Does Your Mine Use Syclo or SAP Work Manager? Consider Innovapptive and mWorkOrder
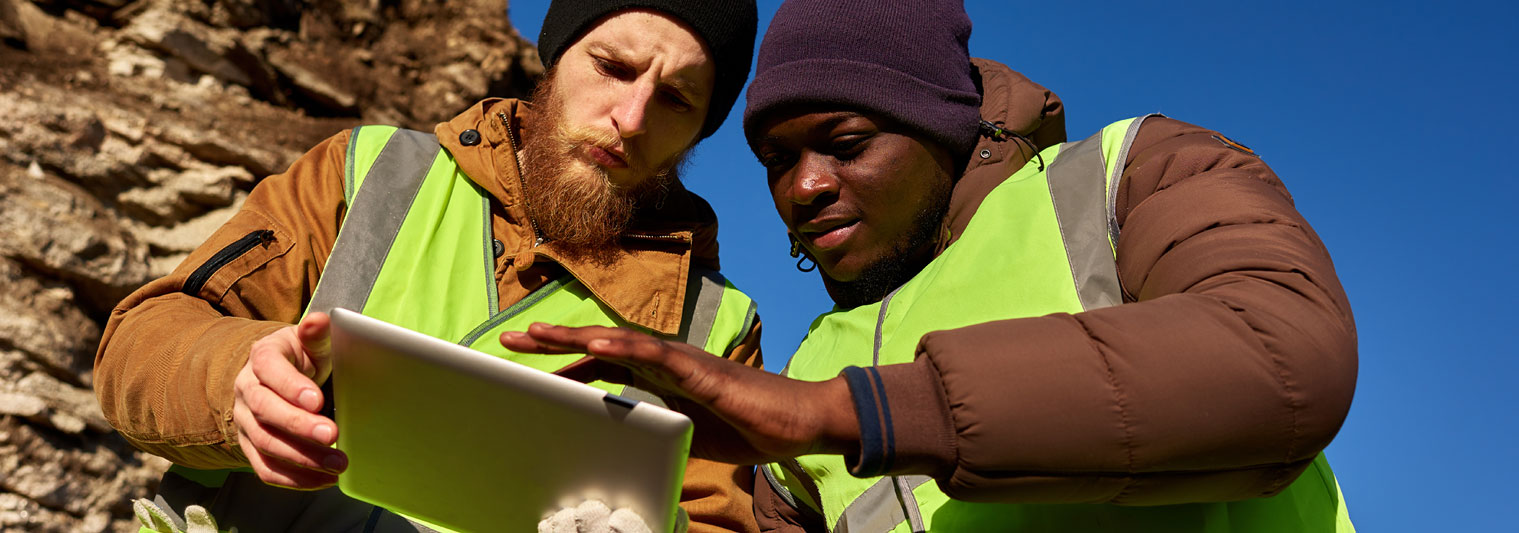
Mining is a complex industry. For one, it almost always operates in remote areas far from infrastructure. Mines are found in the sides of mountains, at the bottoms of deep basins, in tropical forests and in the deep desert – but seldom in the middle of a big city. It also uses highly specialized equipment and machinery found nowhere else. These include earthmovers, blasting tools, crushers, and feeding and conveying equipment. Finally, it’s a rugged industry with many environmental and safety regulations and oversight.
When a piece of mining equipment or machinery unexpectedly goes down, production quickly grinds to a halt and revenues stop flowing. A gold mine has only one product: gold. A coal mine only has one product: coal. A nickel mine has only one product: nickel. These mines can’t switch to another product to keep money coming in. Therefore, machine and equipment maintenance is one of the most important functions at any mining operation.
Many mining companies have been using SAP Work Manager (formerly Syclo Work Manager) running on the SAP Mobile Platform. SAP has announced that it will end support of its on-premise SAP Mobile Platform in 2022. Mining companies that had started with Syclo and transitioned to SAP Work Manager on the SAP Mobile Platform have been stuck in the crossroads of different supporting mobile application development technologies on a single platform.
The SAP Mobile Platform itself is built on an OData Web Protocol, while the acquired Syclo Solution sits on a different technology stack, powered by Syclo Agentry. After SAP’s 2012 Syclo acquisition, customers of that provider have been caught in the crossroads of different types of technologies, unhappily bouncing from technology to technology ever since.
SAP’s investments are now redirected to their cloud offerings on the SAP Cloud Platform with SAP Asset Manager becoming their latest offering. SAP Asset Manager intends to help customers address their field mobility on the Cloud and is a new and unproven solution with limited features and capabilities. SAP Asset Manager must go through the necessary maturity curve before it’s ready for prime time.
The mining industry has been one of the laggards in adopting digital transformation for operations and maintenance. However, mining customers need a best-in-class solution to respond to the current COVID-19 crisis.
In the COVID-19 era, customers need a highly robust, dynamic, agile, intuitive and user-friendly field mobility solution that can not only deliver a “Mobile-First” solution for the field worker, but also deliver real-time insights of field work to the back office and key executives. It’s now an imperative, and not a nice to have. At Innovapptive, we call this a “Connected Workforce” experience to help best-in-class companies rapidly embrace “Social Distancing” as an immediate priority. Stricter public health and government regulations require mining customers to invest in a longer-term technology platform that’s capable of responding to such dynamic regulations and public health guidelines almost immediately.
The digital universe is evolving into ever-more intelligent, faster and cheaper smartphones and tablets with Wi-Fi capabilities. The market need for new platforms has also dramatically changed. Customers want to take full advantage of smartphones, tablets and infrastructure to have truly seamless experiences in the field or in the mine.
Fortunately, there’s good news for forward-looking mining companies to embrace new business models that are demanding them to embrace new policies, job instructions and standard operating procedures (SOP’s) to adapt to crises such as COVID-19. This is a great opportunity for mining companies to rethink their digital and technology strategy to keep their field workers highly productive, safe, practice “social distancing,” and almost immediately implement dynamic government and public health regulations and guidelines. Identifying continued opportunities to improve your bottom line is now a necessity in an unpredictable, uncertain and volatile world that we expect to witness in the next few years.
Innovapptive (see a two-minute video) is a mobile-first connected workforce platform provider that saves companies millions of dollars on mining equipment maintenance. It allows customers to quickly respond to stricter government and public health regulations and guidelines to make “Safety First” policies and standard operating procedures (SOPs) readily and digitally available as workflows to all mine field workers. Mineworkers can almost immediately practice and embrace “Social Distancing.”
Newmont Mining is one of our largest mining customers that utilizes mWorkOrder solution to manage mine equipment maintenance. mWorkOrder allows Newmont to seamlessly connect field workers, back-office systems, machines and methods that they can use to proactively manage maintenance programs to reduce unscheduled downtime, keep production running and improve operational efficiency.
Innovapptive gives mining companies the freedom to modernize their operations without technology limitations, challenges and frustrations. Some of the benefits witnessed by our customers include:
Productivity
- 100% elimination printing, sorting, collating and distributing work orders
- 40% to 60% reduction in tech time for data entry
- 15% to 20% reduction in work order reworks due to incomplete information
- 40% to 60% increase supervisor/planner capacity for higher level activities
- 40% to 60% reduction technician overtime due to efficiencies gained
Maintenance
- 25% to 50% reduction in downtime and production delays
- 70% to 80% reduction in preventable failures
- 40% to 60% reduction in maintenance backlog
Compliance
- 40% to 60% reduction in worker compensation payments
- 70% to 80% reduction in cost of fines and remediation due to environmental incidents
- 70% to 80% reduction in safety incidents
mWorkOrder is a fully code-free, configurable, mobile-first solution that enables mining companies to:
- Get real-time alerts and push notifications on current plant/asset/equipment status and condition.
- Improve data collection and reporting during operator rounds, field inspections and risk assessments.
- Issue emergency work orders, prioritize tasks, and enhance planning and scheduling to respond quickly to issues before they become problems.
mWorkOrder (watch a 10-minute video) digitally connects a mine’s maintenance staff with site management and back-office systems through smartphones, tablets, scanners, wearables, drones, etc. mWorkOrder provides the maintenance staff the flexibility and agility they need to do their jobs efficiently. Supervisors, managers and directors, meanwhile, have immediate access to mission-critical information digitally collected in the field via desktop apps. Leadership can make informed decisions based on field-verified facts rather than intuition. With timely and accurate data, labor and resources can be more effectively deployed throughout the mine, reducing duplication of effort, preventable failures and unscheduled downtime.
If you’re looking for the same functionality and benefits you received in an EAM solution from Syclo – and more – schedule a free demo of Innovapptive’s mWorkOrder today by calling 844-464-6668 or by clicking here.
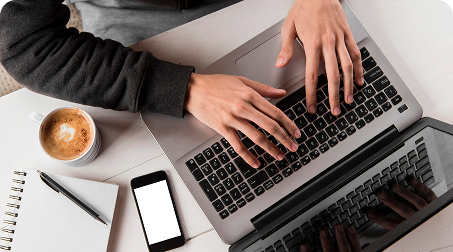
See It In Action
Schedule a personalized demo to see how our solutions can help your business thrive.
- 22-04-2025
The $3.6B Unlock: Solving the Chemical Industry’s Labor Crisis and EBITDA Pressure in One Move
“Constraints don’t slow innovation—they force it.”
- 21-04-2025
Chemical Industry's Margin Erosion: A Wake-Up Call for Operational Efficiency Amid China's Oversupply
The global chemical industry is facing mounting challenges, with revenue declines and shrinking...
- 21-04-2025
Why Wrench Time Isn’t Improving: The Hidden Costs of Traditional Maintenance Scheduling
For years, industrial leaders have relied on a common but flawed assumption: "Better planning and...