Take Advantage of the Pop-Up Warehouse Strategy Using Mobile-First Digital Transformation

In this blog, you’ll learn:
- Creating large warehouse spaces is a costly endeavor
- Temporary, or pop-up, warehouses are one way to more cheaply and efficiently distribute products to customers
- Three key steps to consider when setting up a pop-up warehouse
- The role of digital transformation in organizing and operating a pop-up warehouse
The warehouse is the heart of your supply chain. Different companies, including manufacturers, distributors, wholesalers, importers and retailers, operate multiple warehouses. These companies work hard to make their processes leaner and more productive.
However, they fail to implement best practices. Instead, they let inefficient practices prevail in their warehouse. According to McKinsey, these account for 30 percent to 50 percent of total supply chain costs.
For new and small organizations, the expenses of creating a large warehouse space can be enough to sink their business. Add to this, the expensive price tag that comes with sophisticated warehouse management systems.
We're here to tell you that there’s a solution available. With pop-up warehousing, midsize organizations can optimize the management of very simple environments.
Here are three steps in establishing a future-ready pop-up warehouse:
Step one
Identify the gaps and challenges you experience that need resolution to successfully transform your business model. From the difficulty in handling temporary peaks in inventory volume to costly and lengthy shipping requirements, organizations must be able to pinpoint operational issues that constrain warehouse operations.
Step two
Future-proof your strategy. Craft data-driven scenarios to increase operations efficiency at every touchpoint. Pop-up warehouses enable a less-complex, more flexible warehouse operations. To stay ahead, businesses need to implement strategies that will lead them to further significant improvements in inventory turnover, customer service levels and ultimately, overall sales.
Step three
Determine and integrate the systems required. Review existing systems for your operations, as well as alternative solutions in the market. Thanks to “the Amazon effect,” industry leaders need to equip employees with devices designed to enable greater order fulfillment speed and accuracy. Enhanced warehouse mobility can serve your business more improved enterprise-wide visibility.
According to Zebra Technologies, 90 percent of warehouse executives plan to use mobile handheld computers and tablets for real-time, direct access to warehouse management systems.
Maybe you’re one of these executives and you want to take advantage of the pop-up warehouses and technology to improve your distribution and supply chain. What do you do next?
One way is to harness the power of digital transformation. Companies are turning to digital transformation to solve their warehouse and inventory concerns. What is digital transformation? Essentially, it’s the integration of digital technology into all areas of a business. It’s changing how problems are solved and value delivered to customers. It’s challenging the status quo, rethinking operating models and becoming more agile in responding to issues.
Innovapptive, a mobile-first digital transformation provider, offers a solution that enables businesses take make full use of pop-up warehouse strategy. With its Mobile Inventory and Warehouse Management Platform (mInventory), distributors can quickly set up and operate pop-up warehouses practically anywhere that will enable them to reach customers in a low-cost, low-complexity manner.
mInventory users enjoy:
- Immediate access to real-time data via desktop or any mobile device online or offline.
- Reduced manual data entry.
- Fewer errors due to incomplete information.
- Better planning and scheduling.
- Faster turns.
- Less shrinkage.
To learn more about Innovapptive’s mobile solutions for inventory and warehouse management, schedule a free demo today by calling 844-464-6668 or by clicking here.
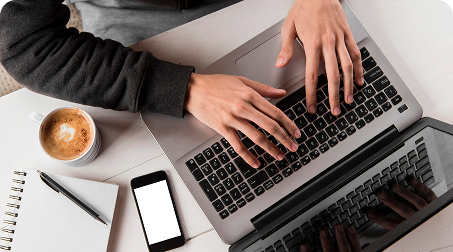
See It In Action
Schedule a personalized demo to see how our solutions can help your business thrive.
- 22-04-2025
The $3.6B Unlock: Solving the Chemical Industry’s Labor Crisis and EBITDA Pressure in One Move
“Constraints don’t slow innovation—they force it.”
- 21-04-2025
Chemical Industry's Margin Erosion: A Wake-Up Call for Operational Efficiency Amid China's Oversupply
The global chemical industry is facing mounting challenges, with revenue declines and shrinking...
- 21-04-2025
Why Wrench Time Isn’t Improving: The Hidden Costs of Traditional Maintenance Scheduling
For years, industrial leaders have relied on a common but flawed assumption: "Better planning and...