Digitally Solving the Remote Warehouse Management Dilemma
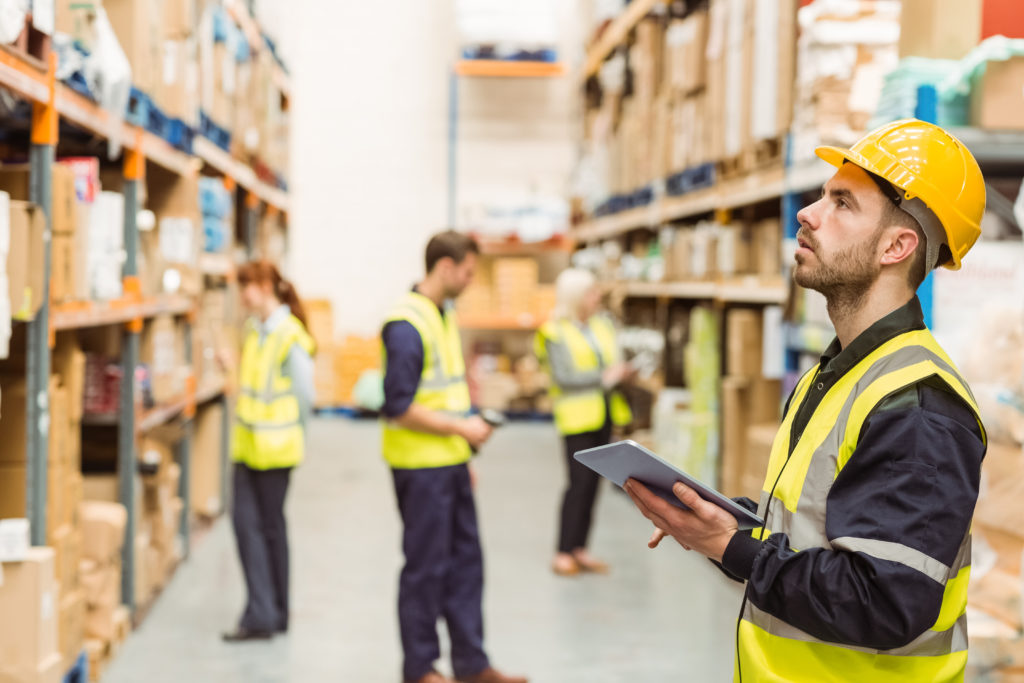
In today’s digital era, technological advancements such as the internet of things (IoT), mobility and AI are opening new doors of opportunity. At the same time many companies, especially those involved in warehouse and inventory management, are still dependent upon aging legacy systems. Many companies control and maintain their remote warehouses from where their supply chain operations take place.
Technology Trends Impacting Remote Warehouse Management
Most of the challenges associated with warehouse and inventory management arise from relying on manual processes, outdated systems, inconsistent data-entry, wasted hours spent tracking down the items stored in the wrong location and more. It creates hurdles providing real-time inventory information.
Having too much unnecessary inventory in stock not only consumes storage space, but also eats into the company’s bottom line. Even unexpectedly running out of stock of essential inventory items causes delays.
Frontline warehouse workers still engage in bulky paper-based processes, and they must transfer data from warehouse to the office and back. Errors caused by manual data-entry lead to delays in the supply chain and sacrifices customer expectation.
Challenges Associated with Remote Inventory Management and How to Overcome Them
There’s the immediate need to break down barriers in inventory management and supply chain. Mobile devices are transforming every corner of human lives. For example, people use mobile devices for playing games, paying their bills, replying to emails on the go, and more.
Now, the time has come for warehouse leaders to leverage the benefits of mobility. To streamline inventory management and add accuracy to the process company-wide, warehouse workers need a mobile solution that can overhaul these issues and boost the efficiency in the warehouse operations. The greatest combination of super-flexibility and easy user interface offered by an enterprise remote warehouse mobile app is invaluable.
Best Practices Using High-Availability Centralized Enterprise Mobile Apps
Providing warehouse employees with an enterprise remote warehouse mobile app can dramatically improve inventory management, resource utilization and enhance productivity. The improved visibility into a diverse array of warehouse and Inventory management allows companies to coordinate activities more precisely and help aligning the business operation within remotely located warehouse and workers teams.
Enabling warehouse employees anytime, anywhere access of business information won’t only provide real-time visibility, increase their convenience, but also greatly help in managing physical inventory movement in real-time. This will improve almost all warehouse functioning from picking, put away, packaging, and shipping, receiving, to cross-docking.
The enterprise mobile app doesn’t only streamline supply chain operations, increase warehouse employees’ productivity, but can greatly enhance safety and emergency response.
Enterprise Mobile Solution for Warehouse Inventory Control and Remote Warehouse Management
Innovapptive offers an SAP-certified, simple, consumer-grade mobile solution - mInventory> - that lets you perform day-to-day inventory transactions through handheld devices and laptops by accessing the master data of the SAP inventory module. The app uses RFID peripheral to automate critical inventory transactions such as inventory cycle counting, goods receipts, goods issue and stock lookups, resulting is accurate and up to date inventory information in SAP. The mInventory mobile app, precise tracking and paperless management of inventory help you increase productivity, lower costs, optimize your supply chain, and improve customer service. It helps you avoid production downtime and enhance your operational efficiency.
Business benefits gained by implementing mInventory:
- Reduce inventory carrying costs with access to real-time stock levels,
- Ensure accurate, up to date inventory information by using barcode scanning for data entry,
- Speed up receipt and back-order reporting to and from shipping/receiving,
- Manage physical inventory movement in real time and improve inventory accuracy,
- Perform physical and cycle counts quickly and achieve greater accuracy of inventory levels,
- Streamline inventory cycle counting and reduce the number of FTEs for cycle counting.
Key Features of mInventory:
- Ruggedized peripherals for RFID, Bar Code or QR Code Scans,
- Scan RFIDs, Bar Codes and QR Codes to ship and receive inventory
- Accept and distribute incoming materials by purchase order,
- View stock detail information at the plant, storage location, and batch level, anytime, anywhere,
- Pre-pick materials and issue, return or transfer goods electronically,
- Ensure inventory cycle count scheduling, counting, and adjustments,
- Print packing slips and bill of lading documents from SAP wirelessly.
Want to Discover More? Here’s How
Watch our short video highlighting how mInventory transformed a client’s warehouse management. Then click here to schedule a free, no-obligation at your convenience.
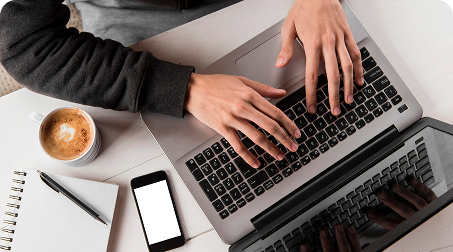
See It In Action
Schedule a personalized demo to see how our solutions can help your business thrive.
- 20-08-2025
Building the future of Industrial Operations with Innovapptive and AWS
Most manufacturers have already gone digital. Yet business outcomes haven’t moved in step. Many...
- 22-04-2025
The $3.6B Unlock: Solving the Chemical Industry’s Labor Crisis and EBITDA Pressure in One Move
“Constraints don’t slow innovation—they force it.”
- 21-04-2025
Chemical Industry's Margin Erosion: A Wake-Up Call for Operational Efficiency Amid China's Oversupply
The global chemical industry is facing mounting challenges, with revenue declines and shrinking...