Connected Inventory: 5 Advantages of Automating Inventory Management for Your Food and Beverage Company
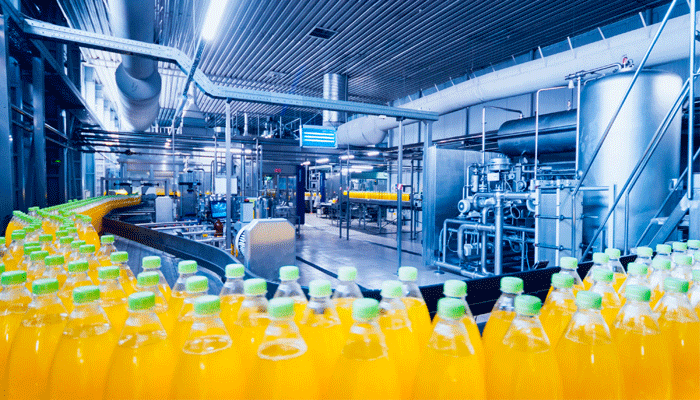
Food and beverage industry trends are widely based on seasonal produce and consumer food choices. Inventory in the food and beverage industry, majorly food products, are quickly perishable and hence have a limited shelf life. The real-time traceability of raw materials throughout the supply chain is essential to avoid food contamination and consequential health hazards. So, food and beverage companies need a proper inventory management system in place to help their staff determine and manage the expiry dates of materials.
The dangers of foodborne diseases are high when the materials are not properly processed or not stored hygienically. Any such unwanted incidents may induce uncontrollable consequences just as the novel coronavirus was allegedly transmitted from bat meat to humans and has created the COVID-19 pandemic. This will damage the reputation of a food and beverage company and can lead to its shutdown. So, it is equally important for food and beverage companies to ensure that standard operating procedures are strictly followed.
What’s tainting inventory management in the food and beverage industry?
Food and beverage companies have attained technical prowess and transformed their production units with advanced machinery. However, most of them are still using legacy systems and paper trails for executing inventory management operations. Human errors are obvious while entering data manually. That inaccuracy has a steep price. IBM estimates that poor-quality data costs U.S. companies $3.1 trillion a year. To ensure the correctness of data, inventory staff should invest extra time cross checking things. A food and beverage company can choose either data accuracy or speed, both of which play key roles in operations.
Today’s food and beverage warehouse managers are under increasing stress to streamline their operations and enhance operational efficiencies. According to a recent study by Honeywell on this topic, the research found the following:
- 80 percent of surveyed participants need to find an average of 19 percent cost savings from existing operations.
- 43 percent say high turnover and employee retention is their biggest issue.
- Online orders received by 2 p.m. need to be fulfilled the next day. Warehouse operations face a myriad of productivity pressures.
The speed you see in manual data collection is not the speed you need to stay competitive in the modern-day world. Legacy systems carry a number of avoidable roadblocks to achieving true speed and accuracy.
Some of these are:
- Unnecessary travel from back-office to the warehouse. Warehouse staff needs to visit the back-office to collect documents and other materials needed to execute tasks. If they forget any single paper, they need to travel again to the back-office.
- Manual data entry: While performing receiving and issuing goods, physical inventory or cycle counting, warehouse staff needs to track the batch number or serial numbers of the raw materials. They need to keep track of the expiry dates and other product information that helps determine the shelf-life of the materials. Manually entering this data can lead to errors.
- Unreliable data: Once they are done with the task, they need to carry the papers back to the back-office, where the data is entered into the ERP systems such as SAP and IBM Maximo. Meanwhile, some papers may get lost, causing data unreliability.
In addition, the cost of outdated technologies and inefficient processes are also very steep:
- 3,000 work hours are lost/year in the average warehouse due to inefficient processes.
- 60 percent agree that huge savings can be achieved by cutting seconds off operational workflows.
- $459K can be saved by process re-engineering, and connected worker and mobile technologies.
Automate inventory management with Connected Inventory:
Connected Inventory solutions use advanced digital technologies for automatic identification data capture to improve throughput and speed. These solutions empower the warehouse staff with mobile devices that will eliminate manual, tedious and linear paper based processes and offer real-time insights into the inventory.
The advantages of using Connected Inventory for inventory management in the food and beverage industry are:
- Single source of information: A mobile Connected Inventory solution enables warehouse staff to access all required documents via their mobile phones or other rugged hand-held devices. This will eliminate unnecessary travel to the back-office and saves time.
- Remove human errors: An ideal Connected Inventory solution features Optical Character Recognition (OCR) and barcode scanning capability. These features enable warehouse staff to read the serial numbers and batch numbers of the raw materials and feed them directly into the ERP systems. This will completely eliminate the scope for human errors in data entry.
- Real-time notifications to avoid spoilages: Connected Inventory solutions will automatically alert warehouse managers about the expiry dates and critical information on the food materials. This will help the warehouse managers ensure the products are used before they perish. This will avoid waste and food contamination.
- Enforce standard operating procedures: As we discussed earlier, following standard operating procedures in food processing, storing, and transporting is crucial. If these procedures are not documented properly, employees may miss some important steps, leading up to food decays and related health hazards. Using a Connected Inventory solution, warehouse managers can enforce standard operating procedures and ensure they are strictly adhered to.
- Capture tribal knowledge: Tribal knowledge is the knowledge about something that is not documented but gained by experience. Senior employees in the warehouse know how to respond to a particular situation as they have already experienced it. Sooner or later, they will retire and young employees will replace them. These novice employees may not have tribal knowledge to respond to a particular situation. And this may cause great financial losses and occupational hazards. Connected Inventory solution will enable warehouse staff to document their knowledge by instantly creating forms and checklists in real-time. This information will be stored in the back-office systems and can be shared with employees across the organization.
Do you want to see how a Connected Inventory solution works for your food and beverage company? Reach out to team Innovapptive for a customized live demo. Or you can dial 1-844-464-6668 and talk to our Connected Inventory expert.
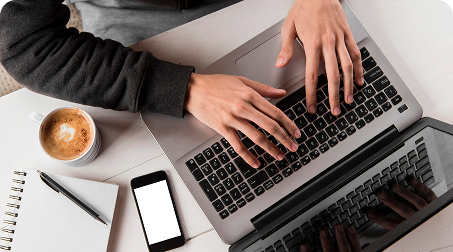
See It In Action
Schedule a personalized demo to see how our solutions can help your business thrive.
- 22-04-2025
The $3.6B Unlock: Solving the Chemical Industry’s Labor Crisis and EBITDA Pressure in One Move
“Constraints don’t slow innovation—they force it.”
- 21-04-2025
Chemical Industry's Margin Erosion: A Wake-Up Call for Operational Efficiency Amid China's Oversupply
The global chemical industry is facing mounting challenges, with revenue declines and shrinking...
- 21-04-2025
Why Wrench Time Isn’t Improving: The Hidden Costs of Traditional Maintenance Scheduling
For years, industrial leaders have relied on a common but flawed assumption: "Better planning and...