5 Warehouse Best Practices to Mitigate COVID-19 Risks & Workplace Safety

The current COVID-19 pandemic has highlighted the importance of supply chains in our everyday lives in a dramatic way. Under normal circumstances when we go to the supermarket the shelves are stacked high to meet our desire for an ever-increasing range of different products and pack sizes.
In recent weeks, panic buying has overwhelmed the retail supply chain, leading to empty shelves and fear that those who really need food will be left without. Critical pharmaceuticals and medical products like paracetamols (a pain reliever), ventilators and personal protective equipment (PPE) required to treat the sick have also been unavailable. In many cases, the supply chain players - retailers, manufacturers, health care providers and governments - have stated there is enough inventory in the supply chain, it’s just not in the right place.
How to overcome these COVID-19 challenges to ensure efficient warehouse management and workplace safety?
There are five best practices to boost warehouse throughput. They are:
- Warehouse layout optimization
- Cross-docking
- Workload smoothing
- Cycle counting
- Mobile technology adoption
1. Warehouse layout
There are lots of opportunities to optimize operational efficiency by embracing warehouse layout best practices. One of the most important warehouse design principles is to minimize travel distance in the warehouse for both people and machinery to maximize productivity and safety.
Goods picking is a labor-intensive process and typically accounts for more than 50 percent of labor costs. Avoiding congestion in the warehouse minimizes travel time and distance, thereby increasing productivity. A simple process called Frequency Zoning can achieve this. In this process, the most frequently picked products are placed in the most accessible part of the warehouse.
Warehouse managers should focus on maximizing warehouse space utilization. This will provide enough space for warehouse staff to efficiently execute processes including order picking, packing, delivery, and goods receipt. This will also reduce errors and positively impact all other business processes. Managers should also ensure clear marking of bin locations, warehouse zones and clear directions around the site for drivers and visitors to improve warehouse throughput.
2. Cross-docking
Cross-docking is a warehouse best practice to improve warehouse throughput. This practice eliminates product putaway from regular warehouse operations by providing customer order data even before the product arrival. When the inbound products arrive, they are moved directly to the goods dispatch bay based on the order information available.
Though cross-docking has been used extensively in the retail supply chain, its adoption in other sectors is considerably low. Cross-docking provides the opportunity to boost warehouse throughput but requires careful coordination of inbound and outbound processes.
It’s worth assessing the potential for cross-docking in the following circumstances:
- Customer orders in full-pallet quantities (no case picking required)
- Limited warehouse space for storage
- Short shelf-life product
- Just-in-time deliveries, e.g. automotive parts
- e-Commerce transshipment depots
Made-to-Order products - Non-stocked items (not stored in the warehouse)
3. Workload smoothing
Warehouse operations are faced with steep peaks and troughs throughout a week. For example, Monday and Tuesday are busier as retailers order products to replenish the empty shelves, whereas towards the weekend the warehouse is quieter.
Workload smoothing ensures an even spread of work across each day of the week. The principle of smoothing warehouse operations and resource requirements applies to other warehouse activities, too. For example, in the goods receipt, you don’t want all inbound deliveries arriving on Wednesday morning, so the warehouse should adopt a booking system which allocates days and time windows to suppliers. Similarly, with warehouse resources, you don’t want all your forklift trucks going in for a major service on the same day and all your warehouse staff going on leave in the same week.
While some elements of workload smoothing will be under the control of the warehouse manager, e.g. annual leave, other elements require collaboration with suppliers and customers. For example, you can work with buyers to confirm an agreed delivery day for each supplier and work with sales to ensure customer delivery days are evenly spread over the week.
Workload smoothing puts the Warehouse Manager in control and ensures warehouse throughput targets can be achieved. This warehouse best-practice principle requires close collaboration with suppliers and customers.
4. Cycle counting
Cycle counting involves the physical counting of a subset of all the products in the warehouse regularly. Physical counts are then compared with the systems inventory and accuracy calculated. Regular inventory counting means the cause of discrepancies can be properly investigated and corrected quickly. Cycle counting is a great way to improve warehouse inventory accuracy.
Poor inventory accuracy causes sub-optimal warehouse operations with an adverse impact on warehouse throughput. Cycle counting is a great way to drive up inventory accuracy and throughput in warehouses.
Key elements of an effective cycle count process include:
- Agree on a regular cycle count frequency by product. For example - Fast movers – count every week; Medium movers – count every month; Slow movers – count every six months.
- Develop a robust cycle count process; for example, blind counting (the counter should not be able to see the system’s inventory). Ensure clear segregation of duties to ensure counters cannot write-off inventory.
- Ensure that cycle counting becomes a regular daily activity – a key part of the job!
5. Mobile technology adoption
While automated warehouses used by companies such as Amazon grab the headlines, many companies are using technology in their warehouse that has changed little over the past 20 years. Companies have made large investments in their ERP systems to provide integrated business control, but operations like warehousing have often been neglected.
The ERP is used to provide control of product movement into and out of the warehouse but other processes including goods receipt, putaway, picking and cycle counting are running on paper. Even basic technologies like barcoding have not been widely adopted.
Paper-based processes are inherently inefficient, inaccurate and will greatly reduce your warehouse throughput. The good news for those companies stuck in a technology time warp is that help is at hand. A modern, mobile-first solution, Innovapptive’s mInventory is linked directly to the ERP system and eliminates paper from warehouses.
Innovapptive’s mInventory is built on the patented RACETM (Rapid Application Configuration Engine) platform, which integrates operational efficiency with occupational safety through Dynamic Forms. This highly-configurable, no-code solution enables mining companies to create COVID-19 preparedness checklists based on the guidelines of regulators like CDC and OSHA. These checklists enforce mining workers to follow standard operating procedures to prevent the spread of the coronavirus. Thus, mInventory enables warehouses to remain operational and productive at a time of potential worker shortages.
Watch an online demonstration of mInventory in action by clicking this link. This demonstration showcases mInventory’s features and illustrates its benefits. To learn more about how Innovapptive’s mInventory can help your company increase its warehouse productivity and enhance employee safety during the COVID-19 pandemic, call 888-464-6668. Our experts are standing by to answer your questions, listen to your needs and to configure a solution to overcome your warehouse challenges.
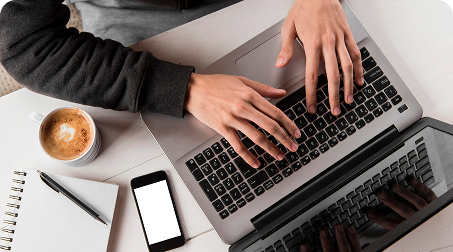
See It In Action
Schedule a personalized demo to see how our solutions can help your business thrive.
- 22-04-2025
The $3.6B Unlock: Solving the Chemical Industry’s Labor Crisis and EBITDA Pressure in One Move
“Constraints don’t slow innovation—they force it.”
- 21-04-2025
Chemical Industry's Margin Erosion: A Wake-Up Call for Operational Efficiency Amid China's Oversupply
The global chemical industry is facing mounting challenges, with revenue declines and shrinking...
- 21-04-2025
Why Wrench Time Isn’t Improving: The Hidden Costs of Traditional Maintenance Scheduling
For years, industrial leaders have relied on a common but flawed assumption: "Better planning and...