Connected Workers: How Utilities Can Drive Operational Efficiency with Industry 5.0
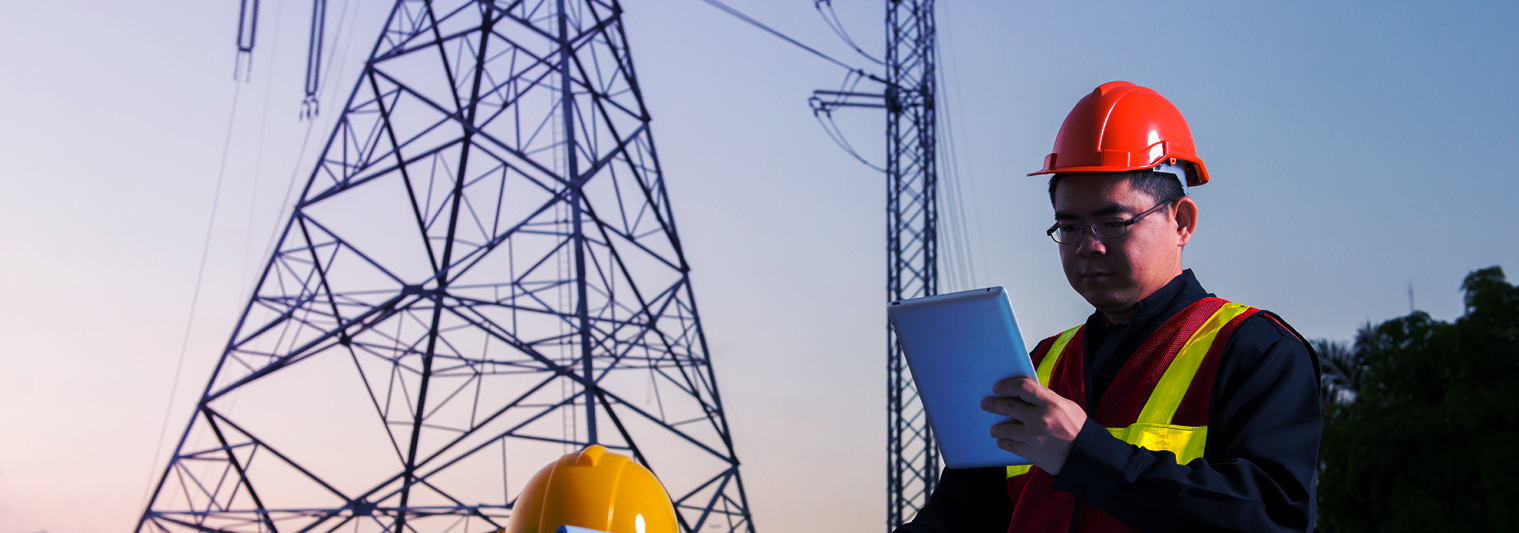
Industry 5.0: the fifth industrial revolution is key to the change in the way organizations work across all the industries. Industry 5.0 will bring humans back in front. It will connect people to the already interconnected devices, platforms, and processes in intuitive ways to help them perform optimally. Especially for the utility industry, it creates many opportunities to improve productivity, performance and achieve best in class operational efficiency. Utility companies face a range of powerful disruptions such as advancements in technology, shareholder expectations and demand of customers for shorter response times at a minimal cost. Digital technologies, such as AI, IoT, wearables, intelligent connected assets, machine learning , connected workers, are some of the ever-changing technologies available. Utilities are tapping into these new technologies to serve increasingly sophisticated customers and improve operational efficiencies.
Organizations in the utility industry use technologies, equipment, and a connected workforce that combine to deliver customers reliable and environmentally sustainable power, water, and gas. Utility companies' core activities revolve around their field workforce. It is difficult for organizations to track the field workforce for optimization, if disconnected. A connected workforce can improve safety while achieving regulatory compliance.
Digital technology that connects frontline and field workers with their work environment for productivity, safety, and profit gains is the solution. By connecting the industrial (field and frontline) workers with the back office, utility companies achieve better operational efficiency with access to real-time data when it is needed. This connectivity in turn, helps increase productivity and lets workers be more focused on their jobs. Through connected workers, companies can gain get a real-time glance at worker activity. Managers, supervisors, or executives can make the right decisions from handheld devices that connect with the company's ERP.
Achieve Higher Productivity, Safety, and Performance with Connected Workers
The concept of the Connected Worker has a great potential in Industrial Transformation. Digitally connecting frontline workers is increasingly viewed as a core aspect of digitalization initiatives and it makes complex and time-consuming tasks easier. Innovapptive believes that implementing the right connected platform, your workers are empowered to improve organizational efficiency and productivity.
Innovapptive offers the next generation Connected Workforce Platform™ that seamlessly connects your entire field workforce, executive and back office to achieve higher operational excellence and efficiency, resulting in maximized customer satisfaction & revenue. The platform connects your field workers with what they need, when and where they need it. The platform features integrated, field-ready mobile applications to enhance interconnectivity, maximize the value of data, automate core processes, and optimize your organization’s most important workflows. The Connected Workforce Platform™ uses built-in integrations to connect your SAP®, IBM Maximo, and other back-office systems with advanced mobile applications. By combining these powerful tools, organizations can bridge communication and information gaps between executive teams, field technicians, plant operators, warehouse operators, maintenance engineers, and back-office staff.
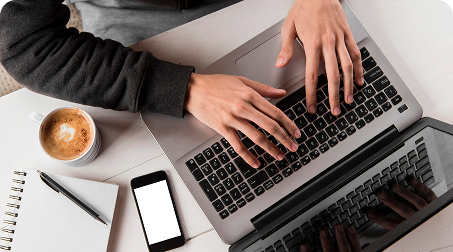
See It In Action
Schedule a personalized demo to see how our solutions can help your business thrive.
- 22-04-2025
The $3.6B Unlock: Solving the Chemical Industry’s Labor Crisis and EBITDA Pressure in One Move
“Constraints don’t slow innovation—they force it.”
- 21-04-2025
Chemical Industry's Margin Erosion: A Wake-Up Call for Operational Efficiency Amid China's Oversupply
The global chemical industry is facing mounting challenges, with revenue declines and shrinking...
- 21-04-2025
Why Wrench Time Isn’t Improving: The Hidden Costs of Traditional Maintenance Scheduling
For years, industrial leaders have relied on a common but flawed assumption: "Better planning and...