5 Challenges Facing Chemical Companies in 2022: Can Mobile Workforce Management Offer a Solution?
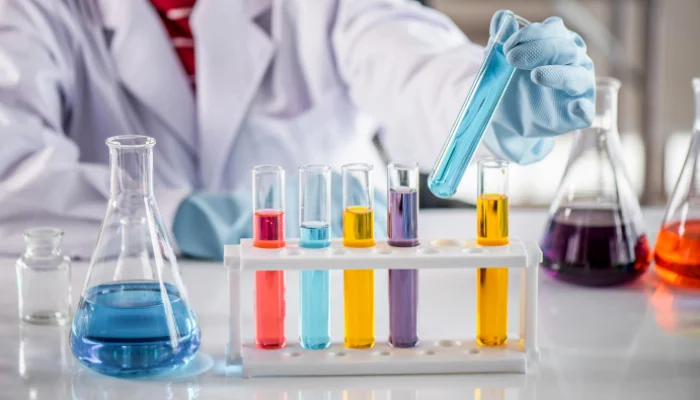
Mobile workforce management solutions such as connected worker platforms can solve 5 major maintenance challenges for chemical plants.
The chemical industry emerged strong from the economic crisis in 2020 and continued the rally in 2021. However, this journey isn’t without its challenges. Companies will need to face new barriers in addition to the existing ones. Here are five chemical industry challenges companies need to address to keep up growth and increase revenues as we enter the mid-2020s. Learn how a mobile workforce management solution can help chemical companies effectively meet and overcome these tests.
1) Fighting Climate Change: The chemical industry is one of the Top 3 contributors to global carbon emissions. Chemical products are carbon-intensive. For example, global ammonia production accounts for 1.8% of total carbon dioxide emissions. However, chemical products are essential for most of the low-carbon technologies, making this sector 'hard to abate.' As the world is more concerned about climate change, chemical companies need to explore new approaches to contain carbon emissions. They need to focus on boosting their efficiency while pursuing breakthrough technologies and utilizing renewables.
2) Skills Gaps: The Great Crew Change has opened up a wide skills gap in the chemical industry as experienced workers are hanging their boots. The chemical industry is facing difficulties in finding the right talent, who can combine scientific knowledge with digital skills. The industry greatly needs collaborative working, knowledge sharing across organizational and international boundaries. Transferring knowledge from senior technicians to newcomers is essential to bridge the skills gap. Leveraging mobile connected worker technologies like configurable digital work instructions will help you enhance your employees’ skills and boost operational efficiency.
3) Occupational Safety: Chemical industry is notoriously known for safety incidents as it deals with hazardous materials and heavy equipment. Companies have been taking measures to prevent accidents. However, with growth and expansion comes greater challenges. Most other manufacturing industries rely on the chemical industry. Chemical companies are scaling up their production and upgrading their systems. So, safety measures are an everyday activity. Equipment failures, insufficient safety checks, operator errors, and ignoring warnings are major causes for accidents. Frontline workers in chemical companies are unconnected because of the inefficiency of paper-based processes they use. Companies can use mobile operator rounds solutions to boost efficiency.
4) Supply Chain Volatility: Chemical companies heavily rely on supply chains as they procure raw materials from different parts of the world. Global supply chains are vulnerable to disruptions due to pandemics, geopolitical matters, blockage of sea lanes, etc. Chemical companies have limited or no control over these factors. However, they can identify signals of an upcoming disruption and manage their inventory levels to match the supply and demand. Though they use inventory management solutions, they need to find gaps in their supply chain management (which includes raw materials, final products and spare parts inventory). Isolating supply chain management from other departments is a troublemaker. You should create an integrated digital ecosystem to get an end-to-end visibility into production and business operations.
5) Controlling Operating Costs: Chemical companies are facing tough competition from new competitors from emerging markets. Production costs in those countries are cheaper and they have better access to the international market. This is tightening the race. Also, customers of chemical companies, who are in other manufacturing industries, are fighting demand volatility. Chemical companies need to collect and analyze market data to observe demand patterns and make informed decisions. Chemical plants should run at their full capacity to earn higher ROI. To achieve this, companies should rehaul their operations with advanced capabilities like connected worker technologies.
Discover the Power of Mobile Workforce Management
Innovapptive offers a best-in-class mobile workforce management solution to help chemical companies advance their digital transformation efforts. This solution uses the versatility and agility of mobile-first frontline worker applications to replace inefficient manual processes that cause low productivity, higher operating costs, decreased safety and other problems as described in this blog. Instead, frontline workers are empowered to accomplish their tasks faster, safer and cheaper than before. Request a free demo today or call 844-464-6668 to talk to our experts.
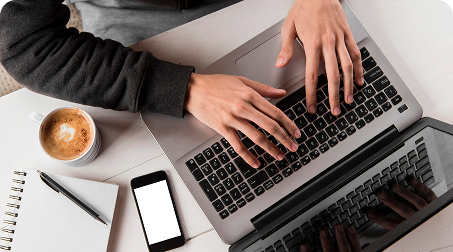
See It In Action
Schedule a personalized demo to see how our solutions can help your business thrive.
- 20-08-2025
Building the future of Industrial Operations with Innovapptive and AWS
Most manufacturers have already gone digital. Yet business outcomes haven’t moved in step. Many...
- 22-04-2025
The $3.6B Unlock: Solving the Chemical Industry’s Labor Crisis and EBITDA Pressure in One Move
“Constraints don’t slow innovation—they force it.”
- 21-04-2025
Chemical Industry's Margin Erosion: A Wake-Up Call for Operational Efficiency Amid China's Oversupply
The global chemical industry is facing mounting challenges, with revenue declines and shrinking...