Predictive Maintenance or Preventive Maintenance: Which is Your Strategy?
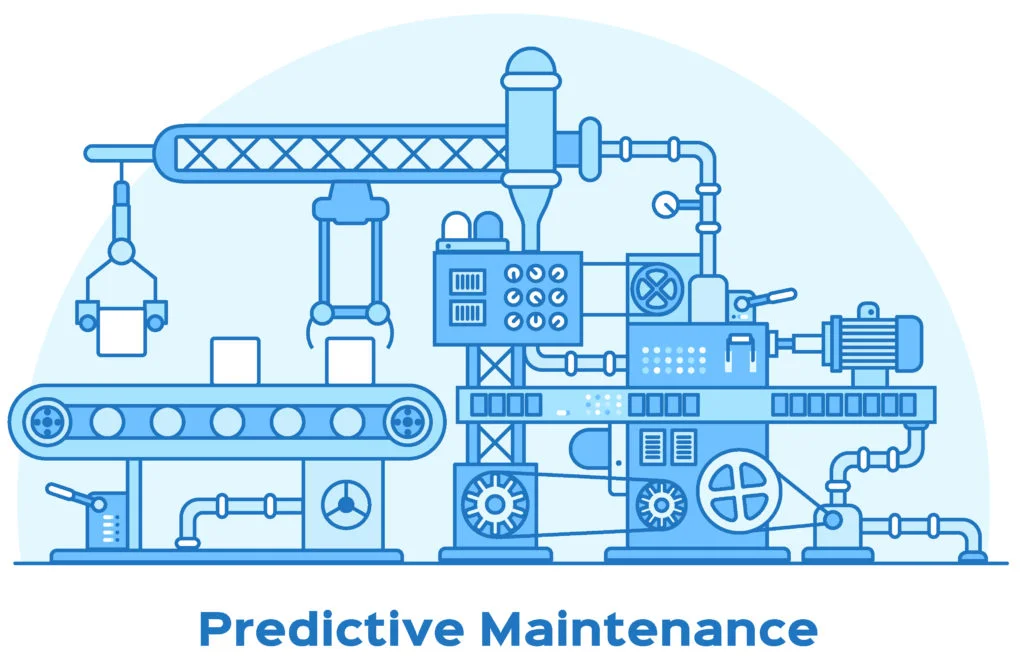
The Maintenance Dilemma: Balancing Proactivity with Efficiency
Imagine this: your production line grinds to a halt. A crucial piece of equipment has unexpectedly failed, costing you valuable time, resources, and potentially, dissatisfied customers. This scenario, unfortunately, is a familiar one for many organizations across various industries, highlighting the critical yet challenging task of maintenance.
The Two Pillars of Maintenance: Traditionally, organizations have relied on two primary approaches to equipment maintenance: preventive maintenance and predictive maintenance. While both aim to prevent unplanned downtime and ensure the smooth operation of equipment, they differ in their philosophy and execution.
Preventive Maintenance: This time-based or meter-count driven approach involves performing maintenance tasks at predetermined intervals, regardless of the equipment's actual condition. It's like changing your car's oil every 5,000 miles, even if it seems to be running perfectly.
Predictive Maintenance: This proactive approach utilizes data and advanced analytics to predict potential equipment failures before they occur. Imagine having sensors that monitor your car's engine health and alert you before a breakdown, allowing you to address the issue preemptively.
In today's mobile-first world, technology plays a crucial role in optimizing both preventive and predictive maintenance strategies. Mobile solutions provide a convenient and versatile platform for managing maintenance tasks, empowering a data-driven and efficient approach.
Understanding Preventive Maintenance
Preventive maintenance, a traditional and widely used approach, focuses on scheduled maintenance tasks performed at predetermined intervals, regardless of the equipment's actual condition. These intervals are typically based on:
- Manufacturer recommendations: Equipment manufacturers often provide recommended service intervals for routine maintenance tasks like oil changes, filter replacements, and component inspections.
- Industry best practices: Established industry standards can provide guidance on appropriate maintenance frequencies for specific equipment types.
- Historical data: Analyzing past maintenance records can help identify recurring issues and inform future scheduling strategies.
Benefits of Preventive Maintenance:
- Cost-effectiveness: Regularly scheduled maintenance can help prevent costly equipment failures and repairs, potentially saving money in the long run.
- Reduced downtime: By addressing minor issues before they escalate, you can prevent unplanned downtime and maintain smooth operations.
- Minimized breakdowns: Proactive maintenance helps ensure equipment operates within safe and efficient parameters, minimizing the risk of unexpected breakdowns.
- Improved safety: Regular maintenance helps identify potential safety hazards before they can cause accidents or injuries.
A study by Uptime Engineering found that preventive maintenance can significantly reduce maintenance costs, with an average decrease of 23%. Additionally, the Society for Maintenance & Reliability Professionals (SMRP) reports that organizations implementing effective preventive maintenance programs can experience a 15% to 30% reduction in unplanned downtime. For example, a manufacturing company implements a preventive maintenance program for its production line machinery. The program includes regular lubrication, component inspections, and filter replacements based on manufacturer recommendations. This proactive approach helps prevent unexpected equipment failures, ensuring smooth production and on-time delivery of products.
Limitations of Preventive Maintenance:
- Over-maintenance: Scheduling maintenance tasks too frequently can be wasteful and unnecessary, increasing costs and reducing production uptime.
- Under-maintenance: Conversely, extending maintenance intervals beyond recommended guidelines can increase the risk of equipment failures and related costs.
- Limited focus on actual equipment condition: This approach doesn't consider the equipment's actual operational state, potentially leading to unnecessary maintenance tasks on healthy machinery.
Preventive maintenance, while a well-established approach, offers advantages in cost-control, mitigating downtime, and ensuring equipment reliability. However, it's crucial to avoid over-maintenance or under-maintenance and find the optimal balance based on your specific context and equipment needs.
The next chapter will explore how mobile technology can be leveraged to optimize and integrate both preventive and predictive maintenance strategies for a comprehensive maintenance approach.
Understanding Predictive Maintenance
Predictive maintenance moves beyond the "fix it when it breaks" mentality and instead embraces proactive problem-solving. It relies on continuous monitoring of equipment health through various techniques, such as:
- Sensor data collection: Sensors embedded within equipment collect real-time data on vibration, temperature, and other critical parameters.
- Condition monitoring: Analyzing collected data allows for identifying anomalies and potential issues before they escalate into full-blown failures.
- Advanced analytics: Machine learning algorithms analyze vast amount of data to predict equipment failures and suggest optimal maintenance schedules.
Unlike preventive maintenance, which focuses on scheduled interventions, predictive maintenance allows you to:
- Address potential problems before they occur: This minimizes unplanned downtime and associated costs, ensuring smoother production processes.
- Optimize maintenance resources: By focusing on equipment requiring attention, you can avoid unnecessary preventive tasks and utilize resources more effectively.
- Extend equipment lifespan: Proactively addressing potential issues helps prevent further damage and prolongs the lifespan of your equipment.
Advantages of Predictive Maintenance:
- Increased reliability: Proactive maintenance reduces the risk of unexpected equipment failures, leading to more reliable and consistent operations.
- Reduced downtime: By addressing issues early, you minimize unplanned downtime, resulting in increased productivity and efficiency.
- Extended equipment lifespan: By identifying and addressing issues before they escalate, you can prevent premature equipment wear and tear, extending its lifespan and maximizing its return on investment.
- Reduced maintenance costs: By focusing on critical maintenance needs and avoiding unnecessary preventive tasks, you can optimize your maintenance budget.
Effectiveness in Action: A study by McKinsey & Company found that predictive maintenance can reduce unplanned downtime by 30% to 50% in various industries. Additionally, a report by ARC Advisory Group states that organizations can expect a return on investment (ROI) of 5:1 to 10:1 by implementing predictive maintenance strategies. For instance, a power plant utilizes predictive maintenance software to monitor the health of its turbines. By analyzing sensor data, the system identifies a developing issue in a critical bearing. The plant schedules a targeted maintenance intervention, replacing the bearing before it fails and avoiding a potential power outage that could impact thousands of customers.
Predictive maintenance, while requiring an initial investment in technology and expertise, offers significant benefits for organizations seeking to enhance operational efficiency, optimize resource utilization, and maximize return on investment.
The Critical Role of Mobile Maintenance Solutions
In today's data-driven world, mobile technology plays a critical role in optimizing both preventive and predictive maintenance strategies. By leveraging mobile solutions, product managers and maintenance personnel can:
- Access real-time data and insights: Equip workers with mobile apps and devices that provide immediate access to critical information like equipment status, maintenance schedules, and historical data, enabling them to make informed decisions at the point of work.
- Improve communication and collaboration: Facilitate seamless communication and collaboration between maintenance personnel, supervisors, and engineers through mobile platforms. This allows for faster problem-solving, efficient task delegation, and improved knowledge sharing.
- Enhance data collection and analysis: Utilize mobile apps for real-time data collection through features like image capture, audio recording, and voice notes. This data can be seamlessly fed into analytical tools for deeper insights and informed decision-making.
- Streamline workflows and improve efficiency: Mobile solutions can automate routine tasks like work order generation, preventive maintenance checklists, and reporting, freeing up valuable time for technicians to focus on complex issues.
Innovapptive’s Mobile Plant Maintenance Solution offers a user-friendly and intuitive interface accessible on various mobile devices. Our solution allows remote access to key functionalities, empowering maintenance teams to:
- Monitor equipment health: View real-time sensor data, identify potential issues, and schedule preventive maintenance tasks.
- Manage work orders: Create, assign, and track work orders for both preventive and corrective maintenance activities.
- Access knowledge base: Utilize offline access to maintenance procedures, troubleshooting guides, and equipment manuals.
- Capture and share information: Use photo and video capture features to document issues, share findings, and collaborate with colleagues.
Quantifying Value with Maintenance Strategies
While cost reduction is a significant benefit of optimized maintenance strategies, it's crucial to consider a holistic approach when evaluating the value they provide. Here are some key metrics to consider:
- Return on Investment (ROI): Calculate the financial benefits of implementing new strategies by comparing the cost savings against the initial investment. This includes considering reduced downtime, maintenance costs, and improved equipment lifespan.
- Increased uptime and throughput: Measure the impact on production line availability and throughput rate. Improved maintenance practices can significantly reduce unplanned downtime, leading to increased output and higher revenue potential.
- Improved equipment lifespan: Track the average lifespan of critical equipment before replacement. Implementing effective maintenance strategies can significantly extend equipment life, minimizing capital expenditure on new equipment purchases.
- Reduced safety incidents: Implement safety metrics like recordable incident rate (RIR) and lost workday rate (LWR) to assess the impact of improved maintenance practices on workplace safety. Proactive maintenance can significantly reduce the risk of equipment failures leading to accidents and injuries.
Cost Savings Illustrated: Through Preventive and Predictive Approaches:
Let's consider a scenario. A manufacturing plant experiences an average of 10 unplanned downtime events per year, each lasting 4 hours and costing $10,000 in lost production.
Preventive Maintenance Approach: By implementing preventive maintenance, the plant reduces unplanned downtime by 50%, saving 5 events (5 events * 4 hours/event * $10,000/hour) = $200,000 annually.
Predictive Maintenance Approach: Predictive maintenance further reduces downtime by 30%, resulting in an additional 1.5 events saved (5 events * 30%) = 1.5 events. This translates to additional cost savings of 1.5 events * 4 hours/event * $10,000/hour = $60,000 annually.
This simplified example demonstrates the potential cost savings achievable through both preventive and predictive maintenance strategies. Quantifying the value of your maintenance strategies goes beyond simply chasing cost reductions. By considering multifaceted metrics like uptime, equipment lifespan, and safety improvements, you can build a stronger case for investment and demonstrate the overall positive impact on your organization's performance.
Crafting an Effective Maintenance Strategy: From Planning to Execution
Developing a comprehensive maintenance strategy requires a structured approach and collaboration between various stakeholders. Here's a roadmap to guide you through the process:
- Define Your Goals and Objectives:
-
- Identify key performance indicators (KPIs) to track progress. These could include uptime, maintenance cost reduction, improved equipment lifespan, or specific safety metrics.
- Set realistic and measurable goals for each KPI, considering factors like industry benchmarks and historical data.
- Analyze Your Equipment and Needs:
-
- Conduct a thorough inventory of your equipment and gather information like age, criticality, maintenance history, and manufacturer recommendations.
- Identify potential failure points and prioritize equipment based on its impact on production and revenue.
- Evaluate Existing Practices:
-
- Assess the effectiveness of your current maintenance strategies. This includes both preventive and any existing predictive maintenance practices.
- Identify areas for improvement and potential gaps in your current approach.
- Choose the Optimal Strategy:
-
- Determine the appropriate combination of preventive and predictive maintenance strategies for each piece of equipment, considering factors like cost, feasibility, and potential benefits.
- Integrate technology solutions: Leverage mobile tools to automate tasks, improve data collection, and facilitate communication and collaboration among your maintenance team.
- Develop a Detailed Plan:
- Create a comprehensive maintenance plan outlining:
- Specific maintenance tasks: Clearly define the tasks required for both preventive and predictive maintenance for each equipment type.
- Scheduling and frequency: Determine the frequency of preventive tasks and define triggers for predictive interventions based on sensor data analysis.
- Resource allocation: Assign appropriate personnel and resources to each maintenance task based on skillsets and workload.
- Implement and Monitor:
-
- Effectively roll out the maintenance plan through training sessions and clear communication channels.
- Continuously monitor the performance of your strategy by tracking your KPIs and adjusting your plan based on collected data and feedback.
Developing a comprehensive maintenance strategy requires careful planning, collaboration, and leveraging the power of mobile technology. By following the outlined steps and assuming an active role in the process, product managers can ensure the successful implementation of a strategy that maximizes equipment uptime, minimizes costs, and ultimately contributes to a more efficient and productive organization.
Are You Ready To Unlock the Power of Smarter Maintenance?
At Innovapptive, we understand the unique challenges faced by organizations in optimizing their maintenance strategies. Our Mobile Plant Maintenance Solution is designed to empower your team with the tools and functionalities needed to implement a holistic approach, maximize uptime, and optimize costs.
By taking action today, you can unlock the significant potential of combined preventive and predictive maintenance strategies, powered by mobile technology, and position your organization for a future of increased efficiency, productivity, and sustainable success. Request a free demo today to let our experts analyze your specific needs and demonstrate how our solution can help you achieve your maintenance goals.
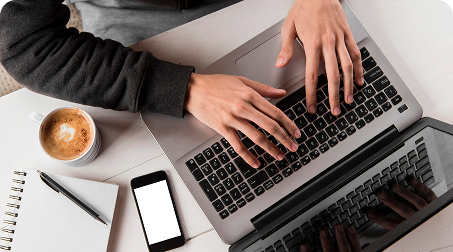
See It In Action
Schedule a personalized demo to see how our solutions can help your business thrive.
- 20-08-2025
Building the future of Industrial Operations with Innovapptive and AWS
Most manufacturers have already gone digital. Yet business outcomes haven’t moved in step. Many...
- 22-04-2025
The $3.6B Unlock: Solving the Chemical Industry’s Labor Crisis and EBITDA Pressure in One Move
“Constraints don’t slow innovation—they force it.”
- 21-04-2025
Chemical Industry's Margin Erosion: A Wake-Up Call for Operational Efficiency Amid China's Oversupply
The global chemical industry is facing mounting challenges, with revenue declines and shrinking...