How to Build an AI-Powered Maintenance Strategy in 5 Simple Steps

Key Takeaways
- An AI-powered plant maintenance solution automates work order generation, prioritizes tasks, and provides real-time updates, optimizing workflows and reducing downtime.
- It creates adaptive, step-by-step instructions, standardizes procedures, and prevents failures through predictive analytics.
- AI-powered tools like voice-to-text and automated forms improve accuracy and efficiency, streamlining data capture and documentation while reducing administrative burdens.
The Rise of AI-Powered Plant Maintenance
Forty years ago, Hollywood depicted Artificial Intelligence (AI) as a terrifying force in The Terminator, where AI took control of the world’s nuclear weapons to destroy humanity. Fast forward to 2024, and AI has become a powerful tool, especially in industrial plant maintenance, where its benefits far outweigh any fears. Industrial organizations are increasingly adopting AI-powered plant maintenance solutions to enhance their asset management programs and work order management. The primary reasons for this include:
- Predictive Maintenance: AI analyzes sensor data to detect potential issues early, reducing downtime and associated costs.
- Enhanced Decision-Making: AI processes vast amounts of data rapidly, providing insights for more effective maintenance strategies.
- Increased Efficiency: By automating routine tasks and optimizing schedules, AI frees up workers to handle more complex issues.
- Real-Time Fixed Assets Monitoring: Continuous AI monitoring prevents equipment failures by sending instant alerts.
- Cost Reduction: AI optimizes resource use, minimizes unexpected breakdowns, and extends equipment lifespan, leading to lower maintenance expenses.
An AI-powered plant maintenance strategy offers substantial benefits for industrial plants:
- Reducing Downtime: AI predicts equipment failures, enabling preemptive repairs and minimizing costly interruptions.
- Optimizing Schedules: AI customizes maintenance schedules based on real-time data, reducing unnecessary downtime and costs.
- Improving Resource Allocation: AI forecasts maintenance needs, optimizing the use of spare parts and labor, and lowering inventory costs.
- Extending Lifespan: AI detects early signs of wear, allowing proactive interventions that extend equipment life.
- Enhancing Safety and Compliance: Continuous AI monitoring ensures adherence to safety regulations, reducing accidents and fines.
Step 1: Leverage an AI-Powered Digital Assistant
AI streamlines work order management by automating and optimizing processes. It generates work orders by analyzing equipment data, ensuring timely maintenance, and preventing delays. AI prioritizes tasks based on urgency, reduces the risk of breakdowns, and provides real-time updates, allowing teams to adapt to changing conditions. It also optimizes resource allocation by matching personnel and parts to tasks, improving efficiency, and lowering costs.
Operational benefits of an AI assistant for work order management include:
- Automated Scheduling: AI optimizes maintenance schedules by automatically prioritizing and assigning tasks based on urgency and equipment condition.
- Efficient Parts Ordering: AI forecasts parts requirements and automates the ordering process, ensuring that necessary components are available when needed, reducing downtime.
- Resource Optimization: AI allocates the right personnel and tools to each task, improving efficiency and ensuring that maintenance is completed on time.
- Proactive Maintenance: AI predicts potential equipment failures and generates work orders preemptively, reducing unexpected breakdowns.
- Real-Time Fixed Assets Monitoring: AI provides continuous updates on work order status, allowing for real-time adjustments and better management of maintenance activities.
- Cost Reduction: By streamlining processes like scheduling, parts ordering, and resource allocation, AI reduces operational costs and minimizes waste.
Step 2: Implement AI-Generated Work Instructions
AI dynamically generates step-by-step work instructions by analyzing equipment data, maintenance history, and manufacturer guidelines. It uses natural language processing to interpret technical documents, breaking down complex information into clear, actionable steps. AI adapts instructions in real-time, considering factors like equipment state and tool availability, ensuring relevance and practicality. It continuously learns from past tasks and user feedback, refining instructions for improved accuracy and effectiveness.
AI-generated work instructions improve work and productivity consistency, reduce errors, and speed up maintenance by:
- Standardized Procedures: AI ensures consistency by providing uniform, step-by-step instructions across all maintenance tasks, reducing variability in execution.
- Error Reduction: Clear, precise instructions minimize the risk of human error, ensuring tasks are completed correctly the first time.
- Faster Task Completion: By breaking down complex tasks into easy-to-follow steps, AI accelerates maintenance processes, reducing downtime and boosting productivity.
- Real-Time Updates: AI adapts instructions in real-time based on current conditions, preventing delays and ensuring the most efficient approach is always used.
- Continuous Improvement: AI learns from past maintenance activities, refining instructions to improve future task performance, leading to ongoing productivity gains.
Step 3: Prioritize Risks with AI-Driven Insights
AI identifies high-risk maintenance needs in industrial plants by analyzing asset data through predictive analytics and pattern recognition. It forecasts potential failures by processing historical and real-time data and detecting anomalies like temperature spikes or vibrations. AI also conducts failure mode analysis, examining past equipment failures to assess similar risks in other assets. It assigns health scores, ranking assets by risk and urgency, enabling focused maintenance on critical areas.
AI empowers industrial plant maintenance teams to focus on mission-critical work by:
- Automating Routine Tasks: AI handles repetitive tasks like scheduling and data entry, freeing teams for more crucial issues.
- Predictive Maintenance: AI predicts equipment failures, allowing teams to prioritize high-impact maintenance and avoid costly downtime.
- Efficient Resource Allocation: AI optimizes resource use, deploying skilled workers to critical tasks.
- Real-Time Fixed Assets Monitoring: AI provides instant alerts on critical issues, enabling quick responses to high-priority situations.
- Data-Driven Decision Making: AI analyzes data to offer insights and recommendations, helping teams prioritize essential tasks effectively.
Step 4: Leverage Advanced Voice Transcription
AI-powered voice-to-text technology enables hands-free data capture in industrial plants, enhancing efficiency and accuracy. Technicians can verbally record observations and task completions in real time, allowing instant data entry without workflow interruptions. This boosts productivity by eliminating manual input and lets technicians focus on their tasks. The AI accurately transcribes spoken words, minimizing errors and correctly categorizing industry-specific terminology.
Adopting a hands-free voice-to-text solution in industrial plant maintenance offers several benefits:
- Faster Data Entry: Technicians can quickly capture maintenance details verbally, speeding up the documentation process and reducing time spent on manual data entry.
- Increased Work Continuity: Hands-free operation allows technicians to record data while working, minimizing disruptions and maintaining workflow continuity.
- Improved Accuracy: Voice-to-text reduces errors associated with manual entry, ensuring more reliable maintenance records and data consistency.
- Enhanced Safety: Technicians can focus on the task at hand without needing to stop for data entry, reducing the risk of accidents and improving overall safety.
- Reduced Paperwork: Automating data capture with voice-to-text significantly decreases the administrative burden, allowing for more streamlined and paperless operations.
- Real-Time Data Availability: Maintenance data is captured and processed instantly, providing immediate access to up-to-date information for better decision-making and planning.
Step 5: Automate Forms with a Gen-AI Form Builder
An AI-driven form builder for industrial plant maintenance automates and customizes documentation by analyzing maintenance needs and equipment data. It dynamically adjusts forms based on real-time inputs, keeping documentation relevant.
The system modifies templates to fit specific scenarios, saving time and ensuring consistency. Technicians can input data via voice, drop-downs, or manual entry, with forms updating automatically. AI also suggests additional fields based on context, ensuring comprehensive data capture.
An AI-driven form builder streamlines data capture and eliminates manual form creation by:
- Automated Form Generation: AI automatically creates maintenance forms based on specific tasks and equipment data, eliminating the need for manual design.
- Dynamic Field Population: It populates fields with relevant data in real-time, ensuring accurate information capture.
- Context-Aware Customization: AI tailors forms to specific scenarios, adapting to changes in equipment status or technician input.
- Reduced Human Error: Automation minimizes errors, leading to more reliable documentation.
- Time Efficiency: AI reduces time spent on form creation, allowing teams to focus on higher-value tasks.
- Instant Data Integration: Captured data is instantly integrated into systems, enhancing workflows and decision-making.
Let’s Recap
AI significantly enhances industrial plant maintenance in five key areas:
- Streamlined Work Order Management: AI automates work order creation, prioritizes tasks, and offers real-time updates, optimizing workflows and resource use.
- Dynamic Work Instructions: AI generates step-by-step instructions that adapt to real-time conditions, reducing errors and improving task consistency.
- High-Risk Maintenance Identification: AI identifies high-risk assets through predictive analytics, enabling focused maintenance and reduced downtime.
- Hands-Free Data Capture: AI-powered voice-to-text improves efficiency and safety by enabling verbal data entry.
- Automated Form Creation: AI dynamically generates and customizes forms, ensuring accurate data capture and real-time collaboration.
Sound intriguing? Innovapptive, a cutting-edge industrial digital transformation company and connected workforce platform provider, stands ready to assist your organization in moving to an AI-powered plant maintenance strategy. Watch our new digital work order management video to learn more.
FAQ
Q: What is an AI-Powered plant maintenances strategy?A: An AI-powered plant maintenance strategy leverages artificial intelligence to predict equipment failures, optimize maintenance schedules, and reduce downtime. This approach enhances efficiency, extends asset lifespan, and minimizes costs by using real-time data and predictive analytics.
Q: How does AI improve maintenance operations in industrial plants?
A: AI enables predictive maintenance, optimizes resources, automates tasks, and provides real-time monitoring, reducing downtime, lowering costs, and enhancing efficiency.
Q: How can an AI assistant streamline work order management?
A: An AI assistant automates work order generation, prioritizes tasks, provides real-time updates, and optimizes resource allocation, improving workflow efficiency.
Q: What are the benefits of AI-generated work instructions?
A: AI-generated work instructions standardize procedures, reduce errors, and adapt to real-time conditions, ensuring consistency and efficiency.
Q: How does AI help in identifying high-risk maintenance needs?
A: AI uses predictive analytics and condition monitoring to identify high-risk assets, allowing maintenance teams to focus on critical tasks.
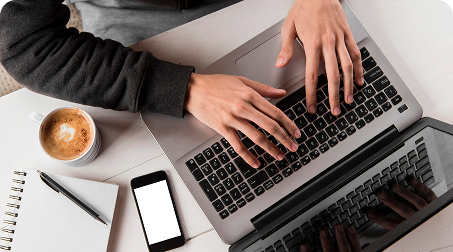
See It In Action
Schedule a personalized demo to see how our solutions can help your business thrive.
- 20-08-2025
Building the future of Industrial Operations with Innovapptive and AWS
Most manufacturers have already gone digital. Yet business outcomes haven’t moved in step. Many...
- 22-04-2025
The $3.6B Unlock: Solving the Chemical Industry’s Labor Crisis and EBITDA Pressure in One Move
“Constraints don’t slow innovation—they force it.”
- 21-04-2025
Chemical Industry's Margin Erosion: A Wake-Up Call for Operational Efficiency Amid China's Oversupply
The global chemical industry is facing mounting challenges, with revenue declines and shrinking...