Empower Your Team with Mobile Maintenance for IBM Maximo
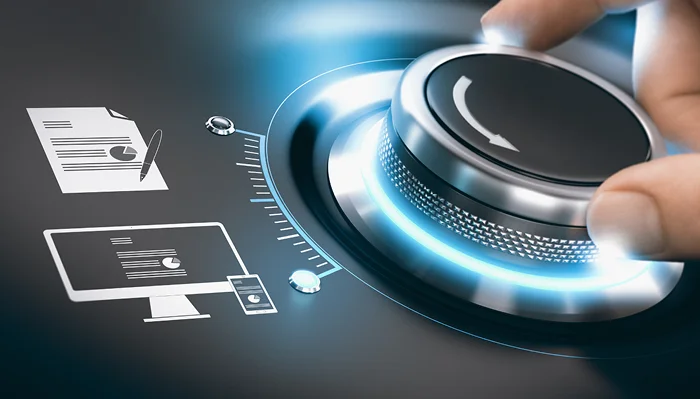
If your maintenance technicians are still manually entering operational data into IBM Maximo, you’re reducing efficiency and productivity. Mobile maintenance for IBM Maximo enables a digitally connected workforce, providing measurable improvements in maintenance operations.
Challenges of Manual Maintenance Reporting
Adopting an integrated mobile frontline worker solution for your IBM Maximo system can help overcome challenges such as:
-
Lack of operational visibility – Delayed data prevents quick decision-making.
-
Inflexible data collection and sharing systems – Paper-based processes slow workflows.
-
Multiple information silos – Maintenance data remains inaccessible across teams.
-
Poor wrench time – More time spent on manual data entry than on repairs.
-
Increasing backlogs – Delayed work orders lead to operational inefficiencies.
-
High equipment downtime – Reduced visibility results in unplanned maintenance.
Is This How You Envisioned Your Maintenance Department Would Operate?
Maintenance is a complex job requiring highly skilled professionals. Manufacturing plants and industrial facilities house billions of dollars worth of equipment that demand consistent, professional upkeep. Every moment of equipment downtime leads to revenue loss, operational disruptions, and impacts customer relationships.
Limitations of Paper-Based Data Collection in IBM Maximo
The IBM Maximo asset management system is designed to digitize operational data, but its capabilities are hindered by manual reporting. Here’s how paper-based data collection limits maintenance efficiency:
-
Lack of operational visibility – Decision-makers receive outdated data, leading to delayed responses.
-
Rigid data collection – Paper-based processes are difficult to modify for evolving business needs.
-
Information silos – Sharing critical data across teams is slow and inefficient.
-
Reduced wrench time – Technicians spend excessive time on manual data entry instead of focusing on equipment maintenance.
-
Increased backlogs – Delays in work order completion lead to growing maintenance workloads.
-
Higher equipment downtime – Delayed maintenance actions increase machine failures and unplanned breakdowns.
The Power of Mobile Maintenance for IBM Maximo
Mobile technology and digital transformation have revolutionized plant maintenance. Organizations can now replace paper-based workflows with a fully digital maintenance ecosystem.
How Mobile Maintenance Solutions Work
Frontline workers equipped with mobile devices, tablets, or wearables can seamlessly record real-time data and integrate it into IBM Maximo. Key capabilities include:
-
Instant data entry and retrieval – Eliminates manual paperwork delays.
-
Real-time work order tracking – Decision-makers can monitor progress and collaborate remotely.
-
Push notifications and alerts – Enables faster response times and proactive maintenance.
-
Two-way communication – Improves technician collaboration with supervisors via video conferencing or messaging.
Advantages of Mobile-Enabled IBM Maximo Maintenance
Mobile frontline worker applications and connected worker platforms offer significant operational benefits:
-
Better collaboration – Enables teams to work together in real-time.
-
Real-time reporting – Ensures instant access to critical maintenance data.
-
Reduced operational costs – Lowers expenses by improving work order efficiency.
-
Increased productivity – Automates work order assignments and tracks technician performance.
-
Efficient data collection – Reduces manual entry errors and improves data accuracy.
Key Benefits of Mobile Maintenance for IBM Maximo
A mobile workforce solution integrated with IBM Maximo allows maintenance teams to:
✔ Gain real-time visibility into asset performance and maintenance status.
✔ Eliminate paper-based documentation, improving mobility and workforce efficiency.
✔ Easily access a user-friendly interface suitable for both technicians and executives.
✔ Generate and track work orders with automated assignments.
✔ Monitor equipment performance to identify early signs of failure.
✔ Speed up work order fulfillment by providing real-time equipment location data.
✔ Trigger safety notifications when assets exceed operational thresholds.
✔ Work in offline mode, ensuring continuous operation even in remote locations.
✔ Shift from reactive maintenance to a proactive asset management strategy.
Digitize Your Maintenance Operations with Innovapptive
Innovapptive specializes in mobile frontline worker solutions that integrate seamlessly with IBM Maximo, empowering organizations to:
-
Improve work order accuracy.
-
Increase technician productivity.
-
Reduce maintenance downtime.
-
Strengthen regulatory compliance.
Schedule a free demo or call 888-464-6668 to discover how mobile maintenance solutions can transform your IBM Maximo operations.
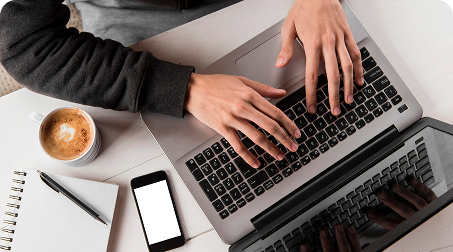
See It In Action
Schedule a personalized demo to see how our solutions can help your business thrive.
- 20-08-2025
Building the future of Industrial Operations with Innovapptive and AWS
Most manufacturers have already gone digital. Yet business outcomes haven’t moved in step. Many...
- 22-04-2025
The $3.6B Unlock: Solving the Chemical Industry’s Labor Crisis and EBITDA Pressure in One Move
“Constraints don’t slow innovation—they force it.”
- 21-04-2025
Chemical Industry's Margin Erosion: A Wake-Up Call for Operational Efficiency Amid China's Oversupply
The global chemical industry is facing mounting challenges, with revenue declines and shrinking...