Three Technologies Transforming the Maintenance, Repairs and Operations (MRO) Value Chain
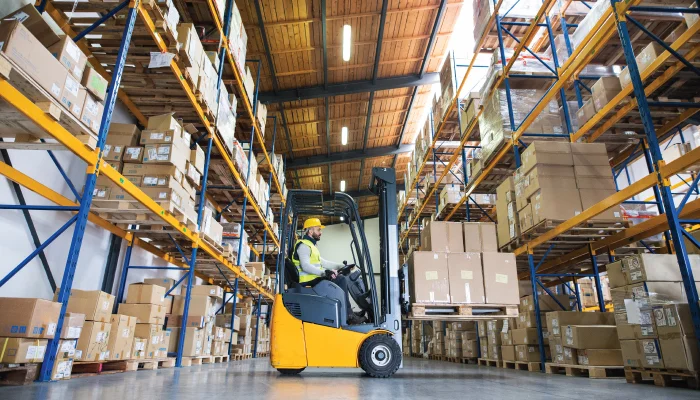
MRO inventory optimization delivers a complete picture how a company’s maintenance, repair, and operations process is performing. Gain valuable insights to improve visibility and decision making. Learn about three new transformative technologies that can boost your company's MRO.
Connected Worker Platform (CWP)
Although companies have invested millions of dollars in their Enterprise Resource Planning (ERP) systems over the past three decades, maintenance, field workers and warehouse staff working outside the office often were overlooked. Technicians needed to return to the office to complete paperwork or get their next assignment. Warehouse workers still struggle with paper pick sheets and inventory count sheets. The lag time between physical work and ERP updates robs managers of real-time visibility into operations.
Maintenance, materials management, and logistics organizations often have separate reporting lines leading to silos and poor decision making. For example, a high proportion of corrective rather than planned maintenance increases maintenance costs and reduces warehouse efficiency as technicians arrive without notice to collect parts. Organizational silos, disconnected Key Performance Indicators (KPIs) and opaque visibility hurt operational performance.
Smartphones and tablets have provided a foundation for improving the MRO value chain. Remote workers can now connect directly with the ERP system to access information and process transactions. However, many organizations use mobile solutions from different vendors for maintenance planning and execution, operator rounds, digital forms, work instructions, and warehousing. Such solutions may be good transactional tools, but they seldom integrate effectively, failing to bridge operational silos and leaving process gaps.
Connected Worker Platforms (CWP) are building on this earlier wave of mobile technology to provide a more comprehensive solution for the MRO value chain. Key CWP features include:
- Desktop Operational Dashboards – Provide real-time operational visibility for managers and supervisors. Managers have an end-to-end view of the MRO value chain, including completed work orders, orders still pending, outstanding supplier deliveries, out-of-stocks, etc. Real-time visibility into operations helps in making timely decisions to resolve problems.
- ERP Process Enhancement – CWPs are correcting the missing functionalities and process gaps in managing the MRO value chain. Leaving paper forms behind, maintenance and inspections are being enhanced by integrating digital forms and work instructions to streamline the end-to-end process. Process gaps inherent in ERP systems are addressed by a kitting process with dashboards showing maintenance and warehouse managers the status of all ongoing activities.
- Mobile solutions – These tools remain a major CWP component but are undergoing revisions to extend end-to-end capabilities to front-line workers. For example, maintenance workers can now view spare parts inventory levels in the warehouse and order parts directly from suppliers.
Freight Control Tower (FCT)
The MRO value chains for parts and equipment are long and complex across industries. If you’re producing oil in Mozambique or mining copper in Indonesia, much of the equipment and spare parts will have started their journey in North America, Europe or China.
The international material flow involves numerous players which makes the associated information flow complex with disintegrated systems, manual processes and disconnects. Besides making management of these value chains difficult, the unavailability of the right part at the right time increases the risk of plant downtime leading to a multi-million dollar hit in lost production.
For years, the majority of freight forwarders have been using track and trace solutions that offer partial visibility. While these solutions capture the date when the material was collected and track the international shipping leg, they do not provide consolidated visibility on all inbound shipments in case multiple players are involved. These solutions based on Electronic Data Interchange (EDI) technology have become obsolete and cost both time and money to integrate different partners across the value chain.
Freight Control Towers (FCT) are modern comprehensive tracking tools that have gained popularity over the traditional track and trace tools in recent times. Let’s look at the advantages of FCT over legacy systems:
- FCT assimilates and displays information from various partner systems and displays it on a unified dashboard offering real-time visibility across the value chain. FCT is based on cloud technology and leverages Application Programming Interfaces (APIs), which are faster and cheaper to implement when compared to the EDI used in traditional tools. The speed and cost with which new partners can be onboarded is a critical success factor for FCT.
- FCT can integrate a full range of partners across the value chain - manufacturers and carriers across all transport modes, retailers, customs, brokers, forwarders and logistics providers. It provides visibility further into the value chain than traditional tracking tools, including manufacturing operations.
- FCT provides customized dashboards to meet the specific needs of each stakeholder in the value chain. The dashboards provide a wealth of information, such as carrier performance, performance by lane, real-time shipment location and landed costs.
- FCT leverages Artificial Intelligence (AI) to predict events. AI can determine the expected arrival date for a shipment and notify customers ahead of time if it's going to be late.
MRO Inventory Optimization Tools
Inventory optimization determines the correct stock holding quantities for MRO parts, balancing service requirements and holding costs. ERP solutions for managing inventory use Materials Requirement Planning (MRP) and simple reorder points/reorder quantities.
The reorder point is when new inventory must be replenished; it's based on historical demand and supplier lead times. However, demand for MRO parts is often intermittent, making it difficult to forecast accurately using traditional approaches. Improving forecast accuracy is critical when up to 50% of unscheduled plant downtime can be due to a lack of spare parts.
Modern MRO parts forecasting tools seamlessly integrate with ERPs. Use them to:
- Leverage Big Data technologies to aggregate data
- Determine reordering points and quantities via specialized algorithms that account for intermittent and variable demand
- Calculate supplier lead times using historical data analysis
- Segment spare parts by criticality
- Perform what-if analyses to design optimum inventory strategies
- Perform “what if” analysis on various scenarios to determine optimum inventory strategies.
Stuck with Outdated MRO Management Technology?
Companies still using older, inefficient MRO management technology owe it to themselves and their frontline workers to investigate the wealth of options available today to improve their warehouse operations and workflows. We’ve discussed three promising technologies in this blog worthy of your consideration:
- Connected Worker Platforms
- Freight Control Towers
- MRO Inventory Optimization Tools
Innovapptive, a mobile inventory solution and connected worker platform leader, can help you with your MRO management technology questions. Our experts are standing by to discuss your needs and ways to successfully meet your MRO challenges. Discover how to boost data accuracy, increase warehouse operations visibility, increase productivity and seamlessly connect frontline workers with back-office supervisors and systems. Schedule a free demo today or call 844-464-6668.
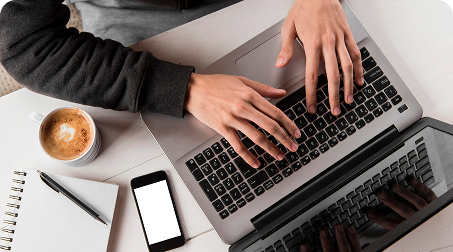
See It In Action
Schedule a personalized demo to see how our solutions can help your business thrive.
- 22-04-2025
The $3.6B Unlock: Solving the Chemical Industry’s Labor Crisis and EBITDA Pressure in One Move
“Constraints don’t slow innovation—they force it.”
- 21-04-2025
Chemical Industry's Margin Erosion: A Wake-Up Call for Operational Efficiency Amid China's Oversupply
The global chemical industry is facing mounting challenges, with revenue declines and shrinking...
- 21-04-2025
Why Wrench Time Isn’t Improving: The Hidden Costs of Traditional Maintenance Scheduling
For years, industrial leaders have relied on a common but flawed assumption: "Better planning and...