A Connected Worker Solution for the Life Sciences Industry
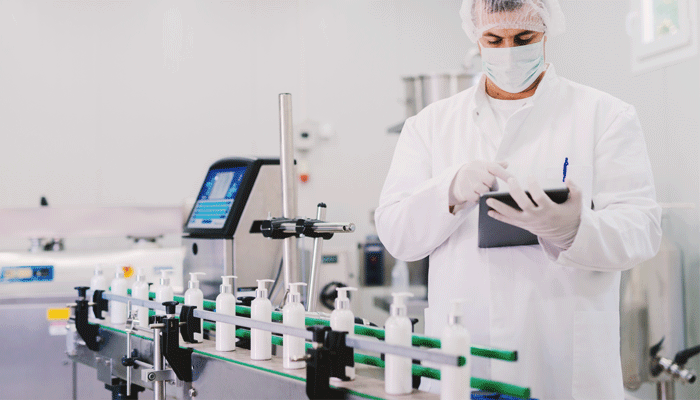
The COVID-19 health emergency is a double-edged sword for the life sciences industry, which is playing a vital role in fighting the pandemic. Manufacturers are struggling to balance production and occupational safety. In hindsight, the COVID-19 crisis has stressed on the importance of front-line worker safety and operational efficiency for labor-intensive industries like life sciences.
Exclusion of front-line operations from digital transformation makes Industry 4.0 incomplete despite a raft of automation. Enterprises have now started to recognize this gap. Industry 5.0 is about digital technologies and robots making humans work better and faster. It refers to the necessary interaction between people and machines. In the manufacturing world, robots usually perform monotonous work, such as welding and painting in car factories and loading and unloading heavy materials in warehouses.
Industry 5.0 offers immense opportunities to improve operational efficiencies, boost productivity, enhance product/service quality and ensure occupational safety in the life sciences industry. Enterprises need to start making front-line workers at the center and forefront of their operations by democratizing digital technologies to improve the working life of a front-line worker in the life sciences industry. Companies should consider implementing a Connected Worker strategy with a comprehensive platform that can rapidly empower the front-line worker to get the jobs done faster, better, cheaper and safer.
Challenges & opportunities in the life sciences industry
According to a research conducted by Deloitte in 2018 titled, “The Connected Worker - Charging Up the Business Services Workforce,” companies are seeing increasing margin pressures and talent challenges. The growing pressure is felt across all labor, asset-intensive industries. This pressure doesn’t just stem from the rising cost of people; these industries are facing increasing demand from customers to deliver higher value for a lower cost. Legacy systems and processes are downgrading operational efficiency of life sciences companies and weakening their resilience. This is where the Connected Worker approach comes into play. The key areas where a Connected Worker solution finds its use cases in the life sciences industry are as follows:
1. Front-line operations: Over the last 40+ years, life sciences companies focused on digitizing information of all aspects of their business operations - finance, sales, supply chain, inventory, procurement, production, planning, maintenance, etc., by implementing ERP systems such as SAP, Oracle, etc. However, these ERP systems were designed for the back office jobs that made a living on data entry into these systems of record.
Traditionally, back office personnel output the ERP data such as work orders or cycle count on paper. The front-line workers then collect the necessary field data on paper, and then the back office personnel input the captured data on paper, back into ERP. The ability for corporations to access information related to all areas of their business in one single system of record was a technology leap forward to drive process and data consolidation. However, the continued disconnect between the front-line worker and the back office remained a highly inefficient, linear, tedious and time consuming process. Front-line workers continued to operate in paper-based workflows or fragmented point solutions that solve few elements of them getting their jobs done faster, better, cheaper and safer.
Many software providers have recently mobilized these paper based processes on tablets and smartphone apps to capture and process the relevant data at the time of job completion. However, the motivation of these mobile solutions is once again for corporations to capture all data in one single system of record and does not focus its attention on improving the working life of a front-line worker to help him access the information they need, when they need it and how they need it - visual, guided, immersive or remote expert assistance with “hands-free” operations.
2. Regulatory compliance: Life sciences is a highly regulated industry. Regulations and regulatory compliance aren’t cheap. Nor is non-compliance. Failure to comply with regulations can cost a life science company hefty fines, sanctions or even jail time for company officials. Non-compliance can often also result in lawsuits from either governments or negatively impacted individuals. Companies are now taking regulatory compliance seriously. However, there are a host of regulations in the life sciences industry - including ISO regulations and EHS regulations on the local, state and federal levels. Staying in compliance with these many regulations can be an onerous, time-consuming task, especially in a paper-based process.
3. Supply chain operations: The global supply chain disruptions and rapidly changing market dynamics are a wakeup call for them to reflect on their inbound and outbound inventory management. Supply chains in the life sciences industry have vertical structures in which a huge amount of cash is tied up in a supply chain. Traditional paper-based inventory management processes aim to optimize inventory locally, typically in a single node of a complex supply chain. This duplicates risk factors at each node and multiplies issues through the entire supply chain. Life sciences companies should think beyond short-term gains to strengthen their resilience against COVID-like emergencies in future.
4. Asset management: The biggest challenge for life sciences companies is to ensure business continuity amid several uncertainties. On one hand, there’s a stark spike in demand for drugs like hydroxychloroquine and paracetamol, and medical equipment like PPEs, ventilators and COVID-19 test kits, etc. On the other hand, supply chain disruptions and mandatory social distancing norms are hindering production. In such scenarios, equipment reliability plays an important role in ensuring business continuity.
Connected Worker solutions for the life sciences industry
Life sciences companies are quickly realizing they need to make investments into a “Connected Worker” platform - a key aspect of industrial digital transformation. Several industries have already deployed digital technologies that connect front-line workers for better productivity, quality and safety. Margin pressures, aging workforce, and attracting and retaining the “digital native” front-line worker is becoming a daunting challenge for enterprise operations. The last mile needs of the front-line worker have been underserved in perpetuity and the “digital native” front-line workers needs a solution that tightly integrates with a system of record like SAP, combined with step by step, visual and guided work instructions that can be accessed and processed on mobile or smart glasses. This is now a necessity and not a nice to have to help enterprises close the last mile between the front-line worker and these large ERPs.
Life sciences is a non-IT-intensive industry that wants digital transformation to be a smooth road, even in the absence of large tech teams and a big budget. So, low-code/no-code platforms - known for their agility, simple cost structure and cross-platform mobility - have proven to be the right choice for life sciences companies. These platforms make application building highly accessible for non-programmers and enterprises with less engineering efforts.
Low-code/no-code platforms enable employees in life sciences companies, though they have no coding knowledge, to create quick solutions to match their business requirements. A maintenance manager can create inspection checklists for newly installed equipment in a matter of minutes and assign it to a technician in one tap. A regulatory compliance officer can create safety checklists and other forms as per quickly changing norms without any considerable delays. These all are possible with a no-code/low-code platform.
Innovapptive’s Connected Worker solutions for life sciences
To quickly understand what working with a no-code/low-code platform in a life science company will be like, see how Innovapptive’s RACETM Dynamic Forms makes its connected worker solutions, including mWorkOrder, mInventory and mAssetTag, flexible, agile and highly customizable. Below, you’ll see how the no-code platform helps enterprises embrace public health regulation guidelines, practice “social distancing” and reduce the risk of COVID-19 disease spread across workforce:
COVID-19 Work Order Execution and Job Safety Instructions – Derived from the CDC’s COVID-19 Preparedness Assessment Test, this checklist mandates technicians complete the coronavirus testing protocol before beginning any work order. This ensures workers don’t take unnecessary risks and remain compliant with health and safety procedures.
COVID-19 Site and Environment Risk Assessment – Conduct regular and thorough risk assessment exercises to determine your organization’s vulnerability to COVID-19. Rank risks by severity and likeliness of occurring, enabling decision makers to take prompt and appropriate action.
To learn more about Innovapptive’s connected worker platform and how it will help life sciences companies boost productivity and ensure safety and quality, visit www.innovapptive.com or call 888-464-6668.
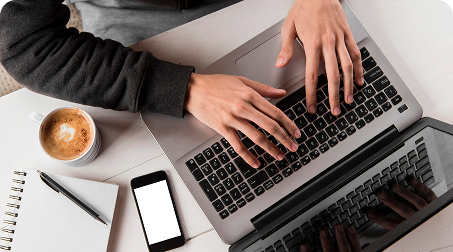
See It In Action
Schedule a personalized demo to see how our solutions can help your business thrive.
- 22-04-2025
The $3.6B Unlock: Solving the Chemical Industry’s Labor Crisis and EBITDA Pressure in One Move
“Constraints don’t slow innovation—they force it.”
- 21-04-2025
Chemical Industry's Margin Erosion: A Wake-Up Call for Operational Efficiency Amid China's Oversupply
The global chemical industry is facing mounting challenges, with revenue declines and shrinking...
- 21-04-2025
Why Wrench Time Isn’t Improving: The Hidden Costs of Traditional Maintenance Scheduling
For years, industrial leaders have relied on a common but flawed assumption: "Better planning and...