The Power of Proactive: A Guide to Preventive Maintenance for Industrial Enterprises
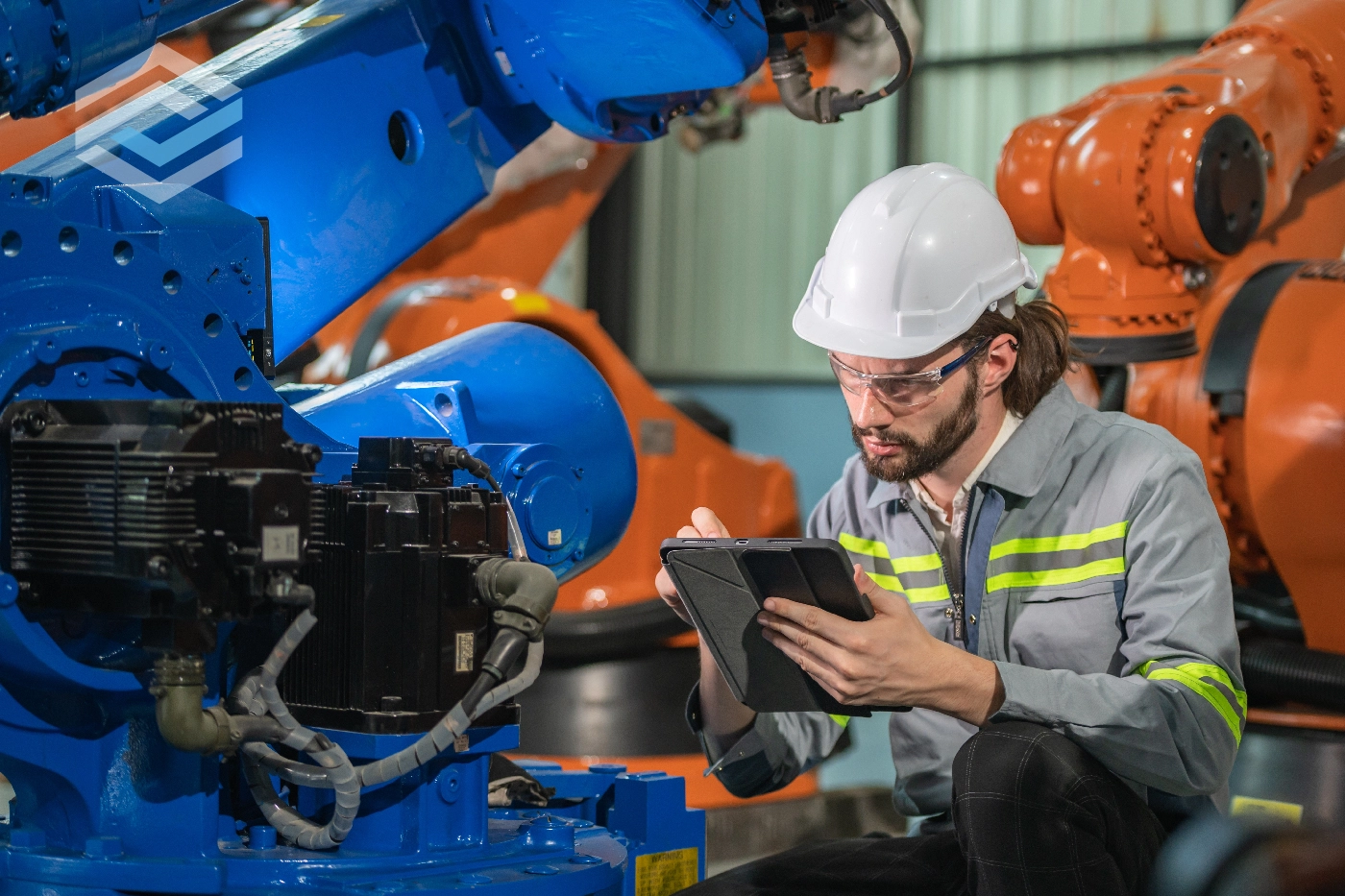
Imagine a production line humming smoothly, meeting deadlines, and exceeding output goals. This ideal scenario hinges on one crucial factor: the reliable operation of your equipment. But what happens when a critical machine fails, bringing production to a screeching halt? This is the unwelcome reality of reactive maintenance – waiting for equipment breakdown before addressing issues.
There's a smarter way. Preventive maintenance is a proactive approach that safeguards your industrial assets, preventing breakdowns and ensuring optimal performance. This ebook dives deep into the world of preventive maintenance, exploring its different types, the advantages it offers, and how to choose the right plan for your large-scale enterprise. We'll also introduce Innovapptive, a connected worker platform designed to streamline your preventive maintenance program and empower your workforce.
Understanding Preventive Maintenance
Preventive maintenance is the systematic care of equipment, machinery, and facilities within your industrial environment. Its core principle is to prevent equipment failures before they occur, minimizing downtime and maximizing productivity. This strategy involves:
- Routine inspections
- Lubrication
- Adjustments
- Part replacements
- Maintenance tasks based on a predetermined schedule or real-time data analysis
Think of it as taking your car for regular oil changes and tune-ups. By addressing potential problems proactively, you prevent them from escalating into major issues that could strand you on the side of the road.
Preventive vs. Reactive Maintenance: A Clear Distinction
The difference between preventive and reactive maintenance boils down to a fundamental shift in approach. Here's a breakdown of their key characteristics:
Preventive Maintenance |
Reactive Maintenance |
|
Impact on Operations |
Minimizes disruptions, ensures smooth running |
Causes delays, disrupts production |
Impact on Costs |
Reduces overall maintenance costs |
Leads to higher repair and replacement costs |
Impact on Equipment |
Extends lifespan, avoids premature failure |
Increases wear and tear, shortens lifespan |
Impact on Safety |
Identifies and addresses hazards proactively |
Risks accidents due to unexpected equipment failure |
The cost savings associated with preventive maintenance are substantial. Studies by industry leaders suggest that companies can achieve a significant reduction in maintenance costs (around 25%) and a substantial increase in equipment lifespan (up to 30%) by implementing a well-designed preventive maintenance program.
The Compelling Advantages of Preventive Maintenance
Beyond cost savings, preventive maintenance offers a multitude of benefits for your industrial enterprise:
1. Enhanced Safety:
By identifying and addressing potential hazards before they cause accidents, preventive maintenance fosters a safer work environment for your employees.
2. Boosted Productivity
Reduced downtime due to equipment failures translates directly to increased productivity and higher output for your operations.
3. Extended Equipment Lifespan
Regular maintenance ensures your equipment operates for a longer period, delaying the need for costly replacements.
4. Improved Efficiency
Well-maintained equipment operates at peak efficiency, leading to lower energy consumption and better overall performance.
5. Optimized Resource Allocation
By anticipating maintenance needs, you can allocate resources more effectively, avoiding scrambling to address unexpected breakdowns.
Preventive Maintenance in Action: Practical Examples
Preventive maintenance can be applied to a wide range of assets within your industrial facility. Here are some common examples:
- Manufacturing Equipment - Regular inspections and lubrication of production line machinery can prevent costly breakdowns and production delays.
- Facilities - Scheduled maintenance of HVAC systems ensures optimal energy efficiency and prevents expensive repairs.
- Vehicles - Regular oil changes, tire rotations, and inspections keep your company vehicles running smoothly and safely.
- Software Systems - Updating software and running regular system checks can prevent security vulnerabilities and ensure smooth operation.
Unveiling the Different Types of Preventive Maintenance
There's no one-size-fits-all approach to preventive maintenance. Specific strategies cater to equipment types and operational needs within various industries. Here's a breakdown of the most common preventive maintenance plans, equipping you with the right tools for the job:
1. Time-Based Maintenance: The Clockwork Caretaker
This approach is the quintessential "check-up" of the preventive maintenance world. Tasks are scheduled at predetermined intervals, regardless of equipment usage. Think of it like a routine well inspection in the oil & gas industry or regularly replacing filters in a chemical processing plant. It's ideal for equipment with predictable wear and tear patterns, such as:
- Chemical Processing Plants:
-
- Distillation Columns: Replacing packing material at defined intervals ensures efficient separation of chemical components.
- Safety Relief Valves: Periodic testing verifies proper operation and prevents safety hazards.
Advantages: Simple to implement, requires minimal upfront investment in data collection infrastructure.
Disadvantages: This may lead to unnecessary maintenance for infrequently used equipment. Doesn't account for real-time equipment health.
2. Condition-Based Maintenance: The Proactive Pathfinder
This method leverages the power of sensors and data analysis. Sensors embedded in equipment continuously monitor key parameters like vibration, temperature, or pressure. Advanced analytics software interprets this data, allowing for maintenance to be scheduled only when necessary. It's ideal for critical equipment where early detection of problems is crucial, such as:
- Manufacturing:
-
- Robots: Sensors can track robot arm movements and identify potential issues with accuracy and repeatability.
-
- Injection Molding Machines: Monitoring pressure and temperature during molding cycles can predict potential part defects and prevent production waste.
Advantages: Minimizes unnecessary maintenance, optimizes resource allocation, and identifies potential issues before they become major problems.
Disadvantages: Requires upfront investment in sensors and data analysis software. May not be suitable for all equipment types or older equipment not designed for sensor integration.
3. Usage-Based Maintenance: The Mileage Minder
This plan bases maintenance on equipment usage data, such as operating hours, number of cycles completed, or volume of material processed. By tracking usage metrics, maintenance can be tailored to the specific workload demands placed on the equipment. It's well-suited for equipment that experiences wear and tear based on usage, such as:
- Oil & Gas:
- Wellhead Pumps: Maintenance schedules are determined by operating hours, optimizing production, and preventing pump failures.
- Drilling Rigs: The number of meters drilled triggers maintenance tasks for drill bits and other critical components.
Advantages: Ensures maintenance aligns with actual equipment usage and avoids unnecessary downtime for infrequently used equipment.
Disadvantages: Requires accurate data collection on equipment usage. May not be suitable for equipment with unpredictable usage patterns.
4. Route-Based Maintenance: The Area Efficiency Expert
This technique prioritizes technician efficiency by grouping maintenance tasks for several pieces of equipment located in a specific area. Technicians follow a predefined route, completing multiple tasks in a single trip. It's ideal for geographically dispersed assets or large facilities with numerous pieces of equipment, such as:
- Mining:
- Open-Pit Mines: Technicians can perform maintenance on haul trucks, shovels, and other equipment operating within a specific mining zone during a single route.
- Underground Mines: Route-based inspections can include ventilation checks, equipment maintenance, and safety audits within designated mining sections.
Advantages: Reduces travel time for technicians and improves overall maintenance efficiency, particularly for geographically dispersed assets or large facilities.
Disadvantages: May not be suitable for critical equipment requiring in-depth inspection or specialized skills.
By understanding these different types of preventive maintenance and their strengths within the context of oil & gas, chemical, mining, and manufacturing industries, you can create a customized preventive maintenance program that optimizes your operations. Remember, the most effective approach often combines elements of different plans for a truly comprehensive strategy.
Choosing the Right Preventive Maintenance Plan for Your Enterprise
The optimal preventive maintenance plan for your enterprise hinges on several key factors:
- Type of Equipment: Different equipment types have varying maintenance needs. A complex CNC machine will require a more elaborate plan than a simple drill press. Consider the complexity, failure potential, and criticality of each asset when devising your preventive maintenance strategy.
- Criticality of Equipment: Equipment essential for production requires a more robust preventive maintenance strategy. Prioritize maintenance on assets that can cause a complete shutdown if they fail. Analyze the impact of equipment downtime on your operations to determine criticality.
- Budgetary Constraints: Cost considerations play a role in choosing the most suitable maintenance plan. Balancing the cost of maintenance with the potential cost of equipment failure is crucial. Consider the cost-effectiveness of each PM approach based on your budget.
- Availability of Data: Condition-based maintenance relies on sensor data availability. If you don't have the infrastructure to collect and analyze equipment health data, this approach might not be feasible. Evaluate your current data collection capabilities before implementing a condition-based preventive maintenance plan.
Innovapptive: Your Connected Worker Platform for Streamlined Preventive Maintenance
In today's industrial landscape, leveraging a connected worker platform like Innovapptive can significantly enhance your preventive maintenance program. Innovapptive empowers you to:
- Centralize and Manage Maintenance Tasks: Create digital work orders, assign tasks to technicians based on skillsets and location, and track progress in real time. This streamlines communication and ensures accountability.
- Empower Your Workforce: Equip technicians with mobile tools to access work orders, view maintenance procedures, and update task statuses on the go. This improves efficiency and reduces errors.
- Leverage Data for Informed Decisions: Integrate sensor data with your PM program to enable condition-based maintenance. Gain valuable insights into equipment health and optimize maintenance schedules.
- Improve Communication and Collaboration: Foster seamless communication between technicians, maintenance managers, and other stakeholders through a centralized platform. This ensures everyone is on the same page.
Key Benefits of Innovapptive's Preventive Maintenance Solution:
- Reduced Downtime: Minimize equipment failures and disruptions with proactive maintenance.
- Lower Maintenance Costs: Avoid expensive repairs and replacements through preventative measures.
- Enhanced Equipment Lifespan: Extend the lifespan of your valuable equipment and maximize your return on investment.
- Improved Safety: Create a safer work environment by addressing potential hazards before they cause accidents.
- Increased Productivity: Boost overall productivity by minimizing downtime and ensuring smooth operations.
Take Control of Your Maintenance Strategy Today!
Innovapptive is your partner in building a strong preventive maintenance program. With our connected worker platform and your proactive strategy, you can increase efficiency, reduce costs, and improve safety.
Schedule a free demo today and discover how Innovapptive can help you streamline your preventive maintenance program!
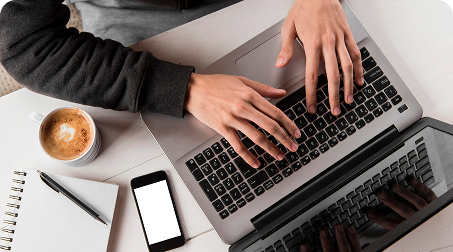
See It In Action
Schedule a personalized demo to see how our solutions can help your business thrive.
- 20-08-2025
Building the future of Industrial Operations with Innovapptive and AWS
Most manufacturers have already gone digital. Yet business outcomes haven’t moved in step. Many...
- 22-04-2025
The $3.6B Unlock: Solving the Chemical Industry’s Labor Crisis and EBITDA Pressure in One Move
“Constraints don’t slow innovation—they force it.”
- 21-04-2025
Chemical Industry's Margin Erosion: A Wake-Up Call for Operational Efficiency Amid China's Oversupply
The global chemical industry is facing mounting challenges, with revenue declines and shrinking...