Enhancing Pipeline and Refinery Maintenance with an Intelligent Connected Worker Platform
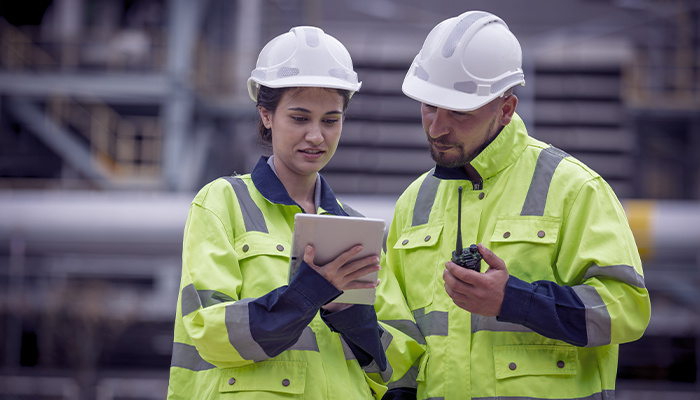
Key Takeaways
- Downtime in refineries can cost between $100,000 and $1 million per hour depending on equipment and process complexity.
- By digitizing workflows and providing mobile access to maintenance tools and real-time data, a connected worker platform enhances worker productivity by up to 20%.
- A connected worker platform with predictive maintenance tools can decrease Mean Time to Repair (MTTR) by up to 20%, resulting in significant cost savings.
Introduction
Oil & gas midstream and downstream companies grapple with significant maintenance challenges that can be mitigated using an intelligent connected worker platform. These platforms integrate mobile technology with real-time data, providing frontline workers with critical tools to address common issues such as equipment failures, safety compliance, and communication gaps.
This blog explores how intelligent connected worker platforms streamline maintenance processes, offering solutions to complex problems by ensuring timely updates, predictive maintenance capabilities, and improved coordination. Discover the innovative ways these platforms support efficient maintenance operations, reduce unplanned downtime, and enhance the safety and reliability of pipelines and refineries.
Issue 1: Unplanned Downtime and Equipment Failures
Unplanned downtime from equipment failures results in significant production losses and high repair costs. Key components affected include:
- Compressors: Failure drops pipeline pressure, reducing flow or stopping gas transmission, leading to supply disruptions and operational downtime.
- Pumps: Halts liquid flow, causing delays, shutdowns, and increased spill risks.
- Valves: Malfunctions can cause leaks, safety hazards, and product loss, sometimes necessitating shutdowns to prevent catastrophic failures.
- Furnaces and Boilers: Disruption of essential heat halts distillation and conversion, leading to downtime and safety hazards from pressure buildup or unburned hydrocarbons.
- Cooling Towers and Heat Exchangers: Failure prevents effective heat dissipation, causing overheating, process disruptions, and potential damage.
Integrate with ERPs, Historians & IoT devices and offer real-time monitoring and predictive analytics. This enables proactive maintenance, reduces unexpected breakdowns, and provides mobile alerts and dashboards to keep workers informed about critical asset conditions.
Issue 2: Inefficient Maintenance Workflows
Traditional paper-based workflows in oil and gas pipeline maintenance lead to errors, delays, and inefficiencies, causing increased downtime, safety risks, and financial losses. Common issues include:
- Lack of Standardized Procedures: Inconsistent maintenance tasks due to missing standardized procedures and checklists result in frequent breakdowns and inefficient resource use.
- Inadequate Record Keeping: Poorly managed, incomplete, or outdated maintenance records hinder tracking, analysis, and planning, leading to repeated mistakes.
- Reactive Maintenance Approach: Relying on reactive maintenance instead of preventive strategies leads to higher costs, longer downtimes, and reduced equipment lifespan.
- Insufficient Training: Lack of training in modern technologies results in improper maintenance techniques, errors, and decreased efficiency and safety.
- Inadequate Use of Technology: Failure to adopt CMMS, IoT, and mobile solutions causes slow response times, higher costs, and missed predictive maintenance opportunities.
Mobile technology enables real-time access to digital work orders, checklists, and forms, streamlining maintenance from task assignment to documentation. With the ability to update backend ERPs like SAP directly from the field, it enhances accuracy and reduces administrative burdens. Capturing wrench time means reliability engineers have half their work done.
Issue 3: Poor Inventory Management
Ineffective management of spare parts and materials leads to maintenance delays, increased downtime, and higher operational costs. Key issues include:
- Inaccurate Inventory Records: Manual errors, unaccounted parts, and delayed updates create discrepancies between actual and recorded stock, causing delays when locating necessary parts.
- Lack of Inventory Visibility: Outdated systems and unintegrated data limit real-time inventory tracking, slowing part identification and access, thus extending repair times.
- Over-Reliance on Manual Processes: Manual inventory tracking with spreadsheets or paper records introduces errors and inefficiencies, increasing the likelihood of stockouts and prolonged repair times.
- Poor Demand Forecasting: Inadequate forecasting leads to overstocking or understocking, either causing critical parts shortages or tying up capital and space, hindering maintenance operations.
- Inadequate Stock Replenishment: Lack of effective replenishment practices results in stockouts or excess inventory, delaying emergency repairs and prolonging downtime.
Mobile inventory management solutions enable real-time tracking of parts, allowing workers to update inventory levels via barcode scanning. This ensures timely availability of parts and reduces downtime from stock shortages, while connected platforms offer visibility into inventory status and facilitate automatic reordering. Achieving 99% inventory accuracy is the goal of an intelligent connected worker platform.
Issue 4: Lack of Real-Time Communication and Collaboration
Maintenance teams in oil and gas often face communication gaps, especially when coordinating across locations and shifts, leading to critical issues:
- Inefficient Coordination: Poor communication results in misaligned schedules, duplicate efforts, or missed activities, causing prolonged downtime and increased costs.
- Inaccurate Information Sharing: Without real-time data, decisions are based on outdated or incorrect information, leading to unnecessary repairs, wrong parts orders, or missed tasks.
- Poor Asset Utilization: Gaps in communication hinder efficient asset use and maintenance planning, resulting in higher costs and more unplanned outages.
- Inventory Mismanagement: Lack of updates on inventory levels causes overstocking or stockouts, delaying repairs and increasing downtime.
- Fragmented Documentation: Real-time communication issues lead to fragmented documentation, complicating compliance reporting, historical analysis, and activity tracking.
Intelligent connected worker platforms provide real-time communication tools like messaging, video calls, and collaborative workspaces, enabling instant information sharing and coordination. Remote assistance features allow for expert guidance, improving response times, and problem resolution.
Issue 5: Compliance and Safety Challenges
Ensuring compliance with safety regulations and industry standards is crucial but challenging, especially in dynamic field environments. Poor maintenance and inventory management can lead to significant safety compliance issues in oil and gas pipeline companies, posing risks to personnel and the environment and exposing companies to legal penalties. Key issues include:
- Equipment Failures: Poor maintenance and delayed repairs can cause leaks, ruptures, and explosions, violating safety regulations like PHMSA and OSHA.
- Inadequate Records: Poor documentation leads to incomplete inspection and maintenance records, making compliance verification difficult and risking fines.
- Delayed Repairs: Unavailability of parts or poor scheduling creates safety hazards, violating OSHA and EPA regulations.
- Environmental Non-Compliance: Poor maintenance can lead to spills and emissions, breaching environmental regulations like the Clean Water Act and Clean Air Act, resulting in fines and remediation.
- Worker Safety Violations: Unsafe working conditions due to inadequate maintenance can lead to legal actions and increased insurance costs.
Mobile technology offers digital safety checklists and regulatory compliance documentation, allowing for real-time updates and tracking. This creates a digital audit trail that simplifies compliance and enhances safety. Shift handovers, which are crucial audit records, are automated with new-age technology as data is captured during daily operator rounds or basic inspections.
The Case for Innovapptive's Intelligent Connected Worker Platform
Innovapptive's Intelligent Connected Worker Platform revolutionizes pipeline and refinery maintenance by integrating real-time data, mobile technology, and IoT-enabled predictive analytics. This platform addresses common challenges in the oil and gas industry, such as unplanned downtime, equipment failures, and inefficient maintenance workflows.
By providing frontline workers with mobile access to critical information and tools, the platform enables proactive maintenance, thereby reducing unexpected breakdowns and minimizing production losses. Features like mobile operator rounds, digital inspections, digital work order management, predictive maintenance capabilities, and seamless ERP integration enhance coordination and communication among maintenance teams, resulting in improved efficiency and safety. This integration not only optimizes maintenance processes but also ensures timely updates and better decision-making, leading to increased operational reliability and reduced downtime.
Innovapptive’s platform streamlines inventory management and enhances compliance and safety protocols. The platform’s real-time inventory tracking and management tools ensure that spare parts are available when needed, reducing delays, and minimizing stockouts. Effective inventory management is crucial for timely repairs and maintenance operations.
Additionally, the platform's digital safety checklists and compliance documentation provide a comprehensive audit trail, simplifying compliance with safety regulations and industry standards. The inclusion of augmented reality (AR) features for remote assistance allows for expert guidance in complex maintenance tasks, improving troubleshooting efficiency and reducing the need for expert travel.
Overall, Innovapptive’s Intelligent Connected Worker Platform delivers significant benefits, including enhanced productivity, reduced maintenance costs, and improved safety, making it a valuable asset for midstream and downstream oil & gas companies.
Intelligent Connected Worker Platform Capabilities
Innovapptive’s Connected Worker Platform is a competitive choice for mid and downstream oil & gas companies, empowering frontline workers, supervisors, and managers through:
- Predictive and Preventive Maintenance: The platform leverages AI/ML and IoT technologies to support predictive maintenance. Sensors and IoT devices provide real-time data on equipment health, enabling the prediction of potential failures before they occur. This proactive approach helps in scheduling maintenance activities during non-peak times, thus avoiding costly unplanned downtime.
- Real-Time Data Integration: Innovapptive’s platform integrates seamlessly with ERP systems like SAP and IBM Maximo, providing real-time data access and synchronization. This integration ensures that frontline workers have immediate access to accurate data regarding inventory, maintenance history, and equipment status, which enhances decision-making and operational efficiency.
- Augmented Reality (AR) and Remote Assistance: AR features within the platform enable remote experts to assist field workers in real time. Using smart devices or AR glasses, technicians can receive visual guidance and support for complex maintenance tasks, reducing the need for expert travel and speeding up troubleshooting and repairs.
- Inventory and Warehouse Management: mInventory supports efficient warehouse and inventory management by offering mobile capabilities for scanning, tracking, and managing inventory transactions. This ensures high accuracy in inventory data and optimizes the availability of spare parts, which is crucial for effective maintenance operations.
- Customizable Digital Workflows: The platform features a no-code/low-code customization tool, RACE™, allowing organizations to tailor workflows and digital forms to their specific needs. This flexibility helps in quickly adapting to changes in maintenance processes and regulatory requirements, ensuring compliance and enhancing productivity.
- Safety and Compliance: Innovapptive’s platform includes digital safety checklists and compliance forms that workers can use on the go. This not only ensures that all safety protocols are followed but also creates a digital audit trail that can be reviewed to maintain regulatory compliance.
- Analytics and Reporting: The platform provides comprehensive dashboards and reporting tools that offer insights into maintenance performance, resource utilization, and operational efficiency. These analytics help in identifying trends, optimizing maintenance schedules, and improving overall operational strategies.
Innovapptive’s Intelligent Connected Worker Platform Components
- Mobile Operator Rounds: mRounds enables operators to create, schedule, and dispatch rounds to mobile devices, follow step-by-step instructions, capture evidence and cycle time, and publish audit trails and anomalies in shift reports. It also generates alerts, notifications, and actions to enhance collaboration between operators, supervisors, and maintenance teams.
- Automated Shift Handovers: mRounds enhances efficiency by automatically summarizing key information from digital operator rounds, standardizing reports, and improving shift communication between outgoing and incoming shifts. It facilitates real-time collaboration, streamlines handovers, and reduces downtime, while proactive risk identification during rounds boosts safety by enabling prompt resolution of potential issues.
- Mobile Inspections: mInspections offers early warnings for pipeline and refinery maintenance and safety, allowing supervisors to deploy digital forms with code-free authoring, schedule inspections, and allocate them to assets and personnel. It records cycle times and field data as an audit trail, improving shift-to-shift information sharing and anomaly detection.
- Mobile Work Order Management: mWorkOrder provides a digital approach to managing work orders. It allows technicians to access and execute work orders from mobile devices, streamlining the process and reducing the reliance on paper-based systems. This enhances efficiency by providing real-time updates and step-by-step digital instructions, which helps in minimizing errors and reducing downtime.
- Digital Work Instructions: Digital Work Instructions mitigate talent shortages and knowledge loss by providing trainees with step-by-step, visually guided instructions on mobile devices, supported remotely by managers or technicians. Visual aids ensure correct task execution and adherence to safety precautions.
- Inventory and Warehouse Management: mInventory supports efficient warehouse and inventory management by offering mobile capabilities for scanning, tracking, and managing inventory transactions. This ensures high accuracy in inventory data and optimizes the availability of spare parts, which is crucial for effective maintenance operations.
The Innovapptive Intelligent Connected Worker Platform offers three control centers:
- Maintenance Control Center (MCC): Integrated with mWorkOrder. Supervisors and managers can assign work orders to maintenance workers, send notifications, see real-time spare parts availability and kit status, and monitor work order progress from a single interface. Field workers can execute work orders within a paperless process.
- The Work Instructions Authoring Tool: Integrated with mWorkOrder. Maintenance planners and supervisors can create and attach digital work instructions to work orders to ensure work is completed right the first time with no reworks or backlogs.
- Spare Parts Control Center (SPCC): Integrated with mInventory. Digitizes warehouse processes to ensure maintenance teams receive the right parts at the right time to increase productivity. Supply chain managers can use the SPCC to assign and monitor warehouse tasks such as kitting parts for work orders.
Intelligent Connected Worker Platform Benefits
Mid and downstream oil & gas companies can enjoy many benefits from adopting the Innovapptive Intelligent Connected Worker Platform:
- Improved Operational Efficiency: By digitizing and automating workflows, the platform reduces manual errors and paperwork, leading to increased operational efficiency. This streamlines processes such as maintenance scheduling, inspections, and shift handovers.
- Enhanced Worker Safety: Real-time hazard reporting, digital safety checklists, and remote assistance capabilities help in identifying and mitigating safety risks promptly, thus improving overall safety compliance and reducing incident rates.
- Reduction in Downtime: Predictive maintenance tools and real-time monitoring reduce unplanned downtime by anticipating equipment failures and enabling proactive maintenance. This improves equipment reliability and availability.
- Cost Savings: The platform’s efficiency improvements and predictive capabilities lead to significant cost savings by minimizing repair costs, optimizing inventory levels, and reducing overtime and downtime costs.
- Better Decision-Making: Access to real-time data and advanced analytics facilitates informed decision-making at all levels of the organization. Managers can monitor performance metrics and adjust strategies based on up-to-date information, leading to better resource allocation and operational planning.
Results Refiners and Pipeline Companies Can Expect to See
Innovapptive customers report enjoying the following results:
- Reduction in Downtime: By facilitating predictive maintenance and real-time issue resolution, Innovapptive’s platform helps reduce unplanned downtime by up to 17-22%.
- Increased Efficiency: Enhances worker productivity by up to 20% through streamlined workflows and improved access to information.
- Cost Savings: Decreases Mean Time to Repair (MTTR) by up to 20%, leading to significant cost reductions.
FAQ
- What is an Intelligent Connected Worker Platform?
An Intelligent Connected Worker Platform integrates mobile technology with real-time data to provide frontline workers with critical tools and information, improving maintenance, safety, and operational efficiency in industries such as oil and gas.
- How does unplanned downtime affect oil and gas companies?
Unplanned downtime in oil and gas operations can result in substantial financial losses, with downtime costing up to $1 million per hour depending on equipment failure and process complexity.
- What are the most common causes of maintenance issues in pipelines and refineries?
Common causes include equipment failures (e.g., compressors, pumps, valves), inefficient workflows, poor inventory management, communication gaps, and compliance challenges related to safety regulations.
- What is the difference between reactive and proactive maintenance?
Reactive maintenance addresses equipment failures after they occur, leading to higher costs and longer downtimes. Proactive maintenance focuses on predicting and preventing issues, reducing operational disruptions, and extending equipment lifespan.
- How can mobile technology improve refinery maintenance workflows?
Mobile technology allows real-time access to digital work orders, checklists, and forms, reducing errors and streamlining maintenance processes from task assignment to documentation, ultimately lowering administrative burdens and downtime.
- How does Innovapptive’s Intelligent Connected Worker Platform help reduce unplanned downtime?
Innovapptive’s platform uses predictive analytics and IoT devices to monitor equipment health in real-time, enabling proactive maintenance and reducing unplanned downtime by up to 22%.
- What features of Innovapptive’s platform enhance safety and compliance?
The platform includes digital safety checklists and compliance documentation, creating a real-time audit trail to ensure adherence to safety regulations and improve overall workplace safety.
- How does Innovapptive’s platform improve communication among maintenance teams?
The platform offers real-time communication tools such as messaging, video calls, and collaborative workspaces, ensuring instant information sharing and better coordination, particularly during maintenance tasks.
- How does Innovapptive’s platform improve inventory management for maintenance operations?
Innovapptive’s mobile inventory management solution provides real-time tracking of parts and materials, helping to achieve 99% inventory accuracy and ensuring that critical parts are available when needed, reducing delays and downtime.
- What role does augmented reality (AR) play in Innovapptive’s platform?
AR features allow remote experts to assist field workers in real-time, providing visual guidance for complex maintenance tasks. This reduces troubleshooting time and the need for expert travel, improving overall efficiency.
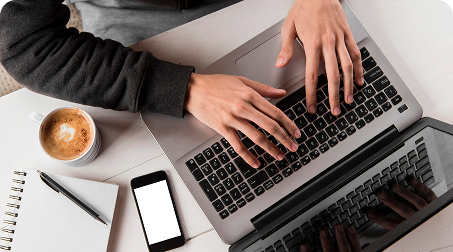
See It In Action
Schedule a personalized demo to see how our solutions can help your business thrive.
- 20-08-2025
Building the future of Industrial Operations with Innovapptive and AWS
Most manufacturers have already gone digital. Yet business outcomes haven’t moved in step. Many...
- 22-04-2025
The $3.6B Unlock: Solving the Chemical Industry’s Labor Crisis and EBITDA Pressure in One Move
“Constraints don’t slow innovation—they force it.”
- 21-04-2025
Chemical Industry's Margin Erosion: A Wake-Up Call for Operational Efficiency Amid China's Oversupply
The global chemical industry is facing mounting challenges, with revenue declines and shrinking...