5 Reasons Why Oil and Gas Facilities Need Digital, Interactive Work Instructions
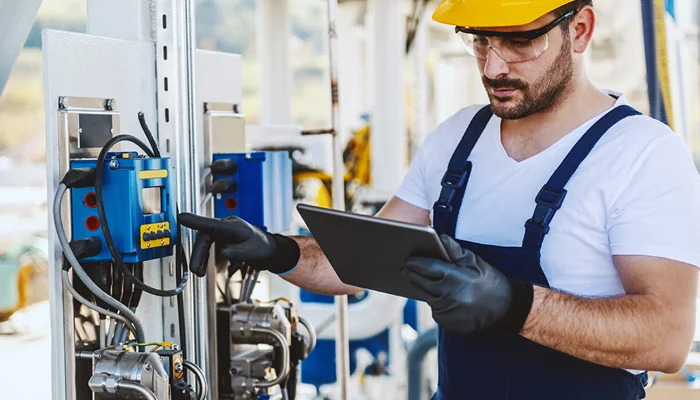
Oil and gas companies face the loss of valuable tribal knowledge while training a new generation of frontline workers. Interactive work instructions can help these organizations recruit and retain workers, increase wrench time, reduce reworks and preserve institutional experience.
Unfortunately, oil and gas companies often overlook their field workers in digital transformation efforts. These organizations stick to old-school practices, including paper-based work instructions for their maintenance teams, which result in poor performance and higher costs. Here are five reasons why upstream, midstream and downstream oil and gas companies should include interactive work instructions (also known as digital work instructions) in any drive to optimize operations and gain a competitive advantage.
Reason 1: Improve Wrench Time
Wrench time is the time a technician spends on actual work using tools. A big part of a tech’s day revolves around getting parts or waiting on work instructions and other documentation. The average oil and gas maintenance technician's wrench time is only 25% to 35%. That means a field tech works only 2.5 to 3.5 hours a day executing the job (for example, repairing a piece of equipment or replacing parts).
Digital work instructions bridge field technicians and experts at the back office, saving considerable time. Technicians directly receive work instructions on their smartphones and jump to the next task without wasting time, boosting wrench time. Wrench time has a proportional relationship with productivity. On average, companies can see a 57% boost in productivity if wrench time rises to 55% from 35%. This increase comes effortlessly without spending additional resources.
Reason 2: Reduce Reworks and Backlogs
A rework is any piece of equipment that fails within 60 days or less after a repair work order's completion. Several factors can cause a rework:
- Poor operating procedures
- Improper maintenance processes
- Subpar materials and parts
- Inadequate maintenance planning
- Lack of proper training or skills
Reworks tend to increase when a maintenance team has a large number of new hires or a less experienced workforce (perhaps due to a rash of retirements or a layoff). New or recent hires naturally lack the experience and know-how built up over a long career. They don’t possess the tribal knowledge of those who have worked at the site for years.
That means, of course, they’re prone to making more mistakes, which leads to more reworks. The more reworks an upstream, midstream or downstream facility has to contend with, the less efficient its overall maintenance is. It also increases the chance for unplanned downtime and production disruptions that can threaten revenues.
Reason 3: Overcome Skills Gaps
Over 60 thousand American oil and gas workers are age 55 or older. They’re literally at retirement’s door. Upstream, midstream and downstream companies face large-scale tribal knowledge losses soon. This loss will create a skills gap in the frontline workforce.
Older workers know things about a plant’s or facility’s operations, processes and equipment that aren’t in any manual or spreadsheet. When a problem arises, they draw upon this deep well of knowledge and experience to help them solve issues.
A younger worker must lean on an older one for mentorship (the ideal solution) or learn through trial and error (the costlier alternative). Trial and error mean past mistakes may be needlessly repeated, leading to more reworks, higher backlogs and a greater risk of unplanned downtime.
Reason 4: Hire and Retain the Best Talent
Younger workers today are comfortable with technology. For them, it’s not something wondrous and new - it’s something they’ve handled and dealt with for as long as they can remember.
Gen Z members (born between 1997 and 2012 and now entering the workforce) are digital natives. They expect their employers to be comfortable with technology, too. Gen Z assumes employers utilize technology as a time and labor-saving tool. These younger workers are often quite surprised – and disappointed – when they learn a company is still using walkie-talkies, Excel spreadsheets, or clunky paper binders and forms to collect and share crucial operational data.
Younger workers value innovation, engagement and collaboration, not the information silos often found in paper-based processes. As a result, they become disenchanted and seek more exciting opportunities elsewhere, resulting in an expensive talent search to replace them.
Reason 5: Maintain Regulatory Compliance
Agencies and the politicians that create EHS rules and regulations are becoming sensitive to the public’s desires for a cleaner environment. They’ve heard employees’ pleas for a safer workplace.
Oil and gas companies need ways to identify safety threats and assess risks to assets and people. They’re seeking ways to mitigate exposure, improve their ability to comply with ever-more-complex regulations and overlapping agencies and limit the potentially negative consequences of fines, sanctions and penalties.
How a Digital or Interactive Work Instructions Solution Can Help
A mobile interactive or digital work instructions application offers oil and gas companies many advantages. The solution revolves around a simple concept: When new hires or less-experienced frontline employees are assigned work orders, they can digitally collaborate from the job site in real time with a veteran counterpart via smartphones, smartglasses or smartwatches.
The more seasoned employee does not have to accompany the frontline worker. He, or she, can be anywhere - in a nearby office or shop, at another unit, or across the world. The two connect via a secure teleconference. During this teleconference, the veteran can “see” what the onsite worker is looking at, answer questions and offer verbal, step-by-step instructions or share documents, photos and videos that can explain proper procedures.
Digital or interactive work instructions enable the real-time sharing of knowledge and boost frontline worker productivity and job satisfaction. They reduce costly errors and reworks, and increase job safety. It lets oil and gas maintenance managers upskill their team, giving greater workforce agility, flexibility and capability.
Learn More about Digital Work Instructions
Innovapptive, a connected worker platform provider, offers a digital work instructions solution that enables oil and gas companies to overcome the problems like those described above. This solution utilizes a prepackaged library of more than 150 digital work instructions, SOPs (standard operating procedures) and digital forms. These forms can be quickly and easily customized and configured to meet specific user needs as part of the company’s RACE™ Dynamic Forms application. To schedule a free demo, call 1-844-464-6668 or click here.
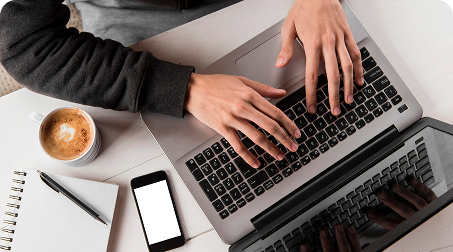
See It In Action
Schedule a personalized demo to see how our solutions can help your business thrive.
- 20-08-2025
Building the future of Industrial Operations with Innovapptive and AWS
Most manufacturers have already gone digital. Yet business outcomes haven’t moved in step. Many...
- 22-04-2025
The $3.6B Unlock: Solving the Chemical Industry’s Labor Crisis and EBITDA Pressure in One Move
“Constraints don’t slow innovation—they force it.”
- 21-04-2025
Chemical Industry's Margin Erosion: A Wake-Up Call for Operational Efficiency Amid China's Oversupply
The global chemical industry is facing mounting challenges, with revenue declines and shrinking...