Reducing Costly Unplanned Downtime in the Chemical Industry
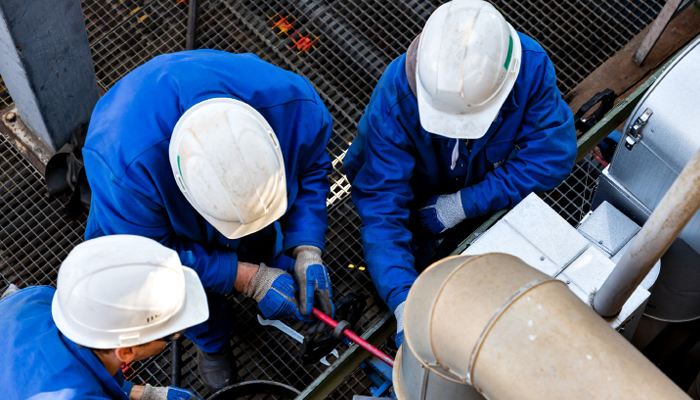
Key Insights
- Downtime Costs: Chemical equipment downtime costs range from $260,000 to $2 million per incident, totaling around $20 billion annually.
- Maintenance Challenges: Frequent equipment failures, harsh working conditions, limited availability of spare parts, reliance on paper records, and a shortage of skilled workers.
- Best Practices: Implementing preventive maintenance and real-time monitoring technology to enhance equipment reliability.
Introduction
Chemical companies depend significantly on machinery for smooth operations. When equipment breaks down, the costs can be exorbitant. According to the Aberdeen Group, downtime incidents cost between $260,000 to $2 million each. If these issues persist, annual costs can soar to $20 billion as reported by IIoT World. Consequently, chemical companies allocate 20-30% of their budgets to equipment maintenance, highlighting its critical role in preventing disruptions, maintaining smooth operations, and minimizing unplanned downtime.
Major Challenges in Chemical Plant Maintenance
Maintaining chemical equipment is challenging and can disrupt even the most robust maintenance plans. Some of the major obstacles include:
- Frequent Breakdowns: Equipment in the chemical industry is exposed to extreme stress, high temperatures, dust, and vibrations, leading to accelerated wear and tear and frequent breakdowns. These interruptions can delay operations and affect downstream processes.
- Unplanned Downtime: Even minor equipment failures can cause significant unplanned downtime, impacting production and posing safety risks as maintenance teams work under pressure to fix issues.
- High Cost of Equipment Failure: Beyond immediate repair or replacement costs, lost productivity due to downtime can heavily impact the bottom line. Additionally, equipment failures can cause environmental damage, further increasing costs.
- Limited Spare Parts: Remote chemical plant locations make it challenging to maintain an adequate stock of spare parts. Long lead times for specific components can delay repairs and exacerbate downtime issues.
- Paper-Based Records: Traditional paper-based maintenance records are prone to errors and loss, leading to missed preventive maintenance schedules, incomplete equipment history, and challenges in identifying trends.
- Skilled Workforce Shortage: The chemical industry faces a shortage of skilled technicians, compromising safety, efficiency, and regulatory compliance.
Primary Maintenance Issues for Chemical Plants
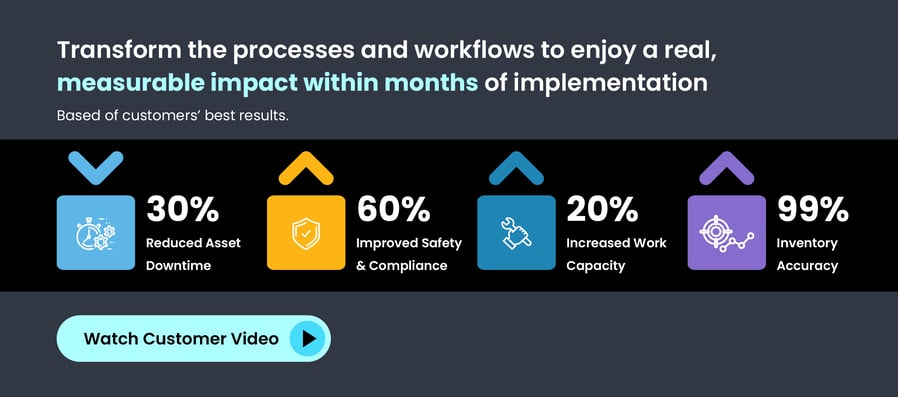
- Aging Equipment: Many operations rely on aging machinery that is more prone to breakdowns and requires increased maintenance efforts.
- Harsh Environments: Chemical environments subject equipment to extreme conditions, accelerating wear and tear.
- Skilled Workforce Shortage: The industry is experiencing a reduction in skilled workers, leading to improper maintenance practices and increased risk of equipment failure.
- Insufficient Funding: Budgetary constraints can result in deferred maintenance, leading to higher long-term costs due to increased repairs and lost production.
- Inefficient Maintenance Procedures: Outdated and inefficient procedures can significantly contribute to equipment problems, resulting in reactive maintenance and operational disruptions.
Discover how a chemical plant cut downtime and achieved record production. Read the case study.
Best Practices for Overcoming Challenges
- Preventive Maintenance: Implementing a comprehensive preventive maintenance program, including regular inspections, servicing, and lubrication, helps identify and address potential problems before they escalate.
- Investing in New Equipment: While maintaining legacy equipment can be tempting, investing in modern machinery offers significant benefits such as improved reliability, efficiency, and longer lifespans, thereby reducing maintenance needs and downtime.
- Training Maintenance Personnel: Investing in training and upskilling existing personnel is crucial. Providing training on specific equipment, troubleshooting techniques, and the latest advancements in maintenance technology fosters a culture of continuous learning.
- Regular Inspections: Conducting regular inspections allows for early detection of potential problems. Adopting condition-based maintenance techniques using real-time data from sensors helps identify and address issues based on actual operating conditions.
Innovapptive’s mWorkOrder Solution
Innovapptive’s mobile plant maintenance solution, mWorkOrder, provides the right balance of simplicity, functionality, and scalability to meet unique business needs within budget. This robust solution optimizes the maintenance process by digitally connecting field workers to office management, enabling effective communication, quicker issue identification, more informed decision-making, and faster responses.
mWorkOrder Features
- Maintenance Control Center: Real-time monitoring of maintenance tasks for supervisors, ensuring operational efficiency.
- Digital Work Instructions: Easy access to work instructions for maintenance crews, enhancing task efficiency.
- Rich Media Integration: Supports capturing photos, videos, and documents, adding detail to work orders and notifications, improving data quality.
- Real-time SAP Integration: Seamless integration with SAP ERP systems, eliminating manual data transfer, and creating a unified ecosystem for managing maintenance operations.
- Asset Health Dashboard: Comprehensive snapshot of equipment history, past work details, and current conditions with expense tracking and issue monitoring.
- Computer Vision: Advanced camera technology to detect wear and tear early, boosting Mean Time Between Failures (MTBF) and enhancing productivity and safety.
- GIS Integration: Promotes efficient processes and better decision-making through an understanding of equipment location and spatial relationships.
Take the Next Step Today
Innovapptive specializes in mobile maintenance management solutions that integrate seamlessly with SAP and IBM Maximo. These solutions improve data accuracy, transform reactive processes, increase technician productivity, and reduce downtime. Watch this two-minute video to understand mWorkOrder’s capabilities and click here for a free demo. For additional questions, our experts are ready to assist at 844-464-6668.
FAQ
Q1. What is mWorkOrder and how does it contribute to plant maintenance?
mWorkOrder is a mobile work order management solution seamlessly integrated with SAP ECC and S/4HANA. It facilitates real-time data capture, immediate work assignment, and improved accuracy, leading to increased asset uptime and plant safety.
Q2. What are the core features of mWorkOrder?
mWorkOrder provides anytime/anywhere mobile access to digitized work orders and asset information, real-time workflow management, online/offline modes, attachment capabilities for photos and documents, and seamless integration with SAP systems.
Q3. Can the mWorkOrder app reduce maintenance costs?
Yes, mWorkOrder can help reduce maintenance costs by providing more accurate and timely data, eliminating manual data entry, and identifying and fixing problematic equipment before breakdowns occur.
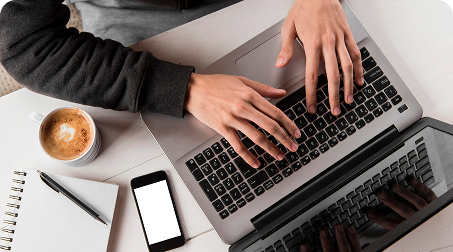
See It In Action
Schedule a personalized demo to see how our solutions can help your business thrive.
- 22-04-2025
The $3.6B Unlock: Solving the Chemical Industry’s Labor Crisis and EBITDA Pressure in One Move
“Constraints don’t slow innovation—they force it.”
- 21-04-2025
Chemical Industry's Margin Erosion: A Wake-Up Call for Operational Efficiency Amid China's Oversupply
The global chemical industry is facing mounting challenges, with revenue declines and shrinking...
- 21-04-2025
Why Wrench Time Isn’t Improving: The Hidden Costs of Traditional Maintenance Scheduling
For years, industrial leaders have relied on a common but flawed assumption: "Better planning and...