Accurately Capturing Wrench Time Key to Lowering Plant Maintenance Costs
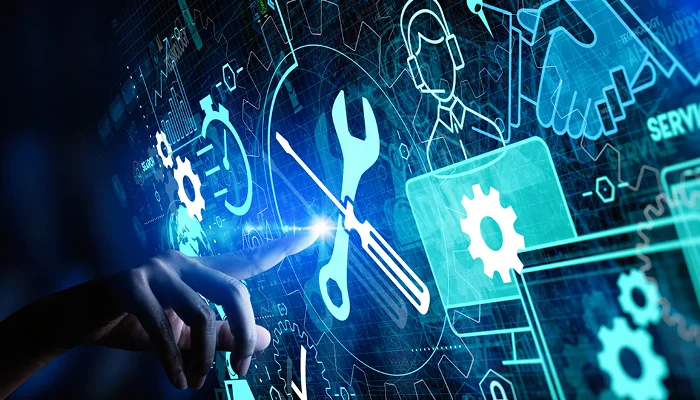
Plant maintenance productivity rates generally hover between 20% to 30%. That means that in a typical eight-hour day, the average technician spends only two to three hours turning a wrench.
Don’t worry… it’s not as if the technician is surfing social media or taking a nap on company time. Well, not as much as you might fear. Instead, the tech is stuck performing other non-productive tasks, such as traveling to and from the job site, awaiting instructions, getting tools and materials, etc.
However, you still have to pay for that non-productive time even though you receive little or no benefit from it.
The same goes for outside maintenance contractors. Half of all plants outsource at least 20% of their overall maintenance; 10% use a contractor to perform half or more of their maintenance activities, including repairs during planned and unplanned downtime incidents. A contractor will still hand you a bill for a full eight-hour day even though real work only occupied a quarter to a third of that time.
In part two of this three-blog series, we’ll examine if connected worker platforms and mobile plant maintenance solutions help asset-intensive industries break this cycle before it worsens.
Mobile Plant Maintenance Apps Offer a Solution
As a plant maintenance manager, you want to ensure you’re getting the most wrench turns you can get for each dollar spent. However, if your plant uses a paper-based maintenance data collection process, you likely don’t have an accurate way to track productivity or time other than what’s manually entered by the technician or submitted by the contractor. That results in a lot more questions than answers. Because of that, not only are labor resources inefficiently allocated, but money is wasted as well. These are resources and funds that could be better used somewhere else… if only you could track them.
Mobile plant maintenance apps can alleviate this knowledge shortfall and free you from entrapment in an information silo. Such apps utilize the flexibility and agility mobile devices – smartphones, tablets, smartwatches, etc. – offer.
Instead of techs tracking their time using paper forms and binders then manually uploading data into SAP PM or IBM Maximo, they can access a mobile plant maintenance app’s digital timekeeping feature via one of their devices. Time information is uploaded automatically into SAP PM or IBM Maximo. A manager or supervisor has immediate, real-time access to accurate, up-to-date about how every technician is spending his or her workday.
Benefits of a Mobile Plant Maintenance System’s Time Capture
A mobile plant maintenance solution with robust time capture capabilities gives managers and supervisors valuable information they can use to make their programs more efficient in terms of using labor resources and spending.
Greater maintenance efficiency can translate into serious cost savings. Process improvement boosts in-house productivity and wrench time, cuts wasted, non-productive activities and reduces the need for expensive outside contractors. For example, a highly efficient operation with 74% wrench time spends $100 million a year versus $400 million a year on inefficient maintenance workforce management and maintenance operations.
These savings can be added directly to the bottom line. C-Suite executives can reinvest this money into new equipment, bolster understaffed departments or ease profit margin pressures.
In part three of this series we’ll introduce a mobile plant maintenance system that can solve your maintenance inefficiencies and labor costs problems. If you haven’t yet read part one, be sure to visit Companies Confront Higher Downtime Costs; Can Mobile Plant Maintenance Offer a Solution?
Coming next: Tracking Wrench Time and Cutting Labor Costs with a Mobile Plant Maintenance Solution.
Want to Learn More?
Innovapptive, a connected worker solution pioneer, specializes in SAP- and IBM Maximo-compatible mobile plant maintenance systems that improve technician productivity, transform reactive processes and cut downtime costs. Schedule a free demo of a world-class connected worker platform or call 888-464-6668 to speak to our industry experts. They’ll be happy to answer your questions, help you calculate return on investments, identify opportunities for efficiencies and savings, and explain how mobile plant maintenance can benefit you.
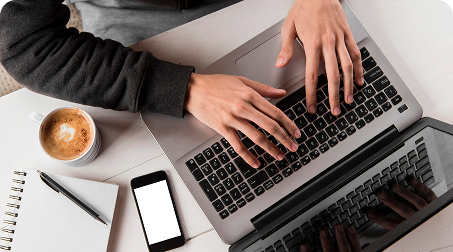
See It In Action
Schedule a personalized demo to see how our solutions can help your business thrive.
- 20-08-2025
Building the future of Industrial Operations with Innovapptive and AWS
Most manufacturers have already gone digital. Yet business outcomes haven’t moved in step. Many...
- 22-04-2025
The $3.6B Unlock: Solving the Chemical Industry’s Labor Crisis and EBITDA Pressure in One Move
“Constraints don’t slow innovation—they force it.”
- 21-04-2025
Chemical Industry's Margin Erosion: A Wake-Up Call for Operational Efficiency Amid China's Oversupply
The global chemical industry is facing mounting challenges, with revenue declines and shrinking...