5 Things to Consider When Choosing a SAP Mobile Inventory and Warehouse Management Solution
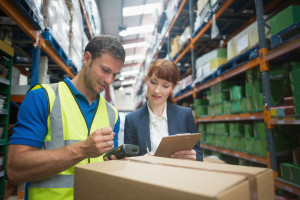
Why is inventory management so crucial for your business?
Too much or too little inventory exerts pressure on your company, increasing carrying costs or resulting in lost sales and revenue. You should strike a balance between supply and demand. Inventory management is not just about the timely movement of physical goods from one location to another, it’s also about managing the vast amount of information associated with these goods.
Efficient inventory and warehouse management is often considered as a time-consuming exercise – greatly influencing the day to day operations and overall success of the business. A mobile inventory management solution streamlines and optimizes your company’s warehouse operations.
Key Considerations While Investing in a Mobile Inventory Management Solution
There’re a variety of solutions available in the market. But one size doesn’t fit all. You should understand your warehouse’s requirements and evaluate each solution with care considering some ideal characteristics of an inventory solution. Some of the considerations include:
- Quick and easy setup - An ideal, best-in-class mobile inventory & warehouse management solution should easily and smoothly integrate with your existing systems. You should carefully consider the prerequisites for setting up a mobile solution, lest your IT team may end up wasting time in complex configurations and maintenance activity.
Look for a solution that has a simple setup, particularly hosted through a cloud service that eliminates huge installation and maintenance costs. This way, a good mobile inventory solution can make the first impression with most of the users, who may be exceptional functional experts, but still a novice in technology.
- Affordable - Even if you have software that boasts of exceptional value-added features, ultimately, cost plays a major role in influencing your purchasing decisions. A typical solution should be affordable including the costs related to maintenance, upgrades and after-sales support. This way, even small or startup businesses can get access to cutting-edge inventory management technology without a huge investment. Companies that are looking to keep their operating costs low can look for a provider that offers the best-in-class solution within their predetermined budget.
- Real-time inventory tracking - A good solution should offer real-time inventory tracking that helps you have a good grasp of accurate inventory levels and data. It should also help in viewing your stock levels or generate reports for quick decision making. A best-in-class solution should feature barcode, RFID, QR code scanning and OCR (Optical Character Recognition) capabilities that will simplify inventory tracking. This will also increase the accuracy of inventory tracking by eliminating the need for manual data entry and human errors.
- Simple and user-friendly interface - As mobile screens are much smaller in size, compared to a desktop monitor, the UI of the solution that you purchase has to be simple and easy to use. It should eliminate complex functional jargon and workflows, while keeping the essentials to ensure that data is quickly accessed and processed to ensure enjoyable user experience.
- Automated inventory transactions - A typical mobile inventory solution can help in streamlining core inventory transactions such as goods receipts, issues, transfers and returns as well as helps in data processing of receivables and much more. This way, your organization can ensure an automated, yet speedy inventory management system that helps in eliminating redundant and inefficient manual processes, while enhancing the overall operational and process efficiency.
There’s one key feature you should look for...
There’s a disconnect between your warehouse and back-office systems, reducing your warehouse throughput. What you should look for is a solution that acts as a nexus between the warehouse and back-office, eliminating all the double work you have been doing. Innovapptive’s mobile inventory management solution is one such unique solution, designed to integrate with the existing SAP systems for modules such as Inventory Management (IM), Warehouse Management (WM) and Extended Warehouse Management (EWM).
Key Features and Value Drivers of Mobile Inventory Management
- Scan RFIDs, barcodes and QR codes to ship and receive inventory,
- Accept and distribute incoming materials by purchase order,
- View stock detail information at the plant, storage location and batch level, anytime, anywhere,
- Receive gods and putaway,
- Pre-pick materials and issue, return or transfer goods electronically,
- Ensure inventory cycle count scheduling, counting and adjustments,
- Print packing slips and bill of lading documents from SAP wirelessly,
- Print USPS, FedEx and UPS shipping labels,
- Check availability of materials while on the job.
Want to See Mobile Inventory Management in Action?
Get in touch with us to get a customized live demo of Innovapptive’s SAP mobile inventory and warehouse management solution, Mobile Inventory Management. Or dial 1-844-464-6668 to talk to our experts.
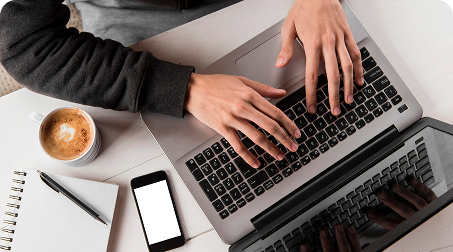
See It In Action
Schedule a personalized demo to see how our solutions can help your business thrive.
- 22-04-2025
The $3.6B Unlock: Solving the Chemical Industry’s Labor Crisis and EBITDA Pressure in One Move
“Constraints don’t slow innovation—they force it.”
- 21-04-2025
Chemical Industry's Margin Erosion: A Wake-Up Call for Operational Efficiency Amid China's Oversupply
The global chemical industry is facing mounting challenges, with revenue declines and shrinking...
- 21-04-2025
Why Wrench Time Isn’t Improving: The Hidden Costs of Traditional Maintenance Scheduling
For years, industrial leaders have relied on a common but flawed assumption: "Better planning and...