Corrective and Preventive Action (CAPA): Why It Matters and How to Improve It
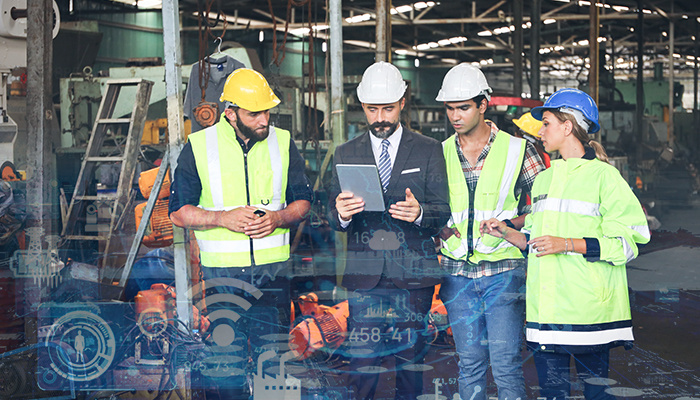
Why Corrective and Preventive Action (CAPA) Matters
No organization is immune to defects, non-conformances, or safety incidents. Whether it’s a product failure, workplace hazard, or operational inefficiency, businesses must take systematic action to address and prevent these issues from recurring. This is where Corrective and Preventive Action (CAPA) comes into play.
CAPA isn’t just about fixing problems—it’s about identifying root causes and implementing long-term solutions that enhance safety, compliance, and operational efficiency. Without a structured CAPA process, organizations risk repeating the same mistakes, leading to costly downtime, compliance violations, and reputational damage.
Despite its importance, many companies still rely on manual CAPA processes, such as spreadsheets or paper-based forms. This approach is slow, prone to errors, and makes tracking corrective actions difficult. Corrective and preventive action software offers a digital alternative that automates workflows, ensures accountability, and improves compliance.
Understanding Corrective vs. Preventive Actions
Corrective Action: Addresses an issue that has already occurred. It involves identifying the root cause, fixing the problem, and ensuring it doesn’t happen again.
Example: A company recalls a faulty batch of products and revises its manufacturing process.
Preventive Action: A proactive measure to prevent potential issues before they arise.
Example: Conducting regular equipment maintenance to prevent unexpected breakdowns.
A strong CAPA process integrates both elements, ensuring that businesses not only respond to issues but also anticipate and prevent them.
The Challenges of Manual CAPA Management
Many companies struggle with CAPA implementation due to:
- Lack of Standardization: Without a defined corrective and preventive action template, employees may document issues inconsistently, leading to gaps in data.
- Delayed Responses: Manual workflows slow down the CAPA process, delaying issue resolution.
- Limited Visibility: Tracking corrective actions across departments becomes difficult without a centralized system.
- Compliance Risks: Regulations like ISO 9001, FDA 21 CFR Part 820, and OSHA require documented CAPA processes. Failing to meet these standards can result in penalties.
Organizations that fail to digitize CAPA management often find themselves struggling with inefficiencies, repeated incidents, and regulatory challenges.
How Digital CAPA Solutions Improve Efficiency
Modern corrective and preventive action software streamlines CAPA management by automating workflows, improving documentation, and ensuring accountability. Here’s how:
- Automated Workflows – Assign corrective actions, set deadlines, and track progress in real time.
- Centralized Data Management – Maintain a single source of truth for all CAPA-related information.
- Root Cause Analysis Tools – Identify and eliminate the root causes of recurring issues.
- Regulatory Compliance – Ensure all CAPA activities align with industry standards.
- Instant Reporting & Audit Trails – Generate reports and track changes for internal and external audits.
By replacing manual processes with a digital system, businesses can reduce errors, save time, and improve overall quality management.
🚀 Ready to streamline CAPA management? Request a demo today.
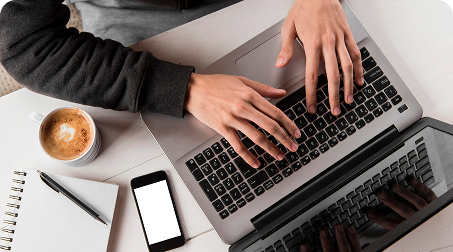
See It In Action
Schedule a personalized demo to see how our solutions can help your business thrive.
- 22-04-2025
The $3.6B Unlock: Solving the Chemical Industry’s Labor Crisis and EBITDA Pressure in One Move
“Constraints don’t slow innovation—they force it.”
- 21-04-2025
Chemical Industry's Margin Erosion: A Wake-Up Call for Operational Efficiency Amid China's Oversupply
The global chemical industry is facing mounting challenges, with revenue declines and shrinking...
- 21-04-2025
Why Wrench Time Isn’t Improving: The Hidden Costs of Traditional Maintenance Scheduling
For years, industrial leaders have relied on a common but flawed assumption: "Better planning and...