3 Major Causes of Unplanned Shutdowns and How to Solve Them
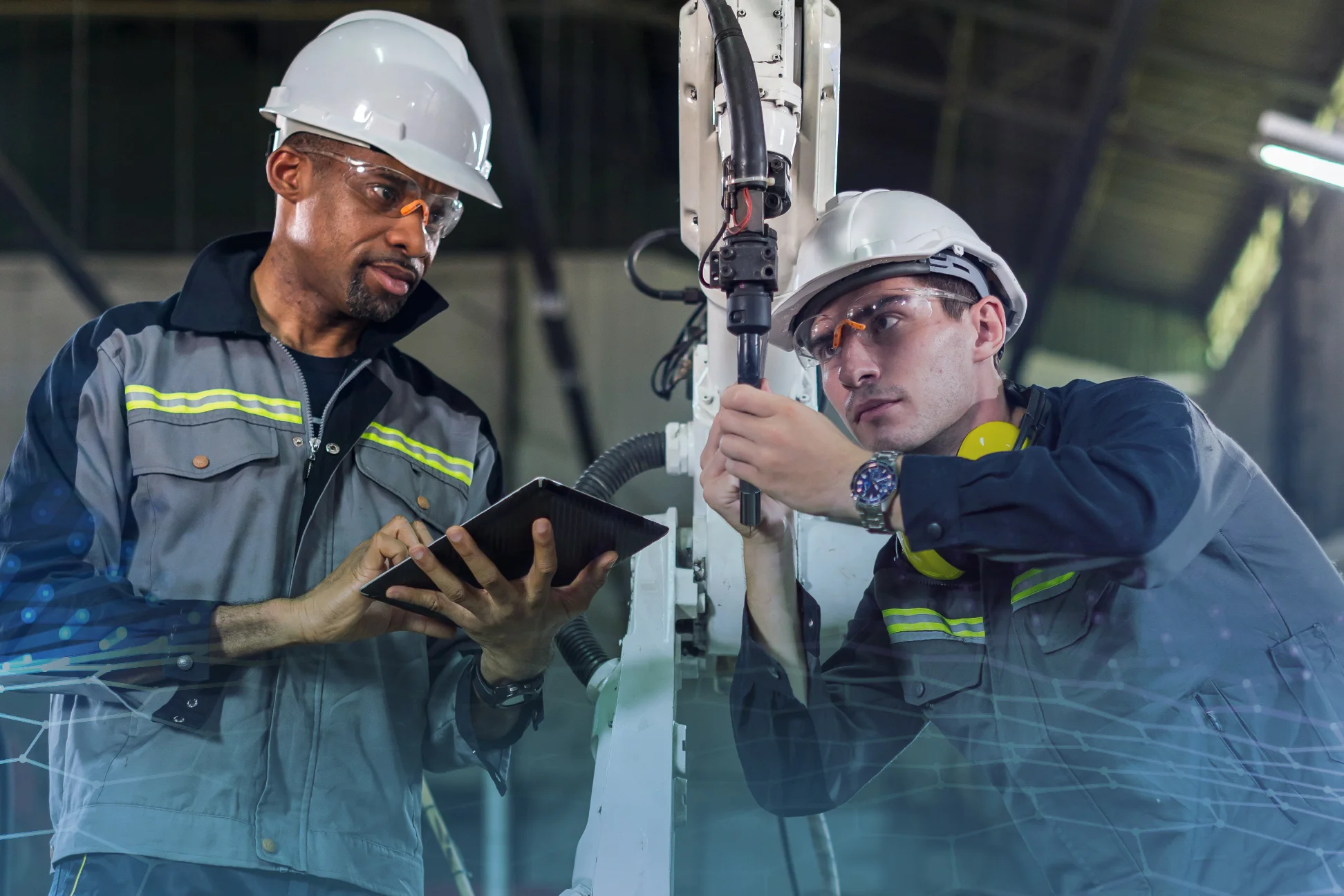
Ever had that sinking feeling in your gut as the red alarm flashes on your control panel, screaming "EQUIPMENT FAILURE"? Your heart races, sweat beads on your forehead, and the dreaded words escape your lips - "unplanned shutdown." At that moment, your carefully planned production schedule crumbles, costs spiral upwards, and customer trust starts to erode.
This isn't just a hypothetical scenario. 82% of large enterprises, like yours, experienced unplanned shutdowns in the past three years, according to Aberdeen Research. And these aren't minor hiccups. Each shutdown costs an average of $260,000 per hour, lasting a gut-wrenching four hours on average. Imagine the lost revenue, missed deadlines, and angry customers that come with that downtime.
But here's the scariest part: over two-thirds of maintenance professionals have no real idea when their equipment needs attention. They're sleepwalking into disaster, relying on outdated paper-based work orders and reactive maintenance that waits for equipment to scream in pain before taking action. This "run-to-failure" approach is like playing Russian roulette with your entire operation.
The good news? This doesn't have to be your reality. There's a cure for the unplanned shutdown headache, and it's right at your fingertips - mobile work order management.
The Culprits Behind the Crisis: Major Causes of Unplanned Shutdowns
While these unplanned shutdowns might seem like sudden storms, they're often fueled by silent, insidious forces lurking within outdated maintenance practices. Let's shed light on the three key culprits wreaking havoc:
1. The Reactive Maintenance Trap
Imagine firefighting without preventative measures, waiting for flames to engulf the building before scrambling for action. That's the essence of reactive maintenance, a strategy heavily reliant on waiting for equipment failure before initiating repairs. This gamble often backfires:
- 66% of maintenance professionals report unplanned downtime due to unavailable spare parts, a direct consequence of this reactive approach.
- Our survey reveals an average downtime duration of 5.2 hours with reactive maintenance, significantly higher than proactive strategies.
- Aberdeen Research estimates 30% more downtime for companies clinging to reactive methods.
2. Blinded by Paperwork: The Visibility Void
Imagine navigating a complex manufacturing plant blindfolded, relying solely on scattered scraps of paper for directions. That's the reality with paper-based work orders, creating:
- Inaccurate data: Manual entries create a fog of outdated information, leaving managers with a skewed view of equipment health and maintenance needs.
- Productivity bottlenecks: Technicians spend precious time deciphering handwritten notes and chasing approvals, hindering efficiency.
- Limited real-time visibility: Identifying potential issues before escalation becomes practically impossible, leaving you vulnerable to sudden shutdowns.
3. Communication Breakdown: The Lost Signals of Siloed Information
Imagine firefighters using smoke signals to coordinate efforts. Sounds chaotic, right? That's the communication equivalent of relying on manual systems for work requests and task assignments:
- Delays and frustrated teams: Technicians waste valuable time searching for the right person to handle urgent issues.
- Incomplete or lost documentation: Confusion and rework arise, further hindering efficiency.
- Disconnects between supervisors and technicians: Prioritizing tasks and allocating resources effectively becomes a challenge.
Slay the Silent Killers of Downtime With Mobile Work Order Management
Remember that sinking feeling from the introduction? Imagine replacing it with a surge of relief and confidence. That's the power of mobile work order management solutions designed to slay the silent killers plaguing your plant. The solution helps you ditch the reactive firefighting and paper-based chaos. Imagine proactive maintenance with real-time equipment health monitoring, technicians armed with mobile work orders for instant access and data capture, and seamless team collaboration with messaging and shared workflows. This isn't just about efficiency; it's reduced costs, boosted productivity, enhanced safety, and happier customers.
This mobile solution paves the path to operational excellence:
- From Paper Chase to Digital Dash: Ditch the mountains of paperwork and empower technicians with real-time information on mobile devices. Studies show a 40% increase in productivity and a 25% reduction in errors with mobile work order solutions.
- From Reactive Roulette to Preventive Power: Leverage sensor data and AI-powered analytics to predict potential issues before they erupt. A 2023 Gartner report predicts 70% of manufacturers will use AI for predictive maintenance by 2025, saving an estimated $1 trillion annually.
- From Communication Catastrophe to Collaboration: Foster seamless communication with a central hub for information exchange. Real-time updates, instant messaging, and task delegation features keep everyone in the loop, ensuring swift action and informed decision-making.
While the mobile work order management platform is a game-changer, remember, it's not a magic bullet. To truly conquer unplanned shutdowns and unlock its full potential, a cultural shift is essential. Get everyone from plant managers to technicians on board, foster a data-driven decision-making environment, and embrace a proactive maintenance mindset. Research shows the rewards: a whopping 50% reduction in unplanned downtime (Aberdeen Strategy & Research, 2024), a 20% productivity boost (LNS Research, 2023), and a 15% increase in Overall Equipment Effectiveness (McKinsey, 2022).
Innovapptive’s mWorkOrder is a comprehensive mobile work order management solution designed to be your trusted ally in the fight against downtime. It empowers you to embrace proactive maintenance, see clearly with real-time data, and unleash the power of communication.
Ready To Step Into A Downtime-free Future?
Ready to join the ranks of 2024's operational excellence champions? Don't let unplanned shutdowns hold you back. Contact us today and discover how our mobile work order management platform can help you achieve your goals. Click here to schedule a free, personalized demo today!
Explore our website for additional resources for more insights on how mWorkOrder is helping other large enterprises overcome their maintenance challenges.
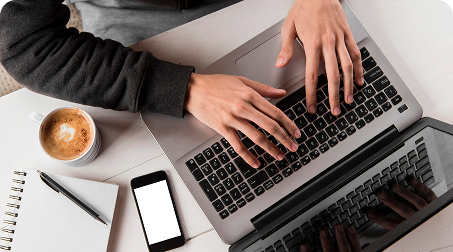
See It In Action
Schedule a personalized demo to see how our solutions can help your business thrive.
- 20-08-2025
Building the future of Industrial Operations with Innovapptive and AWS
Most manufacturers have already gone digital. Yet business outcomes haven’t moved in step. Many...
- 22-04-2025
The $3.6B Unlock: Solving the Chemical Industry’s Labor Crisis and EBITDA Pressure in One Move
“Constraints don’t slow innovation—they force it.”
- 21-04-2025
Chemical Industry's Margin Erosion: A Wake-Up Call for Operational Efficiency Amid China's Oversupply
The global chemical industry is facing mounting challenges, with revenue declines and shrinking...