5 Ways Mobile Technology Can Streamline Warehouse Management
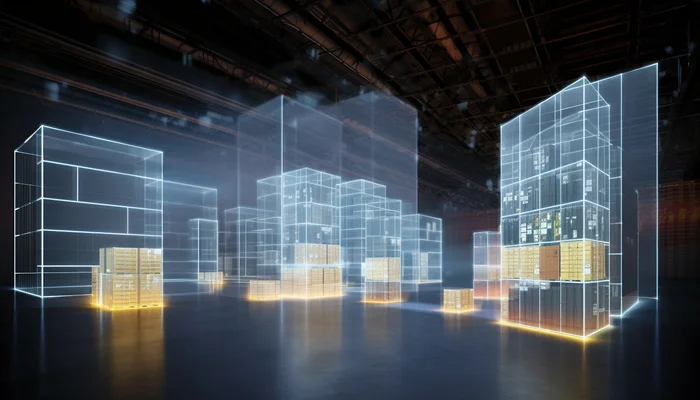
One of the most important warehouse design principles is to minimize movement of people and equipment. Unnecessary movement adds time to warehouse activities like product putaway and order picking, reducing productivity and increasing costs. Currently, many companies are struggling to staff warehouses, which puts an even greater focus on squeezing every incremental improvement from operations.
The diagram below shows five great ways to reduce warehouse movement and drive improvements in warehouse productivity.
Each one of the warehouse improvement opportunities is described in more detail below:
Paperless Warehousing
Many companies operating warehouses still depend on inefficient paper-based processes for goods receipt, order picking, inventory counting, and other activities with staff needing to return to the office to process transactions on a desktop. With a modern mobile solution, all system transactions are captured in real time at the point of the physical work. Additionally, a mobile device allows for barcode scanning of labels and documents for accurate data capture. Any paperwork that arrives with inbound deliveries, such as packing lists and certificates, can be scanned using the mobile device and uploaded into the ERP system for easy retrieval. The opportunity to move to complete paperless warehousing is now a reality.
Frequency Zoning
Based on the Pareto Principle - 20% of product lines in a warehouse will represent approximately 80% of the throughput. This simple rule determines the layout of products in the warehouse, with careful consideration given to the 20% of products often referred to as the "fast movers." These fast-moving products should be located in the most accessible parts of the warehouse, for example, in-ground floor racking locations and nearest to the dispatch bay. When it comes to fast-moving raw materials, such as packaging material, it often makes sense to locate them adjacent to the production lines to facilitate rapid replenishment.
Cross Docking
After completing goods receipt, the standard process in most warehouses is to move products into a bin location in the warehouse - product putaway. Subsequently, the product will be picked against a customer or work order. However, what if the material could be moved directly from the goods receipt bay to the dispatch bay in response to an order? This would cut out product putaway and picking, reducing warehouse movement, and increasing productivity. The process of moving products directly from goods receipt to the dispatch bay is known as cross docking. Cross docking requires accurate scheduling of inbound product flows with outbound orders. Once the cross-docking process is running, it will drive real benefits in reduced product handling, damages, and warehouse costs.
Multi-Order Picking
Picking small customer orders can be inefficient with operators needing to traverse the whole warehouse for each separate order. Small orders can be summarized into a single pick list (batch picking), with the operator presenting all required information on the mobile device. The operator only needs to traverse the warehouse once for all the small orders, reducing movement and saving time. A secondary sort into individual customer orders is completed on the dispatch bay. As a rule of thumb, a small order would be any single order that would not fill the picker’s pallet on one circuit of the warehouse. For example, if a full-picked pallet typically holds 30 cases, then small orders for five cases or less might be suitable for batch picking.
Task Interleaving
The forklift truck is the workhorse of the warehouse and it’s very inefficient to have them running around empty. In many warehouses, it's typical to dedicate staff to one activity, e.g., product putaway or picking. Task interleaving combines different warehouse activities to maximize the utilization of materials handling equipment and people. For example, the forklift driver is directed to putaway a pallet of finished products from production into a bin and then to pick a pallet for a customer order from a nearby bin location. Warehouse management systems can be used to optimize task interleaving across all warehouse activities, reducing the movement of materials handling equipment and increasing productivity.
Companies need to rise to the challenge of increasing warehouse complexity, including SKU proliferation, shorter delivery lead times, and staff shortages. The five practical methods described here will minimize movement and provide a very effective way to increase warehouse productivity.
To learn more about mInventory, schedule a free demo today or watch a video here.
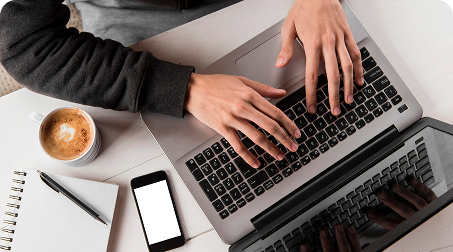
See It In Action
Schedule a personalized demo to see how our solutions can help your business thrive.
- 20-08-2025
Building the future of Industrial Operations with Innovapptive and AWS
Most manufacturers have already gone digital. Yet business outcomes haven’t moved in step. Many...
- 22-04-2025
The $3.6B Unlock: Solving the Chemical Industry’s Labor Crisis and EBITDA Pressure in One Move
“Constraints don’t slow innovation—they force it.”
- 21-04-2025
Chemical Industry's Margin Erosion: A Wake-Up Call for Operational Efficiency Amid China's Oversupply
The global chemical industry is facing mounting challenges, with revenue declines and shrinking...