Reducing Technician Turnover and Managing Gen Zers Through Mobile Workforce Management
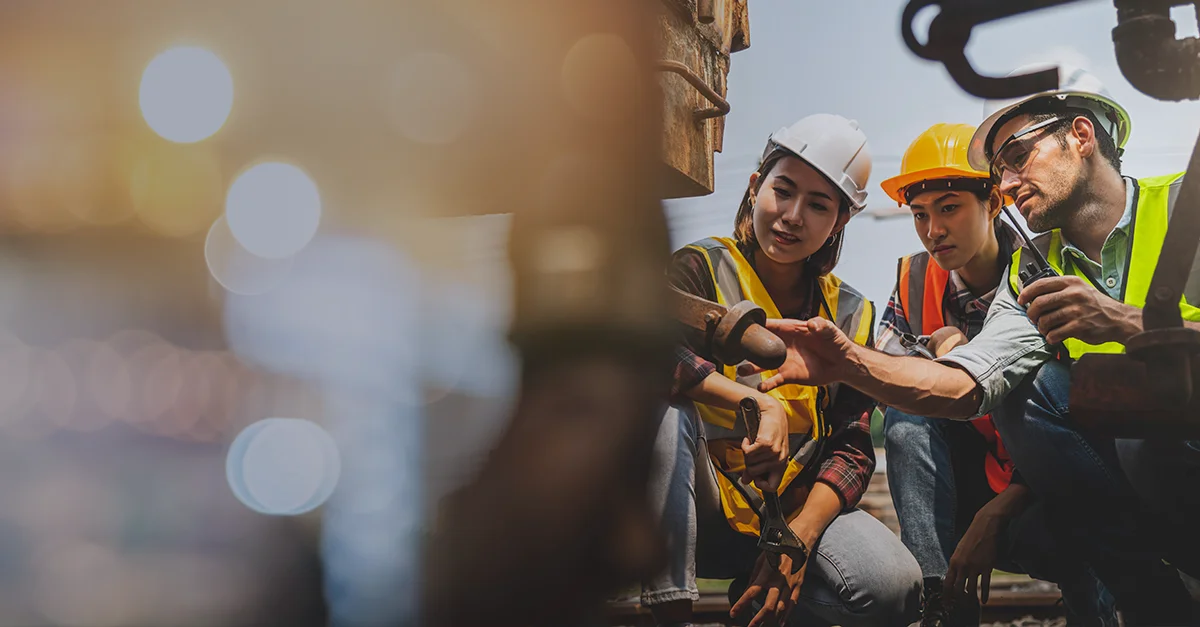
Gen Z workers are digital natives. They expect the companies they work for to use the latest technology. If they use outdated manual processes, these young workers are quick to leave. A mobile workforce management solution can cut maintenance technician turnover and help recruit Gen Z workers.
In our survey of plant managers, 52% answered “Yes” to the question: “Are you challenged with workforce attrition and change management?” In many asset-intensive industries, such as oil and gas, the older generation of field technicians is entering retirement age, leaving the less-experienced members of the workforce to pick up the slack.
Mobile Workforce Management platforms offer a solution to this growing problem.
Concerns about the “Great Crew Change”
One problem is that the incoming workforce is not replacing outgoing workers at an equal rate. According to some estimates, for every two workers dropping out of the oil and gas workforce, there’s only one coming in. This phenomenon is often called the Great Crew Change.
The ongoing COVID-19 pandemic has exacerbated the situation as the number of retired employees has doubled in the 15 months since the pandemic began. The U.S. Bureau of Labor Statistics reports that more than 70 million employees left their jobs in some manner between March 2020 and March 2021.
This puts pressure on leadership to keep pace with operations while searching for qualified new workers to refill their declining workforce. 84% of our survey respondents agree that they are concerned about the ‘Great Crew Change’ and experiencing a gap with the incoming young workforce. The skills gap in the industrial workforce is predicted to leave more than 2 million positions unfilled by 2028.
With older, highly experienced technicians retiring, knowledge of how to run the operation is lost. There are also fewer people around to train the new technicians. This is a skills gap within the company. To make matters worse, the few new technicians who are entering the workforce in asset-intensive industries don’t tend to stick around long.
The Incoming Gen Z Workforce
For Baby Boomers, sticking with a company for the long term was standard. However, it’s more common today for workers to switch jobs every few years. A research from Bankrate revealed that 77% of Gen Zers are thinking about quitting their jobs.
Gen Zers prefer digital processes to analog ones. They use higher-end technologies in their personal lives. It’s no surprise that they have a more positive view of IT strategies that encourage the use of personal devices at work.
With a generation increasingly well-versed in mobile technology and digital connectivity, dealing with outdated, linear, tedious and paper-based operations is highly inefficient. Data collection and processing for inventory and warehouse management, enterprise asset management or fixed asset management processes is particularly frustrating. This frustration, in turn, could contribute to poor morale and employee turnover.
The True Cost of Technician Turnover
According to the Work Institute’s 2020 Retention Report, employee turnover costs companies $15,000 per employee, totalling more than $630 billion in 2019. Each phase of the employee on boarding process incurs a cost to the company. This includes recruiting cost, sign-on bonuses, relocation expenses and background checks etc. However, technician turnover incurs more than the visible costs.
The Society for Human Resource Management reports that an employer needs more than 40 days on average to fill a vacant position. This adds more stress on the management and other team members, affecting employee morale and decreasing productivity.
What’s the Solution?
Leadership must ensure operations run smoothly despite the challenges with the incoming young workforce.
To do this, managers should institute comprehensive on-boarding procedures to ensure new workers clearly understand their roles and how they fit into the overall operation. This will demonstrate to the young workers their jobs have a meaningful impact on the company, a value that holds strong importance to them. Additionally, managers are tasked with boosting employee morale to reduce turnover and with ensuring operations continue smoothly despite a shrinking workforce.
One way to accomplish this is by digitizing operations across maintenance processes. This will appeal to Gen Z workers already used to interacting with electronic and digital devices.
Rather than issuing work orders and inspection checklists in paper binders, or capturing physical inventory movement on paper or outdated “mainframe” looking blue screens on bulky handheld rugged devices, organizations can switch to a “mobile-first” operations platform.
Workers can view and process work orders, and complete inspection forms and checklists via mobile devices. This reduces manual data entry into back office ERP systems, boosting technician productivity, which saves time and reduces frustration. Another important factor is to deliver personalized workflows by user, roles, sites or geographies to drive highest adoption of a “mobile-first” operations platform.
With the entire workforce digitally connected via a mobile workforce management solution, workers and back offices can connect and create a digital dialogue across physical transactions and access important documents while in the field.
For example, an inexperienced technician can instantly look up a needed part in a digitized manual on their mobile device. Mobile plant maintenance systems deliver not only increased technician productivity, but also better morale and job satisfaction. Such a solution also boosts efficiency for the entire plant.
Are you struggling to overcome the Great Crew change and Skills Gaps?
The Great Crew Change is a real challenge for many industries. As experienced workers retire, there is a shortage of skilled workers to replace them. This can lead to unplanned downtime, safety incidents, and decreased productivity.
Innovapptive's mWorkOrder mobile workforce management solution can help you overcome these challenges.
mWorkOrder is a cloud-based solution that provides a mobile-friendly user interface for workers and supervisors. It helps you to:
- Reduce unplanned downtime by up to 90%
- Improve safety by reducing safety incidents by 80%
- Increase workforce capacity by 50%
- Increase wrench time by 17%
mWorkOrder is also highly customizable, so you can tailor it to the specific needs of your workforce. With our patented Rapid Application Configuration Engine (RACE), you can instantly personalize the Gen Z workforce experience by user, roles, sites, or geographies.
See how mWorkOrder can help you overcome the Great Crew Change and Skills Gaps. Click here to see a free demonstration of mWorkOrder, call us at (844) 464-6668, or download our whitepaper on eliminating work order and maintenance backlogs. Don't let the Great Crew Change and Skills Gaps hold you back. Get started today!
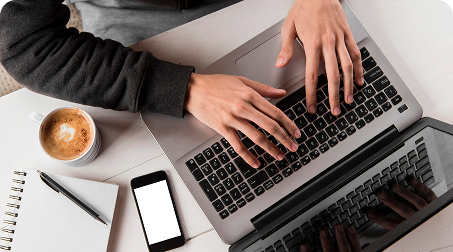
See It In Action
Schedule a personalized demo to see how our solutions can help your business thrive.
- 20-08-2025
Building the future of Industrial Operations with Innovapptive and AWS
Most manufacturers have already gone digital. Yet business outcomes haven’t moved in step. Many...
- 22-04-2025
The $3.6B Unlock: Solving the Chemical Industry’s Labor Crisis and EBITDA Pressure in One Move
“Constraints don’t slow innovation—they force it.”
- 21-04-2025
Chemical Industry's Margin Erosion: A Wake-Up Call for Operational Efficiency Amid China's Oversupply
The global chemical industry is facing mounting challenges, with revenue declines and shrinking...