Why Equipment Breaks Down: A Connected Worker Solution Perspective
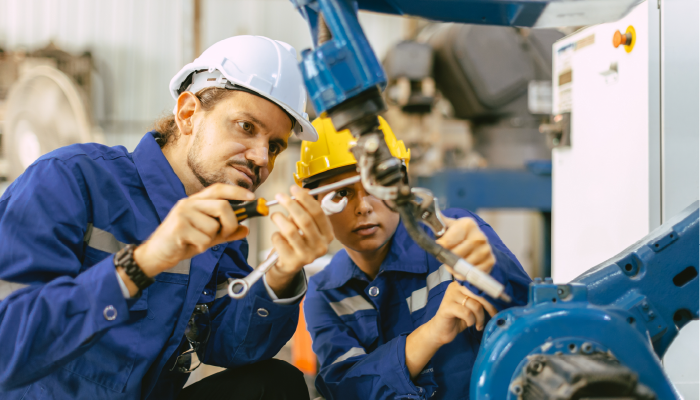
Key Takeaways
- Connected Worker Solutions Lay the Foundation for Predictive Maintenance: By starting with robust preventive maintenance processes enabled by connected worker platforms, companies can significantly reduce downtime by 36% and create a pathway toward advanced predictive maintenance, driving potential savings of up to $34 million annually in asset-intensive industries.
- Improved Communication Minimizes Errors: Connected worker solutions that incorporate digital shift handovers and AI-guided maintenance reduce human error by 30%, improving operational efficiency.
- Optimized Spare Parts Management: Connected worker solutions streamline inventory management, ensuring critical parts availability, reducing downtime, and lowering inventory costs by up to 25%.
Introduction
Equipment breakdown remains one of the most pressing operational challenges across sectors such as mining, chemicals, oil and gas, and manufacturing. In an era where continuous production and operational efficiency are paramount, unplanned equipment downtime doesn’t just affect profitability; it also compromises safety, product quality, and timely deliveries.
According to a 2022 Deloitte report, unplanned downtime can cost industrial manufacturers up to $50 billion annually, with equipment failure accounting for nearly 42% of this figure. Implementing predictive maintenance strategies can significantly reduce these costs by identifying potential issues before they lead to full-scale breakdowns.
This blog explores the primary reasons why equipment breaks down and how connected worker solutions can prevent these failures.
Key Causes of Equipment Breakdowns
- Lack of Preventive Maintenance: Preventive maintenance helps organizations avoid costly repairs and unplanned downtime by identifying potential issues before they turn into significant problems. However, many businesses still rely heavily on reactive maintenance strategies.
- Overuse and Fatigue: Industries like oil and gas or mining often operate equipment beyond recommended limits. Overuse leads to mechanical fatigue, increasing the likelihood of breakdown.
- Human Error: Human error continues to be one of the leading causes of equipment failures. Miscommunication during shift handovers, lack of proper training, and non-compliance with maintenance protocols can exacerbate wear and tear.
- Obsolete or Improper Equipment: Using outdated equipment often increases the risk of failure, especially when organizations try to stretch the operational lifespan of assets to avoid large capital investments.
- Environmental and Operational Conditions: In certain industries, environmental conditions like temperature, humidity, or exposure to corrosive materials significantly contribute to equipment breakdown.
- Supply Chain Issues with Spare Parts: Delays in accessing spare parts can significantly extend equipment downtime, leading to increased operational costs. The growing demand for spare parts, coupled with global supply chain disruptions, has made timely access even more difficult.
- Environmental and Operational Conditions: In certain industries, environmental conditions like temperature, humidity, or exposure to corrosive materials significantly contribute to equipment breakdown.
According to the World Economic Forum, the digitalization of spare parts production, such as 3D printing, has become a key solution to these challenges. Manufacturers are increasingly adopting digital inventory strategies to produce parts on demand, reducing the dependency on traditional supply chains and cutting downtime risks. These innovations help mitigate disruptions, ensuring critical parts are available when needed to minimize delays and associated costs.
The Cost of Downtime Across Industries
Unplanned downtime continues to be a significant financial burden, particularly in asset-heavy industries like oil and gas, chemicals, and mining. In the oil and gas sector, unplanned downtime is especially costly. Offshore platforms experience an average of 27 days of unplanned downtime annually, leading to financial losses of approximately $38 million. For those with suboptimal maintenance practices, this number can skyrocket to $88 million per year. Even a seemingly minor downtime event of just 3.65 days—or 1% of the year—can cost an oil and gas company over $5 million, according to Hydrocarbon Engineering.
In the chemical industry, the costs are similarly staggering. Downtime in this sector averages around $125,000 per hour, according to Industry Today, affecting not only production but also contributing to delays in processes downstream. Given that over two-thirds of companies in industries like chemicals and refining experience unplanned downtime at least once per month, the cumulative financial impact is significant.
In the mining industry, unplanned downtime is driven by environmental factors and aging equipment, which can severely disrupt operations. Studies indicate that inefficient maintenance strategies cost mining companies millions annually, with the average downtime expense being as high as $180,000 per hour in some cases, according to MRO Magazine. These disruptions are often caused by harsh environmental conditions, including dust, heat, and mechanical wear from continuous heavy usage. As a result, mining companies face not only direct costs from repairs but also lost production time, which can accumulate to substantial financial losses over the course of a year.
The High Cost of Equipment Failures
In the oil and gas industry, downtime-related expenses extend well beyond just the direct costs of equipment repairs. According to Hydrocarbon Engineering, 71% of these costs are attributed to repairs, while 40% stem from labor, and another 37% from logistics. This clearly shows that the financial burden of unplanned downtime involves extensive coordination and effort across multiple areas, not just the physical repair of equipment.
Similarly, MRO Magazine highlights how downtime can sharply increase labor costs, especially when emergency repairs necessitate overtime or hiring additional contract workers. The need to expedite parts that are not readily available further drives up operational costs, compounding the overall financial impact of unplanned outages.
Moreover, equipment failures in remote oil and gas locations can also result in extensive delays due to long lead times for spare parts, exacerbating the downtime costs.
How Connected Worker Solutions Prevent Equipment Breakdown
Connected worker platforms, equipped with real-time data and predictive maintenance tools, offer a proactive approach to reducing unplanned downtime. According to McKinsey & Company, predictive maintenance strategies can cut downtime by 36% compared to reactive approaches. This reduction allows companies to schedule maintenance before equipment failures escalate, leading to significant savings. In the oil and gas sector, these strategies can save up to $34 million annually by enabling more efficient maintenance planning and avoiding costly unplanned outages.
In addition to cost savings, predictive maintenance improves equipment reliability. McKinsey reports that adopting these technologies can reduce overall maintenance costs by 30-50%, further enhancing operational efficiency and production.
By integrating real-time data with optimized maintenance workflows, connected worker platforms help industries make data-driven decisions, ensuring better resource allocation and reducing the dependency on traditional, often slow, maintenance practices. For industries with remote or difficult-to-access facilities, such as oil and gas, mining, or chemicals, connected worker solutions also improve communication and inventory management, ensuring the availability of critical spare parts when needed.
How Else Do Connected Worker Solutions Reduce Costly Downtime?
- Real-time Data and Predictive Maintenance: Connected worker platforms leverage IoT devices and advanced analytics to continuously monitor equipment conditions in real-time. Predictive maintenance reduces unplanned downtime by identifying potential failures before they occur. A Deloitte 2022 study showed that predictive maintenance can lead to a 10-20% increase in equipment uptime, reducing downtime costs significantly.
- Improved Communication During Shift Handover: Miscommunication during shift changes is a leading cause of operational errors. Connected worker platforms facilitate digital shift handovers, reducing the risk of human error. A Capgemini 2021 survey found that companies using digital shift handovers reduced human error by 30%.
- Optimized Spare Parts Management: By integrating advanced spare parts inventory management into maintenance workflows, connected worker platforms streamline the availability of critical parts when they are needed most. This proactive approach helps organizations avoid the pitfalls of stockouts, overstocking, and extended lead times that often result in prolonged downtimes. According to a report by IBM, effective spare parts management can reduce the working capital tied up in inventory by up to 25% while simultaneously lowering the costs of carrying excess stock. Moreover, by leveraging real-time data and analytics, businesses can achieve higher accuracy in forecasting demand for parts, ensuring that maintenance teams have the right parts at the right time, ultimately reducing the risk of unplanned equipment downtime.
Prevent Breakdowns with a Connected Worker Platform
As industries prioritize operational efficiency, preventing equipment breakdowns has become a critical factor in maintaining competitiveness. Connected worker solutions offer the transformative power to shift from reactive to predictive maintenance, drastically reducing human error and optimizing spare parts management. The result? Reduced downtime, improved safety, and a significant boost in productivity—clear financial advantages that no forward-thinking industrial organization can afford to ignore.
FAQ
What are the main causes of equipment failure in industries like oil & gas and mining?
Equipment failures are primarily caused by a lack of preventive maintenance, overuse, human error, and environmental factors like temperature and humidity. Aging equipment and supply chain issues with spare parts also play a major role.
How does unplanned downtime impact businesses financially?
Unplanned downtime can be extremely costly, with industries like oil & gas losing millions annually. For example, offshore platforms can experience $38 million in annual losses due to downtime, and downtime in the chemical sector can cost $125,000 per hour.
What role does preventive maintenance play in avoiding equipment breakdowns?
Preventive maintenance helps identify potential failures before they occur, significantly reducing the risk of breakdowns. Businesses that adopt predictive maintenance strategies can reduce downtime by 36%, saving millions annually.
How do connected worker platforms help prevent equipment failures?
Connected worker platforms leverage real-time data and predictive maintenance tools to detect equipment issues early, allowing businesses to schedule maintenance before major failures occur. This can save industries like oil & gas up to $34 million annually.
How do connected worker solutions reduce human error in maintenance operations?
These platforms use digital shift handovers and AR-guided maintenance to improve communication and reduce the risk of human error during operations. Studies show that using digital tools can reduce human error by up to 30%.
How do connected worker platforms improve spare parts management?
Connected worker platforms optimize inventory management, ensuring critical spare parts are available when needed. This reduces downtime due to part shortages and lowers inventory costs by up to 25%.
What features does Innovapptive’s Connected Worker Platform offer to prevent equipment breakdowns?
Innovapptive’s platform provides mobile-enabled predictive maintenance, real-time equipment data access, digital shift handovers, and AR-guided maintenance, helping organizations prevent breakdowns and minimize downtime.
How does Innovapptive’s platform improve communication between maintenance teams?
The platform digitizes the shift handover process, ensuring that all team members are updated and aligned, which reduces miscommunication and prevents errors that can lead to equipment failure.
How can Innovapptive’s AR-guided maintenance reduce improper repairs?
Innovapptive’s platform offers augmented reality (AR) tools that guide maintenance workers through complex tasks, reducing the chances of improper repairs and ensuring that equipment is serviced correctly.
What industries benefit the most from Innovapptive’s Connected Worker Platform?
Industries with heavy machinery, such as oil & gas, chemicals, and mining, benefit significantly from Innovapptive’s platform due to its ability to reduce downtime, improve safety, and increase overall productivity.
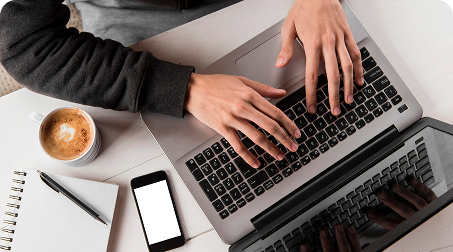
See It In Action
Schedule a personalized demo to see how our solutions can help your business thrive.
- 20-08-2025
Building the future of Industrial Operations with Innovapptive and AWS
Most manufacturers have already gone digital. Yet business outcomes haven’t moved in step. Many...
- 22-04-2025
The $3.6B Unlock: Solving the Chemical Industry’s Labor Crisis and EBITDA Pressure in One Move
“Constraints don’t slow innovation—they force it.”
- 21-04-2025
Chemical Industry's Margin Erosion: A Wake-Up Call for Operational Efficiency Amid China's Oversupply
The global chemical industry is facing mounting challenges, with revenue declines and shrinking...