5 Reasons Why Manufacturers Need Mobile Operator Rounds
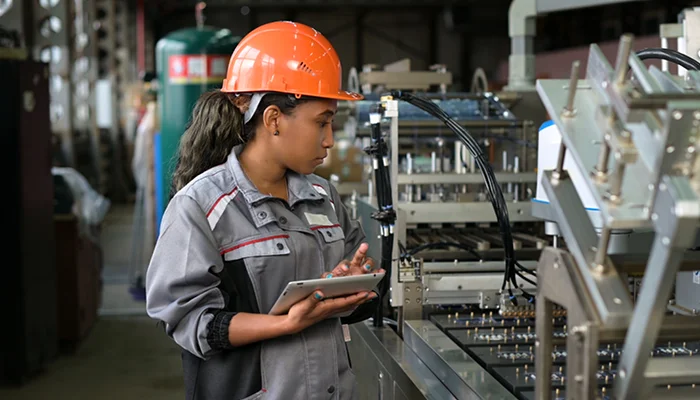
More than two out of every three manufacturing plants in a recent survey revealed they had no idea when their equipment was due for routine maintenance or important upgrades, according to Vanson Bourne. So it’s no surprise that the same survey found that 82% of all plants have suffered at least one unplanned shutdown in the last three years. This lack of knowledge increases maintenance costs, decreases equipment reliability and uptime, and leads to unsafe conditions. Daily mobile operator rounds can reverse this by identifying potential operational and safety issues before they become costly problems.
Unfortunately, too many manufacturing organizations overlook digitizing their operator rounds and conduct them using paper checklists and clipboards. Paper-based operator rounds hinder inspections and increase the chance of human error. They also take additional time to enter the captured information into the back-office ERP, adding delays in getting critical information into the hands of decision makers for action.
Mobile-first operator rounds help manufacturing companies organize, conduct, share, and review daily equipment and safety inspections. The solution provides maintenance managers, supervisors, and frontline workers instant operational visibility, greater flexibility, and reporting agility.
Benefits of Digitizing Operator Rounds
Here are five key areas where a mobile operator rounds solution connected can make a significant impact on maintenance activities and safety compliance.
Reduce preventable failures – The majority of plant equipment failures are avoidable. Many plants still use a reactive run-to-failure maintenance strategy that delays repairs until something breaks. A mobile-first operator rounds lets manufacturing plants become more proactive in their maintenance activities. Instead of waiting for a part or piece of equipment to break before starting repairs or replacement, a mobile-first operator rounds program enables maintenance teams to identify any issues and take appropriate action ahead of any failure.
Decrease unplanned downtime – The average manufacturing plant suffers 800 hours of unscheduled downtime yearly, according to Due.com, which Forbes estimates costs the industry $50 billion every year. This situation not only negatively impacts production, it also puts customer relations at risk and affects the bottom line. Mobile operator rounds deliver greater real-time visibility into current production equipment condition. It gives decision makers actionable insights to take remedial action to forestall equipment failures and increase asset uptime.
Improve productivity –Planners can configure or edit a round plan based on unique plant needs and changing regulatory rules. Meanwhile, operators can conduct the round, collect required information, and trigger corrective workflow completely on a mobile device (smartphone or tablet). This capability means operators can complete rounds much quicker, obtain more-thorough data, and automatically share that information with supervisors and managers in real time. There is no need to route paper round forms or manually enter round data into the back-office ERP. This means operators can rapidly get back to their primary duties.
Reduce costs – Related to the above point, administrative costs are cut because no manual data entry is necessary by either a technician or a back-office staff member. There's no reason to print out, route, scan, or store completed paper forms. Maintenance costs drop because there are fewer equipment breakdowns and failures.
Boost compliance – Mobile-first operator rounds enable quick and accurate risk assessment and modeling, with accurate real-time data to boost forecasting, planning, and scheduling. Mitigation efforts become more effective as complete information is collected about safety hazards and conditions throughout the plant. Swifter action on potential hazards and risks results in fewer safety incidents, cutting missed work time, fines, and penalties.
What Makes Innovapptive’s mRounds Cloud-based Mobile Operator Rounds the Best Choice
Innovapptive, a global connected worker solution leader, has developed a Cloud-based mobile operator rounds solution called mRounds. mRounds offers asset-intensive organizations – like manufacturing plants – the ability to digitize important plant operations and safety functions without the need to tie them into a back-office enterprise resource planning system (ERP) like SAP.
mRounds offers several distinct advantages that set it apart from other solutions now on the market:
- Easy configuration to meet your unique needs - Customize mRounds to local geographies, specific end-user roles, and more. No previous technical knowledge or coding experience is required.
- Completely digital solution - Get rid of paper forms and binders. mRounds work on mobile devices and wearables.
- No back-office system is required – mRounds can operate as a standalone, Cloud-based solution untethered to an ERP. This can reduce operating costs and provide greater utility in use. The application can be integrated with an ERP if needed.
- Intuitive and easy to use - Frontline workers can be productive immediately as the solution requires little or no training. mRounds' superior user experience promotes high user adoption rates.
- Get up and running instantly – mRounds can be deployed in as little as two weeks, providing a rapid time to value.
Want to Take Your Operator Rounds to a Higher Level
Visit our dedicated mRounds microsite to discover more about the benefits of moving from a paper-based process or an ERP-integrated solution. Or, watch a short, 2-minute video illustrating mRounds’ many benefits. Ready to make a move? Schedule a free demo today or call 844-464-6668 to speak to one of Innovapptive’s experts.
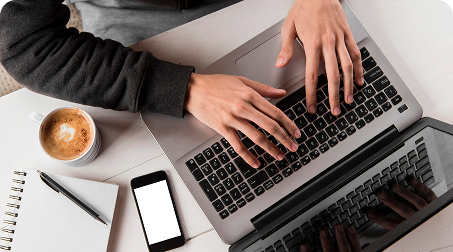
See It In Action
Schedule a personalized demo to see how our solutions can help your business thrive.
- 20-08-2025
Building the future of Industrial Operations with Innovapptive and AWS
Most manufacturers have already gone digital. Yet business outcomes haven’t moved in step. Many...
- 22-04-2025
The $3.6B Unlock: Solving the Chemical Industry’s Labor Crisis and EBITDA Pressure in One Move
“Constraints don’t slow innovation—they force it.”
- 21-04-2025
Chemical Industry's Margin Erosion: A Wake-Up Call for Operational Efficiency Amid China's Oversupply
The global chemical industry is facing mounting challenges, with revenue declines and shrinking...