Three Unique Features of Innovapptive’s Digital Work Instructions

Industries face two major challenges as the Great Crew Change arrives. The first is a widening skills gap. The average age of front-line industrial technicians in the U.S. is 45.3. Many senior technicians are retiring or are rapidly approaching retirement age. They’re taking valuable tribal knowledge with them. The second challenge is poor wrench time caused by a skills gap among incoming front-line workers. The average wrench time is only between 25% - 35% in most asset-intensive companies. This means a field tech works only 2.5 to 3.5 hours executing the job. For those companies looking to solve these problems, Innovapptive’s Digital Work Instructions offers a path to overcome skills gaps and improve productivity.
Digital Work Instructions Solution Must Haves
A best-in-class digital work instructions solution should at minimum include the following features to empower your technicians:
- Offline capability: Establishing strong Wi-Fi networks in remote locations is complex and costly for companies whose facilities and fixed assets are often spread across wide geographies. A digital work instructions solution should enable front-line workforces to access visual, guided work instructions in offline conditions and sync when the connection is restored.
- Multimedia support: The human brain processes videos 60,000 times faster than text. Maintaining critical industrial equipment involves following complex steps and workflows. Offering visual work instructions via multimedia (including videos and images) helps front-line workers quickly understand processes and take note of hazards and warnings. This enhances occupational safety and improves workers’ efficiency.
- Intuitive design: Your front-line workforce can be made up of several generations of people with varying degrees of technological adaptability. Your solution will drive employees away from adoption if it is cumbersome. Only well-trained staff can use a non-intuitive solution but with great difficulty. A best-in-class Digital Work Instructions solution needs an intuitive user interface.
- Ability to collect actionable information: Insights into time taken for executing jobs empower planning teams with actionable data to plan scheduling effectively. For example, Innovapptive’s Digital Work Instructions solution is integrated with work orders. The solution captures total time taken for executing specific work orders, helping managers to track cycle time per operator.
Why is Innovapptive Better?
Innovapptive, a Connected Worker platform provider, offers a Digital Work Instructions solution that helps you build a highly efficient, productive workforce via collaborative workplaces. Innovapptive’s Digital Work Instructions solution offers a compact set of features (including the ones discussed above and more) and bridges the gap between field technicians and experts at the back-office.
These unique features set the solution apart from the competition:
- Integration with ERP systems: Innovapptive’s Digital Work Instructions solution seamlessly integrates with existing ERP systems such as SAP and IBM Maximo. This empowers front-line technicians with updated job-specific instructions and support at the right time. Integration increases wrench time and efficiency of the front-line workforce while reducing training time, translating into a higher ROI for digital work instructions.
- Integration with work orders: Typically, work instructions are used while executing work orders as part of maintenance operations. Why switch tabs between a work order app and a work instructions solution? Innovapptive’s Digital Work Instructions is integrated with its mobile work order management solution to offer a hassle-free experience to users. This empowers field technicians with instructions specific to a work order, which boosts efficiency.
- Creating multiple instructions at the same time: Thousands of operational procedures and maintenance workflows occur simultaneously in a manufacturing plant. Authoring work instructions one by one becomes cumbersome, increasing the burden on your team. Digital work instructions contain multimedia files and annotations, further complicating the process. What if a digital work instructions solution allows your technical writers to upload content into a spreadsheet and with a few clicks, multiple work instructions are automatically created? Creating work instructions is no longer a complex, time-consuming job. Innovapptive’s Digital Work Instructions offers this efficiency-driving feature.
Want to Learn More about Innovapptive’s Digital Work Instructions?
Click here to schedule a live demo or call 1-844-464-6668 to talk to our experts.
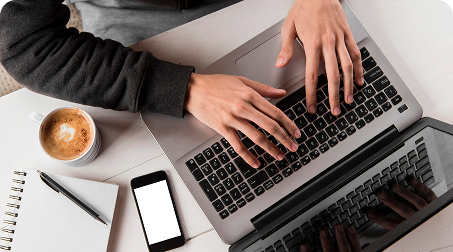
See It In Action
Schedule a personalized demo to see how our solutions can help your business thrive.
- 20-08-2025
Building the future of Industrial Operations with Innovapptive and AWS
Most manufacturers have already gone digital. Yet business outcomes haven’t moved in step. Many...
- 22-04-2025
The $3.6B Unlock: Solving the Chemical Industry’s Labor Crisis and EBITDA Pressure in One Move
“Constraints don’t slow innovation—they force it.”
- 21-04-2025
Chemical Industry's Margin Erosion: A Wake-Up Call for Operational Efficiency Amid China's Oversupply
The global chemical industry is facing mounting challenges, with revenue declines and shrinking...