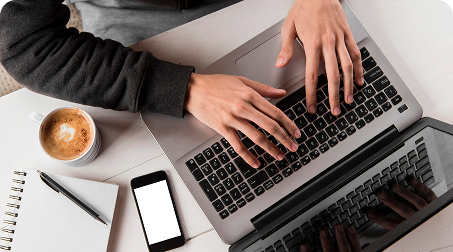
See It In Action
Schedule a personalized demo to see how our solutions can help your business thrive.
- 20-08-2025
Building the future of Industrial Operations with Innovapptive and AWS
Most manufacturers have already gone digital. Yet business outcomes haven’t moved in step. Many...
- 22-04-2025
The $3.6B Unlock: Solving the Chemical Industry’s Labor Crisis and EBITDA Pressure in One Move
“Constraints don’t slow innovation—they force it.”
- 21-04-2025
Chemical Industry's Margin Erosion: A Wake-Up Call for Operational Efficiency Amid China's Oversupply
The global chemical industry is facing mounting challenges, with revenue declines and shrinking...